- Home
- >
- UV Cure Adhesive
- >
- UV Cure Cyanoacrylate Adhesive
UV Cure Cyanoacrylate Adhesive
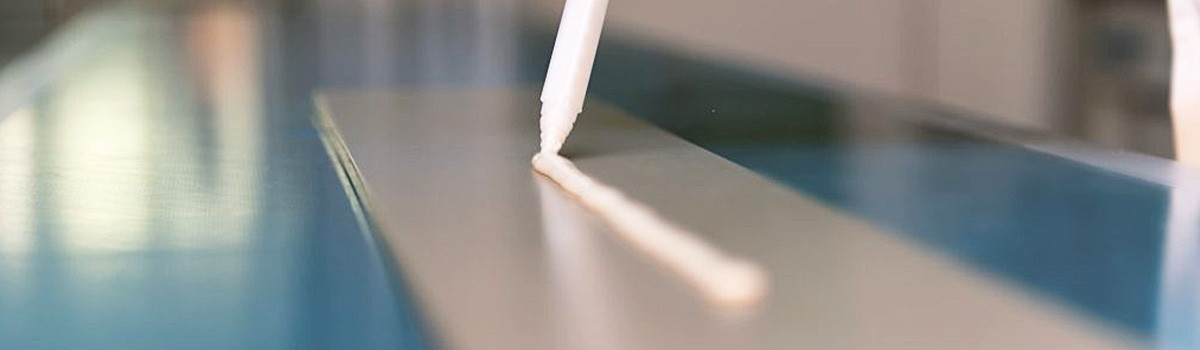
UV Cure Cyanoacrylate Adhesive is a revolutionary bonding solution that combines cyanoacrylate’s strength with UV curing’s efficiency. This adhesive is widely used across industries for its quick bonding capabilities and versatility. This guide explores various UV Cure Cyanoacrylate Adhesive aspects, from its applications to usage tips and safety considerations.
Table of Contents
ToggleWhat is UV Cure Cyanoacrylate Adhesive?
UV-cure cyanoacrylate adhesive, also known as UV-curable cyanoacrylate, is a type of adhesive that belongs to the cyanoacrylate family. Cyanoacrylate adhesives are fast-bonding, high-strength adhesives known for their ability to bond quickly to various substrates. They are commonly referred to as “super glues.”
The UV cure aspect refers to curing or hardening the adhesive. Unlike traditional cyanoacrylate adhesives that cure through moisture in the air, UV cure cyanoacrylate adhesives require exposure to ultraviolet (UV) light to initiate the curing process. Once exposed to UV light, these adhesives undergo a rapid polymerization reaction, forming a solid bond between the joined surfaces.
UV cure cyanoacrylate adhesives are often used in applications requiring a fast and reliable bond. UV light allows for precise control over the curing process, making it suitable for applications in electronics, medical devices, optics, and other fields where quick and accurate bonding is essential.
Critical features of UV cure cyanoacrylate adhesives may include:
- Rapid curing:The adhesive hardens quickly upon exposure to UV light, reducing the time required for the bonding process.
- High bond strength:Cyanoacrylate adhesives are known for their strong bond, and the UV curing process enhances this strength.
- Versatility:These adhesives can bond to many substrates, including plastics, metals, and glass.
- Precision:UV light allows for precise control over the bonding process, making it suitable for applications that require accuracy.
It’s important to note that proper safety precautions should be taken when using UV-cure cyanoacrylate adhesives, including wearing appropriate protective gear and ensuring adequate ventilation when working with UV light sources.
How does UV curing work in this adhesive?
UV curing in adhesives involves using ultraviolet (UV) light to initiate a chemical reaction that transforms liquid or gel-like adhesives into a solid state. The adhesives used in this process are typically formulated with photoinitiators, compounds that can absorb UV light and then initiate a polymerization reaction in the adhesive.
Here’s a general overview of how UV curing works in adhesives:
- Formulation:Adhesive formulations for UV curing typically include monomers, oligomers, and photoinitiators. Monomers are the building blocks of polymers, and oligomers are short chains of monomers. Photoinitiators are chemicals that absorb UV light and become activated.
- Application:The liquid or gel-like adhesive is applied to the surfaces that need to be bonded.
- Exposure to UV Light:Once the adhesive is in place, it is exposed to UV light. UV light has a specific wavelength range, typically between 200 and 400 nanometers, capable of activating the photoinitiators in the adhesive.
- Initiation of Polymerization:When the photoinitiators absorb UV light, they undergo a chemical transformation and generate reactive species, such as free radicals or cations. These reactive species then initiate the polymerization process by causing the monomers and oligomers in the adhesive to link together, forming a three-dimensional network of polymer chains.
- Curing:As polymerization progresses, the liquid or gel adhesive solidifies into a durable, cross-linked structure. This process is known as curing.
- Completion:Once the UV exposure is complete, the adhesive is fully cured, and the bonded surfaces are now securely joined.
UV curing in adhesives offers several advantages, including rapid curing times, minimal heat generation, and the ability to control the curing process precisely. It is commonly used in industries where quick and efficient bonding is essential, such as electronics, medical devices, and specific manufacturing processes. Additionally, the cured adhesive often exhibits desirable properties such as high strength, flexibility, and resistance to chemicals and heat.
What are the primary applications of UV Cure Cyanoacrylate Adhesive?
UV-cure cyanoacrylate adhesives, known as UV-curing instant or light-curable adhesives, cure rapidly when exposed to ultraviolet (UV) light. These adhesives find applications in various industries due to their fast curing times and strong bonding properties. Here are some primary applications of UV-cure cyanoacrylate adhesives:
Electronics Assembly:
- Bonding and encapsulating electronic components.
- Tacking and securing components in place during assembly.
Medical Devices:
- Bonding and assembling medical devices, including catheters and sensors.
- Joining plastic and metal components in medical equipment.
Optical Applications:
- Bonding lenses, prisms, and other optical components.
- Assembling and repairing eyewear.
Dental Applications:
- Bonding dental prosthetics and appliances.
- Securing orthodontic brackets and components.
Automotive Industry:
- Relating plastic and metal components in automotive interiors.
- Sealing and bonding applications in car manufacturing.
Jewelry Manufacturing:
- Bonding gemstones and metal components in jewelry.
- Repairing and assembling delicate jewelry pieces.
General Assembly and Bonding:
- Rapid bonding of various materials, including plastics, metals, and ceramics.
- Assembly of small parts in manufacturing processes.
Printed Circuit Board (PCB) Manufacturing:
- Bonding and securing electronic components on PCBs.
- Encapsulation of sensitive electronic parts.
Aerospace Applications:
- Bonding lightweight materials in aircraft components.
- Repairing and assembling aerospace components.
UV Coating and Laminating:
- Applying thin coatings for protection or enhancement.
- Laminating and bonding films or layers in various applications.
Consumer Goods:
- Bonding and assembling components in consumer electronics.
- Repairing household items and appliances.
Medical Imaging Devices:
- Bonding and building components in imaging devices.
- Encapsulation of sensitive components.
UV-cure cyanoacrylate adhesives are valued for their ability to provide rapid, precise, and strong bonds, making them suitable for applications where quick curing and high bond strength are essential. Additionally, using UV light to cure on demand allows for better control over the bonding process.
Can it bond with different materials?
UV-curable cyanoacrylate adhesives, also known as light-curing cyanoacrylate adhesives, combine the fast bonding properties of cyanoacrylate with the curing capabilities of ultraviolet (UV) light. These adhesives are designed to bond quickly and securely when exposed to UV light, making them suitable for various applications. However, the bonding success with different materials can depend on several factors.
Material Compatibility:
- Plastics:UV-curable cyanoacrylate adhesives can bond well with many plastics, but the success depends on the specific type of plastic. Some plastics may be more challenging to bond due to their chemical composition.
- Metals:These adhesives can generally bond well with metals, but surface preparation may be necessary to ensure optimal adhesion. Cleaning the metal surfaces and using proper adhesion promoters can enhance bonding.
- Glass:UV-curable cyanoacrylate adhesives are often effective for bonding glass materials.
- Ceramics:They can work well with certain ceramics, but the adhesion strength may vary depending on the specific type of ceramic.
Surface Preparation:
- Proper surface preparation is crucial for the success of UV-curable cyanoacrylate adhesives. Surfaces should be clean, dry, and free from contaminants like oils, grease, or dust.
Adhesive Properties:
- The adhesive’s formulation and properties may influence its compatibility with different materials. Some UV-curable cyanoacrylate adhesives are designed for specific applications and materials.
UV Light Exposure:
- Adequate exposure to UV light is essential for the curing process. The intensity and duration of UV light exposure can impact the strength of the bond.
Temperature and Environmental Conditions:
- The curing process may be affected by temperature and environmental conditions. Ensure the adhesive is used within the recommended temperature range and under suitable environmental conditions.
Testing:
- It’s advisable to conduct small-scale tests before using the adhesive on a larger scale or for critical applications. This helps determine the compatibility and bond strength of specific materials.
Always follow the manufacturer’s recommendations and guidelines for your specific UV-curable cyanoacrylate adhesive. If in doubt, you can consult the manufacturer or perform a compatibility test to ensure optimal performance for your particular application.
What makes it suitable for rapid bonding applications?
UV-curable cyanoacrylate adhesives are suitable for rapid bonding applications due to a combination of factors that make them unique and advantageous in specific scenarios:
Fast Curing:
- One of the key features is the rapid curing time. When exposed to ultraviolet (UV) light, these adhesives can cure within seconds, providing quick bonding between substrates. This fast curing is especially beneficial for applications where efficiency and speed are essential.
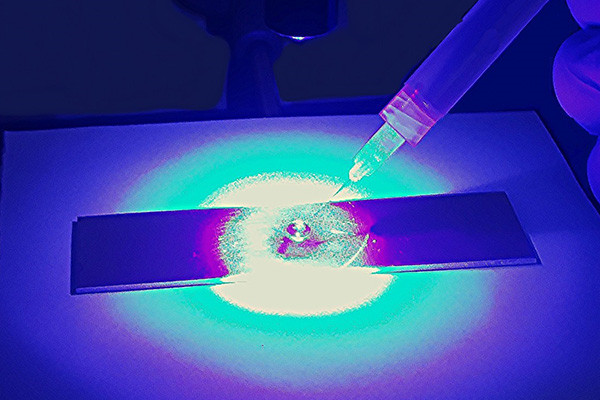
Instant Bonding Properties:
- Like traditional cyanoacrylate adhesives, UV-curable cyanoacrylates offer instant bonding upon contact with the substrate surfaces. This immediate adhesion eliminates the need for clamping or extended curing times, contributing to the overall speed of the bonding process.
Reduced Fixturing Time:
- The need for external fixtures or clamps is minimized due to the quick curing under UV light. This feature allows for easier handling of bonded components shortly after the adhesive is applied and exposed to UV light.
High Bond Strength:
- UV-curable cyanoacrylate adhesives strengthen muscular bonds, providing reliable and durable connections between materials. This is important in applications where the bonded components experience mechanical stress or other forces.
Versatility in Application:
- These versatile adhesives connect various materials, including plastics, metals, glass, and ceramics. Their broad compatibility makes them suitable for multiple applications in different industries.
Minimal Heat Generation:
- The curing process involves UV light, which generates minimal heat compared to other methods, such as heat or chemical curing. This is advantageous when bonding heat-sensitive materials.
Precision and Control:
- UV-curable cyanoacrylate adhesives offer precise control over the application process. The adhesive remains liquid until exposed to UV light, allowing for accurate positioning of components before curing.
Reduced Wastage:
- The fast curing time and instant bonding properties contribute to a reduction in material wastage. Operators can quickly move on to the next steps in the manufacturing process, minimizing downtime and optimizing efficiency.
Automation Compatibility:
- The rapid curing nature of UV-curable cyanoacrylate adhesives makes them compatible with automated processes, enhancing production line efficiency and throughput.
It’s important to note that while UV-curable cyanoacrylate adhesives are well-suited for rapid bonding applications, the choice of adhesive should be based on the specific requirements of the application and the materials being bonded. Proper surface preparation and adherence to manufacturer guidelines are crucial for achieving optimal results.
Are there variations in viscosity available?
UV-curable cyanoacrylate adhesives are known for their fast-curing properties and high bond strength. However, the viscosity of these adhesives can vary based on the specific formulation and intended application. Viscosity is crucial in adhesive selection, affecting how easily the adhesive flows and wets the substrate.
Manufacturers often offer UV-curable cyanoacrylate adhesives in different viscosity grades to accommodate various bonding requirements. The viscosity is usually measured in centipoise (cP) or mPa·s (millipascal-seconds).
Here are some common viscosity grades for UV-curable cyanoacrylate adhesives:
- Low Viscosity (Thin):These adhesives have a low viscosity, allowing them to flow easily into tight spaces and provide fast wetting on surfaces. They are suitable for applications where a thin bond line is desirable.
- Medium Viscosity:Adhesives with medium viscosity balance flowability and gap-filling capability. They are versatile and can be used in various applications, providing good wetting and bonding on different substrates.
- High Viscosity (Thick or Gel):High-viscosity adhesives are thicker and less prone to running. They are suitable for vertical or overhead applications and can provide better gap-filling properties.
The choice of viscosity depends on the specific requirements of the application. For instance, bonding small, delicate components may benefit from a low-viscosity adhesive for precise application, while a high-viscosity adhesive might be preferred for connecting larger, uneven surfaces.
It’s important to note that the actual product offerings may vary between manufacturers. If you have specific viscosity requirements, you should check with adhesive suppliers for the available options in their product lines.
How long does the UV curing process take?
The UV curing process time can vary depending on several factors, including the type of material being cured, the thickness of the material, the intensity of the UV light source, and the specific curing formulation. UV curing is a rapid process compared to traditional methods like heat curing.
In many cases, UV curing can take seconds to a few minutes. For example, in manufacturing UV-curable coatings, adhesives, and inks, exposure to UV light triggers a photochemical reaction that quickly hardens or cures the material. However, remember that the exact time can vary based on the factors mentioned earlier.
Following the manufacturer’s recommendations and guidelines for the specific UV-curable material you are working with is crucial to ensure proper curing and optimal performance. If you have a particular material or application in mind, consulting the material’s technical data sheet or contacting the manufacturer would provide more accurate information about the UV curing time.
What are the advantages over traditional cyanoacrylate adhesives?
Cyanoacrylate adhesives, commonly known as superglues, have been widely used for bonding various materials due to their quick curing time and strong bonding properties. However, advancements in adhesive technology have led to the development of newer formulations with advantages over traditional cyanoacrylate adhesives. Some of these advantages include:
- Flexibility:Newer adhesive formulations may offer improved flexibility, making them suitable for applications where traditional cyanoacrylates might become brittle over time. This is particularly beneficial in applications where materials are subject to movement or stress.
- Gap-filling properties:Some advanced adhesives are designed to fill gaps in the bonded surfaces, providing better adhesion even when the mating surfaces are not perfectly aligned. This can be advantageous in applications where precision in alignment is challenging.
- Resistance to harsh environments:Certain adhesive formulations exhibit enhanced resistance to environmental factors such as moisture, heat, and chemicals. This makes them more durable and reliable in applications where traditional cyanoacrylates might degrade.
- Extended cure time:While cyanoacrylates are known for their fast curing, some applications may benefit from longer adhesives. This allows for better positioning of components before the adhesive sets, making it easier to achieve precise alignments.
- Improved temperature resistance:Advanced adhesives may offer better performance at high and low temperatures, expanding their applicability in extreme temperature variations.
- Reduced odor and blooming:Some newer formulations are designed to have reduced odor during curing and are less prone to blooming, which is the white residue that can sometimes appear around the bonded area.
- Enhanced bond strength:While cyanoacrylate adhesives are known for their strong bonds, newer formulations may provide even greater bond strength, ensuring a more reliable and durable connection between materials.
- Specialized formulations:Manufacturers may develop specialized formulations tailored for specific applications, such as medical-grade adhesives, electronics adhesives, or automotive adhesives, each optimized for the unique requirements of the respective industry.
It’s important to note that the choice of adhesive depends on the specific application requirements, and the advantages of newer formulations may vary depending on the context and materials involved.
Are there any limitations or considerations during the application?
UV cure cyanoacrylate adhesive, like any other material, has specific limitations and considerations during application. Here are some crucial points to keep in mind:
- Substrate Compatibility:Ensure that the substrates you are bonding are compatible with the adhesive. Some materials may be more challenging to bond due to their composition or surface properties.
- Surface Preparation:Proper surface preparation is crucial for the adhesive to bond effectively. Surfaces should be clean, dry, and free from contaminants like grease, oil, or dust. Some materials may require additional surface treatments for optimal adhesion.
- UV Exposure:UV-cure curing cyanoacrylate adhesives rely on exposure to ultraviolet (UV) light. Ensure the adhesive receives adequate UV light exposure to initiate and complete the curing process. Inadequate exposure can result in incomplete curing and compromised bond strength.
- Light Intensity and Wavelength:The curing process’s effectiveness depends on the intensity and wavelength of UV light. Ensure the light source is compatible with the adhesive’s curing requirements. Some adhesives may have specific recommendations for optimal UV light conditions.
- Cure Time:UV-cure cyanoacrylate adhesives typically cure rapidly when exposed to UV light. However, the cure time can vary depending on adhesive formulation, substrate materials, and environmental conditions. Follow the manufacturer’s recommendations for curing time.
- Gap Filling:Cyanoacrylate adhesives, including UV cure variants, are generally unsuitable for large gap-filling applications. The bond strength may be compromised if a significant gap exists between the bonded surfaces. Ensure the adhesive is applied in thin, even layers for the best results.
- Temperature and Humidity:Environmental conditions, such as temperature and humidity, can impact curing. Adhere to the recommended temperature and humidity ranges specified by the manufacturer for optimal performance.
- Safety Precautions:Exercise proper safety precautions when working with UV-cure cyanoacrylate adhesives. UV light can harm the eyes and skin, so use appropriate personal protective equipment (PPE) such as safety glasses and gloves.
- Storage Conditions:Store the adhesive according to the manufacturer’s guidelines. Exposure to light and air can affect the shelf life and performance of the adhesive. Follow recommended storage conditions to ensure the longevity and efficacy of the product.
Always refer to the specific product datasheet or technical information provided by the manufacturer for detailed instructions and considerations particular to the UV-cure cyanoacrylate adhesive you are using.
Can it be used for outdoor applications?
UV-cure cyanoacrylate adhesives are designed to cure rapidly when exposed to ultraviolet (UV) light. These adhesives are commonly used for bonding various materials, including plastics, glass, metal, and rubber. Whether a UV cure cyanoacrylate adhesive is suitable for outdoor applications depends on several factors:
- UV Resistance:UV cure adhesives generally resist UV light, but prolonged exposure to sunlight may cause degradation over time. Some formulations may be more UV-resistant than others, so it’s essential to check the product specifications provided by the manufacturer.
- Temperature Resistance:Outdoor applications often expose materials to various temperatures. Ensure that the UV-cure cyanoacrylate adhesive you choose can withstand the temperature extremes of your specific outdoor environment.
- Moisture Resistance:Outdoor environments may involve exposure to rain, humidity, or other forms of moisture. Selecting an adhesive that offers good moisture resistance is crucial to prevent degradation or loss of bonding strength.
- Substrate Compatibility:Consider the types of materials you need to bond outdoors. UV cure cyanoacrylate adhesives are versatile, but some formulations may be better suited for specific materials.
- Application Conditions:Follow the manufacturer’s recommendations for application conditions. UV cure adhesives typically require proper light exposure for curing. The adhesive may not cure effectively if the application area is consistently shaded.
- Sealing and Protection:In some outdoor applications, it might be necessary to protect the bonded area from direct exposure to sunlight, moisture, or other environmental factors. Consider whether additional sealing or protective measures are needed.
Always refer to the product datasheet or technical specifications provided by the manufacturer for detailed information on the adhesive’s outdoor performance characteristics. You can also contact the manufacturer directly for specific guidance on the suitability of their UV cure cyanoacrylate adhesive for outdoor applications.
What safety precautions should be taken when using UV Cure Cyanoacrylate Adhesive?
UV Cure Cyanoacrylate Adhesive, also known as UV-curing CA adhesive or UV glue, is an adhesive that cures quickly when exposed to ultraviolet (UV) light. While using UV-cure cyanoacrylate adhesive, following safety precautions is essential to ensure individuals’ well-being and achieve the best results. Here are some safety precautions:
Personal Protective Equipment (PPE):
- Wear appropriate PPE, including safety glasses or goggles, to protect your eyes from UV light exposure.
- Consider using gloves to prevent skin contact with the adhesive.
Ventilation:
- Use the adhesive in a well-ventilated area to minimize exposure to fumes.
UV Light Source:
- Use the recommended UV light source specified by the adhesive manufacturer.
- Avoid direct UV light exposure to your eyes, which can cause eye damage.
Skin Protection:
- Minimize skin contact with the adhesive. If contact occurs, wash the affected area with soap and water immediately.
Clothing:
- Avoid contact with clothing, as the adhesive can bond fabric together. If contact occurs, follow the manufacturer’s instructions for removal.
Surfaces:
- Ensure that the surfaces to be bonded are clean, dry, and free from contaminants. Proper surface preparation is crucial for achieving a solid bond.
Storage:
- Store the adhesive in a cool, dry place, away from direct sunlight, and follow the manufacturer’s recommendations for storage conditions.
Read and Follow the Instructions:
- Carefully read and follow the manufacturer’s instructions and safety data sheet (SDS) for your specific UV-cure cyanoacrylate adhesive.
Emergency Preparedness:
- Be aware of emergency procedures in case of accidental exposure or ingestion. Have access to emergency contact information and seek medical attention if necessary.
Keep Out of Reach of Children:
- Store the adhesive in a secure location away from children’s reach.
Disposal:
- Follow proper disposal procedures for the adhesive and any associated materials, following local regulations.
Avoid Overexposure:
- Limit exposure time to the UV light and the adhesive to reduce the risk of skin and eye irritation.
Always consult the specific safety guidelines provided by the UV cure cyanoacrylate adhesive manufacturer, as different products may have specific recommendations and precautions.
Are there specific UV light requirements for curing?
UV-cure cyanoacrylate adhesives, also known as UV-curable instant adhesives, are designed to cure rapidly when exposed to ultraviolet (UV) light. The UV light initiates the curing process, which triggers a photoinitiator in the adhesive to start the polymerization reaction. To achieve optimal curing results, it’s essential to consider specific UV light requirements:
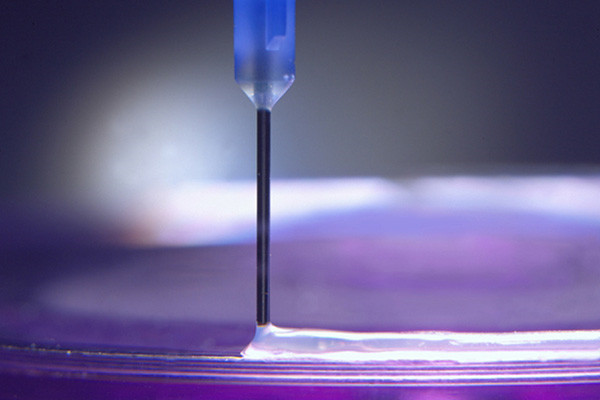
- Wavelength:UV adhesives typically require specific UV light wavelengths for adequate curing. The wavelength is usually in the range of 320 to 400 nanometers (nm). Ensure the UV light source emits light within this range to activate the adhesive properly.
- Intensity:The intensity of the UV light is crucial for efficient curing. The adhesive manufacturer will specify the recommended intensity levels for curing their product. Insufficient UV intensity may result in incomplete curing, affecting the bond strength and performance.
- Exposure Time:The exposure time to UV light is also a critical factor. The adhesive manufacturer will provide guidelines on the recommended exposure time required for complete curing. Following these guidelines is essential to ensure the adhesive reaches its full strength.
- Distance from Light Source:The distance between the UV light source and the adhesive can impact curing. Follow the adhesive manufacturer’s recommendations regarding the optimal distance for curing. Placing the adhesive too far or close to the light source may affect the curing process.
- Substrate Transparency:The transparency of the bonded substrates can influence UV curing effectiveness. Transparent or translucent substrates allow UV light to penetrate and cure the adhesive more efficiently. Opaque materials may require prolonged exposure or additional measures to ensure proper curing.
- Temperature:Some UV-cure adhesives may be sensitive to temperature variations. It’s advisable to check the manufacturer’s specifications for the recommended temperature range during curing. Extreme temperatures can affect the curing process and the overall performance of the adhesive.
Always refer to the technical data sheet or product information provided by the adhesive manufacturer for specific recommendations regarding UV light requirements. These guidelines will help ensure proper curing and optimal UV-cure cyanoacrylate adhesive performance.
What is the shelf life of this adhesive?
The shelf life of UV cure adhesives and traditional cyanoacrylate adhesives can vary based on several factors, including the specific formulation of the adhesive and how it is stored. Here are some general guidelines:
UV Cure Adhesives:
- UV cure adhesives typically have a longer shelf life than traditional cyanoacrylate adhesives.
- Depending on the formulation and packaging, the shelf life can range from several months to a few years.
- Storing UV-cure adhesives in a cool, dark place away from direct sunlight is essential to prevent premature curing.
Cyanoacrylate Adhesives:
- Traditional cyanoacrylate adhesives, commonly known as superglues, have a shorter shelf life compared to UV-cure adhesives.
- The shelf life is usually around 1 to 2 years when stored in a cool, dry place.
- Exposure to air can cause cyanoacrylate adhesives to cure over time, so it’s crucial to keep the containers tightly sealed.
In both cases, manufacturers typically provide an expiration date on the product packaging. Following the recommended storage conditions and using the adhesive within its specified shelf life is essential for optimal performance. If the adhesive has exceeded its shelf life, it may not cure properly or lose effectiveness.
Always check the product information and guidelines provided by the manufacturer for specific details about the shelf life and storage recommendations for the particular adhesive you are using.
Can it be used in medical applications?
The use of adhesives, including UV cure and cyanoacrylate adhesives, in medical applications depends on the specific formulation and intended purpose. Some adhesives are designed and approved for medical use, while others may not meet regulatory standards or pose potential health risks.
- UV Cure Adhesives:
- UV cure adhesives are used in various medical applications, including bonding medical devices, assembling components, and even in some dental procedures.
- Medical-grade UV cure adhesives are formulated to meet specific biocompatibility and safety standards required for medical use.
- These adhesives are often used because of their rapid curing properties and the ability to bond various substrates.
- Cyanoacrylate Adhesives:
- Cyanoacrylate adhesives, commonly known as superglues, have been used in specific medical applications.
- Medical-grade cyanoacrylate adhesives are designed to be biocompatible and suitable for specific medical bonding purposes.
- They have been used in wound closure (though this is less common now with the availability of specialized medical adhesives) and in some dental applications.
It’s important to note that using adhesives in medical applications is subject to strict regulatory requirements. Medical-grade adhesives should comply with standards such as ISO 10993 for biocompatibility. Additionally, the specific use case and intended application should be considered.
Always consult with regulatory authorities, follow relevant guidelines, and choose adhesives explicitly approved for medical use when working on medical devices or applications. Manufacturers of medical-grade adhesives provide detailed information about their products’ biocompatibility, sterilization, and other relevant properties.
Are there post-curing steps required?
The need for post-curing steps after using UV cure adhesives and traditional cyanoacrylate adhesives depends on the project’s specific type of adhesive, application, and requirements. Here’s a general overview of both classes:
UV Cure Adhesives:
Post-Curing Steps:
- Exposure to UV Light:UV cure adhesives typically require exposure to ultraviolet (UV) light for curing. The duration and intensity of UV exposure will depend on the specific adhesive formulation. Some adhesives may require a brief exposure, while others may need longer exposure times.
- Post-Curing:Some applications may benefit from additional post-curing steps after the initial UV exposure. Post-curing can enhance the performance and durability of the bond. It may involve exposing the bonded area to UV light for an extended period or subjecting it to heat.
- Verification:It’s essential to verify that the adhesive has fully cured by checking its physical properties. Manufacturers usually provide guidelines for complete curing, such as checking for hardness, clarity, or other specific characteristics.
Traditional Cyanoacrylate Adhesives:
Post-Curing Steps:
- Instant Curing:One of the advantages of cyanoacrylate adhesives is their ability to cure almost instantly upon contact with surfaces. This rapid curing can eliminate the need for additional post-curing steps in many applications.
- Pressure and Contact:Achieving a solid bond with cyanoacrylate adhesives often involves applying pressure and ensuring close contact between the bonded surfaces. Post-application, maintaining this pressure for a short period can enhance the bond.
- Avoidance of Moisture:Cyanoacrylate adhesives can be sensitive to moisture, interfering with the curing process. Therefore, avoiding exposure to excess moisture during and after application is advisable.
While UV cure adhesives may require specific UV exposure for curing and may benefit from additional post-curing steps, traditional cyanoacrylate adhesives often set rapidly, and their curing process is typically instantaneous. Always refer to the manufacturer’s instructions and recommendations for the adhesive you use to ensure proper curing and bonding.
What is the recommended storage condition?
The recommended storage conditions for UV cure adhesives and cyanoacrylate adhesives (super glue) may vary depending on the product and manufacturer. However, here are some general guidelines:
UV Cure Adhesives:
- Store in a cool, dark place: UV-cure adhesives are sensitive to light, incredibly ultraviolet light. Storing them in a cool, dark place can help prevent premature curing.
- Please keep away from heat: Excessive heat can also accelerate the curing process, so storing UV-cure adhesives away from heat sources is advisable.
Cyanoacrylate Adhesives:
- Store in a cool, dry place: Cyanoacrylate adhesives can degrade when exposed to moisture. Storing them in a relaxed, dry environment can help maintain their effectiveness.
- Seal the container tightly: To prevent water from entering the adhesive container, seal it tightly after each use.
Always refer to the product-specific guidelines provided by the manufacturer. The storage recommendations may be indicated on the product packaging or datasheet. Adhering to the manufacturer’s instructions will help ensure the longevity and proper performance of the adhesives.
Can it be used in high-temperature environments?
The suitability of UV cure adhesives and cyanoacrylate adhesives in high-temperature environments depends on the specific formulation of the adhesive and its intended application. Here’s a general overview:
- UV Cure Adhesives:
- UV cure adhesives can have varying temperature resistance depending on the formulation. Some UV-cure adhesives are designed to withstand high temperatures, while others may not suit such conditions.
- It’s essential to check the product datasheet or technical specifications provided by the manufacturer for information on the temperature resistance of the specific UV cure adhesive you are using.
- Some UV cure adhesives may be suitable for applications in moderate to high-temperature environments, but exceeding the recommended temperature limits can affect their performance.
- Cyanoacrylate Adhesives:
- Cyanoacrylate adhesives generally have limited resistance to high temperatures. They can soften or lose their bonding strength when exposed to elevated temperatures.
- The typical temperature resistance for standard cyanoacrylate adhesives is around 180°F to 250°F (82°C to 121°C).
- Consider using specialized cyanoacrylate formulations designed for heat resistance for applications in high-temperature environments. Some manufacturers offer heat-resistant or high-temperature cyanoacrylate adhesives with improved performance at elevated temperatures.
Always refer to the product documentation provided by the adhesive manufacturer for accurate information on temperature resistance and suitability for specific environmental conditions. If high-temperature resistance is critical for your application, consult the manufacturer or choose an adhesive specifically formulated for such requirements.
Can it be used in high-temperature environments?
The suitability of UV cure adhesives and cyanoacrylate adhesives in high-temperature environments depends on the specific formulation of the adhesive and its intended application. Here’s a general overview:
UV Cure Adhesives:
- UV cure adhesives can have varying temperature resistance depending on the formulation. Some UV-cure adhesives are designed to withstand high temperatures, while others may not suit such conditions.
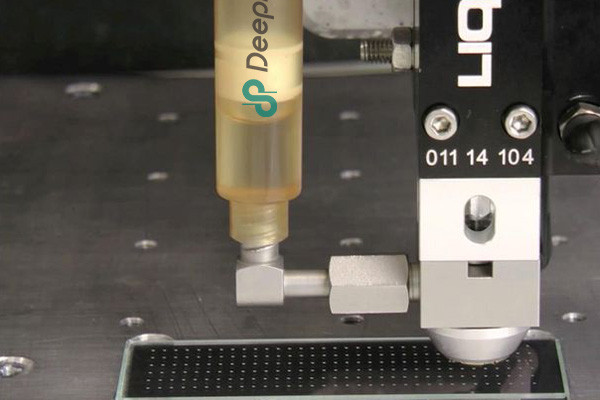
- It’s essential to check the product datasheet or technical specifications provided by the manufacturer for information on the temperature resistance of the specific UV cure adhesive you are using.
- Some UV cure adhesives may be suitable for applications in moderate to high-temperature environments, but exceeding the recommended temperature limits can affect their performance.
Cyanoacrylate Adhesives:
- Cyanoacrylate adhesives generally have limited resistance to high temperatures. They can soften or lose their bonding strength when exposed to elevated temperatures.
- The typical temperature resistance for standard cyanoacrylate adhesives is around 180°F to 250°F (82°C to 121°C).
- Consider using specialized cyanoacrylate formulations designed for heat resistance for applications in high-temperature environments. Some manufacturers offer heat-resistant or high-temperature cyanoacrylate adhesives with improved performance at elevated temperatures.
Always refer to the product documentation provided by the adhesive manufacturer for accurate information on temperature resistance and suitability for specific environmental conditions. If high-temperature resistance is critical for your application, consult the manufacturer or choose an adhesive specifically formulated for such requirements.
Can it be used in high-temperature environments?
The suitability of UV cure adhesives and cyanoacrylate adhesives in high-temperature environments depends on the specific formulation of the adhesive and its intended application. Here’s a general overview:
UV Cure Adhesives:
- UV cure adhesives can have varying temperature resistance depending on the formulation. Some UV-cure adhesives are designed to withstand high temperatures, while others may not suit such conditions.
- It’s essential to check the product datasheet or technical specifications provided by the manufacturer for information on the temperature resistance of the specific UV cure adhesive you are using.
- Some UV cure adhesives may be suitable for applications in moderate to high-temperature environments, but exceeding the recommended temperature limits can affect their performance.
Cyanoacrylate Adhesives:
- Cyanoacrylate adhesives generally have limited resistance to high temperatures. They can soften or lose their bonding strength when exposed to elevated temperatures.
- The typical temperature resistance for standard cyanoacrylate adhesives is around 180°F to 250°F (82°C to 121°C).
- Consider using specialized cyanoacrylate formulations designed for heat resistance applications in high-temperature environments. Some manufacturers offer heat-resistant or high-temperature cyanoacrylate adhesives with improved performance at elevated temperatures.
Always refer to the product documentation provided by the adhesive manufacturer for accurate information on temperature resistance and suitability for specific environmental conditions. If high-temperature resistance is critical for your application, consult the manufacturer or choose an adhesive specifically formulated for such requirements.
What are the critical differences between UV Cure and traditional cyanoacrylate adhesives?
UV-cure adhesives and traditional cyanoacrylate adhesives are both types of adhesives, but they have some critical differences, particularly in terms of their curing mechanisms. Here are the key distinctions:
Curing Mechanism:
- UV Cure Adhesives:These adhesives cure or harden when exposed to ultraviolet (UV) light. The curing process is initiated by UV light, typically in the 200-400 nm wavelength range. This allows for precise control over the curing process, as it only occurs when and where UV light is applied.
- Cyanoacrylate Adhesives:Traditional cyanoacrylate adhesives, often known as superglues, cure through a reaction with moisture in the air. The presence of water activates the adhesive and initiates the polymerization process, forming a solid bond.
Curing Speed:
- UV Cure Adhesives:UV-cure adhesives generally cure very quickly, often within seconds to minutes, depending on the UV light source’s intensity and the adhesive layer’s thickness.
- Cyanoacrylate Adhesives:Cyanoacrylate adhesives also cure rapidly but may take longer than UV-cure adhesives. The curing time is influenced by factors such as humidity and temperature.
Application and Flexibility:
- UV Cure Adhesives:UV-cure adhesives are often used in applications where precise control over the curing process is essential. They are suitable for bonding materials that may be sensitive to heat, as the curing is achieved without generating significant heat.
- Cyanoacrylate Adhesives:Cyanoacrylate adhesives are versatile and can bond various materials, including plastics, metals, and rubber. They are known for their quick bonding ability but may generate heat during curing.
Bond Strength:
- UV Cure Adhesives:UV-cure adhesives can provide strong bonds, but the strength may vary depending on the specific formulation and the bonded materials.
- Cyanoacrylate Adhesives:Cyanoacrylate adhesives generally provide solid and rigid bonds. The bond strength is often influenced by the substrate and the conditions under which the adhesive cures.
Environmental Factors:
- UV Cure Adhesives:UV-cure adhesives may be sensitive to UV light exposure, so care must be taken to shield them from sunlight or other UV sources before use.
- Cyanoacrylate Adhesives:Cyanoacrylate adhesives may be more tolerant of environmental conditions, but their curing can be affected by variations in humidity and temperature.
While both UV-cure and traditional cyanoacrylate adhesives offer fast curing times and strong bonds, the choice between them depends on the application’s specific requirements, the materials being bonded, and the desired characteristics of the final bond. UV-cure adhesives are particularly advantageous when precise control over curing is crucial.
Are there any innovative uses or emerging trends with UV Cure Cyanoacrylate Adhesive?
Keep in mind that developments may have occurred since then. Here are some potential innovative uses and emerging trends with UV cure cyanoacrylate adhesive:
Electronic Component Bonding:
- UV cure cyanoacrylate adhesives are being explored for bonding delicate electronic components. The quick curing time is advantageous in assembly processes, and the adhesive’s ability to connect various materials makes it suitable for electronics manufacturing.
Medical Device Assembly:
- The medical industry is increasingly looking into UV-cure cyanoacrylate adhesives for bonding and assembling medical devices. The rapid curing process is advantageous in the production of disposable medical devices.
Optical Bonding:
- UV cure cyanoacrylate adhesives bond optical components, such as lenses and displays. The adhesive’s clarity and quick curing time make it suitable for applications where optical properties are crucial.
Automotive Applications:
- UV cure cyanoacrylate adhesives can be used in automotive assembly for bonding components quickly and efficiently. This includes applications in interior and exterior parts and bonding electronic components.
Flexible Substrates:
- The flexibility of UV-cure cyanoacrylate adhesives makes them suitable for bonding flexible substrates, such as in the production of flexible electronics and wearable devices.
3D Printing Post-Processing:
- UV cure cyanoacrylate adhesives are used in post-processing steps for 3D printed parts. They can be applied to bond and strengthen layers, improving the overall strength and durability of the printed object.
UV Cure Cyanoacrylate Tapes:
- Adhesive tapes that use UV-cure cyanoacrylate technology are emerging. These tapes can be used for various applications, providing a convenient and quick bonding solution.
Improved Formulations:
- Ongoing research may lead to improved formulations of UV-cure cyanoacrylate adhesives, addressing specific industry needs such as enhanced adhesion to certain substrates, increased flexibility, or resistance to harsh environmental conditions.
Always check for the latest developments and consult with industry experts to get the most up-to-date information on innovative uses and emerging trends in UV cure cyanoacrylate adhesive technology.
Conclusion:
In conclusion, UV Cure Cyanoacrylate Adhesive is a game-changer in the adhesive industry, offering rapid bonding solutions with the added benefit of UV curing. Whether you are working on intricate projects or demanding applications, this adhesive provides a reliable and efficient bonding solution. Stay informed with our guide to make the most of this innovative adhesive technology.
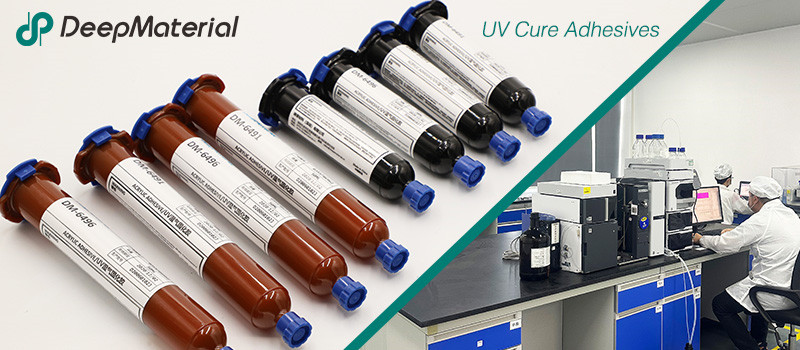
DeepMaterial
Based on the core technology of adhesives, DeepMaterial has developed adhesives for chip packaging and testing, circuit board level adhesives, and adhesives for electronic products. Based on adhesives, it has developed protective films, semiconductor fillers, and packaging materials for semiconductor wafer processing and chip packaging and testing. More…
UV Curing Adhesives
UV light cure have a number of benefits making them a popular choice among many product assembly and manufacturing applications. Many UV light cure adhesives can provide a nearly instantaneous bond to difficult substrates like glass and plastic. UV cure adhesives often require an accelerator or UV light for a bond to form.
Adhesive Blogs & News
The latest adhesive industry science and technology, Deepmaterial news, and market trends and forecasts.
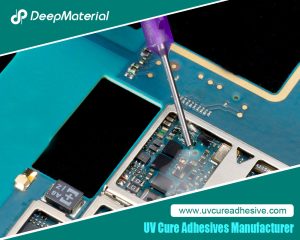
Biocompatibility of LED UV Glue Adhesive and Its Application Potential in Medical and Food Packaging Fields
Biocompatibility of LED UV Glue Adhesive and Its Application Potential in Medical and Food Packaging Fields LED UV glue adhesive has been widely applied in numerous fields due to its advantages such as rapid curing and easy operation. However, in fields with stringent safety requirements like medical and food packaging, its biocompatibility after curing becomes
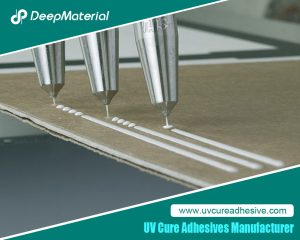
Biocompatibility of LED UV Glue Adhesive and Its Application Potential in Medical and Food Packaging Fields
Biocompatibility of LED UV Glue Adhesive and Its Application Potential in Medical and Food Packaging Fields LED UV glue adhesive has been widely applied in numerous fields due to its advantages such as rapid curing and easy operation. However, in fields with stringent safety requirements like medical and food packaging, its biocompatibility after curing
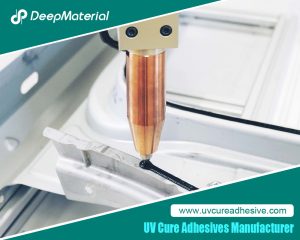
Exploring the Environmental Performance of UV Glue and Strategies for Optimizing Odor and VOC Content
Exploring the Environmental Performance of UV Glue and Strategies for Optimizing Odor and VOC Content UV glue, as an adhesive that achieves rapid curing through ultraviolet (UV) light irradiation, has been widely applied in numerous fields such as electronics, optics, healthcare, and automobiles, thanks to its advantages of fast curing speed, high bonding strength, and
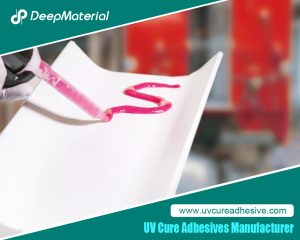
Compatibility Analysis and Countermeasures of LED UV Glue with Automated Production Equipment
Compatibility Analysis and Countermeasures of LED UV Glue with Automated Production Equipment LED UV glue has been widely used in modern manufacturing due to its advantages such as fast curing speed, high bonding strength, and environmental friendliness. However, in the automated production process, if there are problems with the adaptability between the glue and equipment
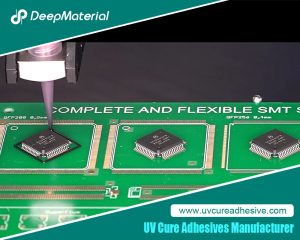
Influence of Viscosity and Thixotropy of Glue on the Quality of Glue Dots in the Dispensing Process and Solutions
Influence of Viscosity and Thixotropy of Glue on the Quality of Glue Dots in the Dispensing Process and Solutions The dispensing process is an important part of the application of LED UV glue adhesive, and the quality of this process directly affects the final performance of the product. The physical properties of the glue,
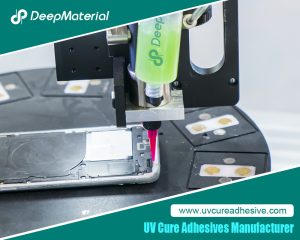
Aging Mechanism and Modification Strategies of LED UV Glue under Long-term Ultraviolet Irradiation
Aging Mechanism and Modification Strategies of LED UV Glue under Long-term Ultraviolet Irradiation LED UV glue, with its advantages of fast curing speed, high bonding strength, and environmental friendliness, has been widely used in fields such as optical device packaging, electronic assembly, and medical devices. However, in scenarios where it is exposed to ultraviolet environments