- Home
- >
- Material Bonding
- >
- UV Cure Adhesive For Polypropylene
UV Cure Adhesive For Polypropylene
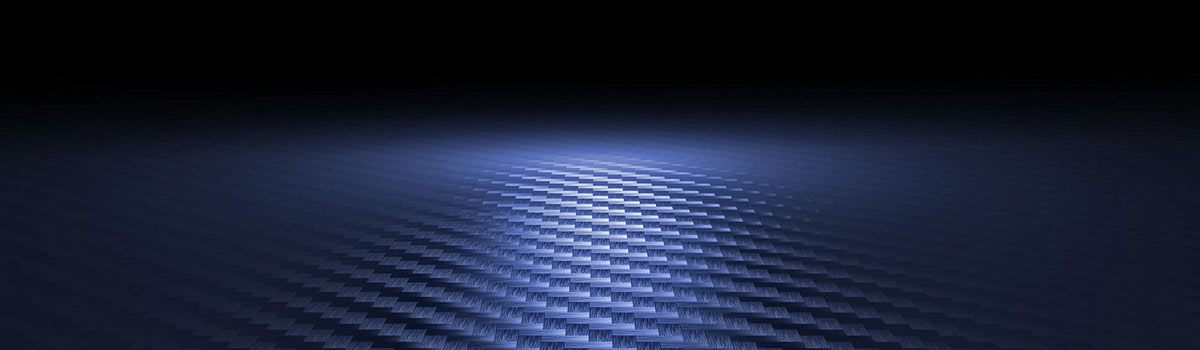
Introduction: Welcome to our comprehensive guide on UV Cure Adhesive, tailored explicitly for Polypropylene. UV-curable adhesives have emerged as pioneers in bonding solutions, providing efficient and rapid bonding for various materials. Regarding Polypropylene, a material known for its challenging adhesive properties, UV-cure adhesives present a groundbreaking solution. This category explores the unique characteristics, applications, and advantages of UV Cure Adhesive for Polypropylene, shedding light on the transformative capabilities of this cutting-edge bonding technology.
Table of Contents
ToggleWhat makes Polypropylene a challenging material for adhesion?
Polypropylene (PP) can be challenging for adhesion due to several inherent properties of the material:
- Low Surface Energy:Polypropylene has a low surface energy, so it doesn’t readily form strong bonds with other materials. This soft surface energy makes it difficult for adhesives to wet and spread over the surface, leading to poor adhesion.
- Chemical Inertness:Polypropylene is chemically inert and does not readily react with other substances. Adhesives often rely on chemical reactions to create strong bonds, and the lack of reactive sites on Polypropylene’s surface makes it resistant to forming adhesive bonds.
- Non-Polar Nature:Polypropylene is a non-polar polymer, and many adhesives are designed to adhere well to polar surfaces. The non-polar nature of Polypropylene limits the available bonding sites for adhesives that rely on polar interactions.
- Crystalline Structure:Polypropylene is crystalline, producing a relatively smooth and impervious surface. The lack of surface irregularities makes it harder for adhesives to lock onto the substrate mechanically.
To improve adhesion to Polypropylene, specific surface treatments and techniques may be employed:
- Surface Activation:Methods such as corona treatment or plasma treatment can increase the surface energy of Polypropylene, making it more amenable to adhesion.
- Chemical Primers:Apply primers or adhesion promoters designed to enhance Polypropylene’s bonding properties, providing a more reactive surface.
- Mechanical Roughening:Abrading or roughening the surface of Polypropylene mechanically increases the surface area and provides better bonding sites for adhesives.
- Specialized Adhesives:Some adhesives are specifically formulated to bond well with Polypropylene. These adhesives often contain additives or have formulations addressing the challenges of Polypropylene’s surface properties.
It’s important to note that the success of adhesion to Polypropylene depends on the specific application, the type of adhesive used, and the environmental conditions the bonded materials will experience.
How does UV Cure Adhesive differ from traditional bonding methods?
UV cure adhesive, also known as ultraviolet (UV) light-curable adhesive, differs from traditional bonding methods in several ways. Here are some key distinctions:
Curing Mechanism:
- UV Cure Adhesive:UV cure adhesives rely on a photochemical reaction initiated by exposure to ultraviolet light. When the adhesive is exposed to UV light, it undergoes a rapid curing process, transforming from a liquid or gel into a solid state.
- Traditional Bonding Methods:Traditional bonding methods, such as mechanical fasteners, welding, or chemical adhesives, often rely on processes like evaporation of solvents, chemical reactions, or physical interlocking.
Speed of Cure:
- UV Cure Adhesive:UV cure adhesives typically cure very quickly, often within seconds to minutes, depending on factors such as the UV light’s intensity and the adhesive layer’s thickness.
- Traditional Bonding Methods:Traditional methods may take longer to achieve a strong bond, especially if they involve waiting for chemical reactions or adhesives to dry or cure over an extended period.
Precision and Control:
- UV Cure Adhesive:UV curing provides precise control over the curing process. The adhesive remains in a liquid or gel state until exposed to UV light, allowing for accurate positioning and alignment before curing.
- Traditional Bonding Methods:Some methods may offer less precision and control, especially if they involve fixing or setting processes over time.
Bond Strength and Properties:
- UV Cure Adhesive:UV-cured bonds can exhibit high strength and durability. The fast curing process minimizes the chances of contamination, and the resulting bond may have excellent chemical and environmental resistance.
- Traditional Bonding Methods:The strength and properties of bonds formed through conventional methods depend on the specific technique and materials used. Some traditional methods may offer different levels of consistency or resistance to environmental factors.
Application Flexibility:
- UV Cure Adhesive:UV cure adhesives are suitable for bonding various materials, including plastics, glass, metals, and certain rubbers. The precise application of UV light allows for selective curing in specific areas.
- Traditional Bonding Methods:Different methods may be more suitable for explicit materials or applications. Welding, for example, may be ideal for metals, while certain adhesives may be optimized for bonding particular substrates.
Environmental Considerations:
- UV Cure Adhesive:UV curing is often considered more environmentally friendly as it typically involves little to no volatile organic compounds (VOCs) and produces minimal waste.
- Traditional Bonding Methods:Some traditional bonding methods may include using solvents, adhesives with VOCs, or other materials with environmental implications.
It’s important to note that the choice between UV cure adhesive and traditional bonding methods depends on the application’s specific requirements, the materials being bonded, and other factors such as production speed and cost considerations.
What are the critical features of UV Cure Adhesive for Polypropylene?
UV cure adhesives for bonding polypropylene (PP) must possess critical features to ensure adequate adhesion and performance. Polypropylene is known for its low surface energy, making bonding challenging. Here are some essential elements of UV cure adhesives for polypropylene:
Low Viscosity:
- UV cure adhesives for polypropylene should have a low viscosity to ensure good wetting and penetration into the substrate. This helps maximize the contact area between the adhesive and the polypropylene surface.
Adhesion Promoters:
- Some UV cure adhesives include adhesion promoters or surface modifiers specifically designed for polypropylene. These additives enhance the affinity of the adhesive to the polypropylene surface.
Low Shrinkage:
- Low shrinkage during the curing process is essential to prevent stress on the bond line. Excessive shrinkage could lead to reduced bond strength and potential failure.
Flexibility:
- Polypropylene is a flexible material, and the adhesive should be able to accommodate the movement and flexibility of the substrate without cracking or delamination.
Chemical Resistance:
- The adhesive should resist chemicals that may come in contact with the bonded assembly. This is particularly important in applications that expose the related parts to harsh environments.
Fast Cure Time:
- UV cure adhesives are known for their rapid cure times, which is advantageous for high-throughput manufacturing processes. Quick curing helps in minimizing production time and improving efficiency.
UV Transparency:
- The adhesive must be transparent or transmit UV light effectively to ensure proper curing. This is crucial for achieving solid and durable bonds.
Temperature Resistance:
- The cured adhesive should withstand the temperature conditions to which the bonded assembly may be exposed during its service life.
Surface Preparation:
- Adequate surface preparation is essential for bonding polypropylene. To enhance adhesion, some adhesives may require pre-treatment of the polypropylene surface, such as corona treatment or primers.
Optimized Formulation:
- UV cure adhesives designed for polypropylene should have a formulation optimized for bonding this specific substrate. This may involve a balance of different chemical components to address the challenges of polypropylene.
It’s important to note that selecting a UV cure adhesive for polypropylene should be based on the application’s specific requirements, and testing should be conducted to ensure compatibility and performance. Manufacturers often provide technical data sheets and guidelines for properly using their products.
Can UV Cure Adhesive withstand harsh environmental conditions?
UV cure adhesives, also known as ultraviolet-curing adhesives, cure or harden when exposed to ultraviolet (UV) light. These adhesives have several advantages, such as rapid curing, minimal heat generation, and bonding of various substrates. However, their performance under harsh environmental conditions depends on the specific formulation and intended application.
UV cure adhesives can exhibit good resistance to certain environmental factors, but their durability may vary based on characteristics such as:
- UV Resistance:While UV cure adhesives cure under UV light, prolonged exposure to UV radiation can sometimes lead to degradation. Some formulations include UV stabilizers to enhance resistance to UV exposure.
- Temperature Resistance:Some UV-cure adhesives may have limitations in extreme temperature conditions. It’s essential to check the temperature range specified by the manufacturer to ensure the adhesive can withstand the intended environmental conditions.
- Chemical Resistance:The resistance of UV cure adhesives to chemicals depends on the specific formulation. Some adhesives may be more resistant to chemicals, solvents, or corrosive substances than others.
- Moisture Resistance:Many UV cure adhesives provide good moisture resistance, but this can vary based on the formulation. If an application involves water or high humidity exposure, choosing an adhesive with appropriate moisture resistance properties is crucial.
- Mechanical Strength:UV cure adhesives can offer excellent bonding strength, but the specific application and the forces the adhesive will be subjected to should be considered. Some formulations may have better resistance to mechanical stress and impact.
- Substrate Compatibility:The ability of UV cure adhesives to bond to specific substrates varies. It’s essential to choose an adhesive that is compatible with the materials being bonded.
To ensure the UV cure adhesive meets the required performance criteria in harsh environmental conditions, it’s recommended to consult with the adhesive manufacturer or supplier. They can provide specific information on the adhesive’s capabilities, limitations, and compatibility with the intended operating conditions. Additionally, conducting thorough testing or considering alternative adhesive technologies may be necessary for critical applications in extreme environments.
What industries benefit most from UV Cure Adhesive on Polypropylene?
UV cure adhesives are versatile and find applications in various industries due to their fast curing time, strong bonding properties, and suitability for bonding different substrates. Regarding bonding polypropylene, UV cure adhesives can offer several advantages, including bond strength, clarity, and minimal heat generation during curing. Some industries that benefit from UV cure adhesives on polypropylene include:
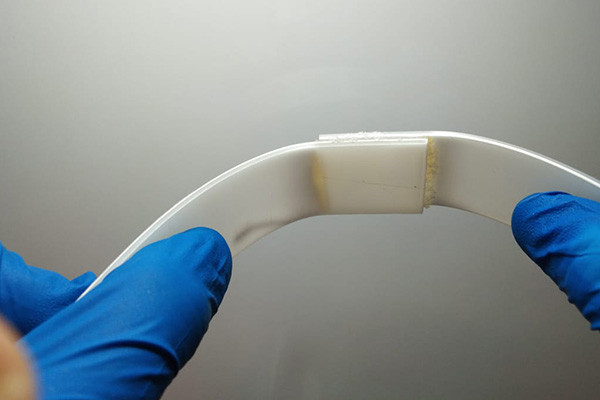
- Medical Devices:UV cure adhesives are commonly used to assemble medical devices, particularly those made from polypropylene. The quick curing time and the ability to bond transparent materials make them suitable for applications like clicking plastic components in medical instruments.
- Electronics:UV cure adhesives are used in the electronics industry for connecting various components, including polypropylene. The rapid curing process is advantageous for high-volume production, and the adhesive’s ability to connect dissimilar materials is beneficial for electronic assemblies.
- Automotive:UV cure adhesives are employed in the automotive industry for connecting plastic components, including polypropylene parts. This is useful in assembling interior components, exterior trims, and other vehicle plastic elements.
- Packaging:UV cure adhesives are used in the packaging industry for bonding plastic materials, including polypropylene. They can assemble packaging components, ensuring a strong and rapid bond for various packaging applications.
- Optical Industry:UV cure adhesives are commonly used in the optical industry for bonding lenses and other optical components. The clarity of the adhesive and its ability to bond transparent materials, such as polypropylene, make it suitable for optical applications.
- Consumer Electronics:The consumer electronics industry often utilizes UV-cure adhesives for clicking plastic components in electronic devices. Quick curing time and strong bonds are advantageous for efficient manufacturing processes.
- Aerospace:UV cure adhesives may be used in specific aerospace applications where rapid bonding of lightweight materials, such as polypropylene, is required. However, the selection of adhesives in aerospace applications is highly regulated, and compliance with specific industry standards is crucial.
It’s important to note that the suitability of UV cure adhesives for polypropylene bonding depends on various factors, including the specific formulation of the adhesive and the intended application. Additionally, industry standards and regulations may influence the choice of adhesives in specific sectors. Before selecting an adhesive for a particular application, it’s recommended to consult with adhesive manufacturers and adhere to industry-specific guidelines and requirements.
Are there specific considerations for surface preparation when using UV Cure Adhesive?
Surface preparation is crucial when UV cure adhesives to ensure proper adhesion and optimal performance. Here are some general considerations:
Cleanliness:
- Ensure that the surfaces to be bonded are thoroughly clean. Any contaminants, such as dirt, grease, or oils, can interfere with the bonding process and reduce adhesion.
Surface Activation:
- Some substrates may benefit from surface activation to enhance adhesion. This can be achieved through methods such as plasma treatment or corona treatment. Activated surfaces provide better bonding sites for the adhesive.
Surface Roughness:
- In some cases, slightly roughening the surfaces can improve adhesion. However, the degree of roughness should be within the adhesive manufacturer’s recommendations. Excessive roughening may lead to stress concentrations or reduce the effectiveness of the adhesive.
Compatibility:
- Ensure that the substrate materials are compatible with the UV cure adhesive. Some materials may inhibit the curing process or react negatively with the adhesive, affecting its performance.
Moisture and Contaminant Prevention:
- UV-cure adhesives are sensitive to moisture. Ensure that the surfaces are dry and free from any moisture before applying the adhesive. Additionally, protect the adhesive from exposure to ambient light during application to prevent premature curing.
Surface Energy:
- Consider the surface energy of the substrates. Adhesion can be improved if the substrate’s surface energy matches that of the adhesive. Low-energy surfaces may require additional treatment or primers.
UV Transmission:
- Ensure the substrates allow sufficient UV light transmission for the adhesive to cure properly. Opaque or thick materials may require longer exposure times or different curing methods.
Surface Temperature:
- UV cure adhesives may have temperature limitations. Ensure that the substrate temperature is within the recommended range for proper curing. Extreme temperatures can affect the curing process and final bond strength.
Adhesive Compatibility:
- Verify that the specific UV cure adhesive suits the intended substrates and application conditions. Different formulations may be designed for particular materials or environmental requirements.
Always refer to the manufacturer’s guidelines and recommendations for surface preparation, as these can vary depending on the specific UV cure adhesive used. Additionally, perform adhesion tests on representative samples to ensure that the chosen adhesive meets the performance requirements for your application.
How does the curing process of UV adhesives contribute to bond strength?
The curing process of UV (ultraviolet) adhesives plays a crucial role in contributing to bond strength. UV adhesives are adhesives that cure or harden when exposed to ultraviolet light. The curing process involves polymerization reactions that form a solid and durable bond between the bonded surfaces. Here’s how the curing process contributes to bond strength:
Initiation of Polymerization:
- UV adhesives typically contain photoinitiators, substances that absorb UV light and initiate the polymerization process. When the adhesive is exposed to UV light, these initiators activate, starting the polymerization reaction.
Cross-Linking and Chain Formation:
- Polymerization involves the formation of molecular chains from monomers present in the adhesive. Cross-linking occurs as these chains interconnect, creating a three-dimensional network structure. This network enhances the adhesive’s strength and stability.
Chemical Bond Formation:
- Chemical bonds are formed between the adhesive and the substrate surfaces during polymerization. These bonds may include covalent bonds or other intermolecular solid forces, depending on the chemistry of the adhesive and the materials being bonded.
Uniform and Consistent Curing:
- UV curing is typically rapid, allowing for quick and uniform adhesive curing. This uniformity contributes to consistent bond strength across the entire bonded area. It minimizes the likelihood of weak spots or uneven curing that could compromise the bond.
Reduced Thermal Stress:
- UV curing is a low-temperature process compared to some other curing methods. This is particularly beneficial when bonding heat-sensitive materials. The reduced thermal stress during curing helps maintain the integrity of the related materials and contributes to the overall bond strength.
Minimal Residual Stress:
- UV adhesives often produce minimal residual stress during the curing process. This is advantageous as excessive residual stress can lead to deformation or damage of the bonded materials. The absence of such stress contributes to the longevity and reliability of the bond.
Curing in Thin Layers:
- UV adhesives can cure in thin layers, making them suitable for applications where precision and satisfactory bonding are essential. The ability to heal in thin layers contributes to high bond strength, especially in applications where a thin bond line is desirable.
The curing process of UV adhesives contributes to bond strength by initiating polymerization, facilitating the formation of a solid and uniform molecular network, promoting chemical bonds between the adhesive and substrates, and minimizing thermal and residual stresses. The result is a durable and reliable bond suitable for various industrial applications.
Can UV Cure Adhesive be used for both flexible and rigid Polypropylene applications?
UV cure adhesives can be used for bonding both flexible and rigid Polypropylene (PP) applications. Still, it’s essential to choose the right type of UV adhesive formulation based on the specific characteristics of the Polypropylene substrate and the intended application.
Polypropylene is known for having low surface energy, making it challenging for adhesives to adhere effectively. To bond Polypropylene successfully, it’s recommended to use adhesives designed to bond to low-energy surfaces. Some UV cure adhesives are formulated with particular adhesion promoters or primers to enhance bonding on substrates with low surface energy.
Here are some considerations for using UV cure adhesives with Polypropylene:
Surface Preparation:
- Clean the Polypropylene surface thoroughly to remove contaminants, oils, or residues that might hinder adhesion.
- Sometimes, a surface treatment or primer may be recommended to improve adhesion. Ensure the primer is compatible with the Polypropylene and UV adhesive.
Adhesive Selection:
- Choose a UV cure adhesive such as polypropylene for bonding low-energy surfaces.
- Some adhesives are designed to be more flexible, making them suitable for connecting flexible Polypropylene, while others may be better for rigid applications.
Compatibility:
- Ensure that the UV adhesive is compatible with both the flexible and inflexible forms of Polypropylene you are working with.
UV Light Exposure:
- UV cure adhesives require exposure to ultraviolet (UV) light for curing. Ensure that the adhesive receives adequate UV light exposure to achieve a complete cure.
Testing:
- Before full-scale production, conducting small-scale tests is advisable to confirm the bond strength, flexibility, and other relevant properties of the adhesive on your specific Polypropylene substrate.
Always refer to the manufacturer’s guidelines and data sheets for the UV adhesive you plan to use. If in doubt, consult with the adhesive manufacturer or a technical expert to ensure the selected UV cure adhesive is suitable for your specific flexible or rigid Polypropylene application.
Are there limitations or constraints when using UV Cure Adhesive on Polypropylene?
UV-cure adhesives can be effective for bonding various substrates, but there are some limitations and constraints when using them on polypropylene (PP). Polypropylene is a thermoplastic polymer known for its low surface energy and chemical resistance, which can pose challenges for adhesive bonding. Here are some considerations:
Surface Energy:
- Polypropylene has a low surface energy, which makes it difficult for adhesives to wet and bond effectively. UV-cure adhesives may struggle to form strong bonds on low-energy surfaces like polypropylene.
Surface Treatment:
- Surface treatment of polypropylene is often required to enhance adhesion. Techniques such as corona or flame treatment can increase the surface energy and improve the adhesion of UV-cure adhesives.
Adhesion Promoters:
- Adhesion promoters or primers designed with polypropylene may be necessary to facilitate bonding. These substances help create a more favorable surface for the adhesive to adhere to.
Cure Depth:
- UV-cure adhesives rely on exposure to ultraviolet light for curing. The ability of UV light to penetrate through thick or opaque materials can be limited. Ensure that the adhesive receives adequate UV light exposure for proper curing.
Temperature Sensitivity:
- UV-cure adhesives can be sensitive to temperature variations. Some formulations may perform poorly at extreme temperatures. It’s essential to consider the intended application conditions.
Chemical Resistance:
- Polypropylene is resistant to many chemicals, including some adhesive components. Ensure that the chosen adhesive is chemically compatible with polypropylene and will provide the required performance over time.
Flexibility and Mechanical Properties:
- Consider the flexibility and mechanical properties of the cured adhesive to the application’s needs. Different UV-cure adhesive formulations may have varying levels of flexibility and strength.
Testing:
- Always conduct thorough testing under the specific conditions of your application to ensure the adhesive’s performance on polypropylene. Real-world conditions, such as stress, temperature fluctuations, and chemical exposure, should be considered.
It’s essential to consult with the adhesive manufacturer for guidance on selecting the appropriate UV-cure adhesive for bonding polypropylene and to follow their recommendations regarding surface preparation and application conditions. Testing the bond strength and durability in your specific application conditions is crucial to ensure the success of the adhesive bonding process.
What role does wavelength play in the curing process of UV adhesives?
In the curing process of UV (ultraviolet) adhesives, wavelength plays a crucial role as it determines the energy level of the UV light used for curing. UV adhesives typically contain photoinitiators, compounds that absorb UV light and undergo a chemical reaction, initiating the polymerization of the adhesive.
The wavelength of UV light is measured in nanometers (nm), and different photoinitiators are sensitive to specific ranges of UV wavelengths. Therefore, selecting the appropriate wavelength is essential for adequate curing. The two main categories of UV light relevant to adhesive curing are UVA (320-400 nm) and UVB (280-320 nm).
Here’s how wavelength affects the curing process:
- Matching the Photoinitiator: UV adhesives are formulated with specific photoinitiators that respond to certain UV wavelengths. The light source must emit UV radiation at the wavelength the photoinitiator is sensitive to. If the wavelength is outside the optimal range for the photoinitiator, the curing process may need to be more efficient and complete.
- Penetration Depth: Different wavelengths penetrate materials to varying depths. Shorter wavelengths (e.g., UVB) have higher energy but lower penetration depth, while longer wavelengths (e.g., UVA) penetrate deeper. The choice of wavelength depends on the adhesive and the application. For instance, if bonding occurs between layers of materials, a wavelength with better penetration may be preferred.
- Surface Cure vs. Through-Cure: Surface curing involves hardening only the outer layer of the adhesive, while through-curing extends through the entire thickness. The wavelength selection can influence whether surface cure, through-cure, or both are achieved.
- Substrate Compatibility: The bonded materials may have different levels of UV transparency. The wavelength should be chosen to match the transparency of the materials to ensure adequate curing throughout the bonded interface.
- Intensity and Exposure Time: The intensity of the UV light, along with the exposure time, also influences the curing process. The correct wavelength, intensity, and exposure time combination is crucial for achieving the desired mechanical properties and bond strength.
Understanding the role of wavelength in the curing process of UV adhesives is essential for optimizing the adhesive’s performance. The selection of the appropriate UV wavelength should be based on the adhesive formulation, substrate characteristics, and the desired curing depth.
Can UV Cure Adhesive be used for bonding dissimilar materials to Polypropylene?
UV cure adhesives are versatile and can bond with various materials, including Polypropylene. However, successful bonding of dissimilar materials to Polypropylene may require careful consideration of the specific adhesive properties and surface preparation.
Polypropylene is a low-surface-energy material, which can make adhesion challenging. Here are some factors to consider when using UV cure adhesive for bonding dissimilar materials to Polypropylene:
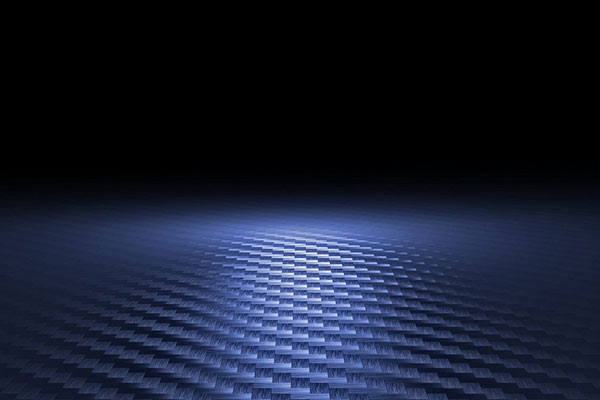
Surface Preparation:
- Polypropylene surfaces should be cleaned to remove contaminants, oils, or residues. This can be done using a suitable solvent or a surface treatment method like corona or plasma treatment to increase surface energy and enhance adhesion.
Adhesive Selection:
- Choose a UV cure adhesive compatible with Polypropylene and the dissimilar material. Some adhesives may have better adhesion properties to specific substrates, so check the manufacturer’s recommendations or conduct tests.
Adhesion Promoters:
- Adhesion promoters may enhance the bonding between Polypropylene and the adhesive. These substances improve the wetting of the adhesive on the substrate surface, promoting better adhesion.
Testing and Validation:
- Before full-scale production, it’s essential to conduct small-scale tests to ensure the effectiveness of the UV cure adhesive for the specific combination of materials. Adhesion testing should be performed under conditions similar to the intended application.
Curing Conditions:
- Follow the recommended curing conditions specified by the adhesive manufacturer. Proper UV exposure is crucial for achieving maximum bond strength.
Temperature and Environmental Conditions:
- Consider the temperature and environmental conditions to which the bonded materials will be exposed. Some adhesives may have temperature or chemical resistance limitations.
Flexibility and Thermal Expansion:
- Consider the flexibility and thermal expansion characteristics of both Polypropylene and the dissimilar material to ensure that the bonded joint can withstand the intended service conditions.
Always refer to the technical data sheets and guidelines provided by the adhesive manufacturer for specific recommendations and compatibility information. Additionally, conducting adhesion tests on a small scale before full-scale production is advisable to ensure the suitability of the chosen UV cure adhesive for your specific application.
Are there safety precautions to consider when working with UV Cure Adhesive?
Working with UV cure adhesives requires specific safety precautions to ensure individuals’ well-being and achieve proper results. Here are some general safety guidelines to consider:
Protective Equipment:
- Wear appropriate personal protective equipment (PPE), including safety glasses or goggles to protect your eyes from UV radiation.
- Wear gloves to prevent direct contact with the adhesive.
UV Exposure:
- Avoid direct exposure of skin and eyes to UV light. UV cure adhesives typically use ultraviolet light to cure, and prolonged exposure can be harmful.
Ventilation:
- Work in a well-ventilated area or use local exhaust ventilation to minimize fume exposure.
Skin Contact:
- Avoid skin contact with the adhesive. In case of accidental contact, wash the affected area thoroughly with soap and water.
Eye Protection:
- In addition to safety glasses or goggles, consider using a face shield if there is a risk of splashing or exposure to larger quantities.
Material Compatibility:
- Ensure that the UV cure adhesive is compatible with the materials being bonded. Some materials may be sensitive to UV radiation.
Read and Follow the Instructions:
- Carefully read and follow the manufacturer’s instructions and guidelines for the specific UV cure adhesive you are using.
Storage:
- Store UV-cure adhesives according to the manufacturer’s recommendations, including temperature and humidity.
Emergency Preparedness:
- Be aware of emergency procedures in case of accidental exposure or ingestion. Have access to emergency eyewash stations and showers.
Training:
- Provide proper training to individuals working with UV cure adhesives, including information on potential hazards and safe handling practices.
Curing Time:
- Allow sufficient curing time for the adhesive as specified by the manufacturer. Improper curing may result in reduced bond strength.
Waste Disposal:
- Dispose of waste materials, including cured adhesive, according to local regulations and guidelines.
Always refer to the specific safety data sheet (SDS) provided by the manufacturer for detailed information on the hazards, safe use, and handling of the UV cure adhesive you are using. Also, consult with safety professionals or experts if you have specific concerns or questions about working with UV cure adhesives in your application.
How does UV Cure Adhesive impact the aesthetics of Polypropylene joints?
UV cure adhesives can be used with various materials, including polypropylene, to create strong and durable bonds. However, the impact on the aesthetics of polypropylene joints can depend on several factors:
Clarity and Transparency:
- UV cure adhesives are available in different formulations, and some are designed to be clear and transparent. If maintaining the transparency of polypropylene is crucial for the aesthetics of the joint, you should choose a UV adhesive formulated explicitly for clarity.
Yellowing:
- Some UV-cure adhesives may yellow over time when exposed to UV light. This yellowing can affect the appearance of the polypropylene joint. Selecting a UV adhesive with good UV stability is essential if the joint is exposed to sunlight or other UV sources.
Surface Preparation:
- Polypropylene is known for its low surface energy, making it challenging for adhesives to bond effectively. Proper surface preparation, such as cleaning and sometimes using adhesion promoters, is crucial to achieving a solid bond. The effectiveness of surface preparation may influence the aesthetic impact.
Cure Time:
- UV cure adhesives typically cure rapidly when exposed to UV light. The fast cure time can be advantageous for production efficiency but may also limit the time available for adjusting the alignment of parts before the adhesive sets. This can impact the precision and appearance of the joint.
Bond Strength and Clarity Balance:
- Achieving a balance between bond strength and maintaining the aesthetics of the joint is essential. Some high-strength adhesives may need to be more straightforward or transparent, so when selecting the adhesive, one should consider the mechanical requirements and aesthetic preferences.
Application Method:
- The method used to apply the UV adhesive can also influence aesthetics. Precision in application is essential to avoid excess adhesive that could affect the appearance of the joint.
Testing and Validation:
- Before implementing UV cure adhesives on a larger scale, it’s advisable to conduct testing and validation to ensure that the chosen adhesive meets both the mechanical and aesthetic requirements for the specific polypropylene application.
UV cure adhesives can provide strong bonds for polypropylene joints. Still, careful consideration of formulation, yellowing tendencies, surface preparation, cure time, and application methods is necessary to achieve the desired aesthetics. It’s recommended to consult with adhesive manufacturers or conduct small-scale tests to determine the best adhesive for a particular polypropylene bonding application.
What advancements have been made in UV Cure Adhesive technology for PolypropylenePolypropylene?
UV cure adhesives are known for their rapid curing and bonding properties, making them suitable for various applications.
Advancements in UV cure adhesive technology for PolypropylenePolypropylene may include:
- Improved Adhesion Strength:Researchers and manufacturers may have developed formulations that enhance the adhesion strength of UV-cured adhesives on polypropylene surfaces. This is crucial for ensuring durable and reliable bonds.
- Reduced Cure Time:Efforts may have been made to reduce further the cure time required for UV-cured adhesives on polypropylene polypropylene, making the process more efficient and cost-effective.
- Adaptation to Different PP Grades:Polypropylene comes in various grades with different characteristics. Advancements may involve the development of UV cure adhesives that can bond effectively to a broader range of polypropylene grades.
- Enhanced Chemical Resistance:Improvements in the chemical resistance of UV cure adhesives for PolypropylenePolypropylene may have been achieved, making them more suitable for applications where exposure to harsh chemicals is a concern.
- Compatibility with Various Substrates:Adhesive formulations might have been refined to ensure compatibility with a broader range of substrates commonly used with PolypropylenePolypropylene.
- UV LED Technology:Advances in UV LED technology could have been integrated into UV cure adhesive systems, offering benefits such as energy efficiency, longer life, and precise control over the curing process.
- Environmental Considerations:There could be a focus on developing UV cure adhesives that are more environmentally friendly, with reduced volatile organic compounds (VOCs) or other hazardous components.
It’s important to note that the specific advancements can vary based on ongoing research, industry needs, and technological developments. To get the most up-to-date information on advancements in UV cure adhesive technology for polypropylene polypropylene, it is recommended to check recent publications in industry journals and contact manufacturers or researchers in the field.
Is UV Cure Adhesive suitable for high-temperature Polypropylene applications?
UV cure adhesives are generally versatile and can bond to various substrates. However, their suitability for high-temperature applications, especially with polypropylene, depends on the specific formulation of the UV cure adhesive.
Polypropylene is known for its low surface energy, making bonding challenging. UV cure adhesives are often used for bonding applications where fast curing and bonding to various substrates are required. To enhance the adhesion to polypropylene, surface treatment or priming may be necessary.
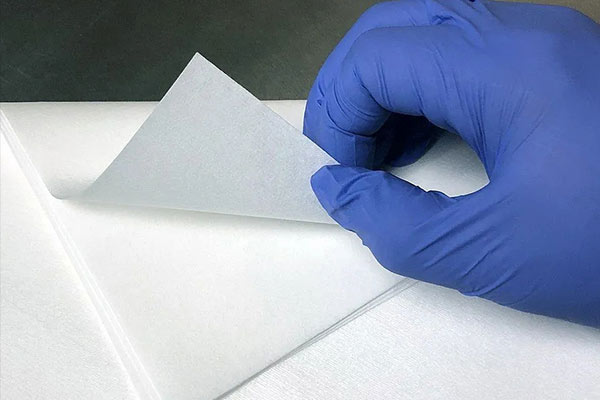
Regarding high-temperature resistance, it’s crucial to check the specifications provided by the manufacturer of the UV cure adhesive. Some UV-cure adhesives are designed to withstand higher temperatures, but limitations may remain.
If you are working on a critical application with high temperatures, it’s recommended to consult with the adhesive manufacturer directly. They can provide specific information about the compatibility of their product with polypropylene and its performance under high-temperature conditions. Additionally, they might offer guidance on surface preparation or priming to improve adhesion.
Always follow the manufacturer’s recommendations and guidelines for adequately applying and curing the adhesive to ensure optimal performance.
How does the cost of UV Cure Adhesive compare to traditional bonding methods?
The cost of UV cure adhesive compared to traditional bonding methods can vary depending on several factors, including the specific application, material requirements, and production processes. Here are some general considerations:
Material Costs:
- UV cure adhesives may have a higher initial cost per unit than traditional adhesives. However, the overall material cost can be influenced by factors such as the amount of adhesive required for the application and the efficiency of the curing process.
Labor Costs:
- UV cure adhesives often offer faster curing times compared to traditional adhesives. This can lead to increased efficiency in production processes, potentially reducing labor costs associated with waiting for adhesives to set or cure.
Energy Costs:
- Traditional bonding methods, such as thermal or chemical curing, may require additional energy sources for the curing process. UV cure adhesives typically cure with ultraviolet light, which may have lower energy consumption.
Equipment Costs:
- UV cure systems require specific equipment, such as UV lamps or LED lights, which may contribute to the initial setup costs. Traditional bonding methods use different equipment, and the cost will depend on the complexity of the machinery required.
Process Time:
- UV cure adhesives often provide faster cure times, increasing production throughput and reducing the time components spend in the manufacturing process. This can have an impact on overall production costs.
Waste and Cleanup:
- UV cure adhesives may generate less waste and require minimal cleanup compared to some traditional adhesives, contributing to potential cost savings.
Application Specifics:
- The specific requirements of the application can significantly influence the cost comparison. For particular applications or materials, the benefits of UV-cure adhesives, such as their ability to bond quickly and cleanly, may outweigh any additional upfront costs.
While UV cure adhesives may have higher upfront costs, their speed, efficiency, and reduced energy consumption advantages can contribute to overall cost savings in specific applications. The cost-effectiveness of UV cure adhesives will depend on the particular needs and constraints of the application. It’s advisable to conduct a thorough cost analysis, taking into account both direct and indirect costs, to make an informed decision based on the requirements of your project.
Can UV Cure Adhesive be used for bonding Polypropylene in medical devices?
UV cure adhesives are known for their ability to provide rapid bonding through ultraviolet (UV) light exposure. However, bonding polypropylene can be challenging because it has a low-energy surface, meaning it has a low surface tension that makes it difficult for adhesives to adhere effectively.
In the case of medical devices, it’s crucial to ensure that the adhesive used complies with relevant regulatory requirements and standards, such as those set by the U.S. Food and Drug Administration (FDA) or other appropriate authorities depending on the country.
Some UV cure adhesives are formulated to bond well with Polypropylene, and manufacturers may provide specific information about compatibility with various substrates. It’s recommended to consult with the adhesive manufacturer and give details on your particular application, including the type of Polypropylene and the environmental conditions to which the medical device will be exposed.
Additionally, surface treatment of Polypropylene may be necessary to enhance adhesion. Methods such as corona or plasma treatment can modify the surface of Polypropylene, improving its wettability and allowing for better adhesion of the UV cure adhesive.
In summary, while some UV cure adhesives may be suitable for bonding polypropylene in medical devices, it’s essential to:
- By consulting the adhesive manufacturer, check the compatibility of the UV cure adhesive with Polypropylene.
- Ensure that the adhesive meets regulatory requirements for medical devices.
- Consider surface treatment options to enhance the adhesion of the adhesive to Polypropylene.
Always follow the manufacturer’s recommendations and guidelines for the adhesive and the substrate to achieve reliable and compliant bonding in medical device applications.
What are the environmental benefits of using UV Cure Adhesive for Polypropylene?
UV cure adhesives offer several environmental benefits when bonding polypropylene and other materials. Here are some of the key advantages:
- Reduced VOC Emissions:Traditional adhesives often contain volatile organic compounds (VOCs) that can be released into the atmosphere during curing. UV cure adhesives typically have lower or zero VOC content, leading to reduced emissions and a smaller environmental footprint.
- Energy Efficiency:UV cure adhesives cure rapidly when exposed to ultraviolet light, resulting in energy savings compared to other curing methods that require higher temperatures or longer processing times. The quick curing process contributes to energy efficiency and can lead to lower overall energy consumption.
- Reduced Hazardous Byproducts:UV cure adhesives generally do not produce hazardous byproducts during curing. This contrasts some solvent-based adhesives that can release harmful chemicals into the environment. The absence of such byproducts contributes to a cleaner and safer manufacturing process.
- Longer Shelf Life and Less Waste:UV cure adhesives often have a longer shelf life than traditional adhesives. This longer shelf life reduces the likelihood of adhesives expiring before use, leading to less waste and a more sustainable manufacturing process.
- Precise Application and Minimal Excess:UV cure adhesives can be precisely applied to specific areas, reducing the need for excess adhesive. This precision minimizes material waste and makes manufacturing more efficient, contributing to environmental sustainability.
- No Need for Solvents or Chemical Activators:Some adhesive processes require solvents or chemical activators, which can have environmental and health implications. UV cure adhesives eliminate the need for such additional chemicals, simplifying manufacturing and reducing environmental impact.
- Lower Heat Output:UV curing involves minimal heat output compared to some thermal curing processes. This is advantageous for temperature-sensitive substrates like polypropylene, as it minimizes the risk of thermal damage to the material during bonding.
- Improved Worker Safety:UV cure adhesives often have lower toxicity and flammability than solvent-based adhesives, contributing to a safer working environment for manufacturing personnel.
It’s important to note that while UV cure adhesives offer these environmental benefits, the overall sustainability of a product or process depends on various factors, including the entire product lifecycle, disposal considerations, and the specific formulation of the adhesive. Manufacturers should consider a holistic approach to sustainability when evaluating adhesive options.
Are there any ongoing research developments in UV Cure Adhesive technology?
UV cure adhesive technology has been an area of ongoing research and development. However, please note that technological developments can occur rapidly, and I may need the latest information. Here are some trends and areas of interest in UV cure adhesive technology up to my last update:
- Formulation Improvements:Researchers have been enhancing the formulation of UV cure adhesives to improve their performance, such as adhesion strength, flexibility, and resistance to various environmental conditions.
- Faster Cure Times:Efforts have been made to reduce the cure times of UV cure adhesives. More rapid curing can increase productivity in manufacturing processes.
- Customization for Specific Applications:Researchers are exploring ways to tailor UV-cure adhesives for specific applications, such as electronics, medical devices, or automotive components. This involves optimizing the adhesive properties to meet the unique requirements of each industry.
- Improved Compatibility with Substrates:Adhesive bonding often involves different types of materials. Researchers are developing UV cure adhesives that exhibit better compatibility with various substrates, including plastics, metals, and composites.
- Enhanced Environmental and Health Characteristics:There is a growing emphasis on developing UV cure adhesives with reduced environmental impact and improved safety profiles. This includes efforts to reduce volatile organic compound (VOC) emissions and use hazardous substances in adhesive formulations.
- Innovation in Application Techniques:Researchers are exploring new application techniques for UV cure adhesives, such as inkjet printing and 3D printing. These innovations aim to expand the range of applications and improve the precision of adhesive placement.
- UV LED Technology:The adoption of UV LED curing technology continues to grow. UV LEDs offer advantages such as energy efficiency, longer lifespans, and reduced heat generation compared to traditional UV lamps. Ongoing research focuses on optimizing UV LED curing systems for various adhesive applications.
Scientific journals, industry publications, and attending relevant conferences or trade shows where researchers and industry experts share their findings and innovations to get the latest information on ongoing UV cure adhesive technology developments.
What advice can be given for optimizing the application of UV Cure Adhesive on Polypropylene?
Applying UV cure adhesive on polypropylene can be challenging due to the low surface energy of polypropylene, which can hinder adhesion. However, by following some guidelines, you can optimize the application process. Here are some tips:
Surface Preparation:
- Clean the polypropylene surface thoroughly to remove contaminants, such as oils or residues, that could inhibit adhesion.
- Use a cleaning agent designed explicitly for polypropylene or a mild detergent.
Surface Activation:
- Consider using a surface activation method like plasma or corona to enhance adhesion. These methods increase polypropylene’s surface energy, allowing better adhesive wetting.
Primer Application:
- Apply a primer designed for polypropylene bonding. Primers can improve the adhesion of UV-cure adhesives by promoting better wetting and bonding to the substrate.
Adhesive Selection:
- Choose a UV cure adhesive specifically formulated for bonding polypropylene. These adhesives often contain adhesion promoters that enhance bonding to low-energy surfaces.
Proper UV Exposure:
- Ensure that the adhesive receives the correct amount of UV exposure. Follow the manufacturer’s recommendations regarding the required intensity and duration of UV light exposure for proper curing.
Adhesive Thickness:
- Control the adhesive thickness to ensure adequate curing. Excessive adhesive thickness may hinder complete curing, leading to reduced bond strength.
Applicator Settings:
- Set the dispensing equipment properly to consistently and even apply the UV cure adhesive. This is crucial for uniform curing and optimal bond strength.
Temperature and Humidity Control:
- Maintain appropriate environmental conditions during the curing process. Extreme temperatures or humidity levels can affect the adhesive curing process.
Testing and Validation:
- Conduct adhesive bond strength tests on sample joints to ensure the chosen adhesive and application process meet the required specifications.
Follow Manufacturer Guidelines:
- Always follow the guidelines provided by the adhesive manufacturer. They often offer specific recommendations for surface preparation, application, and curing.
Remember, the success of the UV cure adhesive application on polypropylene depends on proper surface preparation, adhesive selection, and curing conditions. Testing and validation are essential steps to ensure the effectiveness of the bonding process for your specific application.
Conclusion:
In conclusion, adhesives have witnessed a transformative leap with UV Cure Adhesive for Polypropylene. This guide aimed to unravel the intricacies of this innovative bonding solution, from its unique features to diverse applications. As industries continue to evolve, UV Cure Adhesive is a beacon of efficiency, resilience, and adaptability in Polypropylene bonding. Embrace the future of adhesive technology with UV Cure Adhesive – unlocking unprecedented possibilities in material bonding.
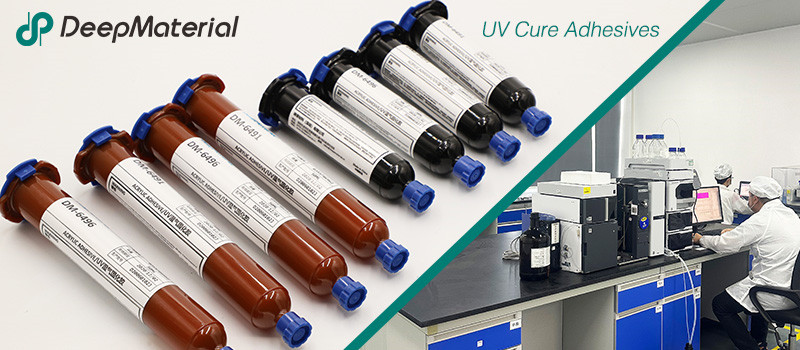
DeepMaterial
Based on the core technology of adhesives, DeepMaterial has developed adhesives for chip packaging and testing, circuit board level adhesives, and adhesives for electronic products. Based on adhesives, it has developed protective films, semiconductor fillers, and packaging materials for semiconductor wafer processing and chip packaging and testing. More…
UV Curing Adhesives
UV light cure have a number of benefits making them a popular choice among many product assembly and manufacturing applications. Many UV light cure adhesives can provide a nearly instantaneous bond to difficult substrates like glass and plastic. UV cure adhesives often require an accelerator or UV light for a bond to form.
Adhesive Blogs & News
The latest adhesive industry science and technology, Deepmaterial news, and market trends and forecasts.
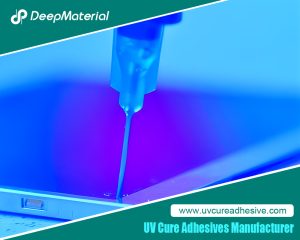
The Diverse Application Exploration of Conformal Coating Materials
The Diverse Application Exploration of Conformal Coating Materials Conformal coating is a kind of coating material that can form a uniform, continuous, and protective layer on the surface of an object. In the electronic field, it is mainly used to protect printed circuit boards (PCBs) and their components from environmental factors such as moisture,
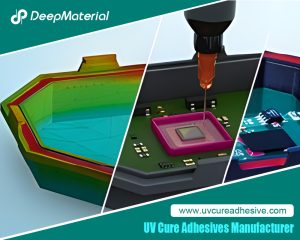
Main Chemical Characteristics of Conformal Coating
Main Chemical Characteristics of Conformal Coating Conformal coating, as a functional coating material widely used in fields such as electronics and aerospace, can form a uniform, continuous, and flexible protective film with certain protective properties on the surface of the coated object. The quality of its performance depends largely on its chemical characteristics, including
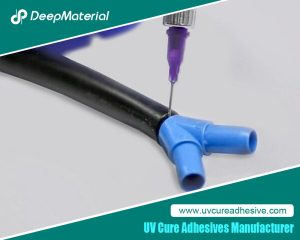
Exploring the Mystery and Application of Conformal Coating Spray
Exploring the Mystery and Application of Conformal Coating Spray In today’s highly developed field of electronic technology, protecting the reliability and stability of electronic devices is of paramount importance. Conformal coating spray, as an effective protective measure, is playing an increasingly important role. It not only provides excellent protective performance for electronic components but
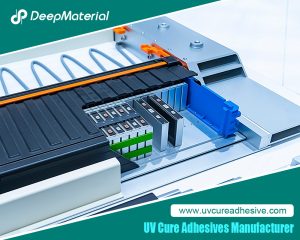
Research and Analysis on Types of Conformal Coatings
Research and Analysis on Types of Conformal Coatings Elaborate on the importance of conformal coatings in the electronics industry In today’s highly digital and intelligent era, electronic devices have become an indispensable part of people’s lives and work. From smart phones, tablets to automotive electronic systems and industrial control equipment, the application of electronic
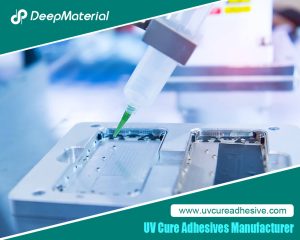
The Application and Development of Conformal Coating for Electronics
The Application and Development of Conformal Coating for Electronics In the present digital and intelligent era, electronic products have become an indispensable part of our lives. From mobile phones used for daily communication to laptops necessary for work and entertainment, from smart home appliances to advanced medical equipment, electronic products are everywhere. Their efficient
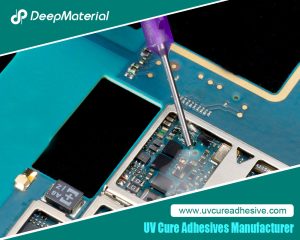
Electrical Potting Compound
Electrical Potting Compound In the vast field of modern electronic technology, Electrical Potting Compound plays a crucial role. It is like the invisible guardian inside electronic devices, providing reliable protection and stable performance support for various precise electronic components. Definition and Classification of Electrical Potting Compound Electrical Potting Compound is a special material