Main Chemical Characteristics of Conformal Coating
Conformal coating, as a functional coating material widely used in fields such as electronics and aerospace, can form a uniform, continuous, and flexible protective film with certain protective properties on the surface of the coated object. The quality of its performance depends largely on its chemical characteristics, including chemical compositions and chemical bond types. In-depth understanding of these chemical characteristics is of great significance for the research, development, production, and application of conformal coatings.
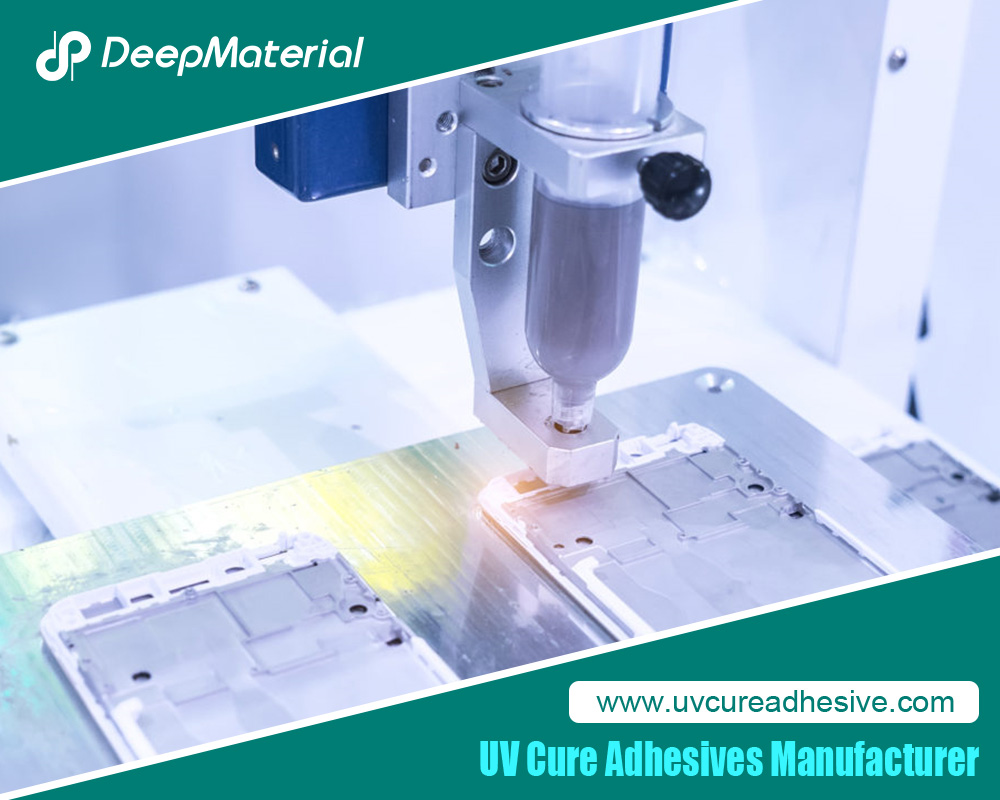
Chemical Compositions of Conformal Coatings
Organic Polymer Matrix
- Epoxy Resin: It is one of the commonly used organic polymer matrices in conformal coatings. Its molecular structure contains epoxy groups, which have high chemical reactivity. Epoxy resin has excellent adhesion and can firmly adhere to various substrate surfaces, such as metals, plastics, and ceramics. It also has good chemical corrosion resistance and can resist certain acids, alkalis, and other chemical substances. During the curing process, the epoxy groups can undergo a ring-opening reaction with the curing agent to form a three-dimensional network structure, thereby improving the hardness and wear resistance of the coating.
- Polyurethane: It has a unique chemical structure and is prepared by the reaction of isocyanates and polyols. Polyurethane conformal coatings have good flexibility and elasticity and can adapt to the deformation of the coated object under different environmental conditions. It also has excellent wear resistance and weather resistance and can maintain the stability of the coating performance for a long time in outdoor environments. In addition, the molecular chains of polyurethane contain urethane groups, and hydrogen bonds can be formed between these groups, which further enhances the cohesion and mechanical properties of the coating.
- Organic Silicone Resin: With a skeleton structure of silicon-oxygen bonds (Si-O), it has many unique properties. Organic silicone conformal coatings have excellent high-temperature resistance and can maintain a stable chemical structure and physical properties in high-temperature environments. It also has good electrical insulation properties and is suitable for the protection of electronic devices. In addition, the surface energy of organic silicone resin is relatively low, and it has good hydrophobicity, which can effectively prevent the erosion of water and moisture on the coated object.
Additives
- Curing Agent: For thermosetting conformal coatings, such as epoxy resin and polyurethane coatings, the curing agent is an essential chemical component. The role of the curing agent is to react with the active groups in the organic polymer matrix, transforming the coating from a liquid state to a solid state. Different types of curing agents will affect the curing speed, hardness, flexibility, and other properties of the coating. For example, amine curing agents react with epoxy resin relatively quickly and can cure the coating in a short time, forming a coating with higher hardness; while anhydride curing agents react with epoxy resin relatively slowly, and the cured coating has better flexibility.
- Diluent: It is used to adjust the viscosity of the conformal coating to make it easier to apply. Diluents are usually some organic solvents, such as toluene, xylene, etc. The diluent will gradually volatilize during the drying process of the coating and will not have a significant impact on the final performance of the coating. However, it should be noted that the selection and dosage of the diluent should be appropriate. Excessive diluent may lead to a decrease in the performance of the coating, such as reduced adhesion and decreased hardness.
- Filler: It can improve the physical properties of the conformal coating, such as hardness, wear resistance, and corrosion resistance. Common fillers include silica, calcium carbonate, talc powder, etc. The addition of fillers can also reduce the cost of the coating and increase the solid content of the coating. For example, silica fillers can improve the hardness and wear resistance of the coating, while calcium carbonate fillers can reduce the cost of the coating.
Chemical Bond Types in Conformal Coatings
Covalent Bond
- Carbon-Carbon Bond (C-C): In the organic polymer matrix, the carbon-carbon bond is the main chemical bond type that constitutes the molecular chain. The carbon-carbon bond has a relatively high bond energy, making the organic polymer have a certain degree of stability. For example, in the molecular chains of epoxy resin and polyurethane, carbon-carbon bonds connect different atomic groups to form molecular chains with a certain length and structure. These molecular chains crosslink with each other during the curing process to form a three-dimensional network structure, thereby improving the strength and hardness of the coating.
- Carbon-Hydrogen Bond (C-H): It is also a common chemical bond type in organic polymers. The carbon-hydrogen bond has a relatively small polarity, making the organic polymer have a certain degree of hydrophobicity. In the conformal coating, the presence of carbon-hydrogen bonds helps to improve the waterproof performance of the coating and prevent water from penetrating into the surface of the coated object. In addition, the vibration frequency of the carbon-hydrogen bond has a specific absorption peak in the infrared spectrum, which can be used for the component analysis and structure identification of the conformal coating.
- Silicon-Oxygen Bond (Si-O): It is the main chemical bond type of organic silicone resin. The silicon-oxygen bond has a relatively high bond energy and has good thermal stability and chemical stability. The silicon-oxygen bond in the organic silicone conformal coating endows the coating with excellent high-temperature resistance and chemical corrosion resistance. At the same time, the presence of the silicon-oxygen bond also makes the organic silicone resin have a low surface energy, with good hydrophobicity and mold release properties.
Hydrogen Bond
- Formation of Hydrogen Bond: In the conformal coating, hydrogen bonds mainly exist between molecules containing polar groups. For example, hydrogen bonds can be formed between the urethane groups in polyurethane. The hydrogen bond is a special intermolecular force. Although its bond energy is lower than that of a covalent bond, it has an important impact on the performance of the coating.
- Influence of Hydrogen Bond on Coating Performance: The existence of hydrogen bonds can enhance the intermolecular interaction force and improve the cohesion and mechanical properties of the coating. For example, in the polyurethane conformal coating, the formation of hydrogen bonds makes the molecular chains more closely arranged, thereby improving the hardness and wear resistance of the coating. In addition, hydrogen bonds can also affect the solubility and water absorption of the coating. Coatings with strong hydrogen bond effects usually have lower solubility and water absorption.
Relationship between Chemical Characteristics and Performance of Conformal Coatings
Relationship between Chemical Compositions and Performance
- Influence of Organic Polymer Matrix on Performance: Different types of organic polymer matrices determine the basic performance of the conformal coating. Epoxy resin-based conformal coatings have excellent adhesion and chemical corrosion resistance and are suitable for occasions with high requirements for protective performance; polyurethane-based conformal coatings have good flexibility and wear resistance and are suitable for the surfaces of objects that need to withstand certain deformation and friction; organic silicone-based conformal coatings have excellent high-temperature resistance and electrical insulation properties and are suitable for the protection of electronic devices and in high-temperature environments.
- Influence of Additives on Performance: The type and dosage of the curing agent will affect the curing speed and final performance of the coating. The selection and dosage of the diluent will affect the construction performance of the coating and the quality of the coating. The type and content of the filler will affect the physical properties of the coating, such as hardness, wear resistance, and corrosion resistance.
Relationship between Chemical Bond Types and Performance
- Influence of Covalent Bond on Performance: The bond energy and bond length of the covalent bond determine the stability and structure of the molecule. Covalent bonds with high bond energy, such as carbon-carbon bonds and silicon-oxygen bonds, make the conformal coating have good chemical stability and thermal stability. The structure of the covalent bond also affects the flexibility and fluidity of the molecular chain, thereby affecting the construction performance and final performance of the coating.
- Influence of Hydrogen Bond on Performance: The existence of hydrogen bonds enhances the intermolecular interaction force and improves the cohesion and mechanical properties of the coating. At the same time, hydrogen bonds can also affect the solubility and water absorption of the coating, which has an important impact on the protective performance of the coating.
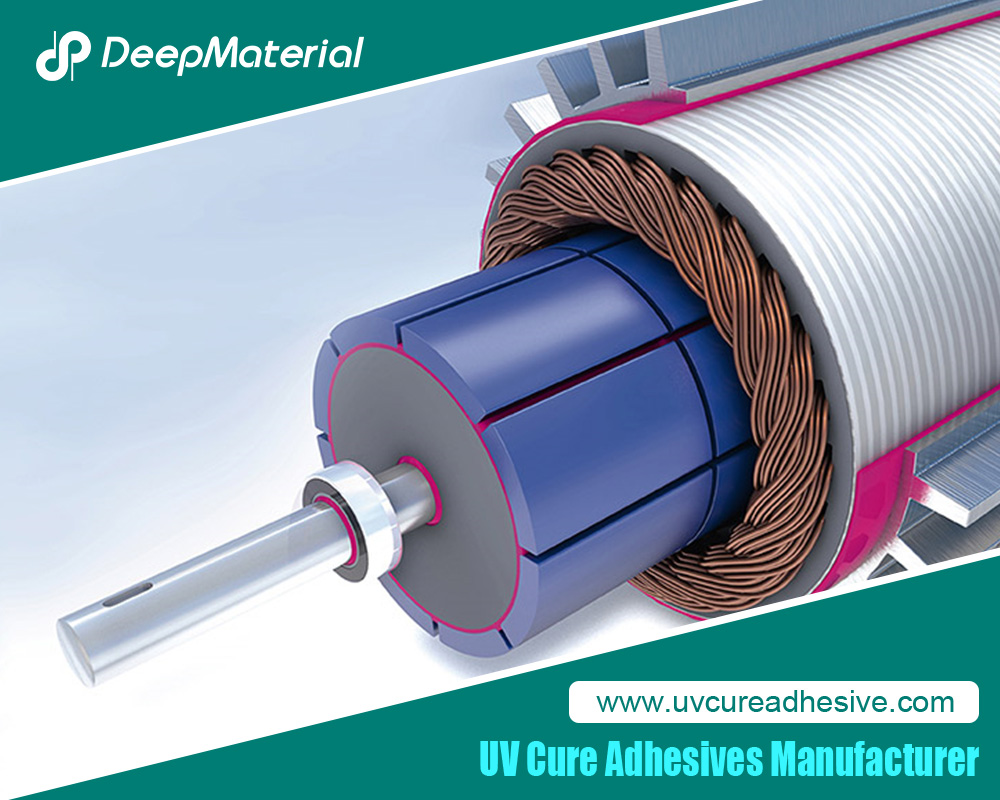
Conclusion
The chemical characteristics of conformal coating materials, including chemical compositions and chemical bond types, play a decisive role in their performance. The selection and proportioning of chemical components such as organic polymer matrices and additives, as well as the existence and action of chemical bond types such as covalent bonds and hydrogen bonds, jointly determine the adhesion, flexibility, wear resistance, chemical corrosion resistance, high-temperature resistance, and other properties of the conformal coating. In-depth understanding of these chemical characteristics helps to develop conformal coatings with more excellent performance to meet the application requirements of different fields. In future research, it is still necessary to further explore new chemical components and chemical bond structures to continuously improve the performance and application scope of conformal coatings.
For more about choosing a comprehensive guide to main chemical characteristics of conformal coating, you can pay a visit to DeepMaterial at https://www.uvcureadhesive.com/ for more info.