High Temperature Adhesive
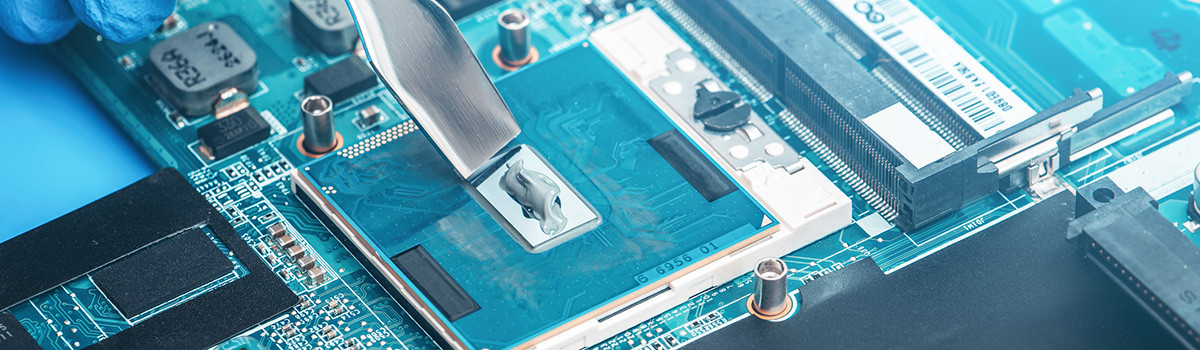
Adhesives have long been the unsung heroes in various industries, holding the fabric of creation together. These bonds become paramount in high-temperature applications, ensuring stability under extreme conditions. High-temperature adhesives, a class of specialized bonding agents, redefine the concept of strength and resilience in environments where typical adhesives falter. From aerospace engineering to everyday DIY projects, the need for robust bonding solutions that withstand extreme heat is undeniable.
This comprehensive guide aims to delve into high-temperature adhesives, uncovering their properties, applications, challenges, and the art of selecting the suitable adhesive for the job.
Table of Contents
ToggleWhat defines a High-Temperature Adhesive?
High-temperature adhesives are pivotal in various industries where extreme heat resistance is crucial for bonding materials. What defines a high-temperature adhesive are its unique properties tailored to withstand elevated temperatures without compromising its adhesive strength or integrity.
A high-temperature adhesive is characterized by its ability to endure intense heat levels, typically ranging from 300°F (150°C) to well over 2000°F (1093°C). The critical defining features include:
- Thermal Stability: These adhesives maintain their bonding strength and structural integrity even when exposed to high temperatures for prolonged periods. They resist thermal degradation and do not soften, melt, or lose adhesion under extreme heat.
- Chemical Resistance: They resist chemical breakdown, ensuring stability when exposed to various chemicals, fuels, oils, and other substances often present in industrial settings.
- Flexibility and Versatility:High-temperature adhesives come in various formulations suitable for different materials, including metals, ceramics, glass, and composites. They offer flexibility in application methods, such as paste, liquid, or tape forms, catering to diverse bonding needs.
- Excellent Adhesion:These adhesives form strong bonds between surfaces, maintaining their grip even under thermal expansion and contraction. They adhere well to various substrates, ensuring reliability in extreme conditions.
- Specialized Formulations:Depending on the intended use, high-temperature adhesives may have additional properties like electrical insulation, corrosion resistance, or flame-retardant characteristics.
Industries like aerospace, automotive, electronics, and manufacturing heavily rely on high-temperature adhesives for critical applications. In aerospace, these adhesives are essential for bonding heat-resistant materials in aircraft engines, ensuring structural integrity at high altitudes where temperatures can soar. Automotive applications involve bonding components in engines, exhaust systems, and braking systems where temperatures can reach extreme levels during operation. High-temperature adhesives are crucial in these areas to maintain the functionality and safety of vehicles.
Why are High-Temperature Adhesives crucial in industries?
In industrial processes, the significance of high-temperature adhesives cannot be overstated. These specialized bonding agents play a pivotal role in various industries, ensuring operations’ integrity, safety, and efficiency, particularly in high-heat environments.
What Are High-Temperature Adhesives?
- Composition:High-temperature adhesives are formulated with compounds resistant to extreme heat, offering stability under elevated temperatures.
- Properties:They exhibit exceptional heat resistance, maintaining structural integrity even when exposed to temperatures exceeding 500°F (260°C).
- Variety:These adhesives come in various forms, including epoxies, silicones, and cyanoacrylates, tailored to specific applications.
Crucial Role in Industries
- Aerospace:In the aerospace sector, high-temperature adhesives are instrumental in bonding components exposed to extreme temperatures during flight, ensuring structural stability and safety.
- Automotive:Within the automotive industry, these adhesives are utilized in engine components, exhaust systems, and brake assemblies, enduring high thermal stress without compromising performance.
- Electronics:In electronic manufacturing, high-temperature adhesives secure sensitive components, withstanding the heat generated by circuits and machinery, ensuring reliability and longevity.
- Industrial Equipment:Heavy machinery and industrial equipment rely on these adhesives to maintain structural integrity in high-heat environments, preventing component failure and ensuring operational efficiency.
Importance and Benefits
- Resilience: They maintain adhesive strength at elevated temperatures, safeguarding bonded components from thermal degradation.
- Enhanced Performance: High-temperature adhesives enable machinery and components to function optimally, minimizing downtime due to heat-related failures.
- Cost Efficiency: By preventing component damage caused by heat, these adhesives contribute to cost savings by reducing repair and replacement expenses.
How do High-Temperature Adhesives differ from standard adhesives?
High-temperature adhesives stand out in adhesive solutions as a specialized category designed to withstand extreme heat conditions. But how do these adhesives differ from standard variants? Let’s explore the distinctive features and advantages that set high-temperature adhesives apart.
What Sets High-Temperature Adhesives Apart?
- Heat Endurance: Unlike standard adhesives, high-temperature variants are engineered to withstand elevated temperatures without compromising their adhesive properties. They exhibit resilience in environments where temperatures soar, making them ideal for applications in industries like aerospace, automotive, and manufacturing.
- Chemical Composition: High-temperature adhesives are formulated using specialized compounds and additives to impart heat resistance. These compounds can include silicone, epoxy, polyurethane, or phenolic resins, tailored to endure extreme thermal conditions without losing their bonding capabilities.
- Application Versatility:While standard adhesives suffice for everyday use, high-temperature adhesives cater to specific industries requiring resilience against extreme heat. They are utilized in bonding heat-sensitive materials like ceramics, metals, and composites, where regular adhesives would fail.
Advantages of High-Temperature Adhesives
- Exceptional Thermal Stability:One of the primary advantages is their ability to maintain structural integrity even at temperatures well beyond the capacity of standard adhesives. This stability ensures longevity and reliability in applications exposed to high heat.
- Enhanced Durability:High-temperature adhesives offer increased durability, ensuring the longevity of bonded components even in challenging environments. This durability factor is crucial in critical industries where failure is not an option.
- Specialized Industrial Applications:Industries such as aerospace, automotive manufacturing, electronics, and industrial equipment heavily rely on high-temperature adhesives due to their ability to withstand extreme conditions, ensuring the integrity of crucial components.
What are the primary applications of High-Temperature Adhesives?
In the realm of industrial applications and manufacturing processes, the significance of high-temperature adhesives cannot be overstated. These specialized adhesives possess unique properties that allow them to withstand extreme temperatures, making them invaluable across various industries. From aerospace engineering to automotive manufacturing, their utility knows no bounds. Let’s explore the primary applications of high-temperature adhesives and their multifaceted role.
What Makes High-Temperature Adhesives Stand Out?
- Thermal Resistance:High-temperature adhesives exhibit exceptional thermal stability, maintaining structural integrity even in extreme heat conditions.
- Chemical Resilience:They offer resistance against various chemicals, ensuring durability and reliability in harsh environments.
- Bond Strength:These adhesives provide robust bonding capabilities, enhancing the longevity and performance of assembled parts.
Automotive Industry
- Engine Components:High-temperature adhesives play a pivotal role in bonding engine components due to their ability to withstand the intense heat generated within the engine compartment.
- Exhaust Systems:They bond and seal exhaust systems, enduring the extreme temperatures and vibrations produced during vehicle operation.
Aerospace Engineering
- Structural Assembly:High-temperature adhesives are vital in aircraft construction, facilitating the bonding of composite materials that form the structural components of aircraft.
- Spacecraft Applications:These adhesives are indispensable in space missions, ensuring the integrity of components subjected to extreme temperature fluctuations in space.
Electronics Manufacturing
- Circuitry and Components:They are employed in electronics to bond and seal components in devices such as computers, where heat dissipation is crucial for performance.
- LED Production:High-temperature adhesives assemble LED modules, providing stability and longevity in high-temperature conditions.
Industrial Equipment and Machinery
- Boilers and Furnaces:They contribute to the assembly and maintenance of boilers and furnaces by bonding heat-resistant materials that withstand high temperatures.
- Power Generation:High-temperature adhesives are used in power generation equipment manufacturing, ensuring secure bonds in turbines and heat exchangers.
How They Enhance Manufacturing Efficiency
- Increased Reliability:Their ability to withstand extreme temperatures ensures the longevity of assembled parts, reducing the need for frequent repairs or replacements.
- Design Flexibility:High-temperature adhesives enable engineers to explore innovative designs using various materials, fostering advancements in product development.
- Cost Efficiency:By minimizing downtime and maintenance, these adhesives contribute to cost savings in industries with high temperatures.
What are the various types of High-Temperature Adhesives?
High-temperature adhesives are crucial in industries where extreme heat resistance is imperative for bonding materials. From automotive to aerospace, these adhesives offer solutions for applications requiring resilience under elevated temperatures.
Understanding High-Temperature Adhesives
High-temperature adhesives come to the rescue when conventional adhesives fail due to high thermal stresses. They are formulated to withstand temperatures far beyond the capabilities of standard adhesives, ensuring structural integrity and reliability.
Types of High-Temperature Adhesives
Silicone-Based Adhesives
- Renowned for their exceptional thermal stability.
- Ideal for sealing and bonding applications.
- Resistant to temperatures ranging from -50°C to 300°C.
- It is commonly used in automotive gaskets, exhaust systems, and electronics.
Epoxy-Based Adhesives
- They are known for their strong bonding and resistance to heat.
- Offer excellent chemical and environmental resistance.
- Capable of enduring temperatures up to 350°C.
- They are widely used in aerospace, construction, and industrial settings.
Cyanoacrylate Adhesives
- Quick-bonding adhesives are suitable for high-temperature environments.
- Resist temperatures up to 180°C.
- They are frequently used in electronic assemblies and metal-to-metal bonding.
Polyurethane Adhesives
- Provide robust bonding strength under elevated temperatures.
- Tolerate temperatures ranging from -40°C to 150°C.
- They are utilized in manufacturing composite materials and structural bonding.
Phenolic Adhesives
- Known for their heat and chemical resistance.
- Can withstand temperatures exceeding 200°C.
- They are commonly applied in bonding wood, laminates, and fire-resistant materials.
Applications and Considerations
High-temperature adhesives find applications in various industries due to their exceptional heat resistance. However, when choosing the appropriate adhesive, several factors must be considered:
- Operating Temperature:Ensure the adhesive’s maximum temperature tolerance aligns with the application’s requirements.
- Bond Strength:Evaluate the necessary strength for the specific bonding application.
- Chemical Resistance:Consider the exposure to chemicals or environmental factors.
- Curing Time:Some adhesives require longer curing periods at elevated temperatures.
How do the characteristics vary among different High-Temperature Adhesives?
When it comes to high-temperature applications, choosing a suitable adhesive is crucial. High-temperature adhesives are pivotal in industries where extreme heat and harsh conditions are commonplace. Understanding the variations and characteristics among different high-temperature adhesives is fundamental in making informed choices for specific needs.
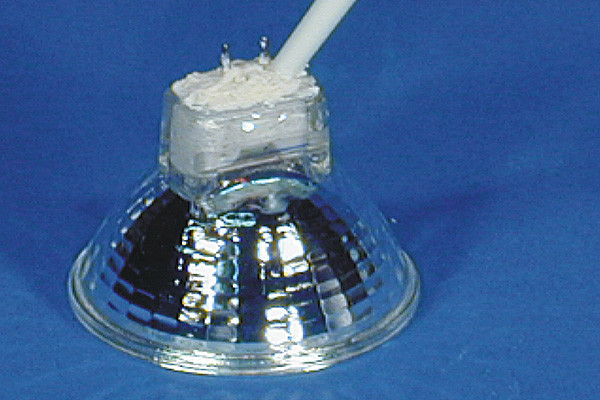
What are High-Temperature Adhesives?
As the name suggests, high-temperature adhesives are specifically formulated to withstand elevated temperatures without compromising their bonding properties. They are designed to maintain structural integrity, adhesion strength, and durability under extreme heat conditions, making them indispensable in various industries.
Variations Among Different High-Temperature Adhesives
Several types of high-temperature adhesives exist, each with its unique composition and characteristics:
Epoxy-Based Adhesives
- They are known for their exceptional bonding strength and resistance to high temperatures.
- They are often used in aerospace, automotive, and electronics due to their reliability and versatility.
Silicone-Based Adhesives
- Renowned for their flexibility, excellent thermal stability, and resistance to moisture and chemicals.
- It is ideal for applications requiring flexibility and enduring high temperatures, such as gaskets and engine seals.
Polyurethane-Based Adhesives
- They are recognized for their toughness, impact resistance, and ability to withstand extreme temperatures.
- Due to their durability, they are frequently used in the construction, manufacturing, and automotive industries.
Phenolic-Based Adhesives
- They are known for their exceptional heat resistance and ability to endure high-pressure conditions.
- It is commonly used in producing composite materials, aircraft components, and high-pressure laminates.
Characteristics Across Different High-Temperature Adhesives
Despite the variations, specific characteristics define high-temperature adhesives:
Temperature Resistance
- It varies among different adhesives, with some capable of withstanding temperatures exceeding 500°F (260°C) while others can endure even higher ranges.
Bond Strength
- Adhesives differ in their bonding strengths under elevated temperatures, affecting their suitability for various applications.
Chemical Resistance
- Some adhesives resist chemicals, acids, and solvents, ensuring stability even in harsh environments.
Flexibility and Toughness
- Varied flexibility and toughness levels cater to specific needs, such as applications requiring vibration resistance or impact resilience.
Choosing the Right High-Temperature Adhesive
Selecting the appropriate adhesive involves considering specific factors:
- Application Requirements:Please consider the bond’s temperature range, environmental conditions, and anticipated stress and evaluate accordingly.
- Substrate Compatibility:Ensure compatibility with the materials being bonded to prevent issues like corrosion or weakening of materials.
- Curing Time and Process:Consider the curing mechanism and time required for the adhesive to achieve its full strength.
- Regulatory Compliance:Confirm adherence to industry standards and regulations concerning safety and performance.
What factors dictate the selection of the right High-Temperature Adhesive for a project?
High-temperature adhesives are the unsung heroes in many industries, crucial for bonding materials that withstand extreme heat conditions. Selecting suitable adhesives from aerospace to automotive, electronics to manufacturing is pivotal for a project’s success. But what factors should one consider when choosing a high-temperature adhesive? Let’s delve into the key aspects:
Application Specifics
- Temperature Range:Determine the maximum and minimum temperatures the adhesive will encounter during the project.
- Duration of Exposure:Assess how long the materials will be subjected to high temperatures.
- Material Compatibility:Understand the types of materials the adhesive needs to bond. Some adhesives work better with certain materials than others.
Adhesive Types and Composition
- Silicone-Based Adhesives:These adhesives are well-known for their exceptional resistance to high temperatures. Additionally, they are flexible and durable, making them an ideal choice for various applications.
- Epoxy Resins:Offer strong bonds and stability at elevated temperatures, suitable for various substrates.
- Cyanoacrylate (CA) Adhesives: Fast-curing and versatile but may not withstand extreme temperatures, as well as other options.
- Polyurethane Adhesives:Provide flexibility and resilience, but their high-temperature resistance might vary.
Strength and Durability
- Shear and Tensile Strength:Consider the forces the bond will endure and choose an adhesive with appropriate strength.
- Chemical Resistance:Evaluate if the adhesive can withstand exposure to chemicals or environmental solvents.
- Thermal Cycling:Assess the adhesive’s ability to withstand repeated heating and cooling cycles without losing integrity.
Application Method and Cure Time
- Curing Conditions:Check if the adhesive requires specific conditions like heat, UV light, or air.
- Cure Time:Consider the project timeline and opt for adhesives that match the desired cure time.
- Ease of Application:Some adhesives are more accessible to apply than others. Factor in the application method that suits the project requirements.
Environmental and Safety Considerations
- Toxicity and VOCs:Assess the health and environmental impact of the adhesive.
- Regulatory Compliance:Ensure the adhesive meets industry standards and regulations.
- Environmental Conditions:Consider factors like humidity, pressure, and exposure to other elements in the project environment.
Cost and Availability
- Cost-Effectiveness:Balance the performance of the adhesive with its cost to find the most suitable option.
- Availability:Ensure the chosen adhesive is readily accessible in the required quantity.
Do High-Temperature Adhesives truly endure extreme environmental conditions?
The demand for adhesives capable of withstanding high temperatures and extreme environmental conditions is paramount in industrial applications. High-temperature adhesives are pivotal in various industries, from aerospace and automotive to electronics and manufacturing. However, the question lingers: Do high-temperature adhesives truly endure these demanding environments? Let’s delve deeper into this crucial inquiry.
Understanding High-Temperature Adhesives
- Composition:These adhesives are formulated using specialized compounds that withstand elevated temperatures.
- Functionality:They maintain structural integrity and bonding strength under extreme heat, ensuring stability and reliability.
- Applications:This adhesive is frequently utilized in applications where traditional adhesives would fail, such as in engines, furnaces, and electronics.
Endurance in Extreme Heat
- Temperature Resistance:High-temperature adhesives are engineered to withstand a broad spectrum of temperatures, ranging from hundreds to thousands of degrees Fahrenheit.
- Thermal Stability:They exhibit exceptional thermal stability, maintaining their adhesive properties even when subjected to prolonged exposure to extreme heat.
- Chemical Resistance:Many formulations possess resistance against chemical reactions induced by high temperatures, ensuring longevity in harsh environments.
Challenges and Solutions
- Degradation: Continuous exposure to high temperatures can cause degradation in conventional adhesives, weakening bonds, and compromised structural integrity.
- Innovative Formulations:Manufacturers constantly innovate, developing adhesives with enhanced heat resistance, improved durability, and reduced degradation under extreme conditions.
- Testing Protocols:Rigorous testing protocols are employed to evaluate the performance of these adhesives in simulated extreme environments, ensuring reliability before deployment.
Industry Applications and Advantages
- Aerospace:High-temperature adhesives are crucial in aerospace engineering, where components experience extreme heat during flights. Their reliability ensures the structural integrity of critical parts.
- Automotive:These adhesives are used in engines, exhaust systems, and braking mechanisms to prevent component failure even under high-temperature conditions, thereby improving vehicle safety.
- Electronics:In electronic manufacturing, they provide thermal management, securing components in devices subjected to elevated temperatures, like LED lighting and circuitry in automotive electronics.
What are the installation and curing processes for High-Temperature Adhesives?
High-temperature adhesives are pivotal in various industries where durability and resilience under extreme conditions are crucial. From aerospace engineering to automotive manufacturing and electronics, these adhesives are designed to withstand elevated temperatures while maintaining structural integrity. Knowing their installation and curing processes is essential for their practical application.
Types of High-Temperature Adhesives
- Epoxy-Based Adhesives: Known for their exceptional bonding strength and resistance to heat.
- Silicone-Based Adhesives: Flexible and resistant to extreme temperatures, chemicals, and moisture.
- Polyurethane Adhesives:Offer a balance between flexibility and toughness, suitable for high-temperature environments.
- Cyanoacrylate Adhesives:This product is designed to be fast-acting and durable, making it ideal for quick repairs when heat exposure is a concern.
Installation Process
- Surface Preparation:Properly clean and degrease the surfaces to be bonded. Any contaminants can hinder the adhesive’s effectiveness.
- Mixing (if applicable):For two-part adhesives like epoxy, follow precise mixing ratios to activate the adhesive properly. Thorough mixing ensures uniformity and optimal bonding strength.
- Application:Apply the adhesive evenly on the surfaces to be bonded. Use a suitable applicator or method based on the adhesive type and the nature of the materials being connected.
- Assembly:Join the surfaces together promptly after applying the adhesive. Apply pressure, if needed, to ensure a snug fit and proper bonding.
Curing Processes
- Heat Curing:Some high-temperature adhesives require exposure to elevated temperatures to cure fully. This process activates the adhesive and ensures maximum strength. Follow manufacturer guidelines for temperature and duration.
- Chemical Curing:Certain adhesives, like cyanoacrylates, cure through exposure to moisture in the air. This process happens relatively quickly.
- Room Temperature Curing:Some adhesives cure at room temperature but might require longer healing times. Patience is vital in allowing these adhesives to achieve their full strength.
Key Considerations
- Temperature Tolerance:Ensure the adhesive chosen can withstand the intended operating temperature range without compromising its bonding strength.
- Substrate Compatibility:Different materials require specific adhesives for optimal bonding. Verify compatibility to prevent potential material damage or weak bonds.
- Safety Measures:Adhere strictly to safety guidelines provided by the adhesive manufacturer. Some adhesives may emit fumes or require protective gear during application.
- Quality Assurance:Conduct tests or trials on a small scale before full-scale application to ensure the adhesive meets the required standards for strength and durability.
What safety precautions should be taken when working with High-Temperature Adhesives?
High-temperature adhesives, engineered to withstand extreme heat conditions, offer invaluable industry solutions. From automotive to aerospace, electronics to construction, these specialized adhesives are pivotal in bonding materials that face elevated temperatures. However, their use demands meticulous care and adherence to safety measures to ensure effectiveness and personal safety.
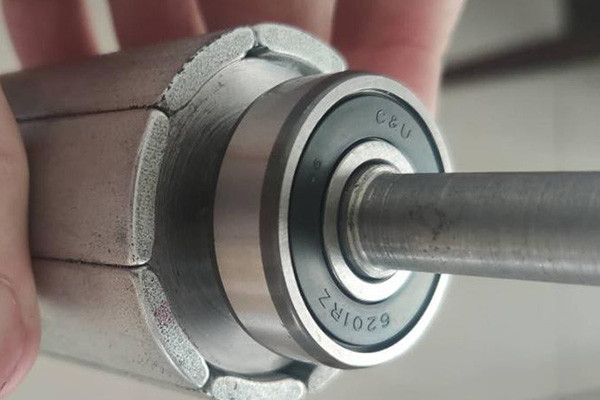
Understanding High-Temperature Adhesives
- Versatile Applications:High-temperature adhesives excel in environments where traditional adhesives fail due to heat exposure.
- Resilient Properties:These adhesives maintain structural integrity at temperatures ranging from 300°F to over 2000°F, depending on the formulation.
- Types:Silicone-based, epoxy, cyanoacrylate, and phenolic adhesives are common variants used in different industries.
Safety Precautions
- Proper Ventilation: Ensure adequate ventilation in the workspace to prevent the accumulation of fumes emitted during adhesive application and curing processes.
- Protective Gear: Use appropriate personal protective equipment (PPE) like gloves, safety glasses, and a respirator mask to shield against potential skin contact, eye irritation, and inhalation of harmful vapors.
- Temperature Regulation:Monitor and control the working environment’s temperature to align with the adhesive’s curing requirements, preventing premature curing or compromised bond strength.
- Read and Follow Instructions:Carefully review the manufacturer’s guidelines and follow their recommended application techniques and curing temperatures for optimal bonding and safety.
- Storage Conditions: Store high-temperature adhesives in their original containers in a controlled environment to maintain efficacy and prevent unintended chemical reactions.
- Avoid Skin Contact:Prevent direct skin contact with the adhesive, as some formulations can cause skin irritation or allergic reactions.
- Emergency Preparedness:Keep emergency protocols and first-aid supplies readily accessible in case of accidental exposure or spills.
- Cleanup Procedures:Use appropriate solvents or cleaners specified by the manufacturer to clean spills or excess adhesive, ensuring proper disposal methods are followed.
- Training and Education: Provide comprehensive training to personnel handling these adhesives, emphasizing safety protocols, proper application methods, and emergency response procedures.
What are the main challenges and limitations of High-Temperature Adhesives?
High-temperature adhesives are pivotal in various industries, offering bonding solutions for extreme conditions. These specialized adhesives, from aerospace engineering to automotive manufacturing, are engineered to withstand intense heat, ensuring structural integrity in challenging environments. However, despite their significance, they come with challenges and limitations that pose hurdles in their application.
Understanding the Main Challenges
High-temperature adhesives encounter several hurdles that limit their efficacy and practicality in specific scenarios:
- Temperature Resistance:The foremost challenge is maintaining adhesive strength at elevated temperatures. While these adhesives are designed for high-heat environments, their effectiveness might diminish beyond certain thresholds.
- Chemical Stability:Exposure to harsh chemicals and solvents can degrade adhesive performance. Ensuring chemical stability while retaining adhesive strength is a significant challenge.
- Thermal Cycling Durability: Frequent heating and cooling cycles can weaken adhesive bonds over time. This cyclic stress can lead to cracking or delamination, compromising the integrity of the bond.
- Adhesion to Diverse Surfaces:High-temperature adhesives might struggle to adhere to various substrates, limiting their versatility in applications requiring bonding to different materials.
- Curing Time and Process:Some high-temperature adhesives have extended curing times or require specific conditions for proper bonding, making them less practical for time-sensitive applications or challenging environments.
- Cost and Accessibility:Developing and acquiring high-temperature adhesives with superior properties often involves high manufacturing costs, impacting their accessibility for widespread use.
Addressing Limitations
Ongoing research and innovation are essential to overcome these challenges and expand the scope of high-temperature adhesives. Promising strategies include:
- Advanced Formulations:Engineers and researchers continually develop new adhesive formulations with enhanced temperature resistance and improved chemical stability to withstand extreme conditions more effectively.
- Nanoengineered Materials: Nanotechnology offers a promising avenue for enhancing adhesives by manipulating materials at the molecular level, optimizing their properties for higher temperature tolerance and better adhesion.
- Hybrid and Composite Solutions:Combining different adhesive types or incorporating reinforcing fibers and fillers can improve the overall performance of high-temperature adhesives, addressing issues related to thermal cycling and adhesion to diverse surfaces.
- Accelerated Curing Methods:Innovations in curing techniques, such as UV or heat-activated curing, aim to reduce curing times and enhance the bonding process, making these adhesives more viable for time-sensitive applications.
- Cost-Efficiency Measures:Research efforts to streamline manufacturing processes and explore cost-effective raw materials can potentially reduce overall production costs, making high-temperature adhesives more accessible to a broader range of industries.
How has technology advanced in the realm of High-Temperature Adhesives?
High-temperature adhesives are crucial for various industries, offering resilient bonding solutions in extreme heat conditions. These adhesives, designed to withstand elevated temperatures without compromising structural integrity, have witnessed significant technological advancements. From aerospace engineering to automotive manufacturing, their evolution has enhanced performance and expanded application possibilities.
The realm of high-temperature adhesives has seen remarkable progress owing to technological innovations. Here’s a glimpse into the strides made in this critical domain:
Chemical Formulations
- Novel chemical compositions:Researchers have developed advanced formulations with superior heat-resistant properties, combining different polymers and additives to enhance thermal stability.
- Nanotechnology integration:Utilizing nanomaterials has created adhesives with exceptional heat resistance, reinforcing the bond strength even under extreme temperatures.
Enhanced Bonding Strength
- Improved bonding under heat stress:The latest formulations exhibit heightened bond strength even in high-temperature environments, ensuring structural integrity in demanding conditions.
- Resistance to thermal cycling:Adhesives now withstand repeated thermal expansions and contractions, maintaining stability over prolonged usage in fluctuating temperatures.
Application Specific Innovations
- Aerospace industry advancements:High-temperature adhesives are engineered to meet the stringent demands of aircraft components, providing durable bonds in engine compartments and other high-heat areas.
- Automotive sector developments:Advancements cater to automotive applications, offering solutions for bonding components in engines, exhaust systems, and braking assemblies.
Environmental Adaptability
- Resistance to harsh chemicals:Adhesives are now more resistant to corrosive chemicals, ensuring durability in environments where exposure to aggressive substances is every day.
- Endurance in extreme conditions:High-temperature adhesives are designed to thrive in extreme situations, from sub-zero temperatures to exceptionally high heat, without compromising performance.
Manufacturing Techniques
- Precision application methods:Advanced manufacturing processes enable precise application of adhesives, ensuring optimal bonding without excess material usage.
- Customizable solutions:Tailored adhesive solutions are now available, precisely addressing specific industry requirements and application needs.
Sustainability and Safety
- Environmentally friendly formulations:Efforts have been made to develop eco-friendly options, reducing the environmental impact of high-temperature adhesives.
- Compliance with safety standards:Adhesives undergo rigorous testing to meet safety standards, ensuring they are reliable and safe for various applications.
The evolution of high-temperature adhesives has significantly transformed industries reliant on robust bonding solutions. These advancements have elevated the performance of materials in extreme conditions and expanded the possibilities for innovation and application across diverse sectors.
Could you provide a comparative analysis of various High-Temperature Adhesives?
High-temperature adhesives are a crucial component in industries where extreme heat resistance is necessary. From aerospace to automotive and manufacturing, these adhesives play a pivotal role in bonding materials that endure high thermal stresses. Choosing suitable adhesives for specific applications requires a nuanced understanding of their properties, strengths, and weaknesses. Let’s delve into a comparative analysis of various high-temperature adhesives to shed light on their differences:
Epoxy Adhesives
- Strengths:The material exhibits outstanding bonding strength, chemical resistance, and versatility.
- Weaknesses:Limited resistance to high temperatures, usually up to 250°F to 300°F (120°C to 150°C).
- Applications:This adhesive is perfect for joining metal, glass, ceramics, and select plastics in environments with moderate temperatures.
Polyimide Adhesives
- Strengths:This material has exceptional thermal stability and can withstand temperatures of up to 500°F to 600°F (260°C to 315°C).
- Weaknesses:It may require high cure temperatures and have limited flexibility.
- Applications:Heat-sensitive materials are often bonded using a standard technique in aerospace, electronics, and automotive industries.
Silicone Adhesives
- Strengths:Superior resistance to high temperatures, up to 500°F to 600°F (260°C to 315°C), flexibility, and excellent electrical insulation properties.
- Weaknesses:Lower mechanical strength compared to other adhesives.
- Applications:These materials are highly valued due to their thermal stability, flexibility, and widespread use in electronics, automotive, and household appliances.
Phenolic Adhesives
- Strengths: Excellent heat resistance, withstanding temperatures up to 500°F to 600°F (260°C to 315°C), and high chemical resistance.
- Weaknesses:Limited flexibility and may require higher pressure for bonding.
- Applications:High-temperature bonding of materials like wood, laminates, and some plastics is often used in the automotive and aerospace industries.
Cyanoacrylate Adhesives (CA)
- Strengths: Quick bonding, good temperature resistance up to 250°F to 300°F (120°C to 150°C), and excellent bonding with various substrates.
- Weaknesses:This statement highlights a limited ability to fill gaps and a lower resistance to certain chemicals.
- Applications:This adhesive is perfect for fast repairs and bonding small pieces in environments with high temperatures.
Critical Considerations for Selection
- Operating Temperature Range:Determine the maximum temperature the adhesive needs to withstand.
- Substrate Compatibility:Ensure compatibility with the materials being bonded.
- Curing Requirements:Consider curing time, temperature, and pressure needed for application.
- Mechanical Strength:Evaluate the required strength for the application.
- Environmental Factors:Assess exposure to chemicals, moisture, and other external factors.
Can you share successful case studies utilizing High-Temperature Adhesives?
In industrial applications, where high temperatures are the norm rather than the exception, the importance of high-temperature adhesives must be balanced. These specialized adhesives are engineered to withstand extreme heat, ensuring durability and reliability in environments that would render conventional adhesives ineffective. High-temperature adhesives are crucial in aerospace, automotive, and everyday consumer products. Let’s delve deeper into their significance and explore some successful case studies showcasing their effectiveness.
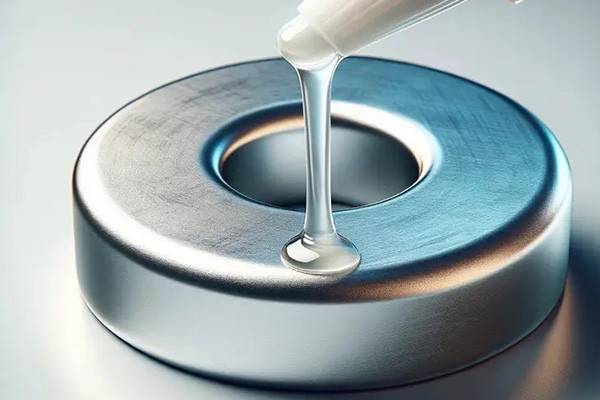
Key Features of High-Temperature Adhesives
- Heat Resistance:These adhesives can endure temperatures ranging from 300°F to over 2000°F, depending on the formulation.
- Chemical Stability:They maintain structural integrity even when exposed to harsh chemicals or solvents.
- Bond Strength:Exceptional bonding properties ensure a robust and reliable hold under extreme conditions.
- Versatility:They cater to various materials, including metals, ceramics, glass, and composites.
Successful Case Studies Utilizing High-Temperature Adhesives
Aerospace Industry
High-temperature adhesives are necessary in the aerospace sector, where components are subject to extreme temperatures during flight. A case study involving a leading aerospace manufacturer showcased the use of these adhesives in bonding critical components within jet engines. The manufacturer achieved enhanced durability and reliability by employing a specialized high-temperature adhesive, leading to increased engine performance and safety.
Automotive Manufacturing
Automotive manufacturers face the challenge of ensuring the longevity of parts exposed to high temperatures, such as engines and exhaust systems. A case study highlighted the implementation of high-temperature adhesives in bonding exhaust components. This improved heat and vibration resistance, reducing component failure and enhancing vehicle performance and longevity.
Electronics and Electrical Industry
High-temperature adhesives are instrumental in electronics, where miniaturization and high operating temperatures are prevalent. A case study involving a leading electronics manufacturer illustrated the use of these adhesives in bonding heat-sensitive components onto circuit boards. The adhesive’s ability to withstand elevated temperatures ensured the reliability and longevity of the electronic devices, reducing the risk of component detachment or failure due to heat exposure.
What are the common mistakes one should avoid when using High-Temperature Adhesives?
High-temperature adhesives are essential in various industries and are renowned for their ability to withstand extreme heat and harsh conditions. Whether in automotive, aerospace, electronics, or manufacturing, these specialized adhesives provide crucial bonding solutions. However, their practical use requires precision and care. Here are common mistakes to avoid when utilizing high-temperature adhesives:
- Inadequate Surface Preparation: Skipping surface cleaning and preparation steps can hinder adhesive effectiveness. For optimal adhesion, surfaces must be free from contaminants like oil, grease, dust, or rust. Use appropriate cleaning agents and methods recommended by the adhesive manufacturer.
- Ignoring Temperature Limits: Exceeding the specified temperature limits can compromise the adhesive’s integrity. Ensure the working temperature aligns with the adhesive’s recommended range. Operating beyond these limits may cause premature failure or weaken the bond.
- Improper Mixing Ratios: Some high-temperature adhesives are two-part systems requiring precise mixing ratios. Inaccurate measurements or incomplete mixing can result in weak bonds or incomplete curing. Always follow the manufacturer’s instructions meticulously.
- Insufficient Cure Time: Rushing the curing process with sufficient time can lead to adequate bond strength. Follow the recommended curing duration before subjecting the bond to high temperatures or mechanical stress.
- Neglecting Safety Precautions: High-temperature adhesives often emit fumes during curing. Neglecting safety gear like masks or proper ventilation can pose health risks. Always work in well-ventilated areas and utilize necessary safety equipment.
- Overestimating Bond Strength: While high-temperature adhesives are robust, overestimating their bond strength might lead to improper design or structural failure. Understand the adhesive’s limitations and ensure it meets the application’s requirements.
- Ignoring Compatibility Issues: Some substrates may not be compatible with certain high-temperature adhesives. Conduct compatibility tests on materials beforehand to prevent bond failure due to incompatibility.
- Neglecting Environmental Conditions: Environmental factors like humidity, UV exposure, or chemical exposure can affect adhesive performance. Consider these factors during application and ensure they align with the adhesive’s specifications.
- Inadequate Storage and Handling: Improper storage conditions or mishandling of adhesives can alter their properties. Store adhesives as per manufacturer guidelines, ensuring proper sealing and controlled temperature to maintain their effectiveness.
- Failing to Seek Expert Advice: If you need more certainty or the application process is uncertain, seeking guidance from adhesive specialists or the manufacturer can prevent costly mistakes. Their expertise can offer valuable insights and ensure proper adhesive use.
Are there any recommended DIY projects involving High-Temperature Adhesives?
High-temperature adhesives are industrial marvels and versatile tools for DIY enthusiasts. Their ability to withstand extreme heat makes them invaluable for various creative and practical projects. Whether you’re a hobbyist or a seasoned DIYer, here are some recommended projects that leverage the potential of high-temperature adhesives:
- Customized Woodworking Creations: It is expected to join different wood elements when making wooden furniture, intricate designs, or decorative pieces. This process is known as bonding, requiring special techniques and materials for a successful outcome. High-temperature adhesives, such as heat-resistant wood glues, offer durable connections, ensuring stability even in high-heat environments.
- DIY Automotive Repairs: Repairing components within the engine bay or exhaust system demands adhesives capable of withstanding intense heat. High-temperature epoxy or silicone adhesives are ideal for fixing gaskets, sealing cracks, or attaching automobile heat shields.
- Heat-Resistant Appliance Repairs: When you need to restore kitchen appliances such as ovens, stoves, or grills, you will require bonding solutions that can withstand high temperatures. High-temperature adhesives can help repair oven doors, seal stove elements, or mend grill components effectively.
- Metalworking and Fabrication: Fabricating metal structures, repairing machinery, or welding alternatives can utilize high-temperature adhesives. They aid in bonding metal components, providing robust and heat-resistant joints without welding.
- DIY Electronics and Circuitry: As electronics generate heat, using high-temperature adhesives is crucial for securing components. They help attach heat sinks, secure wires, or bond circuitry elements within electronic devices.
- Customized Jewelry Making: Crafting jewelry involves joining intricate pieces, and high-temperature adhesives offer a secure bond for metals and heat-resistant gem settings. They enable the creation of unique and durable jewelry pieces.
- DIY Crafts and Art Projects: Various art forms like pottery, ceramic art, or glass crafting benefit from high-temperature adhesives. They assist in repairing or assembling delicate art pieces that may be exposed to heat.
- Outdoor DIY Projects: When creating outdoor fixtures, garden ornaments, or fire pits, it’s essential to use materials that can withstand high temperatures. High-temperature adhesives aid in bonding materials like stones, ceramics, or metals for durable outdoor constructions.
- High-Heat Sealing and Insulation: Insulating pipes, sealing joints, or repairing fireplaces require heat-resistant sealing. High-temperature adhesives, such as heat-resistant sealants or tapes, offer reliable solutions.
- Customizing Sporting Equipment: Repairing sports gear like fishing rods and archery equipment or modifying equipment for extreme conditions can be achieved using high-temperature adhesives.
When embarking on DIY projects involving high-temperature adhesives, it’s crucial to follow manufacturer guidelines, ensure proper ventilation in workspaces, and prioritize safety. Additionally, understanding the specific properties and limitations of the adhesive selected for the project is essential for achieving durable and practical results.
How can High-Temperature Adhesives be safely removed?
High-temperature adhesives are crucial in various industries, from automotive to aerospace, where extreme heat resistance is non-negotiable. While these adhesives excel in bonding under intense temperatures, their removal can pose a challenge. This article explores the nuances of high-temperature adhesives and provides insights on removing them when needed.
Understanding High-Temperature Adhesive
- Resilient Bonds:High-temperature adhesives are designed to withstand extreme heat, making them ideal for applications in environments where conventional adhesives would fail.
- Diverse Applications:These adhesives find applications in industries like automotive, electronics, and aerospace, where components are exposed to elevated temperatures during operation.
Challenges in Removing High-Temperature Adhesives
- Adherence to Substrates:High-temperature adhesives form strong bonds with substrates, making removal a delicate process to avoid damaging the underlying surfaces.
- Residue Concerns:Improper removal can leave behind adhesive residues, affecting the performance of the treated components and complicating subsequent processes.
Safe Removal Techniques
Heat Application
- Gradual Heating:Use a heat gun or hot air blower to heat the bonded area gradually. Applying heat to the adhesive can help soften it, making it easier to peel or scrape off.
Chemical Solvents
- Acetone or Isopropyl Alcohol:Apply these solvents to the adhesive, allowing them to penetrate and weaken the bond. Exercise caution to prevent damage to sensitive materials.
Mechanical Methods
- Scraping or Abrasion:Use a plastic scraper or abrasive pad to remove the adhesive gently. Avoid metal tools to prevent surface scratches.
Soaking
- Immersion in Solvent:Soaking smaller components in a solvent can effectively loosen the adhesive. Ensure compatibility with the substrate material.
Precautions for Safe Removal
- Protective Gear:Wear gloves and safety goggles to safeguard against direct contact with adhesives and solvents.
- Ventilation:Work in a well-ventilated area or use an exhaust system to prevent inhalation of fumes from solvents.
- Test on a Small Area:Before applying any removal method, test it on a small, inconspicuous area to ensure it does not cause damage to the substrate.
Professional Assistance
- Consult Manufacturer Guidelines:Check the adhesive manufacturer’s guidelines for recommended removal techniques to ensure compliance with warranty and safety standards.
- Professional Services:In complex cases or for large-scale removal, consider seeking assistance from professionals with expertise in adhesive removal.
What are the anticipated future trends in High-Temperature Adhesive development?
In the realm of industrial applications, high-temperature adhesives play an indispensable role. These specialized adhesives are engineered to withstand extreme heat, offering durability and reliability in environments where conventional adhesives falter. Developing high-temperature adhesives has become a focal point as technology advances and industries evolve. What does the future hold for these crucial bonding agents? Let’s explore the anticipated trends shaping the evolution of high-temperature adhesives:
Advancements in Material Science
- Nanoengineered Formulations:Researchers are delving into nanostructures to create enhanced thermal stability and bonding strength adhesives. Nano-sized particles can significantly alter material properties, making adhesives more resilient to extreme temperatures.
- Ceramic-Based Adhesives:The integration of ceramics into adhesive formulations is gaining traction. Ceramics offer excellent resistance to heat, corrosion, and thermal cycling, making them a promising component for high-temperature adhesives.
Environmental Sustainability
- Bio-based Adhesives:The shift towards eco-friendly materials extends to high-temperature adhesives. Innovators are exploring bio-based sources to develop adhesives that are heat-resistant and environmentally sustainable.
- Recyclable and Biodegradable Variants:Future trends emphasize the development of adhesives that can be easily recycled or biodegraded without compromising their high-temperature performance, reducing environmental impact.
Customization and Application Specificity
- Tailored Solutions for Industries:The demand for high-temperature adhesives varies across industries. Future trends suggest a move towards customizable formulations to meet specific industry needs, whether in the aerospace, automotive, electronics, or energy sectors.
- Adaptability to Diverse Substrates:Adhesives that can bond diverse substrates under high-temperature conditions will be a sought-after innovation. Catering to various materials opens avenues for broader applications.
Enhanced Performance and Reliability
- Improved Durability and Longevity:The focus remains on developing adhesives that exhibit prolonged durability under extreme conditions. Withstandability to thermal cycling and aging without compromising performance is a crucial goal.
- Higher Temperature Tolerance:Anticipated advancements aim to push the boundaries of temperature tolerance in high-temperature adhesives, allowing them to function effectively in even more extreme heat environments.
Technological Integration
- Innovative Adhesives:Future trends foresee integrating smart technology into high-temperature adhesives. These characteristics could include self-healing properties, real-time monitoring of bond strength, or adaptive bonding capabilities.
- 3D Printing of High-Temperature Adhesives:Utilizing additive manufacturing techniques for high-temperature adhesive production offers precise control over material composition and structural design.
Regulatory Compliance and Safety
- Stringent Compliance Standards:With a growing emphasis on safety and regulatory standards, future trends predict advancements in adhesives that meet or exceed strict industry regulations concerning toxicity, emissions, and health hazards.
- Enhanced Safety Features:Developing adhesives with reduced flammability and volatility will continue to be a priority, ensuring safer working environments.
What’s the environmental impact of using High-Temperature Adhesives?
High-temperature adhesives have become indispensable in various industries, pivotal in assembling materials that endure extreme heat conditions. From aerospace engineering to automotive manufacturing, these adhesives boast unparalleled resilience in environments where traditional glues fail. However, while they offer exceptional performance, there’s a growing concern about their environmental impact. Exploring the ecological footprint of high-temperature adhesives unveils a complex landscape of benefits and challenges.
Environmental Impact
- Chemical Composition:High-temperature adhesives often contain compounds like epoxy resins, silicones, and cyanoacrylates. The production and decomposition of these substances can release volatile organic compounds (VOCs) and greenhouse gases, contributing to air pollution and climate change.
- Energy Consumption:The manufacturing process of these adhesives demands high energy input, often derived from non-renewable sources. The production process produces a considerable carbon footprint, further worsening the environmental impact.
- Waste Generation:Disposal of high-temperature adhesive residues poses a challenge. Improper disposal or incineration can release harmful substances, impacting soil, water, and air quality.
- Limited Biodegradability:Most high-temperature adhesives have limited biodegradability, remaining in the environment for extended periods, potentially causing harm to ecosystems.
Mitigation Strategies
- Research & Development:Investing in eco-friendly formulations is crucial. Innovations focusing on biodegradable components or renewable sources can mitigate the adverse effects of high-temperature adhesives.
- Recycling Programs:Implementing effective recycling programs for adhesive residues can reduce waste and minimize environmental impact.
- Regulatory Frameworks:Stringent regulations mandating environmentally friendly materials or enforcing proper disposal methods can encourage responsible production and usage of high-temperature adhesives.
- Consumer Education:Educating industries and users about the environmental repercussions of these adhesives can lead to more conscious choices and practices.
Could you provide expert tips to maximize the performance of High-Temperature Adhesives?
High-temperature adhesives are the backbone of industries that demand durability and resilience in extreme conditions. Maximizing their performance isn’t merely about applying the adhesive; it’s about understanding the nuances and employing expert strategies. Here are invaluable tips to unlock the full potential of high-temperature adhesives:
Understanding Application
- Surface Preparation:Cleanliness is paramount. Ensure surfaces are free from dirt, oil, moisture, and other contaminants that can compromise the adhesive bond. Proper surface preparation enhances adhesion.
- Temperature Consideration:Assess the operating temperature range. Match the adhesive’s temperature resistance with the application’s actual thermal demands. Choosing an adhesive that exceeds the required temperature range adds an extra layer of safety.
- Adhesive Selection:Different applications demand specific types of adhesives. Select the appropriate adhesive based on substrate materials, operating temperatures, and environmental conditions for optimal performance.
Application Techniques
- Correct Mixing Ratios:Follow manufacturer guidelines meticulously when mixing components. Deviating from the prescribed ratios can significantly impact adhesive strength and durability.
- Uniform Application:Apply the adhesive evenly and consistently. Uneven application can lead to weak spots and compromised bonding strength.
- Curing Conditions:Maintain ideal conditions, including appropriate temperature, humidity, and time. Deviating from these parameters can impede the adhesive’s curing process, affecting its performance.
Enhancing Performance
- Testing and Validation:Perform rigorous testing to validate the adhesive’s performance under simulated conditions. Real-world testing helps ascertain its reliability in actual applications.
- Joint Design:Optimize collaborative design to distribute stress evenly across the bonded surfaces. A well-designed joint minimizes potential weak points, enhancing the adhesive’s effectiveness.
- Post-Cure Inspections:Conduct thorough inspections to ensure the bond’s integrity after curing. Address any imperfections or irregularities promptly to prevent potential failures.
Longevity and Maintenance
- Environmental Factors:Consider ecological factors such as chemical exposure, moisture, and mechanical stress. Regular inspections and maintenance can help preemptively address potential degradation issues.
- Monitoring and Analysis:Implement a monitoring system to track the adhesive’s performance over time. Periodic analysis helps detect any deterioration and allows for timely interventions.
- Reapplication or Repair:In cases of degradation or damage, assess whether reapplication or repair is feasible. Prompt action can salvage the integrity of the bond and prevent further complications.
Conclusion
In industries where reliability is vital, high-temperature adhesives are unsung heroes. This guide has illuminated the multifaceted world of these specialized bonding agents, showcasing their versatility across industries and applications. From withstanding extreme temperatures to fostering innovation in cutting-edge projects, high-temperature adhesives epitomize resilience. As industries evolve and new challenges arise, the role of these adhesives will continue to expand, driving advancements and propelling us toward more innovative solutions. Armed with the knowledge shared here, may your endeavors with high-temperature adhesives be robust and visionary, pushing boundaries and crafting a future built on unyielding bonds.
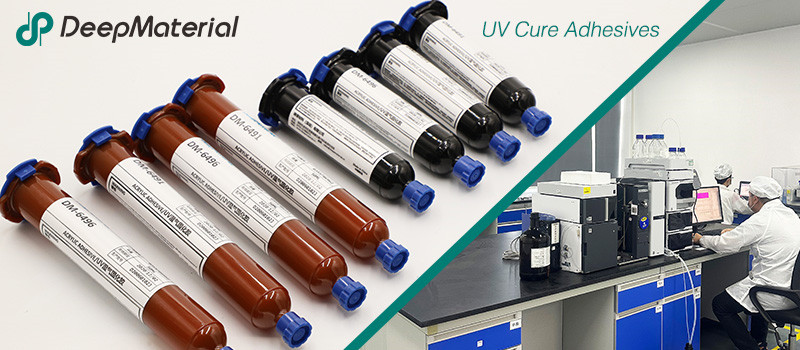
DeepMaterial
Based on the core technology of adhesives, DeepMaterial has developed adhesives for chip packaging and testing, circuit board level adhesives, and adhesives for electronic products. Based on adhesives, it has developed protective films, semiconductor fillers, and packaging materials for semiconductor wafer processing and chip packaging and testing. More…
UV Curing Adhesives
UV light cure have a number of benefits making them a popular choice among many product assembly and manufacturing applications. Many UV light cure adhesives can provide a nearly instantaneous bond to difficult substrates like glass and plastic. UV cure adhesives often require an accelerator or UV light for a bond to form.
Adhesive Blogs & News
The latest adhesive industry science and technology, Deepmaterial news, and market trends and forecasts.
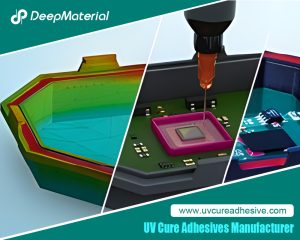
Main Chemical Characteristics of Conformal Coating
Main Chemical Characteristics of Conformal Coating Conformal coating, as a functional coating material widely used in fields such as electronics and aerospace, can form a uniform, continuous, and flexible protective film with certain protective properties on the surface of the coated object. The quality of its performance depends largely on its chemical characteristics, including
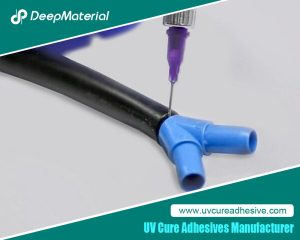
Exploring the Mystery and Application of Conformal Coating Spray
Exploring the Mystery and Application of Conformal Coating Spray In today’s highly developed field of electronic technology, protecting the reliability and stability of electronic devices is of paramount importance. Conformal coating spray, as an effective protective measure, is playing an increasingly important role. It not only provides excellent protective performance for electronic components but
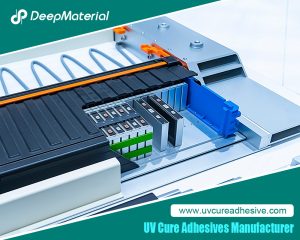
Research and Analysis on Types of Conformal Coatings
Research and Analysis on Types of Conformal Coatings Elaborate on the importance of conformal coatings in the electronics industry In today’s highly digital and intelligent era, electronic devices have become an indispensable part of people’s lives and work. From smart phones, tablets to automotive electronic systems and industrial control equipment, the application of electronic
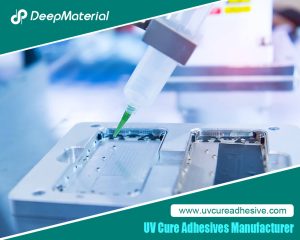
The Application and Development of Conformal Coating for Electronics
The Application and Development of Conformal Coating for Electronics In the present digital and intelligent era, electronic products have become an indispensable part of our lives. From mobile phones used for daily communication to laptops necessary for work and entertainment, from smart home appliances to advanced medical equipment, electronic products are everywhere. Their efficient
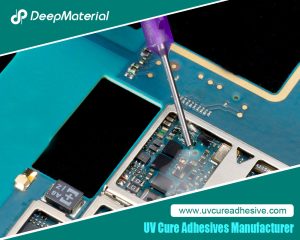
Electrical Potting Compound
Electrical Potting Compound In the vast field of modern electronic technology, Electrical Potting Compound plays a crucial role. It is like the invisible guardian inside electronic devices, providing reliable protection and stable performance support for various precise electronic components. Definition and Classification of Electrical Potting Compound Electrical Potting Compound is a special material
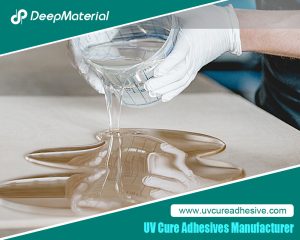
The Mystery and Application of Polyurethane Potting
The Mystery and Application of Polyurethane Potting In the modern industrial and technological fields, Polyurethane Potting is playing an increasingly important role. It not only provides reliable protection for various electronic devices and components but also shows unique advantages in optimizing performance and extending service life. What is Polyurethane Potting Polyurethane Potting is a