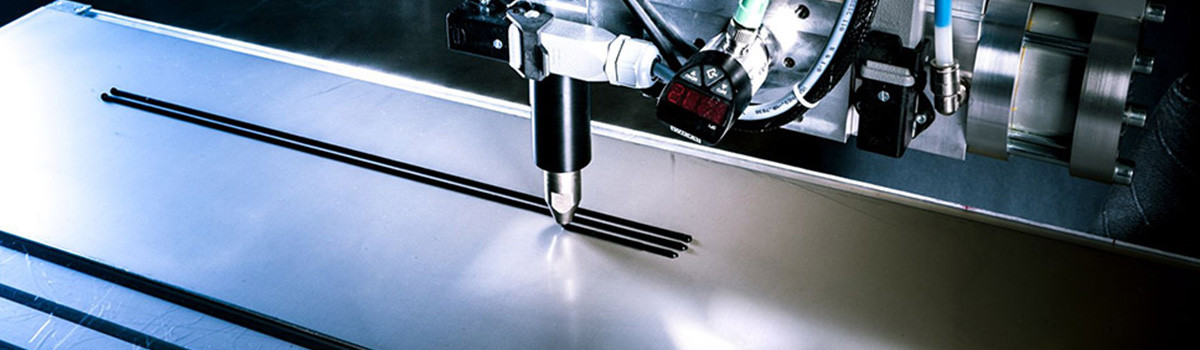
In the dynamic realm of manufacturing and fabrication, the adhesive bonding process stands as a cornerstone where precision and durability intertwine. Among these, “Heat-cured Adhesives” emerge as a beacon of innovation and reliability, leveraging controlled heat to forge bonds that endure the rigors of diverse applications. As we delve into the intricate world of these adhesives, their defining characteristics, chemical compositions, and unparalleled versatility, a narrative unfolds, spotlighting their pivotal role in automotive engineering, aerospace advancements, construction marvels, and the intricate tapestry of electronics manufacturing.
Table of Contents
ToggleWhat defines heat-cured adhesives and their primary characteristics?
Heat-cured adhesives are a specialized bonding agent renowned for their robust bonding capabilities achieved through a curing process induced by heat application. These adhesives find extensive use across industries due to their unique properties and strengths.
What Defines Heat-Cured Adhesives:
- Curing Mechanism:Heat-cured adhesives undergo a chemical reaction that leads to hardening or curing when exposed to elevated temperatures. This process typically involves cross-linking polymers within the adhesive, enhancing its strength and durability.
- Temperature Sensitivity:These adhesives necessitate specific temperature ranges for curing, typically higher than room temperature, ensuring proper bonding and structural integrity. The curing temperature varies depending on the adhesive composition and application requirements.
- Diverse Applications:Heat-cured adhesives cater to diverse applications, ranging from automotive and aerospace industries to electronics and construction, due to their ability to bond various materials, including metals, plastics, and composites.
- Strength and Durability:Upon complete curing, these adhesives exhibit exceptional strength, resilience against environmental factors, and resistance to chemical agents or extreme conditions, making them ideal for applications requiring robust bonding.
- Precision and Control:The curing process often demands precise control over temperature and duration to attain the desired bond strength and properties, requiring expertise and specialized equipment.
- Versatility in Forms:They are available in various forms, including liquid adhesives, films, and pastes, offering flexibility in application methods and catering to specific bonding requirements.
Primary Characteristics of Heat-Cured Adhesives:
- High Bond Strength:Post-curing, these adhesives offer superior bond strength, ensuring reliability in structural applications, such as in the assembly of aircraft components or automotive parts.
- Temperature Resistance:Their ability to withstand elevated temperatures post-curing makes them suitable for applications exposed to high thermal loads or environments.
- Chemical Resistance:Heat-cured adhesives often exhibit resistance to chemicals, oils, and solvents, enhancing their suitability for applications in harsh environments.
- Long-Term Stability:Once cured, these adhesives demonstrate long-term stability, maintaining their integrity over extended periods and contributing to the longevity of bonded materials.
- Customizable Properties:Manufacturers can adjust formulations to meet specific requirements, altering attributes like flexibility, viscosity, or curing time for tailored applications.
How do heat-cured adhesives differ from other types of adhesives?
In the realm of adhesives, the quest for the perfect bonding agent involves a myriad of choices. Among these, heat-cured adhesives are a distinctive option, offering unique characteristics and applications that set them apart from their counterparts. Understanding their differences is key to harnessing their full potential.
Differentiators of Heat-Cured Adhesives
Activation Process
- Heat-Triggered Bonding:Unlike conventional adhesives relying on air drying or solvent evaporation, heat-cured adhesives require specific temperatures to activate their bonding properties.
- Chemical Reaction:They transform exposure to heat, initiating a chemical reaction that solidifies the adhesive, creating a robust bond.
Controlled Cure Time
- Precise Timing:Heat-cured adhesives offer more control over the curing process, allowing operators to manage the duration and temperature required for optimal bonding.
- Rapid Bond Formation:Once exposed to the designated temperature, these adhesives generally achieve quicker curing times than alternatives, expediting production processes.
Enhanced Strength and Durability
- Exceptional Performance:The heat-induced chemical reaction often produces more robust, resilient bonds capable of withstanding harsh conditions such as extreme temperatures or environmental stressors.
- Uniform Bonding:They create more uniform and consistent bonds, minimizing weak spots within the adhesive joint.
Versatility in Applications
- Diverse Substrates: Heat-cured adhesives exhibit compatibility with a wide array of substrates, including metals, plastics, composites, and ceramics, expanding their usability across industries.
- Specialized Uses:Their robust nature makes them ideal for applications where high-strength bonding is crucial, such as in aerospace, automotive, and electronic industries.
Quality Assurance and Safety
- Quality Control:The controlled curing process ensures higher reliability and consistency in the bonding quality, reducing the likelihood of adhesive failure.
- Reduced VOCs:Compared to solvent-based adhesives, heat-cured formulations often produce fewer volatile organic compounds (VOCs), aligning with environmental and safety standards.
Challenges and Considerations
- Equipment Dependency:Proper curing necessitates precise temperature control and specialized equipment, adding to initial setup costs.
- Skill Requirement:Operators may require specific training to handle the heating process effectively, ensuring optimal results.
What are the key components or chemical compositions of these adhesives?
Heat-cured adhesives are a pivotal tool in various industries, bonding materials with precision and durability. Their efficacy lies in a complex chemical composition designed to activate under specific temperatures. Understanding the key components of these adhesives unveils their structural integrity and adhesive prowess.
Essential Components
- Resins:Primarily, heat-cured adhesives contain thermosetting resins, like epoxy, phenolic, or polyurethane. These resins possess molecular structures that enable them to solidify irreversibly upon heating, forming strong bonds.
- Curing Agents:These adhesives rely on curing agents or hardeners, initiating the cross-linking of resin molecules. Amine-based compounds, anhydrides, or peroxides are common curing agents, catalyzing the reaction with the resin upon exposure to heat.
- Fillers:Including fillers, such as silica, glass microspheres, or metal particles, augments the adhesive’s mechanical properties. Fillers enhance strength, stiffness, and resistance to environmental factors.
- Modifiers:Adding modifiers like plasticizers or toughening agents optimizes the adhesive’s flexibility, impact resistance, and overall performance. Ensuring the adhesive’s ability to withstand varying stresses and environmental conditions is crucial.
Chemical Compositions:
- Epoxy Resins:These adhesives predominantly feature epoxy resins composed of epoxide functional groups. When mixed with a hardener, typically amines or anhydrides, these groups undergo curing, forming cross-linked solid networks.
- Phenolic Resins:Comprising phenol and formaldehyde, phenolic resins undergo heat-induced polymerization. They produce rigid and durable bonds, ideal for applications requiring high-temperature resistance.
- Polyurethane Resins:Polyurethane adhesives incorporate isocyanate compounds, reacting with hydroxyl groups in the resin to form urethane linkages. This chemistry yields flexible and rigid bonds suitable for diverse substrates.
Chemical Reaction Mechanisms
- Polymerization:The curing agents trigger polymerization, forming three-dimensional networks within the adhesive. This irreversible process leads to the hardening of the adhesive upon exposure to heat.
- Cross-Linking:Reactive groups in the resin and hardener molecules form cross-links, creating a network structure. This interlocking of molecules enhances the adhesive’s strength and stability.
- Hydrogen Bonding:Some adhesives may also utilize hydrogen bonding mechanisms, where hydrogen atoms within the adhesive molecules form bonds with other electronegative atoms, reinforcing the adhesive’s cohesion.
How does the curing process through heat application work?
Heat-cured adhesives are versatile solutions that are extensively used in various industries due to their exceptional bonding capabilities and durability. The curing process involving heat application is pivotal in ensuring the adhesive achieves maximum strength and reliability. Let’s delve into the intricacies of this process and understand how it operates:
The Curing Mechanism
- Activation of Chemical Reaction:When subjected to heat, the curing agent within the adhesive becomes active, initiating the cross-linking process with the base resin.
- Cross-Linking Formation:Molecules within the adhesive start to interact and form a three-dimensional network. This network strengthens the adhesive, enhancing its mechanical properties.
Factors Influencing the Curing Process
- Temperature:The temperature required for curing depends on the specific adhesive composition. Higher temperatures generally expedite the curing process.
- Time:The duration of heat exposure is critical. It allows sufficient time for the chemical reactions and the bond to attain maximum strength.
- Pressure:Some heat-cured adhesives benefit from applied pressure during curing, ensuring optimal contact between the bonded surfaces.
Understanding the Heat Application
- Oven Curing:Many heat-cured adhesives undergo curing in specialized ovens. These ovens provide controlled temperatures and durations necessary for the curing process.
- Heat Guns or Lamps:Heat guns or lamps are used to apply localized heat, initiating the curing process for smaller-scale applications or repairs.
Advantages of Heat-Cured Adhesives
- High Strength:The curing process produces robust bonds, providing excellent strength and durability.
- Versatility:These adhesives can bond various materials, including metals, plastics, and composites.
- Resistance:Once cured, these adhesives resist heat, chemicals, and environmental factors.
Applications
- Aerospace and Automotive:Heat-cured adhesives are crucial in these industries for bonding components where high strength and reliability are paramount.
- Electronics:They are used in electronic assembly for bonding circuit components and ensuring stable connections.
- Construction:Heat-cured adhesives find applications in the structural bonding of buildings, enhancing structural integrity.
How are heat-cured adhesives utilized in the automotive sector?
In automotive engineering, precision, durability, and safety reign supreme. Integrating innovative materials and techniques is paramount in creating vehicles that meet stringent standards. One such game-changing component in the automotive sector is the utilization of heat-cured adhesives. Through their unique properties and application methods, these adhesives have become a cornerstone in modern automobile manufacturing.
Understanding Heat-Cured Adhesives
- Composition:Heat-cured adhesives are predominantly epoxy-based, containing resin and hardener components. These materials, when combined, undergo a chemical reaction upon exposure to heat, forming a durable bond.
- Application Process: The application of heat-cured adhesives involves precise temperature control. Once applied between surfaces, they are subjected to elevated temperatures, often within specific ranges, triggering the curing process. This process solidifies the adhesive, creating a robust bond.
Integral Role in Automotive Manufacturing
- Structural Integrity:Heat-cured adhesives contribute significantly to the structural integrity of automobiles. They are employed in bonding various components, such as body panels and roof structures, and even in the assembly of electric vehicle batteries. Reinforcing the structural strength not only reduces weight but also contributes to improved fuel efficiency.
- Enhanced Safety:The automotive industry prioritizes safety; heat-cured adhesives are pivotal. By effectively bonding components, these adhesives help create a rigid framework, which improves crashworthiness and overall safety.
- Vibration Dampening:Vehicles endure extensive vibrations during operation. Heat-cured adhesives act as excellent dampening agents, reducing vibrations and noise levels within the vehicle. This results in a quieter and smoother driving experience.
Advantages and Future Prospects
- Increased Efficiency:The application of heat-cured adhesives streamlines manufacturing processes effectively. They enable faster assembly, reduce the need for mechanical fasteners, and provide a more uniform stress distribution across bonded surfaces.
- Environmental Benefits:As automotive manufacturers strive for eco-friendly solutions, heat-cured adhesives align with sustainability goals. They enable the use of lightweight materials, aiding in reducing a vehicle’s carbon footprint by improving fuel efficiency.
- Future Innovations:Continuous research and development in adhesive technology aim to enhance heat-cured adhesives’ properties further. Advancements seek to optimize curing times, improve bonding strength, and expand applicability across diverse automotive components.
What role do they play in aerospace and aviation applications?
In the dynamic world of aerospace and aviation, where cutting-edge technology and precision engineering are paramount, the role of heat-cured adhesives cannot be overstated. These advanced adhesives play a crucial role in ensuring the structural integrity, safety, and performance of various components in aircraft and spacecraft.
Characteristics
- High Strength:Heat-cured adhesives exhibit exceptional bonding strength, making them suitable for joining materials that experience significant stress and load during aerospace operations.
- Temperature Resistance:These adhesives can withstand extreme temperatures, a crucial attribute for components exposed to atmospheric flight conditions and outer space.
- Chemical Stability:Heat-cured adhesives maintain their integrity in the presence of various chemicals, ensuring longevity and reliability in aerospace environments.
Applications in Aerospace and Aviation
Structural Bonding
In the construction of aircraft and spacecraft, structural integrity is paramount. Heat-cured adhesives are widely employed for bonding critical components such as:
- Fuselage panels
- Wing assemblies
- Tail sections
These adhesives provide a lightweight alternative to traditional fastening methods, reducing overall weight and enhancing fuel efficiency.
Composite Material Bonding
Aerospace components often utilize composite materials to balance strength and weight. Heat-cured adhesives are vital in bonding composite materials, ensuring a seamless integration of different layers and enhancing the overall structural integrity.
- Carbon fiber composites
- Fiberglass laminates
- Kevlar-reinforced structures
Electronics and Avionics
In the electronics and avionics systems of aircraft, where precision is critical, heat-cured adhesives are used for:
- Bonding circuit boards
- Securing sensors and transmitters
- Attaching heat-sensitive components
The ability of these adhesives to provide a secure bond without compromising the delicate electronic components is instrumental in maintaining the reliability of the aircraft’s systems.
Are there notable applications in construction and infrastructure?
In the ever-evolving landscape of construction and infrastructure, technological advancements continuously reshape how we build, and heat-cured adhesive stands as a testament to this evolution. This innovative adhesive has carved a niche, offering unparalleled strength, versatility, and efficiency in various construction applications.
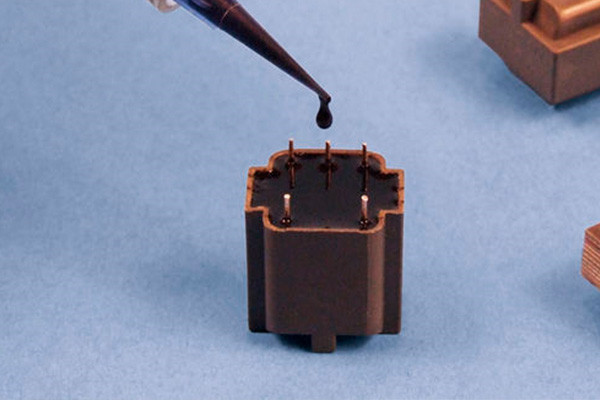
Notable Applications
Composite Materials in Structural Components
- Fiber-Reinforced Composites:Heat-cured adhesives are pivotal in bonding fiber-reinforced composite materials, such as carbon fiber or fiberglass, used in structural components like beams, columns, and panels. The adhesive’s ability to create a strong bond between dissimilar materials enhances structural integrity and durability.
High-strength bonding in Concrete Structures
- Concrete Repair:Heat-cured adhesives offer a reliable solution for bonding concrete elements in infrastructure maintenance and repair. This adhesive aids in repairing cracks, securing anchor bolts, and reinforcing structures, providing superior strength and preventing further deterioration.
Laminated Glass in Architectural Design
- Structural Glass Assemblies:Heat-cured adhesives facilitate the bonding of laminated glass, enabling the creation of innovative architectural designs. These adhesives ensure a secure bond between glass layers, enhancing safety and structural stability in facades, canopies, and other glass structures.
Bonding Metal Components
- Metal Fabrication:Heat-cured adhesives are instrumental in bonding metal components in construction. Whether in joining steel beams or assembling metal frames, these adhesives offer corrosion-resistant bonds, reducing the risk of structural failures.
Advantages and Future Prospects
- Strength and Durability:Heat-cured adhesives provide powerful bonds, enhancing the longevity and reliability of structures.
- Efficiency and Versatility:Their ability to bond diverse materials efficiently expands design possibilities and construction techniques.
- Environmental Benefits:These adhesives often have low volatile organic compound (VOC) emissions, aligning with sustainability goals in construction.
As technology advances, the potential applications of heat-cured adhesives in construction and infrastructure are poised for further growth. Research and development efforts focus on optimizing formulations for specific materials and environments, ensuring even greater reliability and adaptability.
How are these adhesives utilized in electronics and technology manufacturing?
Heat-cured adhesives belong to a class of thermosetting adhesives that undergo a chemical reaction when exposed to heat, transforming from a liquid or semi-liquid state into a solid and durable bond. These adhesives often contain a mixture of resin and hardener components, activating the curing process when subjected to specific temperatures.
Utilization in Electronics Manufacturing
In the intricate landscape of electronics manufacturing, heat-cured adhesives find widespread application across various stages:
- Component Assembly:During the assembly of electronic components onto circuit boards, heat-cured adhesives play a crucial role in bonding delicate parts. They ensure secure adhesion, facilitating the integration of components without compromising the electrical conductivity or functionality of the device.
- Encapsulation and Potting:Heat-cured adhesives are employed in encapsulating and potting electronic components. This process involves covering or embedding components within a protective material to shield them from environmental factors such as moisture, dust, and vibration. Heat-cured adhesives provide robust protection, enhancing the durability and reliability of electronic devices.
- Bonding Dissimilar Materials:Electronics often involve the bonding of dissimilar materials, such as metals, plastics, and ceramics. Heat-cured adhesives offer strong bonding capabilities across various substrates, enabling stable connections between different materials crucial for the structural integrity of electronic devices.
- Sealing and Insulation:In electronic devices, maintaining insulation and preventing the ingress of moisture or contaminants are paramount. Heat-cured adhesives are effective sealants, ensuring a tight seal around components and connections. They aid in maintaining the integrity of the device while providing electrical insulation.
Advantages and Considerations
The utilization of heat-cured adhesives in electronics and technology manufacturing offers several advantages:
- High Strength and Durability:These adhesives form strong and durable bonds, enhancing the overall reliability of electronic devices.
- Resistance to Environmental Factors:Heat-cured adhesives resist moisture, chemicals, and temperature variations, safeguarding electronic components.
- Customization and Versatility:They come in various formulations, allowing customization based on specific application requirements.
What are the distinct advantages of using heat-cured adhesives?
In adhesives, heat-cured adhesives stand out as a versatile and efficient bonding solution. Their unique properties and benefits make them a preferred choice across various industries. Let’s explore the distinct advantages of using heat-cured adhesives:
Superior Bond Strength
- Enhanced Durability:Heat-cured adhesives offer exceptional bond strength, creating durable connections that withstand harsh conditions, extreme temperatures, and mechanical stress.
- Uniform Adhesion:The controlled heating process ensures uniform distribution and bonding, producing superior adhesion between substrates, whether metals, plastics, or composites.
Customizable Application
- Versatility:These adhesives cater to a wide range of materials and applications. From the automotive to aerospace industries, their versatility allows for bonding diverse substrates effectively.
- Tailored Curing:Manufacturers can customize curing parameters like temperature, time, and pressure, optimizing the adhesive’s performance for specific bonding needs.
Increased Production Efficiency
- Rapid Curing:Heat-cured adhesives often have quick curing times, reducing assembly line downtime and accelerating production rates.
- Minimal Surface Preparation:Compared to other adhesives, they often require less surface preparation, saving time and resources during application.
Enhanced Performance
- Temperature Resistance:Heat-cured adhesives maintain their integrity at high temperatures, ensuring structural stability in environments where other adhesives might fail.
- Chemical Resistance:They exhibit excellent resistance to chemicals and solvents, maintaining bond integrity in challenging environments.
Environmental Friendliness
- Low VOC Emissions:Many heat-cured adhesives have formulations with low volatile organic compound (VOC) emissions, contributing to a more eco-friendly manufacturing process.
- Reduced Waste:Their precise application and curing process reduce material wastage, aligning with sustainability initiatives.
Consistent Quality
- Uniform Results:The controlled heating process ensures consistent bonding quality, minimizing variations in adhesion strength between batches or applications.
- Reliability:Heat-cured adhesives offer reliable performance, contributing to bonded assemblies’ overall quality and longevity.
Are there any limitations or challenges associated with their application?
Heat-cured adhesives are renowned for their robust bonding capabilities across various industries. However, despite their effectiveness, these adhesives have specific limitations and challenges in their application, impacting their usage in particular scenarios.
Understanding Heat-Cured Adhesives
- Process Overview:Heat-cured adhesives rely on heat application to initiate bonding, requiring precise temperature control.
- Types and Composition:Various types exist, including epoxy, polyurethane, and acrylic, each with distinct compositions and curing requirements.
- Industrial Significance:These adhesives find widespread use in aerospace, automotive, and construction industries due to their high strength and durability.
Limitations in Application
- Temperature Sensitivity:Heat-cured adhesives necessitate specific temperature ranges for curing, limiting their use in environments where maintaining such temperatures is challenging.
- Substrate Compatibility:Some substrates may be sensitive to high temperatures, making them unsuitable for heat-cured adhesives.
- Time Sensitivity:The curing process requires precise timing, impacting large-scale applications where time management becomes critical.
- Equipment Dependency:Utilizing heat-cured adhesives demands specialized equipment for precise temperature control, increasing operational costs.
- Environmental Constraints:In environmentally sensitive applications, the high temperatures needed for curing can pose challenges or safety concerns.
Challenges in Practical Implementation
- Adhesion Quality Control:Achieving uniform and strong adhesion across surfaces can be challenging, impacting the overall quality of the bond.
- Process Complexity: Applying heat-cured adhesives demands skilled labor and careful handling, increasing the likelihood of errors.
- Cost Considerations:The initial investment in equipment and expertise required for heat-cured adhesives can substantially affect project costs.
- Health and Safety:Handling high temperatures during the curing process poses potential risks to worker safety, necessitating stringent safety protocols.
Overcoming Limitations and Future Prospects
- Research and Development:Ongoing advancements aim to mitigate limitations by developing adhesives with broader temperature ranges and improved substrate compatibility.
- Technological Innovations:Integrating automated systems and advanced equipment enhances precision and efficiency in applying heat-cured adhesives.
- Diversification of Applications:Exploring new industries and adapting the technology for different purposes can expand the utility of heat-cured adhesives.
How does the curing temperature affect the performance of these adhesives?
Heat-cured or thermosetting adhesives encompass a diverse range of bonding agents activated by elevated temperatures. These adhesives, commonly epoxy or acrylic-based, undergo a chemical reaction during curing, transforming from a liquid or semi-liquid state to a hardened, durable bond.
The Crucial Role of Curing Temperature
The curing process’s temperature significantly influences the adhesive’s final characteristics and bond strength. Several key aspects are profoundly affected:
- Bond Strength:The curing temperature directly impacts the adhesive’s bond strength. Higher temperatures often result in stronger bonds due to enhanced cross-linking within the adhesive molecules. This results in increased structural integrity and load-bearing capacity.
- Cure Time:Curing at higher temperatures generally accelerates the process, reducing the time required for the adhesive to reach its maximum strength. Conversely, lower temperatures may extend the curing time, affecting production timelines.
- Chemical Resistance and Durability:Optimal curing temperatures contribute to the adhesive’s chemical resistance and overall durability. Properly cured adhesives exhibit heightened resistance to environmental factors such as moisture, chemicals, and temperature variations.
- Flexibility and Toughness:Curing temperature affects the balance between the flexibility and toughness of the adhesive. Higher temperatures yield a more rigid bond, while lower temperatures produce a more flexible but potentially less robust bond.
Optimizing Curing Temperatures for Superior Performance
The ideal curing temperature demands a delicate balance, considering the specific adhesive, substrate, and intended application. Several factors influence this optimization:
- Manufacturer Recommendations:Adhesive manufacturers often provide guidelines specifying recommended curing temperatures and durations for their products. Adhering to these guidelines ensures optimal performance.
- Substrate Compatibility:Different substrates may require varied curing temperatures for optimal bonding. Understanding the substrate’s thermal limitations is crucial to prevent damage during curing.
- Process Control:Employing precise temperature control mechanisms during curing processes, such as ovens or infrared systems, ensures consistency and reliability in bond strength.
How does substrate material impact the curing process?
In adhesives, heat-cured adhesive is a versatile and efficient solution for bonding various materials. However, the effectiveness of the curing process is greatly influenced by the substrate material used. Let’s delve into the intricacies of how different substrate materials impact the curing process of heat-cured adhesives.
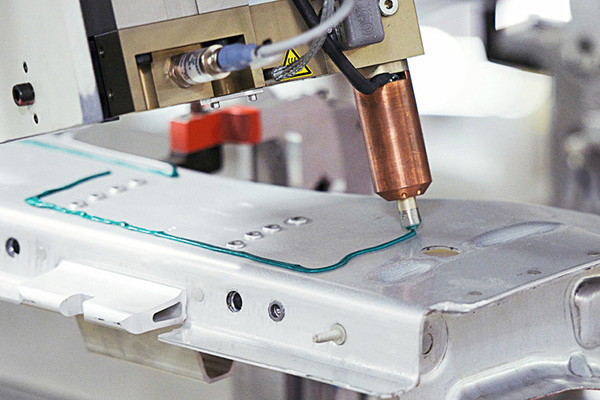
Importance of Substrate Material in Curing
- Chemical Compatibility:Substrate materials vary widely, and their chemical composition directly influences how heat-cured adhesives interact during curing.
- Adhesion Strength:The choice of substrate material can determine the adhesive’s ability to form a strong bond. Some materials might react differently to heat curing, impacting the final bond strength.
Impact of Different Substrate Materials
Metals
- Conductivity:Metals conduct heat efficiently, expediting the curing process of heat-activated adhesives.
- Oxidation Sensitivity:Certain metals are prone to oxidation when exposed to high temperatures, potentially altering the adhesive’s curing properties.
Plastics
- Thermal Conductivity:Plastics have lower thermal conductivity, requiring longer exposure to heat for proper curing. Some plastics might be sensitive to high temperatures, affecting their structural integrity.
- Chemical Composition:Diverse plastic compositions react uniquely to heat curing, demanding precise temperature and time control for optimal adhesion.
Composites
- Layered Structure:Composite materials, comprising multiple layers, pose a challenge during heat curing. Variations in layer composition demand careful consideration to ensure uniform curing throughout the substrate.
- Fiber Orientation:The orientation of fibers within composites can affect heat transfer, impacting the curing process. Adjustments in curing parameters are essential to achieve consistent bonding.
Optimizing Curing Parameters for Different Substrates
- Temperature Control:Understanding the substrate’s heat tolerance is crucial. Adjusting curing temperatures within the safe range prevents substrate damage while promoting adequate adhesion.
- Dwell Time:Substrate materials dictate the required duration for heat exposure. Monitoring and optimizing dwell time ensure complete curing without compromising substrate integrity.
- Surface Preparation: Pre-treating substrates to remove contaminants and improve surface roughness enhances adhesive bonding. Different materials may require specific preparation methods for optimal results.
What role does the curing duration play in achieving optimal bond strength?
When securing bonds in various industries, heat-cured adhesives stand out for their efficacy and versatility. However, achieving the optimal bond strength is more than just using the suitable adhesive. It heavily relies on the curing duration. Let’s delve into the pivotal role that curing duration plays in ensuring the best possible bond strength.
The Basics of Heat-Cured Adhesive
- Composition:Heat-cured adhesives consist of thermosetting polymers that undergo a chemical change upon exposure to heat, transforming from a liquid or semi-liquid state to a solid.
- Application:These adhesives find extensive use in industries such as aerospace, automotive, electronics, and construction due to their robust bonding capabilities under extreme conditions.
Understanding Curing Duration
- Defining Curing Duration:Curing duration refers to the time the adhesive needs to be exposed to specific temperatures for the chemical reactions to occur and achieve optimal bonding strength.
- Impact on Bond Strength:The duration directly affects the bond’s strength, durability, and reliability.
Factors Influencing Optimal Curing Duration
- Adhesive Type:Different heat-cured adhesives have varying chemical compositions, requiring specific durations and temperatures for curing.
- Environmental Conditions:Temperature and humidity can influence curing duration. Higher temperatures generally expedite the curing process, but excessively high temperatures can adversely affect the bond quality.
- Substrate Material:The type and condition of bonded materials impact the curing duration. Porous materials might absorb adhesive differently, affecting the curing time.
Significance of Correct Curing Duration
- Strength and Reliability:A well-cured adhesive ensures maximum bond strength, which is critical for applications subjected to high stress or varying environmental conditions.
- Durability:Optimal curing duration enhances the adhesive’s resistance to environmental factors like temperature fluctuations, moisture, and chemicals.
- Prevention of Failure:Inadequate curing time can weaken bonds, leading to premature failure and potential safety hazards.
Achieving Optimal Bond Strength
- Follow Manufacturer’s Guidelines:Following the manufacturer’s instructions regarding curing temperature and duration is crucial for achieving the desired bond strength.
- Quality Control:Regular testing and quality control measures ensure the curing process meets specified standards, preventing potential issues.
Are there specific environmental conditions that influence curing efficacy?
Heat-cured adhesives are pivotal in various industries, offering robust bonding solutions. The efficacy of these adhesives in achieving optimal curing depends largely on specific environmental conditions. Exploring the influence of environmental factors on the curing process provides crucial insights for maximizing adhesive performance.
Factors Impacting Curing Efficacy
Heat-cured adhesives rely on controlled environmental conditions to achieve the desired bond strength. Several factors significantly influence their curing efficacy:
Temperature
- Optimal Range:Heat-cured adhesives require specific temperatures for curing. Deviations from this range can hinder or prolong the curing process.
- High Temperatures:Excessive heat can lead to premature curing, affecting the adhesive’s properties and compromising bond strength.
- Low Temperatures:Insufficient heat might impede the curing process, resulting in incomplete bonding.
Humidity
- Balanced Moisture:Certain adhesives are sensitive to moisture levels. High humidity can interfere with curing, causing inadequate bond strength.
- Dry Environments:Arid conditions might affect the adhesive’s ability to cure uniformly, impacting its effectiveness.
Pressure
- Uniform Application:Adequate and consistent pressure ensures proper contact between surfaces, facilitating optimal curing.
- Insufficient Pressure:Inadequate pressure may result in voids or uneven bonding, affecting the adhesive’s performance.
Environmental Conditions and Curing Process
Understanding how different environments influence the curing process is crucial:
- Climate Variations:Regions with extreme temperatures or humidity levels can challenge curing. Manufacturers must consider these variations during adhesive application and curing.
- Controlled Environments:Industries often employ controlled environments to optimize curing conditions. Maintaining specific temperature and humidity levels during application is necessary to ensure consistent bonding.
- Time Consideration:Environmental factors may impact curing time. Variances in temperature and humidity might necessitate adjustments to fixing durations for consistent and robust bonding.
Mitigating Environmental Challenges
To enhance curing efficacy despite varying environmental conditions, several measures can be taken:
- Environmental Monitoring: Regular temperature and humidity monitoring during the curing process allows for timely adjustments, ensuring optimal conditions for adhesive bonding.
- Adhesive Formulation:Innovations in adhesive formulations aim to improve resistance to environmental variations, enhancing curing efficacy across diverse conditions.
- Equipment Calibration:Calibrating curing equipment helps maintain precise control over temperature and pressure, minimizing the impact of environmental fluctuations.
How does proper application technique impact the final bond quality?
Heat-cured or heat-activated adhesive is a bonding agent that relies on elevated temperatures to cure and establish a secure bond between materials. This adhesive is commonly used in various industries due to its strength, durability, and versatility.
The Importance of Proper Application Technique
Achieving the desired bond strength and durability with heat-cured adhesive hinges on the precision and care applied during the application process. Here’s how proper technique makes a difference:
Uniform Heat Distribution
- Issue: Inconsistent heat application can lead to uneven curing.
- Impact:Weak spots in the bond, compromising overall strength.
- Solution: Employ precise heat sources and distribution methods for uniform curing.
Surface Preparation
- Issue:Inadequate surface preparation hinders adhesive penetration.
- Impact: Weakened bond and potential for delamination.
- Solution:Thoroughly clean and prepare surfaces, removing contaminants for optimal adhesion.
Temperature and Time Control
- Issue:Incorrect curing temperatures or durations can compromise bond integrity.
- Impact:Suboptimal strength and longevity.
- Solution:Adhere strictly to the recommended temperature and time parameters for optimal curing.
Pressure Application
- Issue:Insufficient pressure during curing can result in weak bonds.
- Impact:Reduced bond strength and potential for bond failure.
- Solution:Apply the appropriate pressure to ensure intimate contact between substrates during curing.
Benefits of Mastering Application Technique
Proper application techniques not only address potential issues but also unlock numerous benefits, including:
- Enhanced Bond Strength:Precise application ensures that the adhesive forms a robust and durable bond, maximizing its strength.
- Extended Lifespan:A well-applied heat-cured adhesive bond exhibits increased resistance to environmental factors, contributing to a longer lifespan.
- Cost Savings:Minimizing the risk of bond failure through proper application reduces the need for rework and repairs, ultimately saving costs.
What are the standard methods for testing the strength of heat-cured adhesives?
Heat-cured or thermosetting adhesives undergo a curing process by applying heat. This results in a chemical reaction that enhances the adhesive’s strength, durability, and temperature resistance. Commonly used in aerospace, automotive, and electronics industries, these adhesives demand precise testing methods to guarantee optimal performance.
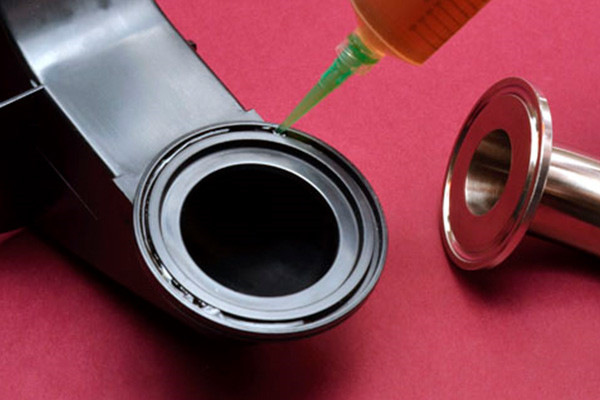
Tensile Strength Testing
One of the fundamental tests for heat-cured adhesives is tensile strength testing. This method evaluates the adhesive’s ability to withstand pulling forces without breaking. The process involves applying force to a bonded specimen until it fractures, providing crucial insights into the adhesive’s performance under tension.
Key considerations for tensile strength testing
- Specimen preparation:Ensure standardized specimen dimensions and bonding conditions.
- Testing conditions:Maintain a controlled environment, including temperature and humidity, to eliminate external variables.
- Reporting:Results should include maximum load, elongation, and failure mode.
Shear Strength Testing
Shear strength testing assesses the adhesive’s resistance to forces parallel to the bonded surfaces. This method is particularly relevant for applications where forces are applied parallel to the bond line, such as structural bonding.
Crucial aspects of shear strength testing
- Sample geometry:Use specimens with standardized dimensions and consider joint configurations relevant to the application.
- Loading conditions:Apply a uniform and controlled force to induce shear stress.
- Analysis:Evaluate the failure mode to understand the bond’s performance under shear forces.
Peel Strength Testing
Peel strength testing is indispensable in scenarios where forces are perpendicular to the bonded surfaces. This method measures the force required to separate related materials at an angle.
Key elements of peel strength testing
- Sample preparation:Follow standardized procedures for specimen dimensions and surface preparation.
- Peel angle:Conduct tests at the specified angle relevant to the application.
- Interpretation:Analyze the failure mode to determine the adhesive’s peel resistance.
Impact Resistance Testing
Evaluating the adhesive’s impact resistance is crucial for applications subjected to sudden impacts. This test involves striking a bonded specimen with controlled force to simulate impact conditions.
Considerations for impact resistance testing
- Test apparatus:An instrumented impact tester ensures precise control over impact parameters.
- Specimen selection:Opt for specimens representative of the actual application conditions.
- Reporting: Record impact energy, failure mode, and any visible damage.
How is the reliability and durability of these adhesives evaluated?
These adhesives undergo meticulous evaluation processes to determine their reliability and durability. These key aspects involve comprehensive testing methods and standards to ensure the adhesives meet stringent requirements. Here’s an insight into how the reliability and durability of heat-cured adhesives are evaluated:
Initial Assessment
- Material Composition Analysis:Understanding the adhesive formulation, including resin types, curing agents, and additives.
- Compatibility Testing:Assessing compatibility with various substrates to ensure optimal bonding strength.
Reliability Testing
- Temperature Resistance:The adhesive is subjected to varying temperature extremes to assess its performance in harsh conditions.
- Chemical Resistance:When evaluating the adhesive, it’s essential to test its resistance to chemicals and solvents it might encounter in its application environment.
- Humidity and Moisture Resistance:Testing the adhesive’s ability to withstand high humidity or moisture-prone conditions without compromising its bond strength.
Mechanical and Physical Properties Evaluation
- Tensile and Shear Strength Tests: Assessing the adhesive’s ability to withstand pulling or shearing forces.
- Flexibility Testing: Evaluating the adhesive’s ability to maintain bonding integrity under stress or movement.
- Impact Resistance:Determining the adhesive’s resilience against sudden impacts or vibrations.
- Peel and Cleavage Testing:Measuring the adhesive’s resistance to delamination or separation from the substrate.
Long-Term Durability Assessment
- Accelerated Aging Tests:Mimicking extended usage conditions to predict the adhesive’s performance over time.
- Creep and Fatigue Testing:Assessing how the adhesive withstands continuous stress or repetitive loading.
- Environmental Exposure Testing:Subjecting the adhesive to UV radiation, salt spray, or other environmental factors it might encounter in its intended application.
Standards Compliance
- Adherence to Industry Standards:Ensuring the adhesive meets specific industry standards (e.g., ASTM, ISO) for reliability and durability.
- Certifications:The process involves obtaining certifications that validate the adhesive’s suitability for particular applications.
Are there specific tests for assessing temperature resistance or aging effects?
Heat-cured adhesives are pivotal in various industries, offering robust bonding solutions in high-temperature environments. As these adhesives endure extreme conditions, they must assess their temperature resistance and aging effects through specific tests.
Importance of Assessing Temperature Resistance and Aging Effects
- Performance Assurance:Understanding how heat-cured adhesives withstand elevated temperatures ensures reliability in demanding applications.
- Safety Compliance:Industries like automotive, aerospace, and electronics require adhesives that maintain integrity under extreme heat for safety and operational purposes.
- Longevity:Assessing aging effects aids in predicting the adhesive’s lifespan and performance over time, ensuring durability and cost-effectiveness.
Specific Tests for Assessing Temperature Resistance
- Thermal Gravimetric Analysis (TGA):Measures weight changes as the adhesive is heated, indicating decomposition temperatures and thermal stability.
- Differential Scanning Calorimetry (DSC): Assesses changes in heat flow, detecting phase transitions and degradation temperatures.
- Thermomechanical Analysis (TMA):Evaluates dimensional changes and material properties concerning temperature variations.
- Peel and Shear Tests at Elevated Temperatures:Determining the adhesive’s strength under specific heat conditions is crucial for bonding performance.
- Aging Tests (Accelerated Aging, Aging in Real-Time):Simulate extended exposure to elevated temperatures to predict long-term effects on adhesive properties.
Insights from Testing
- Threshold Temperatures:Identify the temperature range within which the adhesive maintains structural integrity.
- Degradation Points:Pinpoint temperatures where the adhesive begins to degrade or lose its bonding strength.
- Residual Strength:Assess the adhesive’s capacity to retain adequate bonding capabilities post-exposure to high temperatures.
- Aging Effects:Evaluate changes in adhesion, cohesion, viscosity, and other properties over time and under heat stress.
What advancements are anticipated in heat-cured adhesive technology?
Heat-cured adhesive technology stands at the forefront of innovation, poised for significant advancements that promise to revolutionize manufacturing and assembly processes across industries. As researchers and engineers continue to push the boundaries of this technology, several key advancements are anticipated:
Enhanced Formulations
- Tailored Properties:Anticipate formulations designed for specific applications, offering varying degrees of flexibility, strength, and curing times to suit diverse industry needs.
- Adhesive Customization:Advancements may enable customizable adhesives, allowing manufacturers to fine-tune viscosity and adhesion strength characteristics.
Nanotechnology Integration
- Nano-Enhanced Adhesives:Integrating nanomaterials into heat-cured adhesives could yield superior strength, conductivity, and self-healing properties.
- Enhanced Performance:Nanotechnology infusion may enhance thermal and electrical conductivity, crucial for applications in electronics and aerospace.
Smart and Functional Adhesives
- Self-Monitoring Properties:Future adhesives might incorporate sensors to detect stress, temperature, or structural integrity, providing real-time feedback on bond health.
- Self-Repairing Capabilities:Anticipate adhesives with self-repairing properties, automatically sealing minor fractures or weaknesses in bonded surfaces.
Biocompatible and Sustainable Solutions
- Bio-Based Materials:Advancements may focus on developing adhesives derived from renewable sources, reducing environmental impact, and enhancing biocompatibility for medical applications.
- Biodegradability:Future formulations prioritize biodegradable properties, aligning with industry sustainability goals.
Improved Manufacturing Processes
- Rapid Curing Technologies:Innovations in curing methods could significantly reduce curing times, expedite assembly processes, and enhance production efficiency.
- Compatibility with Automation:Anticipate developments that make heat-cured adhesives more compatible with automated manufacturing systems, optimizing integration and efficiency.
Advanced Application Techniques
- Precision Application:Advancements in application methods may enable more precise and controlled dispensing of adhesives, ensuring optimal bonding with minimal waste.
- Novel Bonding Surfaces: Research could lead to adhesives capable of bonding previously challenging materials, expanding the scope of applications across industries.
How might these innovations impact various industries and manufacturing processes in the future?
The emergence of heat-cured adhesive technology has sparked a transformative wave across various industries, promising a paradigm shift in manufacturing processes. This cutting-edge innovation offers a versatile and efficient solution for joining materials, profoundly influencing diverse sectors. Let’s delve into the potential impacts across industries:
Automotive Sector
- Lightweight Construction:Heat-cured adhesives enable the bonding of dissimilar materials like metal to plastic, facilitating the design of lighter and fuel-efficient vehicles.
- Enhanced Safety:Improvements in adhesive strength contribute to reinforcing structural components, elevating crash resistance, and overall vehicle safety.
- Streamlined Production:Adopting these adhesives accelerates assembly processes, reducing manufacturing time and costs.
Aerospace Industry
- Weight Reduction:By replacing traditional fastening methods with heat-cured adhesives, aircraft can achieve significant weight savings, enhancing fuel efficiency.
- Durability and Performance:These adhesives bolster the integrity of composite structures, ensuring resilience against extreme conditions and increasing aircraft longevity.
- Design Flexibility:This innovation allows for more innovative and aerodynamically efficient designs by facilitating intricate bonding in aircraft components.
Construction and Infrastructure
- Structural Integrity:Heat-cured adhesives contribute to robust bonding in building materials, bolstering structural stability and resilience.
- Sustainable Practices:Their application supports eco-friendly construction by reducing the need for mechanical fasteners, minimizing waste, and optimizing material usage.
- Rapid Construction:Faster curing times of these adhesives expedite construction projects, enabling quicker completion without compromising quality.
Electronics Manufacturing
- Miniaturization and Precision:Heat-cured adhesives facilitate precise bonding in electronic components, supporting the trend toward smaller and more powerful devices.
- Heat Dissipation:Their thermal conductivity aids in efficient heat dissipation, which is crucial for maintaining the performance and longevity of electronic devices.
- Improved Reliability:Enhanced bonding strength ensures more durable connections, reducing the risk of component failure.
General Manufacturing
- Versatility:These adhesives offer compatibility with various materials, opening avenues for innovation in diverse manufacturing processes.
- Cost Efficiency:Streamlined production, reduced material waste, and enhanced efficiency translate to cost savings across industries.
- Adaptable to Automation: The curing process of heat-cured adhesives aligns well with automated manufacturing, fostering seamless integration into automated production lines.
CONCLUSION
As we conclude this exploration, it’s evident that these adhesives stand as stalwarts in forging durability across diverse industries. Their versatility, from automotive advancements to aerospace marvels, construction feats, and intricate electronics, speaks volumes about their indispensability. Yet, within their robustness lies an ongoing quest for innovation. The future promises leaps in Heat-cured Adhesive technology, potentially revolutionizing manufacturing landscapes. It’s an invitation to delve deeper, to consider these adhesive wonders for specific bonding needs, and to anticipate the transformative impact of evolving adhesion technology on the tapestry of industries yet to unfold. Embrace the enduring strength of Heat-cured Adhesives and envision the boundless possibilities they hold for the future of manufacturing and beyond.
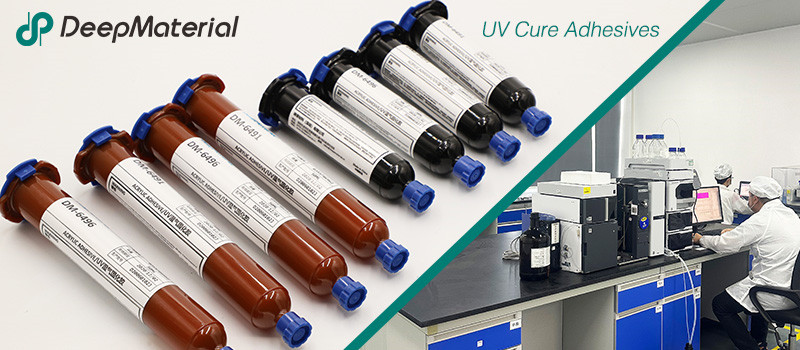
DeepMaterial
Based on the core technology of adhesives, DeepMaterial has developed adhesives for chip packaging and testing, circuit board level adhesives, and adhesives for electronic products. Based on adhesives, it has developed protective films, semiconductor fillers, and packaging materials for semiconductor wafer processing and chip packaging and testing. More…
UV Curing Adhesives
UV light cure have a number of benefits making them a popular choice among many product assembly and manufacturing applications. Many UV light cure adhesives can provide a nearly instantaneous bond to difficult substrates like glass and plastic. UV cure adhesives often require an accelerator or UV light for a bond to form.
Adhesive Blogs & News
The latest adhesive industry science and technology, Deepmaterial news, and market trends and forecasts.
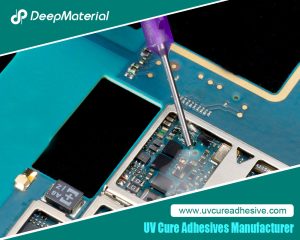
Biocompatibility of LED UV Glue Adhesive and Its Application Potential in Medical and Food Packaging Fields
Biocompatibility of LED UV Glue Adhesive and Its Application Potential in Medical and Food Packaging Fields LED UV glue adhesive has been widely applied in numerous fields due to its advantages such as rapid curing and easy operation. However, in fields with stringent safety requirements like medical and food packaging, its biocompatibility after curing becomes
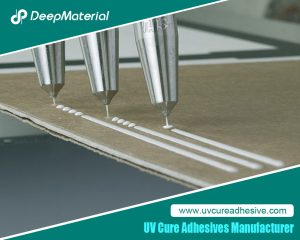
Biocompatibility of LED UV Glue Adhesive and Its Application Potential in Medical and Food Packaging Fields
Biocompatibility of LED UV Glue Adhesive and Its Application Potential in Medical and Food Packaging Fields LED UV glue adhesive has been widely applied in numerous fields due to its advantages such as rapid curing and easy operation. However, in fields with stringent safety requirements like medical and food packaging, its biocompatibility after curing
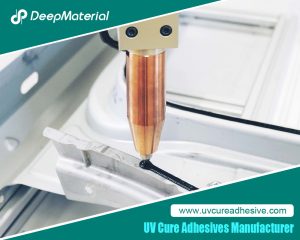
Exploring the Environmental Performance of UV Glue and Strategies for Optimizing Odor and VOC Content
Exploring the Environmental Performance of UV Glue and Strategies for Optimizing Odor and VOC Content UV glue, as an adhesive that achieves rapid curing through ultraviolet (UV) light irradiation, has been widely applied in numerous fields such as electronics, optics, healthcare, and automobiles, thanks to its advantages of fast curing speed, high bonding strength, and
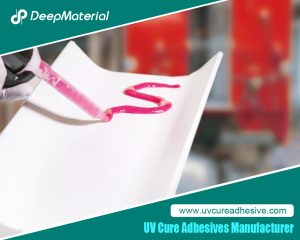
Compatibility Analysis and Countermeasures of LED UV Glue with Automated Production Equipment
Compatibility Analysis and Countermeasures of LED UV Glue with Automated Production Equipment LED UV glue has been widely used in modern manufacturing due to its advantages such as fast curing speed, high bonding strength, and environmental friendliness. However, in the automated production process, if there are problems with the adaptability between the glue and equipment
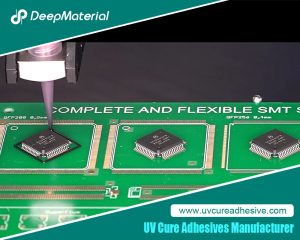
Influence of Viscosity and Thixotropy of Glue on the Quality of Glue Dots in the Dispensing Process and Solutions
Influence of Viscosity and Thixotropy of Glue on the Quality of Glue Dots in the Dispensing Process and Solutions The dispensing process is an important part of the application of LED UV glue adhesive, and the quality of this process directly affects the final performance of the product. The physical properties of the glue,
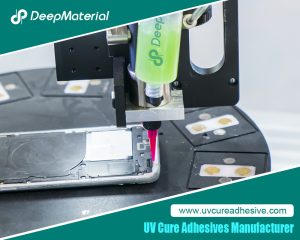
Aging Mechanism and Modification Strategies of LED UV Glue under Long-term Ultraviolet Irradiation
Aging Mechanism and Modification Strategies of LED UV Glue under Long-term Ultraviolet Irradiation LED UV glue, with its advantages of fast curing speed, high bonding strength, and environmental friendliness, has been widely used in fields such as optical device packaging, electronic assembly, and medical devices. However, in scenarios where it is exposed to ultraviolet environments