Analysis of the Influence of Different Construction Environmental Conditions on the Curing of Conformal Coating Materials
Conformal coating plays a crucial role in the protection of electronic devices, and its curing effect directly affects the protection performance. This article deeply explores the influence of different construction environmental conditions such as temperature and humidity on the curing of conformal coating materials, analyzes the physical and chemical changes during the curing process of the coating under different temperature and humidity conditions, aiming to provide a scientific basis for the construction of conformal coating to ensure that it can achieve the best protection effect in practical applications.
Conformal coating is a thin protective coating applied on printed circuit boards (PCBs) and their components, which can protect electronic components from environmental factors such as moisture, dust, chemical substances, and mechanical damage. The curing of conformal coating is a key step in forming an effective protective layer, and construction environmental conditions such as temperature and humidity have a significant impact on its curing process. Understanding these influencing factors is of great significance for optimizing the construction process of conformal coating and improving product quality.
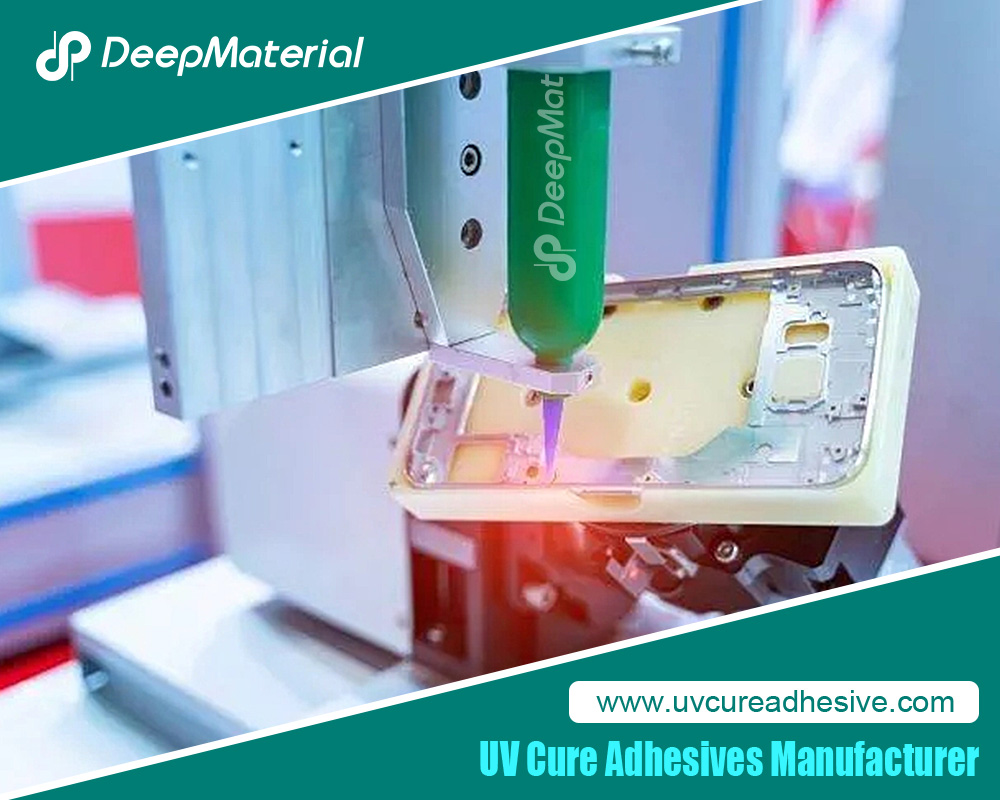
Curing Principle of Conformal Coating
The curing of conformal coating usually involves two processes: physical drying and chemical cross-linking. Physical drying refers to the evaporation of the solvent in the coating, causing the coating to gradually dry. Chemical cross-linking is the formation of chemical bonds between the coating molecules through chemical reactions, thus forming a hard and stable coating. Different types of conformal coating materials (such as acrylic, epoxy resin, silicone, etc.) have slightly different curing mechanisms, but generally, they all involve these two basic processes.
Influence of Temperature on the Curing of Conformal Coating
1. Influence of Temperature on Solvent Evaporation
Temperature is an important factor affecting the solvent evaporation rate. According to the principles of physical chemistry, as the temperature increases, the kinetic energy of the solvent molecules increases, and the molecular movement intensifies, making it easier for the solvent to evaporate from the coating. During the curing process of conformal coating, a higher temperature can accelerate the solvent evaporation rate and shorten the physical drying time. For example, for conformal coatings containing organic solvents, at a lower temperature (such as 10°C), the solvent evaporates slowly, and it may take several hours or even longer to achieve preliminary drying; while at a higher temperature (such as 40°C), the solvent evaporation rate is significantly accelerated, and it may reach the same degree of dryness within dozens of minutes.
However, too high a temperature may also bring some problems. If the temperature is too high, the solvent evaporates too quickly, which may cause a hard shell to form rapidly on the surface of the coating, while the solvent inside cannot evaporate in time, resulting in the formation of bubbles or pinholes inside the coating, affecting the quality and protection performance of the coating. In addition, too high a temperature may also cause some components in the coating to decompose or deteriorate, affecting the curing effect and service life of the coating.
2. Influence of Temperature on Chemical Cross-linking Reaction
The chemical cross-linking reaction is a process that requires a certain amount of energy to occur. An increase in temperature can provide more energy and accelerate the reaction rate. For most chemical cross-linking reactions of conformal coatings, for every 10°C increase in temperature, the reaction rate usually increases by 2 to 4 times. For example, for epoxy resin-based conformal coatings, at a lower temperature (such as 20°C), the cross-linking reaction proceeds slowly, and it may take a long time (such as 24 hours) to achieve complete curing; while at a higher temperature (such as 60°C), the cross-linking reaction rate is significantly accelerated, and it may achieve complete curing within a few hours.
But too high a temperature may also have an adverse effect on the chemical cross-linking reaction. Too high a temperature may cause the cross-linking reaction to be too intense, resulting in excessive cross-linking of the coating molecules and the formation of a coating with greater brittleness, reducing the flexibility and impact resistance of the coating. In addition, too high a temperature may also trigger side reactions, affecting the stability of the cross-linked structure and thus reducing the protection performance of the coating.
Influence of Humidity on the Curing of Conformal Coating
1. Influence of Humidity on Solvent Evaporation
Humidity refers to the content of water vapor in the air. During the curing process of conformal coating, humidity will affect the solvent evaporation rate. When the environmental humidity is high, the partial pressure of water vapor in the air is large, and the resistance for the solvent molecules to evaporate into the air increases, thus slowing down the solvent evaporation rate. For example, in an environment with a relative humidity of 80%, the evaporation rate of the solvent in the conformal coating is significantly lower than that in an environment with a relative humidity of 30%. This is because in a high-humidity environment, the solvent molecules need to overcome the obstruction of more water vapor molecules to evaporate into the air.
The slowdown of the solvent evaporation rate will lead to an extension of the physical drying time of the conformal coating, thereby affecting the entire curing process. If the physical drying time is too long, it may cause the coating surface to absorb too much moisture, resulting in defects such as whitening and blistering of the coating, affecting the appearance and quality of the coating.
2. Influence of Humidity on Chemical Cross-linking Reaction
Humidity also has a certain influence on the chemical cross-linking reaction of conformal coatings. For some conformal coatings that are sensitive to water (such as certain epoxy resin coatings), the moisture in the environment may participate in the chemical reaction and affect the normal progress of the cross-linking reaction. For example, in a high-humidity environment, the epoxy groups in the epoxy resin coating may react with water to form hydroxyl groups, thus consuming the epoxy groups, reducing the effective components of the cross-linking reaction, resulting in a decrease in the degree of cross-linking, and a decrease in the hardness and strength of the coating.
In addition, humidity may also affect the activity of the catalyst in the coating. The curing of some conformal coatings requires the action of a catalyst, and changes in humidity may change the activity of the catalyst. In a high-humidity environment, the catalyst may undergo hydrolysis or other chemical reactions, reducing its catalytic activity and thus slowing down the cross-linking reaction rate.
Analysis of Curing Situations under Different Combinations of Temperature and Humidity
In actual construction, temperature and humidity often exist simultaneously and interact with each other. Different combinations of temperature and humidity will have different effects on the curing of conformal coatings.
For example, in a high-temperature and high-humidity environment, although a higher temperature is conducive to the solvent evaporation and the progress of the chemical cross-linking reaction, high humidity will hinder the solvent evaporation and may have an adverse effect on the chemical cross-linking reaction at the same time. In this case, during the curing process of the conformal coating, problems such as relatively fast surface drying but slow internal drying and the easy occurrence of defects in the coating may occur.
In a low-temperature and low-humidity environment, both the solvent evaporation rate and the chemical cross-linking reaction rate will slow down, resulting in a significant extension of the curing time. If it is in such an environment for a long time, the coating may be contaminated by the outside world before it is completely cured, affecting the quality of the coating.
Measures to Deal with Different Construction Environmental Conditions
In order to ensure that the conformal coating can achieve a good curing effect under different construction environmental conditions, corresponding measures need to be taken.
In terms of temperature, according to the characteristics of the coating and the construction requirements, an appropriate construction temperature range can be selected. For some coatings that are sensitive to temperature, a segmented temperature rise method can be used for curing to avoid problems caused by too high a temperature. At the same time, temperature adjustment equipment such as air conditioners and heaters can be installed in the construction site to control the temperature of the construction environment.
In terms of humidity, the humidity of the construction environment can be reduced through dehumidification equipment, especially for coatings that are sensitive to water. When constructing in a high-humidity environment, the drying time of the coating can be appropriately extended to ensure that the solvent evaporates sufficiently. In addition, conformal coatings with good moisture resistance can also be selected to reduce the impact of humidity on curing.
Conclusion
Temperature and humidity are important construction environmental conditions that affect the curing of conformal coating materials. Temperature mainly affects the curing process by influencing the solvent evaporation rate and the chemical cross-linking reaction rate, while humidity mainly plays a role by affecting the normal progress of the solvent evaporation and the chemical cross-linking reaction. Different combinations of temperature and humidity will have different effects on the curing of conformal coatings. In actual construction, these factors need to be fully considered, and corresponding measures need to be taken to ensure the curing quality of the coating. By reasonably controlling the construction environmental conditions, the protection performance of the conformal coating can be improved, the service life of electronic devices can be extended, and strong support can be provided for the development of the electronics industry. In the future, with the continuous development of conformal coating technology, the research on the relationship between construction environmental conditions and curing will also continue to deepen to meet the increasingly high protection requirements of electronic devices.
For more about choosing a comprehensive guide to UV cure silicone adhesives, you can pay a visit to DeepMaterial at https://www.uvcureadhesive.com/ for more info.