- Home
- >
- UV Cure Adhesive
- >
- UV Curing Potting Compounds
UV Curing Potting Compounds
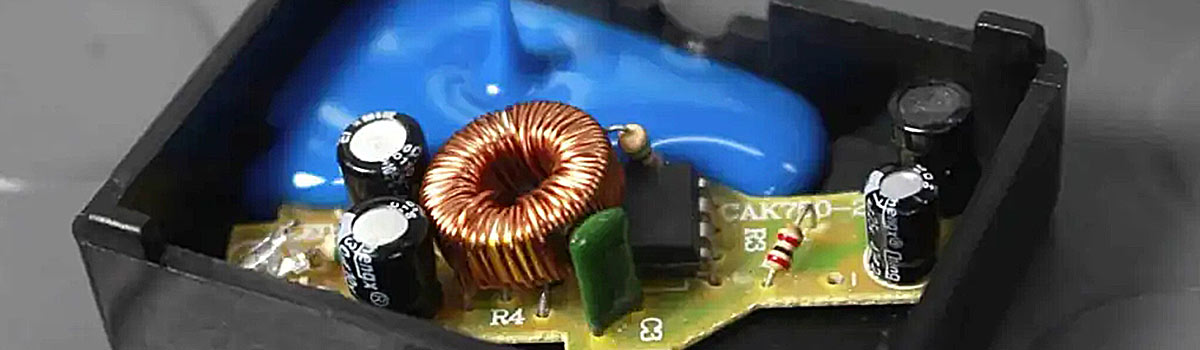
UV curing technology has gained prominence for its efficiency, speed, and versatility in various industrial applications. In this category, we delve into the world of UV-curing potting compounds, exploring their applications, benefits, and diverse industries that benefit from this innovative solution.
Table of Contents
ToggleWhat are UV-curing potting compounds, and how do they work?
UV-curing potting compounds are materials used in electronic and electrical applications to encapsulate and protect components. These compounds are designed to cure or harden when exposed to ultraviolet (UV) light. Potting refers to enclosing electronic parts, such as circuit boards or sensitive devices, in a protective material to shield them from environmental factors like moisture, dust, and chemicals.
Here’s how UV-curing potting compounds work:
- Composition:UV-curing potting compounds typically consist of a liquid resin and a photoinitiator. The resin is a polymer that solidifies or cures when exposed to UV light, while the photoinitiator initiates the curing process when exposed to UV radiation.
- Application:The liquid potting compound is applied to the electronic components. It can be poured, dispensed, or injected to encapsulate and cover the parts that need protection.
- UV Exposure:Once the potting compound is in place, it is exposed to UV light. The UV light activates the photoinitiator in the resin, initiating a polymerization reaction. This reaction causes the resin to undergo a rapid chemical change, transforming from a liquid to a solid or gel-like.
- Curing:The process occurs almost instantly or within a short period, providing a quick and efficient way to encapsulate the components. The speed of the curing process is a significant advantage, especially in manufacturing environments where fast production cycles are essential.
- Properties:The cured potting compound creates a protective barrier around the electronic components, offering resistance against moisture, chemicals, and physical damage. It also provides thermal insulation, improving the overall reliability and longevity of the electronic device.
UV-curing potting compounds are commonly used in industries where rapid processing, high precision, and reliable protection of electronic components are crucial. Some advantages of UV-curing potting compounds include their ability to cure on demand, reduced processing time, and the capability to achieve precise encapsulation around complex shapes and structures. Additionally, these compounds are often chosen for their excellent electrical insulation properties and resistance to environmental factors.
What are the applications of UV Curing Potting Compounds across industries, including electronics and beyond?
UV-curing potting compounds are versatile materials that find applications in various industries, including electronics and beyond. These compounds are used for encapsulation and potting of electronic components and assemblies. Here are some of the applications across different sectors:
Electronics Industry:
- Encapsulation of Electronic Components:UV curing potting compounds are commonly used to encapsulate sensitive electronic components, protecting them from environmental factors such as moisture, chemicals, and mechanical stress.
- Printed Circuit Board (PCB) Protection:These compounds provide a protective layer over PCBs, safeguarding them against environmental damage and enhancing their reliability.
- LED Encapsulation:UV curing potting compounds encapsulate LED modules, providing optical clarity, thermal conductivity, and protection against external elements.
Medical Devices:
- Sensor Encapsulation:UV curing potting compounds are used in the medical industry to encapsulate sensors and other electronic components in devices such as medical monitors and diagnostic equipment.
Automotive Industry:
- Electronic Control Units (ECUs):UV curing potting compounds protect ECUs and other electronic systems in vehicles, ensuring reliability and durability under harsh automotive conditions.
Aerospace and Defense:
- Avionics Encapsulation:Electronic components in aerospace applications, such as avionics systems, benefit from the protection offered by UV-curing potting compounds against vibration, shock, and temperature extremes.
Renewable Energy:
- Solar Panel Encapsulation:UV curing potting compounds are used to encapsulate solar panels, protecting against UV radiation and environmental factors while maintaining optical clarity.
Consumer Electronics:
- Wearable Devices:UV-curing potting compounds encapsulate electronic components in wearable devices, providing flexibility, protection, and durability.
Telecommunications:
- Fiber Optic Component Protection:UV curing potting compounds protect fiber optic components, ensuring signal integrity and reliability in telecommunications equipment.
General Industrial Applications:
- Sealing and Bonding:UV curing potting compounds can be used for sealing and bonding in various industrial applications, providing quick and efficient curing for multiple materials.
Medical Devices:
- Dental Products:UV-curing potting compounds, such as adhesives and restorative materials, manufacture dental products.
Custom Applications:
- 3D Printing:UV curing potting compounds are sometimes used in 3D printing processes, offering rapid curing for intricate designs and structures.
UV curing potting compounds are valued for their rapid curing time, low-temperature curing, and ability to provide a protective and durable encapsulation for sensitive components across diverse industries.
What advantages do UV Curing Potting Compounds offer over traditional potting methods?
UV-curing potting compounds offer several advantages over traditional potting methods, typically using heat-cured or room-temperature-cured materials. Here are some of the critical advantages of UV-curing potting compounds:
Rapid Cure Time:
- UV curing is a fast process compared to heat or room-temperature curing. UV potting compounds can cure within seconds when exposed to ultraviolet light. This allows for high-speed manufacturing processes and increased production efficiency.
Energy Efficiency:
- UV curing does not require heat application, reducing energy consumption in the manufacturing process. Traditional potting methods often use elevated temperatures to cure, leading to higher energy costs.
Reduced Processing Time:
- The fast cure time of UV-curing potting compounds reduces overall processing time. This can lead to higher throughput and shorter production cycles, increasing productivity.
Selective Curing:
- UV curing is a particular process, meaning that curing only occurs when the material is exposed to UV light. This allows for precise control over the curing process, reducing the risk of over-curing or incomplete curing.
Low Volatile Organic Compounds (VOCs):
- UV curing systems often have lower VOC emissions compared to some traditional potting compounds that may release volatile organic compounds during the curing process. This can contribute to a healthier working environment and compliance with environmental regulations.
Improved Quality and Consistency:
- UV curing provides a controlled and uniform cure, producing consistent product quality. The ability to selectively cure specific areas ensures that the material cures evenly and thoroughly, reducing the likelihood of defects.
Reduced Footprint and Equipment Costs:
- UV curing systems typically have a smaller footprint than ovens or other heat-curing equipment. This can be advantageous in facilities with limited space. Additionally, the absence of bulky curing equipment can result in cost savings.
Enhanced Thermal Stability:
- UV-cured potting compounds often exhibit excellent thermal stability, making them suitable for applications where temperature resistance is crucial. The cured material can withstand high temperatures without degrading its properties.
Minimal Shrinkage:
- UV curing can result in minimal shrinkage of the potting material during the curing process. This property is essential for applications where precise dimensional stability is required.
Improved Environmental Resistance:
- UV-cured compounds often resist environmental factors such as moisture, chemicals, and UV radiation. This makes them suitable for applications in challenging or harsh conditions.
While UV curing potting compounds offer these advantages, it’s important to note that the choice of potting method depends on the application’s specific requirements, and factors such as material compatibility, cost considerations, and production volume should be taken into account.
How do you choose the proper UV Curing Potting Compound for a specific application?
Choosing the proper UV-curing potting compound for a specific application involves considering several factors to ensure compatibility with the requirements of your project. Here are some key considerations:
Substrate Compatibility:
- Ensure that the potting compound is compatible with the materials used in your application. It should adhere well to the substrate without causing any damage or degradation.
Curing Time:
- UV curing compounds typically cure quickly when exposed to ultraviolet light. Consider the required curing time for your application and choose a compound that meets those time constraints.
Curing Depth:
- Different UV curing compounds penetrate materials to varying depths. Consider the thickness of the material you are potting and choose a compound that can cure throughout the entire depth.
Chemical Resistance:
- Evaluate the chemical environment the potting compound will be exposed to. Choose a compound resistant to chemicals or solvents in the application environment to ensure long-term stability.
Temperature Resistance:
- Consider the temperature range your application will experience. Ensure the potting compound can withstand the expected temperature extremes without losing its properties.
Electrical Properties:
- If the application involves electronic components, ensure the potting compound has suitable electrical insulating properties. It should also provide good thermal conductivity if heat dissipation is a concern.
Mechanical Properties:
- Evaluate the mechanical stresses the potting compound will be subjected to, such as vibration or impact. Choose a compound with appropriate mechanical properties, such as flexibility or rigidity, to withstand these stresses.
Optical Clarity:
- If optical clarity is essential for your application, choose a UV-curing potting compound that provides the desired level of transparency.
Shrinkage:
- Consider the shrinkage properties of the potting compound after fixing. Excessive shrinkage can lead to stress on components and affect the overall performance.
Regulatory Compliance:
- Ensure that the chosen potting compound complies with relevant industry standards or regulations, especially if your application is in a highly regulated industry.
Supplier Support:
- Choose a reliable supplier who can provide technical support and assistance. They can help you select the most appropriate product for your specific application and troubleshoot any issues that may arise.
It’s crucial to perform thorough testing and validation to ensure that the selected UV curing potting compound meets the specific requirements of your application before full-scale implementation.
What are the critical components of UV Curing Potting Compounds?
UV curing potting compounds are materials used for encapsulating and protecting electronic components. These compounds typically comprise several critical components that provide the desired properties. The specific formulation may vary depending on the manufacturer and the intended application, but some standard components include:
Resin Base:
- Epoxy Resin:Commonly used due to its excellent adhesion, high strength, and chemical resistance.
- Acrylic Resin:Offers good flexibility, electrical insulation, and resistance to UV light.
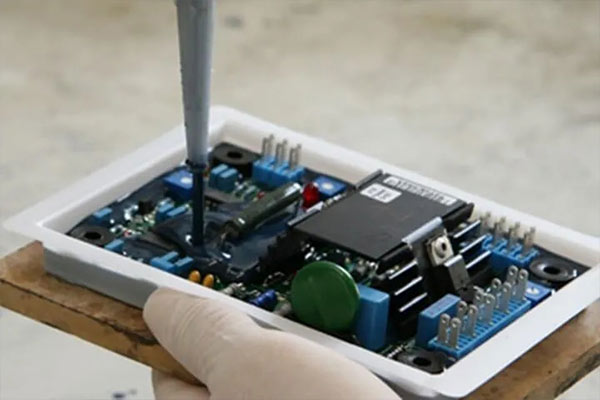
Photoinitiators:
- Photoinitiating System:Initiates the polymerization process when exposed to UV light, leading to the hardening of the resin. Typical photoinitiators include benzoin methyl ether, benzoin ethyl ether, benzoin isobutyl ether, camphorquinone, and others.
Additives:
- Fillers:Provide additional strength, improve thermal conductivity, and reduce shrinkage. Joint fillers include silica, glass beads, or alumina.
- Plasticizers:Enhance flexibility and reduce the brittleness of the cured material.
- Thickeners:Control viscosity for proper application and prevent the settling of fillers.
Stabilizers:
- Antioxidants:Protect the cured material from oxidation and degradation over time.
- UV Stabilizers:Prevent yellowing and degradation caused by prolonged exposure to UV light.
Modifiers:
- Adhesion Promoters:Improve the bond between the potting compound and the substrate.
- Colorants/Pigments:Provide desired color for identification or aesthetic purposes.
Inhibitors:
- Inhibitors or Stabilizers:Prevent premature curing of the potting compound before exposure to UV light.
Solvents:
- Diluents or Solvents:Adjust the viscosity of the formulation for specific application requirements.
Thermal Conductivity Enhancers:
- Thermal Fillers:Improve the cured material’s thermal conductivity, helping dissipate heat generated by electronic components.
It’s important to note that the selection of components depends on the application’s specific requirements, such as thermal conductivity, flexibility, chemical resistance, and adhesion properties. Manufacturers may adjust formulations to meet the needs of different industries and applications.
Can you provide a step-by-step guide to understanding the curing process of UV Curing Potting Compounds?
Certainly! UV-curing potting compounds harden or cure when exposed to ultraviolet (UV) light. The curing process involves several steps. Below is a step-by-step guide to understanding the UV curing process of potting compounds:
Select the Right Potting Compound:
- Choose a UV-curable potting compound that suits your application requirements. Consider thermal conductivity, flexibility, hardness, and chemical resistance.
Prepare the Substrate:
- Ensure that the substrate or surface to be potted is clean, dry, and free from contaminants. Proper surface preparation is crucial for the adhesion and performance of the potting material.
Dispensing the Potting Compound:
- Dispense the potting compound onto the substrate using appropriate dispensing equipment. Ensure that the compound is evenly distributed and covers the components to be encapsulated.
Assemble Components:
- Place the components or parts to be potted into the dispensed potting compound. Ensure the components are correctly positioned and no air gaps or voids exist.
Exposure to UV Light:
- UV curing relies on exposure to ultraviolet light to initiate the curing reaction. Use a UV light source with the appropriate wavelength for your specific potting compound. Standard UV wavelengths include 365 nm and 385 nm.
Controlled Curing Time:
- Exposure time to UV light is critical. Follow the manufacturer’s guidelines for the recommended curing time. Overexposure or underexposure may affect the curing performance and properties of the potting compound.
Monitor Cure Progress:
- Monitor the curing progress by checking the physical properties of the potting compound. Visual cues such as color change or viscosity can indicate the curing state. Some compounds may include indicators for easy visual confirmation.
Post-Curing (Optional):
- Some UV-curable potting compounds may benefit from a post-curing step to ensure complete curing and optimize performance. This may involve additional exposure to UV light or heat.
Testing and Quality Control:
- Once cured, perform testing to ensure that the potting compound meets the desired specifications and provides the required protection and performance for the application.
Final Inspection and Packaging:
- Inspect the potted components for defects or issues after successful curing and testing. If everything is in order, proceed with the final packaging.
It’s essential to follow the manufacturer’s guidelines and recommendations for the specific UV-curable potting compound you are using, as formulations and curing requirements can vary between products.
What does a comparative analysis between UV Curing and conventional curing compounds look like?
A comparative analysis between UV curing and conventional curing compounds involves evaluating various aspects of these two curing methods. Both UV curing and conventional curing methods are used in different industries for curing coatings, adhesives, inks, and other materials. Here’s a breakdown of the key factors to consider in a comparative analysis:
- Curing Mechanism:
- UV Curing:
- Relies on ultraviolet (UV) light to initiate a photochemical reaction that leads to the curing of the material.
- Faster curing times due to the rapid photochemical reactions.
- Conventional Curing:
- Typically involves heat, moisture, or chemical reactions for the curing process.
- Curing times can be longer compared to UV curing.
- UV Curing:
- Curing Speed:
- UV Curing:
- Rapid cure times, often in seconds or minutes.
- Instant curing upon exposure to UV light.
- Conventional Curing:
- Generally slower cure times, ranging from minutes to hours.
- Cure time may be influenced by factors like temperature and humidity.
- UV Curing:
- Energy Consumption:
- UV Curing:
- Requires UV light sources, which can be energy-efficient.
- Energy consumption is often lower compared to the energy-intensive heat curing processes.
- Conventional Curing:
- May require higher energy inputs, especially in processes involving heat curing.
- UV Curing:
- Temperature Sensitivity:
- UV Curing:
- Typically does not generate significant heat during the curing process.
- Suitable for heat-sensitive substrates.
- Conventional Curing:
- May involve elevated temperatures, which can limit the use on heat-sensitive materials.
- UV Curing:
- Chemical Emissions:
- UV Curing:
- Generally produces fewer volatile organic compounds (VOCs) compared to some conventional curing methods.
- Conventional Curing:
- May involve the release of VOCs, especially in solvent-based curing processes.
- UV Curing:
- Adhesion and Material Compatibility:
- UV Curing:
- Provides excellent adhesion to various substrates.
- Limited to materials that are transparent or translucent to UV light.
- Conventional Curing:
- Adaptable to a wide range of materials, including opaque substrates.
- Adhesion performance may vary based on the specific curing method.
- UV Curing:
- Equipment and Setup Costs:
- UV Curing:
- Initial equipment costs for UV lamps and related infrastructure.
- Operating costs may be lower due to energy efficiency and faster curing times.
- Conventional Curing:
- Equipment costs may vary depending on the specific curing method (e.g., ovens, dryers).
- Operating costs can be influenced by energy consumption and maintenance.
- UV Curing:
- Flexibility and Control:
- UV Curing:
- Offers precise control over the curing process, allowing for better process optimization.
- Well-suited for high-precision applications.
- Conventional Curing:
- May offer flexibility in terms of curing conditions but might have less precise control compared to UV curing.
- UV Curing:
the choice between UV curing and conventional curing depends on the specific requirements of the application, material compatibility, and desired production outcomes. Factors such as curing speed, energy consumption, and material adhesion play a crucial role in determining the most suitable curing method for a given process.
What does a comparative analysis between UV Curing and conventional curing compounds look like?
A comparative analysis between UV curing and conventional curing compounds involves evaluating various aspects of these two curing methods. UV and traditional curing methods are used in different industries for curing coatings, adhesives, inks, and other materials. Here’s a breakdown of the critical factors to consider in a comparative analysis:
Curing Mechanism:
- UV Curing:
- It relies on ultraviolet (UV) light to initiate a photochemical reaction that leads to the curing of the material.
- Faster curing times due to the rapid photochemical reactions.
- Conventional Curing:
- Typically involves heat, moisture, or chemical reactions for the curing process.
- Curing times can be longer compared to UV curing.
Curing Speed:
- UV Curing:
- Rapid cure times, often in seconds or minutes.
- Instant curing upon exposure to UV light.
- Conventional Curing:
- Generally slower cure times, ranging from minutes to hours.
- Factors like temperature and humidity may influence cure time.
Energy Consumption:
- UV Curing:
- Requires UV light sources, which can be energy-efficient.
- Energy consumption is often lower compared to the energy-intensive heat-curing processes.
- Conventional Curing:
- It may require higher energy inputs, especially in processes involving heat curing.
Temperature Sensitivity:
- UV Curing:
- Typically, it generates little heat during the curing process.
- Suitable for heat-sensitive substrates.
- Conventional Curing:
- It may involve elevated temperatures, which can limit the use of heat-sensitive materials.
Chemical Emissions:
- UV Curing:
- Generally produces fewer volatile organic compounds (VOCs) compared to some conventional curing methods.
- Conventional Curing:
- It may involve the release of VOCs, especially in solvent-based curing processes.
Adhesion and Material Compatibility:
- UV Curing:
- Provides excellent adhesion to various substrates.
- Limited to materials that are transparent or translucent to UV light.
- Conventional Curing:
- Adaptable to a wide range of materials, including opaque substrates.
- Adhesion performance may vary based on the specific curing method.
Equipment and Setup Costs:
- UV Curing:
- Initial equipment costs for UV lamps and related infrastructure.
- Operating costs may be lower due to energy efficiency and faster curing times.
- Conventional Curing:
- Equipment costs may vary depending on the curing method (e.g., ovens, dryers).
- Operating costs can be influenced by energy consumption and maintenance.
Flexibility and Control:
- UV Curing:
- Offers precise control over the curing process, allowing for better process optimization.
- Well-suited for high-precision applications.
- Conventional Curing:
- It may provide flexibility regarding curing conditions but might have less precise control than UV curing.
The choice between UV curing and conventional curing depends on the application’s specific requirements, material compatibility, and desired production outcomes. Factors such as curing speed, energy consumption, and material adhesion are crucial in determining the most suitable curing method for a given process.
What factors should be considered to ensure optimal performance in applying UV Curing Potting Compounds?
UV-curing potting compounds are used in various applications to encapsulate and protect electronic components. To ensure optimal performance when applying UV-curing potting compounds, several factors should be considered:
Substrate Compatibility:
- Ensure that the potting compound is compatible with the materials of the components being potted. This includes the substrate material, solder joints, and other assembly materials.
Curing Spectrum:
- UV curing compounds rely on specific wavelengths of light for curing. Ensure that the UV light source matches the curing spectrum recommended by the potting compound manufacturer.
UV Light Intensity and Exposure Time:
- Follow the recommended UV light intensity and exposure time guidelines the potting compound manufacturer provided. Inadequate exposure may result in incomplete curing, while excessive exposure may lead to overcuring and potential damage.
Temperature Conditions:
- Consider the ambient temperature during the potting process. Some compounds may have specific temperature requirements for optimal curing. Ensure that the temperature is within the recommended range for the potting material.
Mixing and Dispensing:
- Follow the proper mixing ratios and procedures specified by the manufacturer. Uniform mixing is crucial to achieve consistent curing properties. Use appropriate dispensing equipment to ensure accurate and even application.
Moisture and Contaminant Control:
- UV curing compounds can be sensitive to moisture and contaminants. Ensure the working environment is dry and clean to prevent interference with the curing process.
Potting Depth and Thickness:
- Consider the recommended potting depth and thickness for the specific application. Overfilling or underfilling can affect the performance and reliability of the potted components.
Shrinkage and Expansion:
- Be aware of the shrinkage or expansion characteristics of the potting compound. This is important, especially if the potted components are sensitive to dimensional changes.
Post-Cure Handling:
- Follow any recommended post-cure procedures provided by the manufacturer. This may include additional curing time or steps to ensure the complete and stable curing of the potting compound.
Testing and Quality Control:
- Implement testing procedures to verify the performance and reliability of potted components. This may include mechanical, thermal, and electrical testing to ensure the potting material meets the desired specifications.
Regulatory Compliance:
- Ensure the chosen potting compound complies with relevant industry standards and regulations for the intended application.
By carefully considering these factors, you can help ensure UV-curing potting compounds’ optimal performance and reliability in your specific application. Always refer to the manufacturer’s guidelines and recommendations for the best results.
Are there any case studies highlighting success stories using UV-curing potting compounds?
However, it’s worth noting that advancements in UV-curing technology, including UV-curing potting compounds, have been gaining attention for their efficiency and environmental benefits.
UV-curing potting compounds are often used in electronics and electrical applications to protect components from environmental factors such as moisture, dust, and mechanical stress. These compounds offer rapid curing times, allowing for faster production cycles and increased productivity. The benefits include improved manufacturing processes, reduced energy consumption, and lower environmental impact than traditional potting methods.
To find the most recent and specific case studies, you may want to:
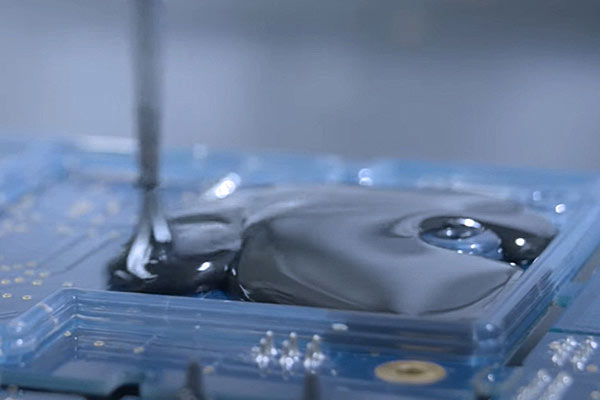
- Check Industry Journals and Publications:Look for articles and case studies in industry-specific journals and publications related to electronics manufacturing, materials science, and UV-curing technologies.
- Contact UV-Curing Manufacturers and Suppliers:Contact companies specializing in UV-curing technologies or providing UV-curing potting compounds. They may have case studies or success stories that showcase the benefits of their products.
- Attend Industry Conferences and Trade Shows:Events related to electronics manufacturing, materials, or UV-curing technologies often feature presentations and exhibits where companies share their success stories and advancements.
- Consult Research Institutions:Academic institutions and research organizations may conduct studies on the applications and benefits of UV-curing technologies. Checking their publications or contacting relevant researchers could yield valuable insights.
- Check Online Industry Forums:Industry forums and online communities where professionals discuss materials and manufacturing technologies might contain shared experiences and case studies.
Remember to verify the credibility of the sources and ensure that the information aligns with your specific needs and industry requirements.
What is the environmental impact of UV Curing Technology, particularly the “green” aspects?
UV curing technology uses high-intensity ultraviolet (UV) light to instantly cure or dry inks, coatings, adhesives, and other materials. This technology has gained popularity for its efficiency and environmental benefits compared to traditional curing methods. However, it’s essential to consider both the positive and potentially negative environmental impacts of UV curing technology.
Positive Environmental Aspects:
- Energy Efficiency:UV curing is generally more energy-efficient than traditional methods because it uses UV lamps that consume less energy than ovens or other heat-based curing processes.
- Reduced Emissions:UV curing often results in lower emissions of volatile organic compounds (VOCs) than solvent-based systems. VOCs contribute to air pollution and can have adverse effects on human health.
- Reduced Waste:The instantaneous curing process reduces the likelihood of defects or errors, minimizing the waste generated in the production process.
- Lower Resource Consumption:UV curing eliminates the need for drying time, reducing the overall production time and resource consumption.
- Improved Worker Safety:Unlike some solvent-based systems, UV curing does not involve using harmful solvents, which can improve workplace safety.
Negative Environmental Aspects:
- Hazardous Materials:Some UV-curable materials may contain dangerous substances. It’s essential to carefully manage the use and disposal of these materials to prevent environmental harm.
- Energy Source:The ecological impact of UV curing can be influenced by the energy source used to power the UV lamps. If the energy source is derived from non-renewable or high-carbon-emission sources, it can contribute to environmental issues.
- Waste Disposal:While UV curing reduces overall waste, the disposal of UV-cured materials can still be a concern. Proper waste management practices are crucial to minimize the environmental impact.
- Initial Capital Investment:Installing UV curing equipment may require a significant initial investment, and manufacturing such equipment can have ecological implications. However, this impact is typically offset by the long-term environmental benefits of the technology.
UV curing technology has several environmentally friendly aspects, such as energy efficiency, reduced emissions, and lower waste generation. However, it’s essential to carefully manage the materials used, energy sources, and waste disposal to maximize the positive environmental impact. As technology advances and industry practices evolve, efforts are being made to address and minimize any potential adverse ecological aspects of UV curing technology.
What are common challenges encountered in UV Curing Potting Applications, and what solutions exist?
UV curing potting applications involve using ultraviolet (UV) light to cure adhesives or potting materials, providing a fast and efficient way to encapsulate electronic components. However, several challenges can arise in these applications, and various solutions exist to address them. Here are some common challenges and potential solutions:
Incomplete Curing:
- Challenge:Inadequate exposure to UV light can result in incomplete curing, leading to issues such as reduced adhesion and mechanical strength.
- Solution:Ensure proper UV light intensity and exposure time. Regularly check and maintain UV lamps to ensure they emit the required intensity. Consider using UV-curable materials optimized for the specific curing conditions.
Shadowing Effects:
- Challenge:Components with complex geometries or those casting shadows can impede UV light penetration, causing incomplete curing in shadowed areas.
- Solution:Use materials with good light penetration or select curing systems with multiple light sources or varying angles to minimize shadowing effects. Optimizing the design to reduce shadowing can also be beneficial.
Material Compatibility:
- Challenge:Some materials may not be compatible with UV curing, limiting the choice of potting compounds.
- Solution:Select UV-curable potting materials consistent with the specific application and substrate. Consult with material suppliers to ensure the intended components and environmental conditions are constant.
Temperature Sensitivity:
- Challenge:Elevated temperatures during the curing process can lead to thermal stress on sensitive electronic components.
- Solution:Choose UV-curable materials with low exothermic reactions or select formulations designed for low-temperature curing. Implement controlled curing environments, such as using chill plates or cooling systems.
Moisture Sensitivity:
- Challenge:Moisture can interfere with the curing process and compromise the performance of UV-curable materials.
- Solution:Ensure a dry environment during the curing process. Consider using materials with moisture-resistant formulations or implement a moisture control system in the potting area.
Adhesion Issues:
- Challenge:Poor adhesion to substrates can result in delamination or reduced reliability of the encapsulated components.
- Solution:Clean and prepare substrate surfaces properly before potting. Use adhesion promoters or primers if necessary. Select UV-curable materials with good adhesion properties to the specific substrates used in the application.
UV Light Intensity Variability:
- Challenge:UV light intensity may vary across the area, leading to inconsistent curing results.
- Solution:Regularly monitor and calibrate UV lamps to ensure uniform light intensity. Consider using systems with advanced controls to maintain consistent UV exposure.
Regulatory Compliance:
- Challenge:Adherence to regulatory standards and environmental requirements may be necessary, and certain UV-curable materials may contain hazardous components.
- Solution:Choose UV-curable materials that comply with relevant regulations and norms. Be aware of safety and environmental considerations, and implement proper handling and disposal procedures.
It’s essential to consult with material suppliers, equipment manufacturers, and industry experts to address specific challenges based on the unique requirements of each UV curing potting application. Regular testing and quality control measures should also be implemented to ensure the reliability of the encapsulated components.
How does UV Curing play a role in LED encapsulation?
UV curing is crucial in LED encapsulation, which refers to protecting and sealing LED components to enhance their durability and performance. A transparent material encapsulates the LED chip and other sensitive components in LED encapsulation. UV (ultraviolet) curing is a specific method employed during this process.
Here’s how UV curing is involved in LED encapsulation:
- Encapsulation Material:The material used for encapsulating LEDs is often a liquid resin or adhesive. This material needs to be cured or solidified to form a protective layer around the LED components.
- UV-Curable Resins:UV-curable resins are commonly used in LED encapsulation. These resins remain in a liquid state until exposed to ultraviolet light. Once exposed, the UV light triggers a polymerization chemical reaction, causing the resin to harden and form a solid, protective layer.
- Instant Curing:One significant advantage of UV curing is its rapid time. UV curing is nearly instantaneous, unlike traditional curing methods that may require heat or extended curing times. This speed is essential for high-volume manufacturing processes, enabling faster production cycles.
- Energy Efficiency:UV curing is an energy-efficient process. The energy from the UV light source is explicitly used to initiate the curing reaction, reducing the overall energy consumption compared to other curing methods that may involve additional heat or prolonged exposure to curing agents.
- Controlled Process:UV curing offers precise control over the curing process. The curing reaction starts and stops almost instantly when exposed to UV light. This control ensures uniform encapsulation and helps prevent overturning or undercutting, which can be critical for maintaining the performance and reliability of the LED.
- Reduced Thermal Stress:UV curing is a low-temperature process compared to other methods. This can be advantageous for LED encapsulation, as it helps minimize thermal stress on the sensitive electronic components of the LED, preventing potential damage due to high temperatures.
UV curing in LED encapsulation provides a fast, energy-efficient, and controlled process for solidifying the encapsulation material around LED components. This method produces durable and high-performance LED devices in an efficient manufacturing environment.
What innovations are on the horizon for UV Curing Potting Compounds, and what can we expect next?
Keep in mind that technological developments continue to evolve, and it’s recommended to check the latest sources for the most up-to-date information. Here are some potential innovations and trends for UV-curing potting compounds:
- Improved Formulations:Researchers and manufacturers will likely continue developing UV-curing potting compounds with enhanced formulations. This could include improvements in mechanical strength, thermal conductivity, and resistance to environmental factors such as moisture and chemicals. Advanced formulations may address specific challenges associated with LED applications, such as the need for thermal management to dissipate heat effectively.
- Customization for Specific LED Types:As the LED industry diversifies with various types of LEDs, including high-power LEDs, UV LEDs, and miniaturized LEDs, there may be a trend toward developing UV curing potting compounds specifically tailored to the requirements of these different LED types. Customized formulations could optimize the performance and reliability of each LED category.
- Multi-functional Compounds:Future UV curing potting compounds may serve multiple functions beyond encapsulation, such as providing optical properties for light diffusion or color enhancement. This could lead to more integrated solutions addressing protective and performance-related aspects in a single material.
- Green and Sustainable Solutions:With an increasing focus on sustainability, there may be efforts to develop UV-curing potting compounds that are more environmentally friendly. This could involve using bio-based materials, reducing hazardous substances, and exploring recyclable or biodegradable options.
- Innovative Materials:Advancements in materials science might lead to the development of “smart” UV-curing potting compounds. These could include materials with self-healing properties or those that can adapt to changing environmental conditions. Intelligent materials could contribute to the longevity and reliability of LED devices.
- Application-Specific Compounds:Manufacturers may develop UV-curing potting compounds designed for specific applications within the broader LED industry. For example, compounds optimized for automotive lighting may have different requirements than those used in consumer electronics or industrial applications.
To stay current on the latest innovations in UV curing potting compounds for LED applications, it’s recommended to monitor industry publications, attend conferences, and keep an eye on updates from materials science and LED technology research. Consulting with industry experts and suppliers can provide insights into emerging trends and technologies.
What safety guidelines should be followed when handling UV Curing Materials?
Handling UV curing materials requires adherence to safety guidelines to ensure individuals’ well-being and prevent potential hazards. Here are some general safety guidelines:
Personal Protective Equipment (PPE):
- Wear appropriate PPE, including safety glasses with UV protection, gloves, and a lab coat or protective clothing. Ensure that the PPE is compatible with the specific UV-curing materials being used.
Ventilation:
- Work in a well-ventilated area to minimize exposure to fumes and vapors. Use fume hoods or local exhaust ventilation systems when handling volatile UV curing materials.
UV Exposure:
- Minimize direct skin and eye exposure to UV radiation. Use UV-blocking safety glasses and ensure that exposed skin is covered. Use a UV shield or barrier if there’s a potential for prolonged exposure.
Training:
- Ensure that personnel handling UV curing materials are adequately trained in safely using and handling these materials. Provide training on emergency procedures and the use of safety equipment.
Storage:
- Store UV curing materials in a cool, dry place, away from direct sunlight, and follow the manufacturer’s recommendations for storage conditions. Store incompatible materials separately.
Handling and Mixing:
- Follow proper procedures for handling and mixing UV curing materials, and strictly adhere to the recommended ratios and conditions specified by the manufacturer.
Emergency Equipment:
- Emergency equipment, including eyewash stations, safety showers, and fire extinguishers, are readily available. Know the location of emergency exits and evacuation routes.
Spill Response:
- Develop and implement a spill response plan. Have absorbent materials, such as spill kits, available to clean up small spills quickly and effectively. Larger spills may require professional assistance.
Labeling:
- Ensure that all containers are appropriately labeled with the name of the material, hazard warnings, and handling instructions. Follow material safety data sheet (MSDS) guidelines.
Equipment Maintenance:
- Regularly inspect and maintain UV curing equipment to ensure it is in good working condition. Follow manufacturer recommendations for maintenance and calibration.
First Aid:
- Train personnel in basic first aid procedures and ensure supplies are readily available. In case of exposure, promptly rinse affected areas with water and seek medical attention if necessary.
Always refer to the specific guidelines and recommendations provided by the manufacturer of the UV curing materials, as they may vary depending on the type of material being used. Additionally, compliance with local, state, and national regulations is essential.
How do you conduct a cost-benefit analysis to evaluate the economic impact of UV Curing Potting Compounds?
A cost-benefit analysis (CBA) is a systematic process used to assess the economic implications of a decision or project. In the context of UV-curing potting compounds, conducting a CBA involves evaluating the costs of implementing these compounds against the anticipated benefits. Here’s a step-by-step guide:
Define the Scope and Objectives:
- Clearly outline the goals and objectives of using UV-curing potting compounds. Identify the specific outcomes or benefits you hope to achieve, such as improved production efficiency, reduced curing time, or enhanced product performance.
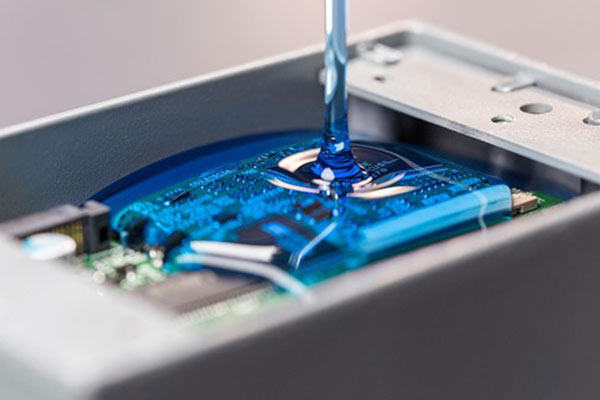
Identify Costs:
- Break down the costs associated with adopting UV-curing potting compounds. This may include:
- Material Costs:The cost of UV curing potting compounds.
- Equipment Costs:UV curing equipment, curing chambers, and related machinery.
- Labor Costs:Training and labor are required to handle UV curing materials.
- Energy Costs:Electricity consumption for UV curing processes.
- Implementation Costs:Initial setup, installation, and any additional infrastructure required.
Quantify Benefits:
- Identify and quantify the benefits expected from using UV-curing potting compounds. This may include:
- Time Savings:Calculate the reduction in healing time and its impact on production cycles.
- Improved Product Quality:Assess any improvements in product performance, durability, or other quality metrics.
- Energy Efficiency:Consider potential energy savings associated with quicker curing times.
- Waste Reduction:Evaluate any reduction in waste materials.
Monetize Benefits:
- Assign monetary values to the quantified benefits. This step involves estimating the dollar value associated with each benefit. For example, time savings can be translated into labor cost reductions or increased production capacity.
Calculate Net Present Value (NPV):
- Discount costs and benefits over time to account for the time value of money. Calculate the Net Present Value using a discount rate. A positive NPV indicates that the benefits outweigh the costs.
Calculate Return on Investment (ROI):
- Determine the ROI by dividing the net benefits by the total costs and expressing it as a percentage. This provides a measure of the profitability of the investment.
Sensitivity Analysis:
- Assess the impact of changes in key variables (e.g., material costs, energy prices) on the CBA results. This helps identify the sensitivity of the analysis to different factors.
Compare Alternatives:
- If there are multiple options, compare the cost-benefit analysis of UV-curing potting compounds with alternative methods or materials. Choose the choice that provides the highest net benefit.
Risk Assessment:
- Consider potential risks and uncertainties associated with implementing UV-curing potting compounds. Evaluate how these uncertainties may impact the overall economic analysis.
Document and Communicate Findings:
- Prepare a comprehensive report summarizing the cost-benefit analysis’s methodology, assumptions, and results. Communicate the findings to relevant stakeholders.
By following these steps, you can systematically assess the economic impact of UV-curing potting compounds and make informed decisions based on a thorough analysis of costs and benefits. Remember that the study’s accuracy relies on the data quality and assumptions used in the process.
What are the global trends and market dynamics in UV Curing Compounds?
Market conditions can change rapidly, and it’s essential to refer to the latest reports, industry publications, and market analyses for the most current information.
However, some general trends and dynamics in the UV curing compounds market included:
- Growing Demand Across Industries:UV curing compounds have applications in various industries, including printing, adhesives, electronics, automotive, and coatings. The demand was driven by their advantages, such as faster curing times, reduced energy consumption, and environmental friendliness.
- Technology Advancements:Ongoing advancements in UV curing technology, such as developing new formulations and equipment, have been influencing the market. Key drivers have been innovations aimed at improving efficiency, performance, and compatibility with different substrates.
- Regulatory Environment:The shift towards more environmentally friendly and sustainable practices has increased interest in UV curing compounds due to their low VOC (volatile organic compounds) emissions and reduced energy consumption compared to traditional curing methods.
- Application Expansion:UV curing technology has expanded into new applications, such as 3D printing, medical devices, and food packaging. This diversification has contributed to the growth of the UV curing compounds market.
- Asia-Pacific Dominance:The Asia-Pacific region, particularly China, has been significant in the UV curing compounds market. The region’s robust manufacturing activities and increasing demand across various industries have contributed to market growth.
To get the most recent and detailed insights into the current global trends and market dynamics in UV curing compounds, consider consulting industry reports, market research studies, and updates from relevant trade associations. Additionally, speaking with industry experts and professionals can provide valuable firsthand information.
Can you provide a comprehensive guide to the compatibility of UV Curing Potting Compounds with different substrates?
Remember that specific formulations of potting compounds may vary, so it’s essential to consult the manufacturer’s recommendations and conduct compatibility testing for your particular application.
Plastics:
- Acrylics (PMMA):UV curing potting compounds generally adhere well to acrylics.
- Polycarbonates (PC):Some UV curing compounds may bond with polycarbonates, but compatibility testing is recommended.
- Polyethylene (PE) and Polypropylene (PP):Adhesion may be challenging, and surface treatment or specific formulations may be required for better compatibility.
Metals:
- Aluminum:UV curing compounds usually adhere well to aluminum.
- Copper:Good compatibility, but the substrate’s surface condition may affect adhesion.
- Stainless Steel:Generally compatible, but surface preparation may improve adhesion.
Glass:
- Borosilicate Glass:Good compatibility; UV curing compounds adhere well.
- Soda-Lime Glass:Generally consistent, but surface treatment may enhance adhesion.
Ceramics:
- Alumina and Zirconia:UV curing compounds usually bond well to ceramic substrates.
- Porcelain:Compatibility may vary, and surface treatment may be necessary.
Composites:
- Fiberglass Reinforced Plastics (FRP):UV curing compounds are generally compatible.
- Carbon Fiber Composites:Compatibility may vary; surface treatment can enhance adhesion.
Rubbers and Elastomers:
- Silicone Rubber:Adhesion can be challenging; specialized formulations may be needed.
- EPDM, Nitrile, and Neoprene:Some UV curing compounds may work well, but testing is recommended.
Ceramic PCBs:
- Alumina-based PCBs:Good compatibility; UV curing compounds can be used.
- LTCC (Low-Temperature Co-fired Ceramic):Generally compatible, but testing is advisable.
Other Considerations:
- Surface Preparation:Proper cleaning and, if necessary, surface treatment can enhance adhesion.
- Thermal and Chemical Resistance:Consider the operating environment and ensure the cured potting compound can withstand temperature and chemical exposure.
Always refer to the specific technical data sheets and guidelines the potting compound manufacturer provided. Additionally, conduct thorough compatibility testing, including adhesion tests and exposure to relevant environmental conditions, to ensure the performance and longevity of the potting material in your specific application.
How are UV-curing potting compounds utilized in the aerospace and automotive industries?
UV-curing potting compounds find several applications in the aerospace and automotive industries due to their unique properties and advantages. Here are some ways in which these compounds are utilized in these sectors:
Aerospace Industry:
Electronic Component Protection:
- UV-curing potting compounds encapsulate and protect electronic components in aerospace applications. This helps safeguard sensitive electronics from environmental factors such as moisture, vibration, and thermal cycling.
Weight Reduction:
- The aerospace industry places a high premium on weight reduction. UV-curing potting compounds are often preferred because they can be applied in thin layers, reducing the overall weight of electronic assemblies.
Quick Cure Time:
- UV-curing compounds offer rapid curing, allowing for faster production cycles and reducing assembly time. This is crucial in the aerospace industry, where efficiency and speed are essential.
Vibration and Shock Resistance:
- The ability of UV-curing potting compounds to form a resilient and durable encapsulation makes them suitable for applications where components are subjected to vibrations and shocks, which are typical in aerospace environments.
Temperature Resistance:
- Aerospace applications often involve extreme temperature variations. UV-cured compounds can be formulated to withstand a wide range of temperatures, making them suitable for use in the harsh conditions of space travel.
Space-Saving Designs:
- The compact nature of UV-cured potting compounds allows space-saving designs, a critical factor in aerospace applications where every inch of space is carefully considered for weight and efficiency.
Automotive Industry:
Electronic Control Units (ECUs) Encapsulation:
- UV-curing potting compounds encapsulate ECUs and other electronic components in automotive applications. This protects sensitive electronics from moisture, chemicals, and thermal stress, ensuring reliable performance.
LED Module Encapsulation:
- In automotive lighting systems, UV-curing compounds encapsulate and cover LED modules. This enhances the durability and longevity of the lighting components.
Sensors and Cameras Protection:
- Sensors and cameras used in modern vehicles for safety and driver-assistance systems are often potted with UV-curing compounds. This protects these components from environmental factors and ensures consistent performance.
Reduced Weight:
- Like the aerospace industry, the automotive sector benefits from the weight reduction of UV-curing potting compounds. This is especially important for electric vehicles, where overall weight directly impacts energy efficiency.
Efficient Production Processes:
- The quick cure time of UV-curing compounds supports efficient production processes in the automotive industry. Faster assembly and shorter curing times contribute to increased manufacturing throughput.
Resistance to Automotive Fluids:
- UV-cured compounds can be formulated to resist automotive fluids such as oils, fuels, and coolants. This is essential for ensuring the long-term reliability of potted components in the engine compartment.
In both industries, it’s crucial to select UV-curing potting compounds with properties tailored to the application’s specific requirements, and compatibility testing is typically conducted to ensure optimal performance and reliability over time.
What regulatory compliance and standards should be adhered to in UV Curing Applications?
UV curing applications involve using ultraviolet (UV) light to cure or dry inks, coatings, adhesives, and other materials. Adhering to regulatory compliance and industry standards is essential to ensure safety, quality, and environmental responsibility. Here are some of the key regulations and standards relevant to UV curing applications:
Occupational Safety and Health Administration (OSHA):
- 29 CFR 1910.1000 – Air Contaminants:This regulation sets exposure limits for airborne contaminants, including UV radiation.
American Conference of Governmental Industrial Hygienists (ACGIH):
- TLVs (Threshold Limit Values):ACGIH provides TLVs for UV radiation exposure, and adhering to these recommended exposure limits is essential.
International Electrotechnical Commission (IEC):
- IEC 60335-2-27:This standard outlines appliance safety requirements, including UV curing equipment. Compliance ensures the safety of electrical and mechanical components.
National Electrical Code (NEC):
- Article 522 – Control Systems for Permanent Amusement Attractions:UV curing equipment may be used in printing and other applications, and compliance with NEC ensures electrical safety.
International Organization for Standardization (ISO):
- ISO 4892-2:This standard provides guidelines for exposing specimens to UV radiation for testing purposes.
FDA Regulations (for UV curing in food packaging):
- 21 CFR 175.300:Compliance with this regulation is necessary for UV-curable inks and coatings used in food packaging.
National Fire Protection Association (NFPA):
- NFPA 70 – National Electrical Code:Ensures electrical safety in installing and using electrical equipment, including UV curing systems.
Control of Substances Hazardous to Health (COSHH):
- Ensures the safe use of chemicals and materials in the UV curing process.
REACH (Registration, Evaluation, Authorization, and Restriction of Chemicals):
- Compliance with REACH regulations is essential for substances used in UV-curable inks and coatings.
Environmental Protection Agency (EPA):
- Compliance with EPA regulations, especially in the handling and disposal of UV-curable materials, to minimize environmental impact.
National Institute for Occupational Safety and Health (NIOSH):
- NIOSH provides guidelines and recommendations for occupational safety, including exposure limits to hazardous agents.
Always check for updates and revisions to these regulations and standards, as they may change over time. It’s also crucial to consult with industry experts, legal professionals, and relevant authorities to ensure compliance with local and international regulations in UV curing applications.
What is the future outlook for emerging technologies in UV-curing potting compounds?
UV-curing potting compounds have gained popularity due to their ability to cure quickly and efficiently, offering advantages such as reduced processing time, energy savings, and improved manufacturing efficiency. Here are some potential future trends and developments in this field:
- Improved Formulations:Ongoing research and development will likely result in the creation of UV-curing potting compounds with enhanced properties, such as better thermal conductivity, electrical insulation, and resistance to environmental factors. These improvements will expand the range of applications for UV-cured potting compounds.
- Customization and Specialization:As industries have diverse requirements, there could be a trend toward more specialized UV-curing potting compounds designed for specific applications. Custom formulations may address the unique needs of various sectors, such as electronics, automotive, and aerospace.
- Adoption in Electronics Manufacturing:The electronics industry is a significant consumer of potting compounds, and UV-curing formulations may see increased adoption in this sector. As electronic devices become smaller and more complex, manufacturers may seek faster and more precise potting solutions offered by UV curing.
- Green and Sustainable Technologies:There is a growing emphasis on sustainability and environmentally friendly manufacturing processes. Future developments in UV-curing potting compounds may focus on more eco-friendly formulations with reduced environmental impact and using renewable materials.
- Integration with Industry 4.0:Integrating UV-curing processes into innovative manufacturing environments, often associated with Industry 4.0, could become more prevalent. Automation, real-time monitoring, and control systems may be implemented to enhance the efficiency and quality of UV-curing processes.
- Global Market Growth:As awareness of the benefits of UV-curing potting compounds increases, there may be a broader global adoption of these technologies. Emerging markets could contribute to the growth of UV-curing technologies.
It’s essential to stay updated on the latest research, industry news, and technological advancements to understand the current state and future trajectory of UV-curing potting compounds. Consulting industry reports, attending conferences, and monitoring developments from key players in the field will provide more accurate and timely information.
Conclusion:
In conclusion, UV Curing Potting Compounds represent a breakthrough in modern manufacturing and assembly processes, offering unparalleled speed, precision, and efficiency. As industries evolve, embracing these compounds opens new possibilities for enhanced product performance and durability. Whether you are an engineer, researcher, or industry professional, this category is a valuable resource for navigating the world of UV Curing Potting Compounds and staying abreast of the latest developments in this dynamic field. Explore the subheadings to gain insights into the diverse applications, best practices, and future trends in UV curing technology.
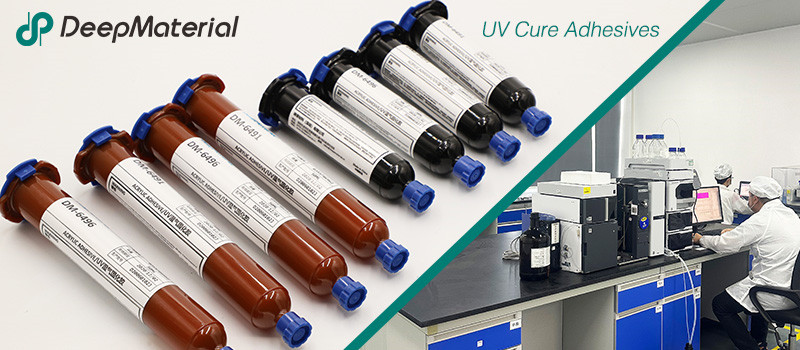
DeepMaterial
Based on the core technology of adhesives, DeepMaterial has developed adhesives for chip packaging and testing, circuit board level adhesives, and adhesives for electronic products. Based on adhesives, it has developed protective films, semiconductor fillers, and packaging materials for semiconductor wafer processing and chip packaging and testing. More…
UV Curing Adhesives
UV light cure have a number of benefits making them a popular choice among many product assembly and manufacturing applications. Many UV light cure adhesives can provide a nearly instantaneous bond to difficult substrates like glass and plastic. UV cure adhesives often require an accelerator or UV light for a bond to form.
Adhesive Blogs & News
The latest adhesive industry science and technology, Deepmaterial news, and market trends and forecasts.
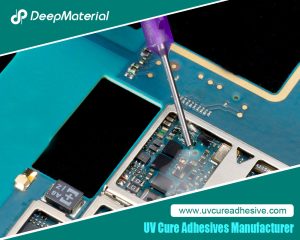
Electrical Potting Compound
Electrical Potting Compound In the vast field of modern electronic technology, Electrical Potting Compound plays a crucial role. It is like the invisible guardian inside electronic devices, providing reliable protection and stable performance support for various precise electronic components. Definition and Classification of Electrical Potting Compound Electrical Potting Compound is a special material
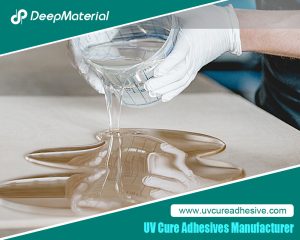
The Mystery and Application of Polyurethane Potting
The Mystery and Application of Polyurethane Potting In the modern industrial and technological fields, Polyurethane Potting is playing an increasingly important role. It not only provides reliable protection for various electronic devices and components but also shows unique advantages in optimizing performance and extending service life. What is Polyurethane Potting Polyurethane Potting is a
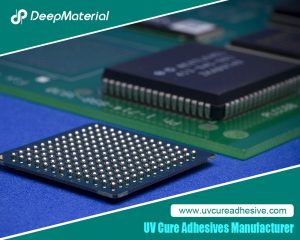
Waterproof Potting Compound: The Invisible Guardian of Electronic Devices
Waterproof Potting Compound: The Invisible Guardian of Electronic Devices In the era of rapid technological development today, electronic devices have become an indispensable part of our lives and work. From smart phones, tablets to smart home devices and industrial control systems, the application of electronic devices is everywhere. However, these devices often face the tests
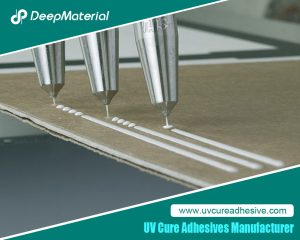
Potting Compound vs Epoxy: A Comparative Study and Application Overview
Potting Compound vs Epoxy: A Comparative Study and Application Overview In the modern industrial and electronic domains, the selection of materials holds a pivotal position in determining the performance, reliability, and longevity of products. Potting Compound and Epoxy are two frequently encountered materials that each demonstrate remarkable capabilities in numerous applications, yet they possess
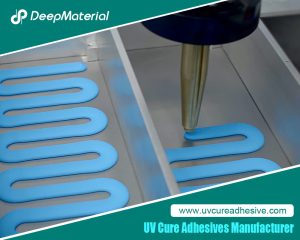
Exploring Potting Compound for Electronics: The Key Material for Providing Reliable Protection to Electronic Products
Exploring Potting Compound for Electronics: The Key Material for Providing Reliable Protection to Electronic Products In the current era of rapid technological development, electronic products have become an indispensable part of our lives. From smartphones, tablets to smart home devices and industrial control systems, the performance and reliability of electronic devices are crucial for
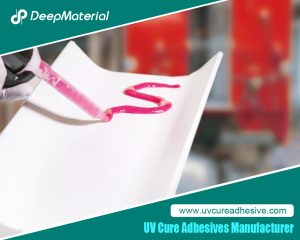
The Wonderful World of UV Curing Potting Compound
The Wonderful World of UV Curing Potting Compound In the rapid development of modern technology, various innovative materials continue to emerge, bringing unprecedented possibilities to applications in various fields. Among them, UV curing potting compound has become a shining star in the field of materials science with its unique performance and wide range of