- Home
- >
- UV Cure Adhesive
- >
- UV Curable Pressure Sensitive Adhesive
UV Curable Pressure Sensitive Adhesive
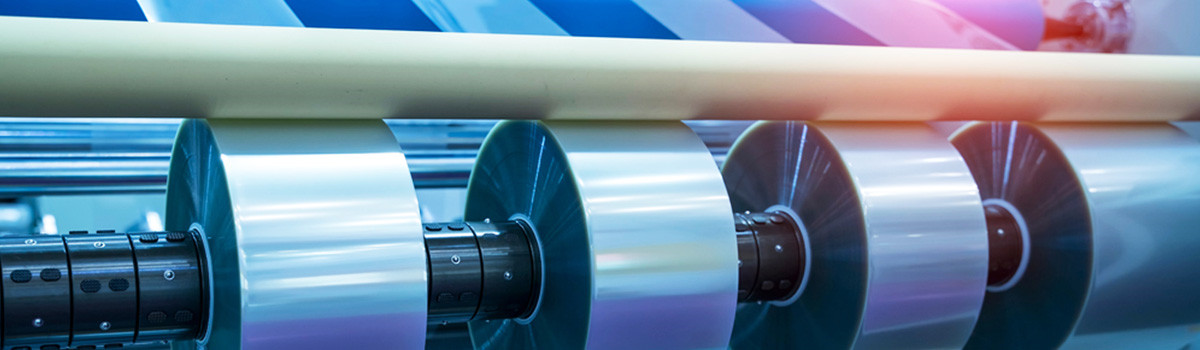
UV Curable Pressure Sensitive Adhesives (UV PSA)adhesives offer a unique combination of quick curing, exceptional bonding strength, and versatility, making them a popular choice in various industries. This guide will explore the characteristics, applications, and key considerations associated with UV PSA. Whether you’re a professional in the field or just curious about adhesive technologies, this page aims to provide valuable insights.
Table of Contents
ToggleWhat is UV-Curable Pressure Sensitive Adhesive?
UV-curable pressure-sensitive adhesives (PSAs) cures or set when exposed to ultraviolet (UV) light. Pressure-sensitive adhesives are materials that adhere to surfaces when light pressure is applied. These adhesives are commonly used in various applications, such as tapes, labels, and graphic films.
Here’s how UV-curable PSAs typically work:
- Composition: UV-curable PSAs are composed of a base adhesive material and photoinitiators. The base adhesive provides the adhesive properties, while the photoinitiators are chemicals that respond to UV light.
- Application: The adhesive is applied to a substrate, such as a film or a label, as a liquid or a coating.
- UV Exposure: When the adhesive-coated substrate is exposed to UV light, the photoinitiators in the adhesive react to the light and initiate a curing process. This process involves the rapid polymerization or crosslinking of the adhesive, transforming it from a liquid or soft state to a solid and durable state.
- Pressure Sensitivity: The cured adhesive retains its pressure-sensitive properties, meaning it adheres to surfaces when light pressure is applied. This makes it suitable for applications where a bond is needed without heat or solvents.
UV-curable PSAs offer several advantages:
- Rapid Curing: UV curing is quick, allowing for high-speed production.
- Low Heat Generation: Unlike other curing methods, UV curing generates minimal heat, making it suitable for heat-sensitive substrates.
- Precise Control: UV curing can be precisely controlled, providing consistency in the curing process.
- Environmentally Friendly: UV-curable adhesives often contain fewer volatile organic compounds (VOCs), making them more environmentally friendly.
These adhesives find applications in industries such as printing, electronics, medical devices, and automotive, where fast and reliable bonding is essential. They are often used to manufacture labels, tapes, and other products requiring a strong, quick, clean bond.
How does UV curing work in adhesives?
UV curing in adhesives is a process where ultraviolet (UV) light initiates a chemical reaction that transforms a liquid adhesive into a solid or semi-solid state. This process is commonly used in various industries, such as electronics, optics, medical devices, and automotive. UV curing offers several advantages, including fast curing times, reduced energy consumption, and precise and controlled bonding.
Here’s a general overview of how UV curing works in adhesives:
- Adhesive Composition:UV-curable adhesives typically comprise monomers, oligomers, photoinitiators, and other additives. Monomers are small molecules that can undergo polymerization, while oligomers are larger molecules that give the adhesive its main properties. The photoinitiator is a critical component that absorbs UV light and initiates the polymerization process.
- Application:The liquid adhesive is applied to the surfaces to be bonded. This can be done manually or through automated dispensing systems.
- Exposure to UV Light:Once the adhesive is in place, it is exposed to UV light with a specific wavelength, typically 200 to 400 nanometers. Commonly, the light source is a UV lamp or LED.
- Photoinitiation:The photoinitiator in the adhesive absorbs the UV light and undergoes a chemical reaction. This reaction generates free radicals or other reactive species, depending on the type of photoinitiator used.
- Polymerization:The free radicals or reactive species initiate polymerization reactions among the monomers and oligomers in the adhesive. Polymerization involves the formation of chemical bonds between the adhesive molecules, leading to the creation of a three-dimensional network.
- Curing:As polymerization progresses, the adhesive transitions from a liquid to a solid or semi-solid. This curing process occurs rapidly, often within seconds or minutes, depending on the adhesive formulation and the intensity of the UV light.
- Final Bond:Once the UV curing process is complete, the sticky forms a strong bond between the surfaces it is applied to. The resulting bond is typically durable, resistant to heat and chemicals, and has a fast cure time.
UV curing is advantageous because it allows for precise control over the process, reducing the need for additional processing time and energy consumption associated with traditional curing methods. Additionally, UV-cured adhesives are often solvent-free, reducing environmental and health concerns.
What are the critical components of UV PSA?
UV Curable Pressure Sensitive Adhesives (UV PSA) cure upon exposure to ultraviolet (UV) light. These adhesives are commonly used in various applications, such as labels, tapes, and medical devices. The critical components of UV PSA include:
- Photoinitiators:These chemicals absorb UV light and initiate the curing process. When exposed to UV light, photoinitiators generate free radicals or other reactive species that react with the monomers or oligomers in the adhesive, causing polymerization.
- Monomers and Oligomers:UV PSAs typically consist of monomers and oligomers, which are the building blocks of the adhesive. Monomers are small, reactive molecules, while oligomers are larger molecules formed by the polymerization of monomers. They contribute to the adhesive’s properties, such as flexibility, tackiness, and overall performance.
- UV Absorbers and Stabilizers:UV absorbers help prevent adhesive degradation due to prolonged UV exposure. Stabilizers may also be included to enhance the long-term stability of the cured adhesive.
- Adhesion Promoters:These compounds enhance the adhesive properties, promoting better bonding to various substrates. Adhesion promoters improve the adhesive’s performance on different surfaces and under other conditions.
- Tackifiers:Tackifiers are added to enhance the initial tack or stickiness of the adhesive. They help the adhesive bond quickly to the substrate upon application.
- Fillers and Reinforcements:Fillers, such as silica or other particulate materials, may be added to modify the rheological properties of the adhesive and improve its mechanical strength.
- Modifiers:Additional modifiers may be incorporated to tailor the adhesive properties, such as viscosity, flexibility, and adhesion strength, to meet specific application requirements.
- UV Light Source:An external source is required to initiate the curing process. This light source emits UV radiation in the appropriate wavelength range for the photoinitiators to activate and create the polymerization of the adhesive.
It’s essential to carefully balance and optimize the formulation of these components to achieve the desired adhesive properties for the specific application of UV PSA. The curing process occurs rapidly upon exposure to UV light, providing fast and efficient bonding in various industrial processes.
What are the advantages of using UV PSA?
UV Curable Pressure Sensitive Adhesives (UV PSA) offer several advantages, making them a popular choice for various applications. Here are some of the key advantages of using UV PSA:
Rapid Cure:
- UV PSAs cure quickly upon exposure to UV light, allowing for fast processing and high-speed production.
- The quick curing time contributes to increased efficiency and shorter production cycles.
Reduced Energy Consumption:
- UV curing requires less energy than traditional curing methods, such as heat- or solvent-based.
- Lower energy consumption leads to cost savings and environmental benefits.
Common Volatile Organic Compounds (VOCs):
- UV PSA formulations often contain fewer or no solvents, resulting in lower VOC emissions during curing.
- This makes UV PSAs a more environmentally friendly option compared to solvent-based adhesives.
High Productivity:
- Due to their rapid curing characteristics, UV PSAs enable continuous and high-speed production processes.
- Reduced processing times contribute to increased productivity and output.
Excellent Adhesion:
- UV PSAs offer robust and reliable adhesion to many substrates, including plastics, metals, and papers.
- The adhesive bond is often immediate and decisive, providing an excellent initial tack.
Customizable Properties:
- Formulations of UV PSAs can be tailored to achieve specific properties, such as flexibility, tackiness, and adhesion strength, to meet diverse application requirements.
- UV PSA formulations are highly customizable to suit various substrates and end-use specifications.
No Solvent Evaporation:
- Unlike solvent-based adhesives, UV PSAs do not require the evaporation of solvents for curing. This eliminates concerns related to solvent retention and associated environmental and health issues.
Consistent Quality:
- UV curing provides a consistent and uniform cure throughout the adhesive, ensuring reliable and repeatable results.
- The absence of solvent evaporation minimizes the risk of defects and inconsistencies in the adhesive layer.
Versatility:
- UV PSAs find applications in various industries, including packaging, electronics, automotive, medical, and more.
- They can be adapted in multiple forms, such as tapes, labels, films, and coatings.
UV Light Control:
- The curing process of UV PSAs can be easily controlled and adjusted by modifying the intensity and duration of UV light exposure, providing flexibility in production.
While UV PSA offers numerous advantages, it’s essential to consider specific application requirements and conditions when choosing adhesives to ensure optimal performance.
In which industries are UV PSAs commonly used?
UV-curable pressure-sensitive adhesives (UV PSAs) find applications in various industries where quick and efficient bonding with the added advantage of rapid curing is essential. Some common industries where UV PSAs are commonly used include:
Printing and Packaging:
- UV PSAs are widely used in the printing and packaging industry for label applications, film laminations, and other adhesive needs. The rapid curing allows for faster processing speeds in printing and packaging lines.
Electronics:
- In the electronics industry, UV PSAs are used for bonding components, display assembly, and other applications where precise and quick bonding is required. UV curing is often preferred to avoid heat-related damage to sensitive electronic components.
Medical Devices:
- UV PSAs are used to assemble medical devices where a fast and reliable bond is crucial. The ability to control the curing process allows for precise and clean bonding, making them suitable for medical tapes and device assembly applications.
Automotive:
- UV PSAs are used for interior trim assembly, gasket bonding, and automotive label applications in the automotive industry. The rapid curing helps in streamlining the manufacturing process.
Aerospace:
- Aerospace applications often require adhesives with high performance and reliability. UV PSAs are used in aerospace for bonding components and applications where a fast cure is advantageous.
Construction:
- UV PSAs find applications in the construction industry for bonding materials like glass, metal, and plastics. They are used where a quick bond and strong adhesion are required.
Woodworking and Furniture:
- UV PSAs are used for bonding veneers, laminates, and other materials in woodworking and furniture manufacturing. The rapid curing process allows for efficient production in these industries.
Optics:
- UV PSAs are used in optics for lens bonding, optical device assembly, and other precision applications where clarity and speed are essential.
Flexible Electronics:
- UV PSAs can bond flexible substrates and components in flexible electronics due to their quick curing capabilities.
Textiles and Apparel:
- UV PSAs find applications in textile and apparel manufacturing for bonding fabrics, attaching labels, and other assembly processes.
It’s important to note that the use of UV PSAs continues to evolve, and new applications may emerge as technology and materials advance.
Are UV PSAs environmentally friendly?
UV-curable pressure-sensitive adhesives (PSAs) are more environmentally friendly than traditional solvent-based adhesives. However, the environmental impact depends on various factors, and it’s essential to consider both the advantages and potential challenges associated with UV PSAs.
Advantages of UV Curable PSAs:
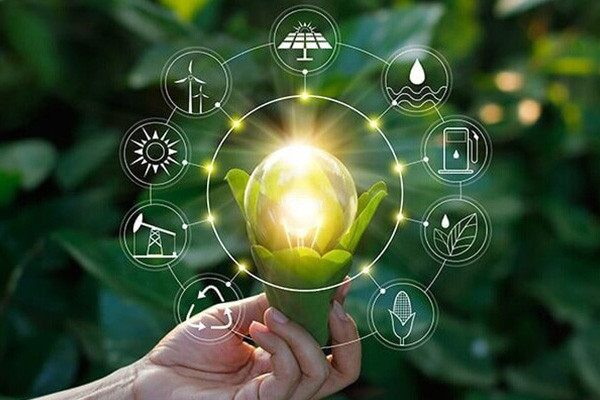
- Reduced Volatile Organic Compounds (VOCs):UV-curing technology typically involves minimal or no solvents, which reduces the emission of VOCs. VOCs can contribute to air pollution and adversely affect human health and the environment.
- Energy Efficiency:UV curing is faster than other curing methods, such as heat or air drying. This energy efficiency can lead to lower energy consumption during the manufacturing process.
- Reduced Waste:UV curing often results in less waste than solvent-based adhesives since solvents are not needed for the evaporation of solvents. This can contribute to a more sustainable production process.
- Improved Productivity:The fast curing time of UV PSAs can enhance production efficiency, reducing resource usage and environmental impact.
Challenges and Considerations:
- Raw Materials:While UV PSAs may have fewer VOC emissions, it’s essential to consider the raw materials used in their formulation. Some UV-curable materials may still contain chemicals that could have environmental and health implications.
- Energy Consumption:While UV curing is generally more energy-efficient, the energy source can impact the overall environmental profile. If the electricity used for UV curing comes from non-renewable sources, it may still contribute to carbon emissions.
- Waste Disposal:Disposing of UV-cured materials can be challenging, and the environmental impact depends on the specific formulation. Some UV-cured materials may be recyclable, while others may pose challenges for disposal.
- Cost Considerations:UV curing equipment and formulations may initially cost more than traditional methods. However, the long-term benefits of energy efficiency and reduced waste may offset these costs.
UV-curable PSAs can be a more environmentally friendly than traditional solvent-based adhesives, primarily due to reduced VOC emissions and energy efficiency. However, it’s crucial to assess the entire life cycle, including raw material sourcing, production, application, and disposal, to comprehensively evaluate their environmental impact. Manufacturers and users should also stay informed about advancements in UV-curing technology and explore ways to enhance its sustainability further.
What substrates are compatible with UV PSA?
UV-curable pressure-sensitive adhesives (PSAs) are often used in various applications requiring rapid curing and strong adhesion. These adhesives are typically used in labels, tapes, and other bonding applications. The compatibility of UV PSAs with different substrates depends on the specific formulation of the adhesive. However, UV PSAs generally exhibit good adhesion to many substrates. Some common substrates that are compatible with UV PSAs include:
Plastics:
- Polyethylene (PE)
- Polypropylene (PP)
- Polyvinyl chloride (PVC)
- Polycarbonate (PC)
- Acrylic (PMMA)
- Polyester (PET)
- Polyethylene terephthalate glycol (PETG)
Metals:
- Aluminum
- Stainless steel
- Copper
- Brass
Paper and Cardboard:
- Coated paper
- Uncoated paper
- Cardboard
Glass:
- Clear glass
- Frosted glass
Wood:
- Plywood
- MDF (Medium-Density Fiberboard)
- Hardwood
Ceramics:
- Glazed ceramics
Fabrics:
- Cotton
- Polyester
- Nylon
Foams:
- Polyurethane foam
- Polyethylene foam
- PVC foam
Rubber:
- Natural rubber
- Synthetic rubber
Other Substrates:
- Concrete
- Fiberglass
- Some painted surfaces
It’s important to note that the performance of UV PSAs can vary based on the specific adhesive formulation, curing conditions, and the surface characteristics of the substrate. Before using a UV PSA in a particular application, it is advisable to conduct thorough testing to ensure compatibility and desired performance. Factors such as surface cleanliness and preparation can also influence the adhesive’s effectiveness. Always follow the manufacturer’s recommendations and guidelines for adequately applying and curing UV PSAs.
Can UV PSAs withstand extreme temperatures?
The ability of UV-curable pressure-sensitive adhesives (PSAs) to withstand extreme temperatures can vary depending on the specific formulation of the adhesive. UV PSAs, in general, may exhibit good thermal stability and resistance to a range of temperatures. Still, their performance can be influenced by factors such as the choice of monomers, oligomers, photoinitiators, and other additives in the adhesive formulation.
Here are some considerations regarding the temperature resistance of UV PSAs:
Low-Temperature Resistance:
- UV PSAs can often maintain their adhesive properties at low temperatures. However, the specific low-temperature performance may vary among different formulations. Some UV PSAs remain flexible and tacky at sub-zero temperatures, while others may become less adhesive in extreme cold.
High-Temperature Resistance:
- UV PSAs may have limitations when exposed to high temperatures. The thermal stability of the components in the formulation can influence the adhesive performance. Some UV PSAs are designed to withstand moderate heat, but others may soften, lose adhesion, or degrade at higher temperatures.
Application-Specific Formulations:
- Manufacturers may offer UV PSA formulations tailored for specific temperature requirements. For example, adhesives intended for automotive or electronic applications might be formulated to withstand higher temperatures. In contrast, those used in general labeling or packaging applications may have different temperature resistance characteristics.
Testing and Validation:
- It’s crucial to consult the adhesive manufacturer’s technical data sheets and specifications. Additionally, conducting thorough testing under the specific temperature conditions relevant to your application is essential to ensure that the UV PSA meets the required performance criteria.
Consideration of Substrates:
- The substrate to which the UV PSA is applied can also affect temperature resistance. Some substrates may absorb or dissipate heat differently, impacting the overall performance of the adhesive at extreme temperatures.
Always follow the manufacturer’s guidelines and recommendations for applying and using UV PSAs properly in specific temperature conditions. If you have specific temperature requirements for your application, consider discussing your needs with the adhesive supplier to identify or develop a formulation that meets your performance criteria.
How fast is the curing time for UV PSA?
The curing time for UV-curable pressure-sensitive adhesives (PSAs) can vary based on several factors, including the adhesive’s specific formulation, the UV light source, and the thickness of the adhesive layer. UV PSAs are designed to cure rapidly under ultraviolet (UV) light exposure, and the curing process typically involves the photopolymerization of the adhesive components.
UV PSAs generally offer speedy curing times, often measured in seconds or fractions of a second. The rapid curing is one of the critical advantages of UV-curable adhesives, making them suitable for high-speed production processes. Some factors influencing curing time include:
UV Light Intensity:
- The intensity of the UV light source is a critical factor affecting curing time. Higher UV light intensities can lead to faster and more efficient curing. Manufacturers may specify recommended light intensity levels for optimal curing performance.
Formulation and Thickness:
- The specific formulation of the UV PSA and the thickness of the adhesive layer can influence curing time. Thicker coatings may require longer exposure times to ensure complete curing.
Substrate and Surface Conditions:
- The type and characteristics of the substrate can impact curing time. Additionally, the cleanliness and condition of the substrate surface can affect the adhesive’s ability to cure properly.
Adhesive Composition:
- The choice of monomers, oligomers, photoinitiators, and other additives in the adhesive formulation can influence the speed of the curing reaction.
Process Parameters:
- Specific production process parameters, such as conveyor speed and distance from the UV light source, may also affect the curing time.
It’s essential to consult the technical data sheets and guidelines the adhesive manufacturer provides for precise information on curing times and optimal curing conditions. Additionally, conducting tests in your specific production environment is advisable to ensure that the UV PSA cures efficiently and meets the performance requirements of your application.
Are there any limitations or challenges with UV PSA?
While UV-curable pressure-sensitive adhesives (PSAs) offer numerous advantages, they also have limitations and challenges. It’s essential to be aware of these factors when considering the use of UV PSAs in specific applications:
Substrate Sensitivity:
- Some substrates may be more challenging for UV PSAs. Highly absorbent or reflective surfaces can impact the curing process, leading to incomplete or uneven curing. Certain plastics or materials with low surface energy require additional surface treatment for improved adhesion.
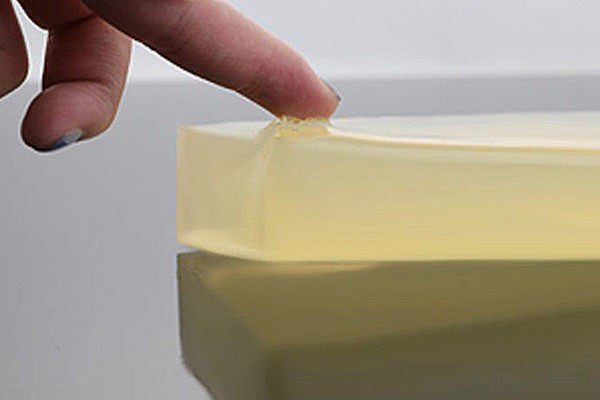
Shadowing Effect:
- UV light may have difficulty reaching areas that are shaded or obstructed. This “shadowing effect” can result in incomplete curing in regions not directly exposed to the UV light source. Proper consideration of the substrate geometry and adhesive application is essential to mitigate this challenge.
Temperature Sensitivity During Application:
- The viscosity of UV PSAs can change with temperature variations, affecting their flow and application characteristics. Adhesive application and curing processes may need adjustments to accommodate temperature changes in the production environment.
Cost of UV Equipment:
- UV curing systems can be expensive to install and maintain. The initial investment in UV equipment, including UV lamps and associated curing systems, maybe a consideration for some applications.
Limited Depth of Cure:
- UV light has a narrow penetration depth, so the curing is generally limited to the surface layer of the adhesive. This limitation may affect UV PSAs’ performance in applications requiring deep penetration.
UV Light Absorption:
- Some pigments and additives in substrates or inks may absorb UV light, reducing their effectiveness in curing the adhesive. This can be a concern when working with colored substrates or printed materials.
UV Radiation Exposure:
- UV radiation poses potential health and safety concerns for operators. Adequate precautions are essential, such as using personal protective equipment and ensuring proper ventilation.
Moisture Sensitivity:
- UV PSAs may be sensitive to moisture during application, affecting their curing performance. Adequate control of humidity in the production environment may be necessary.
Despite these challenges, UV PSAs are widely used due to their fast curing times, environmental benefits (low VOC emissions), and suitability for various applications. Addressing these challenges involves careful formulation, process optimization, and proper equipment selection. It’s crucial to work closely with adhesive suppliers and consider the specific requirements of the intended application.
Can UV PSA be applied manually, or is it automated?
The application of UV-curable pressure-sensitive adhesives (PSAs) can be performed manually or through automated processes, depending on the application’s specific requirements and the production scale. Both manual and automatic application methods have their advantages and limitations.
Manual Application:
- In certain situations, especially for small-scale or prototype production, UV PSAs can be applied manually. This may involve using hand-held dispensing equipment or applying the adhesive directly onto the substrate. Manual application provides flexibility and may be suitable for applications with varying geometries or low production volumes.
Automated Application:
- For large-scale or high-speed production processes, automated application of UV PSAs is often preferred. Mechanical systems can include roll-to-roll coating, screen printing, curtain coating, or other precision dispensing methods. Automation provides consistency, precision, and higher production efficiency. It is commonly used in label manufacturing, electronics, and packaging industries.
Dispensing Equipment:
- Both manual and automated application methods may involve dispensing equipment such as coating machines, screen printers, or robotic dispensers. The choice of equipment depends on the specific application requirements, the substrate, and the desired coating thickness.
UV Curing Systems:
- Regardless of the application method, UV PSAs require exposure to ultraviolet (UV) light for curing. UV curing systems, including UV lamps and conveyors, are integral to the curing process. These systems may be integrated into manual or automated production lines.
The decision between manual and automated application methods depends on factors such as production volume, required precision, cost considerations, and the nature of the application. Automated processes are generally preferred for large-scale manufacturing due to increased efficiency, consistency, and reduced labor costs. However, the manual application may be more suitable for smaller runs, prototyping, or applications with complex geometries.
It’s important to note that regardless of the application method, proper training and adherence to safety guidelines are essential, especially when working with UV PSAs and UV curing equipment. Additionally, the choice of application method should align with the specific needs and goals of the production process.
Are there specific safety considerations when working with UV PSA?
Yes, there are specific safety considerations that should be taken into account when working with UV-curable pressure-sensitive adhesives (PSAs). Here are some important safety guidelines:
UV Radiation Exposure:
- UV PSAs are cured through exposure to ultraviolet (UV) light. UV radiation can be harmful to the skin and eyes. It is essential to use personal protective equipment (PPE) such as UV-blocking gloves, safety glasses, and clothing that covers exposed skin.
Ventilation:
- Ensure proper ventilation in the working area to minimize fume exposure, particularly during curing. Adequate ventilation helps dissipate any volatile components and ensures a safe working environment.
UV Lamp Safety:
- When working with UV curing systems, follow proper procedures for turning on and off UV lamps. Avoid direct exposure to UV light, and use appropriate shielding to protect operators from accidental exposure.
Protective Measures:
- Implement safeguards such as interlocks and safety curtains to prevent unintentional exposure to UV radiation. Follow manufacturer recommendations for the safe use of UV curing equipment.
Personal Protective Equipment (PPE):
- Ensure workers have the necessary PPE, including UV-blocking goggles or face shields, gloves, and appropriate clothing. Regularly inspect and replace PPE as needed.
Skin Contact and Inhalation:
- Minimize skin contact with uncured UV PSA. In case of skin contact, wash the affected area with soap and water. Avoid inhaling fumes, and if working with the adhesive in an enclosed space, ensure proper respiratory protection.
Chemical Exposure:
- Adhesive formulations may contain chemicals that could pose health risks. Review the safety data sheet (SDS) provided by the adhesive manufacturer for information on potential hazards, safe handling procedures, and first aid measures.
Training:
- Provide proper training to personnel working with UV PSAs. Ensure that employees are aware of the potential hazards associated with the materials and equipment they are using and are trained in safe operating procedures.
Emergency Procedures:
- Establish and communicate emergency procedures, including protocols for handling spills, accidental exposures, and first aid. Ensure that emergency equipment, such as eye wash stations and fire extinguishers, is readily accessible.
Storage and Handling:
- Store UV PSAs by the manufacturer’s recommendations, considering factors such as temperature, humidity, and compatibility with other materials. Follow proper handling procedures to minimize the risk of spills or accidents.
Always adhere to the safety guidelines provided by the adhesive manufacturer, and consult the material safety data sheet (MSDS) or safety data sheet (SDS) for detailed information on handling, storage, and emergency response. Additionally, local occupational health and safety regulations should be followed to ensure a safe working environment.
What are the different forms in which UV PSA is available? (e.g., liquid, film, tape)
UV-curable pressure-sensitive adhesives (UV PSA) cure or set upon ultraviolet (UV) light exposure. These adhesives are commonly used in various applications due to their fast curing times and versatility. UV PSAs are available in different forms to suit specific requirements. Some common forms include:
Liquid UV PSAs:
- Liquid UV PSAs are fluid and can be applied using spraying, roll coating, or dispensing methods. They offer flexibility in application and are suitable for bonding irregular surfaces.
Film UV PSAs:
- Film-form UV PSAs come in the form of thin sheets or films. These films can be pre-coated with the UV-curable adhesive and then applied to surfaces. They are often used in applications requiring a precise thickness or consistent coating.
Tape UV PSAs:
- UV PSA tapes consist of a substrate material (such as paper, plastic, or fabric) coated with a layer of UV-curable adhesive. These tapes are convenient and available in various widths and lengths. They are commonly used in bonding, mounting, and other applications.
Sheet UV PSAs:
- Similar to film, UV PSA sheets are pre-coated with the UV-curable adhesive but are typically thicker. These sheets can be cut into shapes and sizes to suit particular applications.
Customized Forms:
- UV PSAs can also be customized based on the application requirements. This may involve creating specific shapes, dimensions, or patterns of adhesive coating to meet the needs of a specific industry or application.
UV PSAs offer advantages such as rapid curing, low-temperature processing, and bonding of various substrates. The choice of form depends on the application’s specific requirements, including the nature of the substrates being connected, the desired bond strength, and the manufacturing process.
Are UV PSAs resistant to chemicals and solvents?
UV-curable pressure-sensitive adhesives (UV PSAs) can vary in chemical and solvent resistance based on their specific formulation and composition. UV PSAs generally exhibit good resistance to certain chemicals and solvents. Still, their performance depends on factors such as the type of substrate, the specific chemicals involved, and the curing conditions.
Critical considerations for chemical and solvent resistance of UV PSAs include:
Chemical Resistance:
- UV PSAs are generally resistant to various chemicals, mainly traditional solvent-based adhesives. However, their performance can vary depending on the substances they encounter. Some UV PSAs may be more resistant to certain chemicals than others, so it’s essential to consider the intended end-use environment.
Solvent Resistance:
- UV PSAs are known for their solvent-free curing process. Once cured, they may exhibit good resistance to some solvents. However, like with chemicals, the resistance can vary. Some solvents may soften or swell the adhesive, affecting its performance.
Substrate Compatibility:
- The chemical and solvent resistance of UV PSAs can be influenced by the type of substrates they are applied to. Compatibility between the adhesive and substrate is crucial for long-term performance. Ensuring the UV PSA is well-matched with the materials it will bond to is essential.
Formulation and Crosslinking:
- The formulation of the UV PSA, including the choice of monomers, oligomers, and additives, can impact its chemical and solvent resistance. Crosslinking during the curing process also contributes to the final properties of the adhesive. Manufacturers may adjust the formulation to enhance resistance to specific chemicals or solvents.
Testing and Validation:
- When chemical or solvent resistance is critical, conducting testing particular to the intended application is advisable. Testing methods can include exposure to the targeted chemicals or solvents and assessing changes in adhesion strength, physical properties, and overall performance.
It’s essential to consult with the adhesive manufacturer or supplier to obtain detailed information about the chemical and solvent resistance of a specific UV PSA product. They can guide the adhesive’s suitability for a particular application and offer recommendations based on the desired performance characteristics.
How does UV PSA compare to other types of adhesives?
UV-curable pressure-sensitive adhesives (UV PSAs) have unique characteristics that differentiate them from other types of adhesives, such as solvent-based adhesives, water-based adhesives, and thermoplastic adhesives. Here’s a comparison of UV PSAs with these different adhesive types:
Curing Mechanism:
- UV PSAs:Cure rapidly upon exposure to ultraviolet (UV) light, leading to fast processing and bonding times.
- Solvent-Based Adhesives:Rely on the evaporation of solvents for curing, which can result in longer curing times.
- Water-Based Adhesives:Cure by water evaporation or absorption, generally requiring more time compared to UV PSAs.
- Thermoplastic Adhesives:Solidify when cooled and regain adhesive properties upon reheating, offering reworkability.
Curing Without Heat:
- UV PSAs:Cure without high temperatures, making them suitable for heat-sensitive substrates.
- Solvent-based and Water-Based AdhesivesMay require elevated temperatures for curing, limiting their use on heat-sensitive materials.
- Thermoplastic Adhesives:Require heating for application and bonding.
Volatile Organic Compounds (VOCs):
- UV PSAs:Typically have low or zero VOCs since they cure without solvent evaporation.
- Solvent-Based Adhesives:Can release VOCs during curing, raising environmental and health concerns.
- Water-Based Adhesives:They tend to have lower VOC content than solvent-based adhesives.
- Thermoplastic Adhesives:VOC content depends on the specific formulation.
Chemical and Solvent Resistance:
- UV PSAs:Can exhibit good resistance to chemicals and solvents, but performance depends on formulation and application conditions.
- Solvent-Based Adhesives:They may offer good resistance to certain chemicals but can be sensitive to others.
- Water-Based Adhesives:They can be more resistant to certain chemicals, with less sensitivity to some solvents.
- Thermoplastic Adhesives:Chemical and solvent resistance can vary depending on the type.
Substrate Compatibility:
- UV PSAs:Can bond to a wide range of substrates, including plastics, metals, and paper.
- Solvent-Based and Water-Based Adhesives:Adhere well to various substrates but may have limitations based on material compatibility.
- Thermoplastic Adhesives:Suitable for specific substrates, with restrictions on certain materials.
Application Flexibility:
- UV PSAs:Offer versatility in application methods, such as liquid, film, tape, and custom forms.
- Solvent-Based, Water-Based, and Thermoplastic Adhesives:Applied in various forms, but specific formulations may be optimized for certain applications.
Choosing the suitable adhesive depends on the application’s specific requirements, including substrate materials, curing conditions, processing speed, and environmental considerations. It’s essential to carefully evaluate the properties of each adhesive type in the context of the intended use.
What role does pressure sensitivity play in UV PSA applications?
The pressure sensitivity in UV-curable pressure-sensitive adhesives (UV PSAs) plays a crucial role in their application and bonding process. The term “pressure-sensitive” refers to the adhesive’s ability to create a bond under light pressure without additional heat or solvent-based curing methods. Here’s a closer look at the role of pressure sensitivity in UV PSA applications:
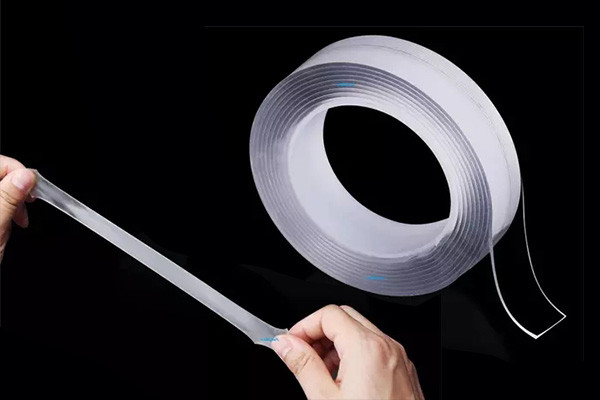
Instant Bonding:
- UV PSAs are designed to provide instant adhesion when exposed to UV light and applied with slight pressure. This feature allows quick bonding without needing prolonged or additional curing methods like heat. The immediate bond formation is advantageous in applications requiring fast assembly or processing.
Ease of Application:
- The pressure-sensitive nature of UV PSAs makes them easy to apply to various substrates. Users can use the adhesive with minimal force, ensuring good contact between the adhesive and the surface. This ease of application is beneficial in applications involving delicate or fragile materials.
Versatility in Substrate Compatibility:
- UV PSAs can adhere to various substrates, including plastics, metals, paper, and other materials. The pressure-sensitive nature allows for adequate bonding to both smooth and irregular surfaces. This versatility makes UV PSAs suitable for diverse applications across different industries.
Adhesion Strength Adjustment:
- The bond strength of UV PSAs can be influenced by the amount of pressure applied during application. Light pressure typically results in a temporary bond that allows repositioning, while firmer pressure leads to a more permanent bond. This adjustability in adhesion strength provides flexibility in application and assembly processes.
Conformability:
- UV PSAs exhibit good conformability, adhering to substrates with varying shapes and contours. This flexibility is essential in applications where the bonding surfaces are not perfectly flat or have irregularities.
Repositioning Capability:
- The pressure-sensitive property allows for repositioning the bonded materials shortly after initial contact. This feature is valuable when precise alignment or adjustments are needed before the adhesive fully cures.
No Heat Requirement:
- Unlike some other adhesives that require heat for activation, UV PSAs can achieve bonding at room temperature. This characteristic is advantageous when working with heat-sensitive materials that elevated temperatures might damage.
The pressure sensitivity of UV PSAs enables easy and quick bonding without the need for heat or solvents. This property, combined with their versatility and ability to adhere to various substrates, makes UV PSAs suitable for a wide range of applications, including labels, tapes, graphic films, and other bonding needs in manufacturing, electronics, and automotive industries.
Are there UV PSA formulations tailored for specific applications?
Yes, UV-curable pressure-sensitive adhesive (UV PSA) formulations are tailored for specific applications. UV PSAs are versatile and can be customized to meet the unique requirements of various industries and applications. The formulation of a UV PSA is a crucial aspect that influences factors such as adhesion strength, flexibility, chemical resistance, and curing speed. Here are some examples of UV PSA formulations tailored for specific applications:
Labels and Packaging:
- UV PSAs used in label and packaging applications often require excellent adhesion to surfaces, including plastic, glass, and paper. These formulations may resist moisture, chemicals, and environmental factors to ensure long-lasting adhesion and label integrity.
Graphics and Signage:
- UV PSAs used in graphics and signage applications must exhibit high clarity and UV resistance to maintain the visual appeal of printed materials. These formulations may also emphasize outdoor durability, flexibility for conformability to curved surfaces, and adhesion to substrates commonly used in the graphics industry.
Electronics Assembly:
- UV PSAs for electronics assembly applications must adhere well to materials commonly found in electronic devices, such as plastics and metals. Additionally, these formulations may prioritize low outgassing to prevent interference with electronic components and may require specific thermal conductivity or insulation levels.
Medical Devices:
- UV PSAs used in medical applications may be designed to meet strict regulatory requirements. These formulations might focus on biocompatibility, sterilization resistance, and skin-friendly properties. They must adhere well to medical-grade materials without causing harm or irritation.
Automotive Applications:
- UV PSAs in the automotive industry may require formulations that resist extreme temperatures, oils, and chemicals in automotive environments. These adhesives might be used for bonding interior components, exterior trims, or vehicle assembly of electronic components.
Solar Panels:
- UV PSAs used in solar panel applications may be designed to bond materials used in photovoltaic modules. These formulations may prioritize durability, weather resistance, and adhesion to various substrates commonly used in solar panel construction.
Optical Films and Displays:
- UV PSAs used in optical applications, such as displays and touchscreens, may require formulations with high optical clarity, low haze, and resistance to yellowing over time. These adhesives must not interfere with the visual quality of the display.
Aerospace Applications:
- UV PSAs used in aerospace applications must meet stringent performance requirements, including resistance to high temperatures, low outgassing, and compliance with aerospace regulations. These formulations may be used for bonding components in aircraft interiors or other aerospace structures.
Manufacturers of UV PSAs often work closely with end-users to understand the specific requirements of their applications and develop formulations that address those needs. Customizing UV PSA formulations allows for various tailored solutions across different industries.
What are the storage and shelf-life considerations for UV PSAs?
Proper storage and handling of UV-curable pressure-sensitive adhesives (UV PSAs) are crucial to maintaining their performance and extending their shelf life. Here are some general considerations for the storage and shelf-life management of UV PSAs:
Temperature and Humidity:
- Store UV PSAs in a relaxed, dry environment. Avoid exposure to extreme temperatures, as high temperatures can accelerate the curing process and potentially reduce shelf life. Humidity control is also essential to prevent moisture absorption, which can affect adhesive properties.
Avoid UV Exposure:
- UV PSAs can cure upon exposure to UV light, so protecting them from direct sunlight and artificial UV sources during storage is essential. Keep the adhesives in opaque containers or packaging to minimize exposure to light.
Sealed Containers:
- Keep UV PSAs in sealed containers to prevent exposure to air and contaminants. Proper sealing helps maintain the integrity of the adhesive and prevents it from drying out or undergoing changes in composition.
Ventilation:
- Ensure adequate ventilation in the storage area to avoid the accumulation of volatile components. Proper ventilation helps maintain the stability of the UV PSA formulation.
Avoid Cross-Contamination:
- Store different formulations of UV PSAs separately to avoid cross-contamination. This is particularly important when dealing with adhesives with specific performance requirements for other applications.
Rotation of Stock:
- Follow a first-in, first-out (FIFO) inventory system to use older stock before newer batches. This practice helps ensure that adhesives are used within their recommended shelf life.
Monitoring Shelf Life:
- Keep track of the shelf life of UV PSAs based on the manufacturer’s recommendations. The shelf life can vary depending on the specific formulation and storage conditions. It’s essential to use the adhesive within the recommended time frame to ensure optimal performance.
Product Packaging:
- Adhere to the manufacturer’s recommendations regarding the proper packaging of UV PSAs. Some adhesives may come in special containers or bags with specific instructions for maintaining product integrity.
Testing Before Use:
- Perform periodic quality control checks on stored UV PSAs to ensure they meet the required specifications. This may involve testing adhesion properties, viscosity, and other relevant characteristics before use.
Manufacturer Guidelines:
- Always follow the guidelines and recommendations provided by the adhesive manufacturer regarding storage conditions, shelf life, and handling procedures. Manufacturers often provide specific instructions based on the unique characteristics of their UV PSA formulations.
By following these storage considerations, manufacturers and users can help ensure that UV PSAs maintain their performance characteristics and adhere to the desired substrates effectively throughout their intended shelf life.
Can UV PSAs be used for medical applications?
UV-curable pressure-sensitive adhesives (UV PSAs) can be used for specific medical applications. However, selecting adhesives for medical applications is highly regulated and requires careful consideration of biocompatibility, sterilization resistance, and adherence to industry standards.
Here are some considerations for using UV PSAs in medical applications:
Biocompatibility:
- Medical-grade adhesives, including UV PSAs, must be biocompatible to ensure they do not cause harm or adverse reactions when in contact with living tissues. Biocompatibility testing is essential to assess the compatibility of the adhesive with the human body.
Cytotoxicity:
- UV PSAs intended for medical applications should undergo cytotoxicity testing to evaluate their potential impact on cell viability. This is particularly important for adhesives that may contact tissues or fluids directly.
Sterilization Compatibility:
- Medical devices and components often undergo sterilization processes. UV PSAs used in medical applications should be compatible with standard sterilization methods such as gamma irradiation, ethylene oxide (EtO) sterilization, or autoclaving without compromising their adhesive properties.
Skin Contact Applications:
- UV PSAs can be used in medical applications involving skin contact, such as wound dressings, medical tapes, and wearable devices. The adhesives must be formulated to adhere securely to the skin while being gentle and not causing irritation.
Regulatory Compliance:
- Adhesives used in medical applications must comply with regulatory standards set by health authorities, such as the U.S. Food and Drug Administration (FDA) or the European Medicines Agency (EMA). Compliance with standards like ISO 10993 for biocompatibility testing is often required.
Application-Specific Requirements:
- Consider the specific requirements of the medical application. For example, adhesives used in diagnostic devices, wearable sensors, or wound care products may have different performance criteria and considerations.
Adhesion to Medical Substrates:
- UV PSAs should exhibit good adhesion to various medical substrates, including plastics, films, and fabrics commonly used in medical device manufacturing.
Custom Formulations:
- Manufacturers may develop custom UV PSA formulations tailored for specific medical applications. These formulations can be optimized for the unique requirements of the intended use, considering factors like flexibility, breathability, and moisture resistance.
Manufacturers and designers in the medical industry need to work closely with adhesive suppliers who specialize in medical-grade materials. These suppliers can guide on selecting or formulating UV PSAs that meet the stringent requirements of medical applications and comply with relevant regulations.
How can UV PSA contribute to product sustainability?
UV-curable pressure-sensitive adhesives (UV PSAs) can contribute to product sustainability in various ways, aligning with broader environmental and eco-friendly goals. Here are several ways in which UV PSAs can support sustainability efforts:
Reduced Energy Consumption:
- UV PSAs cure rapidly upon exposure to ultraviolet light, often in seconds. This fast-curing process eliminates the need for prolonged heating or energy-intensive processes associated with other adhesive curing methods, such as heat-activated adhesives. This can result in significant energy savings during the manufacturing process.
Lower Volatile Organic Compounds (VOCs):
- UV PSAs are typically quiet or accessible from volatile organic compounds (VOCs). VOCs can contribute to air pollution and have environmental and health implications. The use of UV PSAs with low VOC content helps reduce emissions and supports indoor air quality.
Solvent-Free Formulations:
- Unlike some solvent-based adhesives, UV PSAs are formulated without organic solvents. Solvent-free formulations contribute to a healthier working environment and reduce the environmental impact associated with solvent emissions.
Reduced Waste Generation:
- UV PSAs often generate less waste during the manufacturing process compared to some traditional adhesives. Their fast-curing nature allows for quick and precise application, reducing the likelihood of adhesive waste and enabling efficient production processes.
Extended Shelf Life:
- UV PSAs can have a longer shelf life compared to certain other adhesives. This can reduce the frequency of product spoilage and the need for frequent replacements, contributing to overall resource efficiency.
Substrate Versatility:
- UV PSAs can adhere to various substrates, including plastics, metals, and paper. This versatility can reduce material usage as a single adhesive can be applied across multiple materials, promoting resource efficiency.
Recyclability and Convertibility:
- Some UV PSAs are designed to be easily removable or repositionable, facilitating the recycling process. Additionally, UV curing enables converters to create customized shapes and sizes with precision, minimizing material waste in die-cutting processes.
Sustainable Raw Materials:
- Adhesive manufacturers are increasingly exploring using sustainable raw materials in their formulations. This may include bio-based monomers and renewable resources, contributing to a more sustainable supply chain.
Green Certifications:
- Some UV PSAs may qualify for green certifications, such as compliance with environmental standards or being recognized as eco-friendly products. These certifications can ensure the adhesive’s sustainability credentials.
End-of-Life Considerations:
- UV PSAs designed for easy removal or repositioning can contribute to the ease of disassembly and recycling of end-products, promoting circular economy principles.
When considering the sustainability of UV PSAs, it’s essential to evaluate the specific formulation, manufacturing processes, and end-of-life considerations. Collaboration between adhesive manufacturers, converters, and end-users can further enhance sustainability by exploring innovative solutions and best practices throughout the product life cycle.
Conclusion:
In conclusion, UV-curable pressure-sensitive adhesives represent a cutting-edge solution in the adhesive industry. From their rapid curing properties to their wide range of applications, UV PSAs offer numerous benefits for various sectors. This guide addresses common questions and provides a comprehensive overview of UV PSA, helping you make informed decisions about adhesive choices in your projects. If you have further inquiries or specific needs, don’t hesitate to contact our experts for personalized assistance.
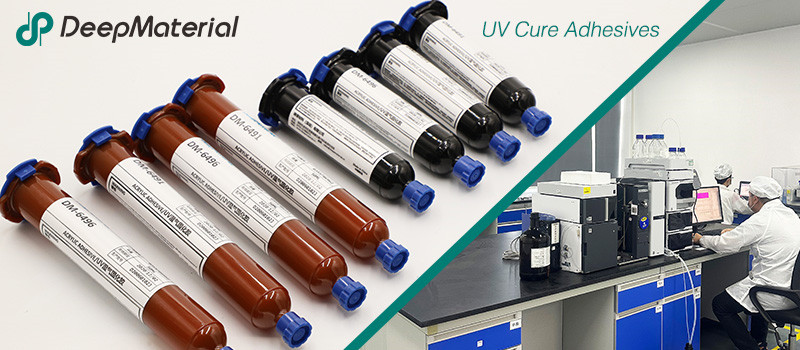
DeepMaterial
Based on the core technology of adhesives, DeepMaterial has developed adhesives for chip packaging and testing, circuit board level adhesives, and adhesives for electronic products. Based on adhesives, it has developed protective films, semiconductor fillers, and packaging materials for semiconductor wafer processing and chip packaging and testing. More…
UV Curing Adhesives
UV light cure have a number of benefits making them a popular choice among many product assembly and manufacturing applications. Many UV light cure adhesives can provide a nearly instantaneous bond to difficult substrates like glass and plastic. UV cure adhesives often require an accelerator or UV light for a bond to form.
Adhesive Blogs & News
The latest adhesive industry science and technology, Deepmaterial news, and market trends and forecasts.
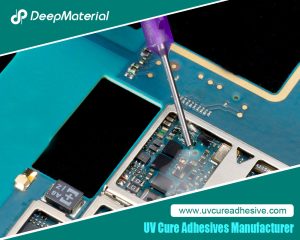
Electrical Potting Compound
Electrical Potting Compound In the vast field of modern electronic technology, Electrical Potting Compound plays a crucial role. It is like the invisible guardian inside electronic devices, providing reliable protection and stable performance support for various precise electronic components. Definition and Classification of Electrical Potting Compound Electrical Potting Compound is a special material
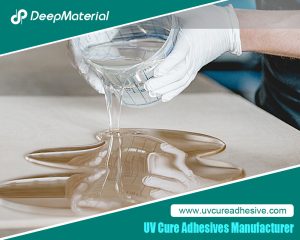
The Mystery and Application of Polyurethane Potting
The Mystery and Application of Polyurethane Potting In the modern industrial and technological fields, Polyurethane Potting is playing an increasingly important role. It not only provides reliable protection for various electronic devices and components but also shows unique advantages in optimizing performance and extending service life. What is Polyurethane Potting Polyurethane Potting is a
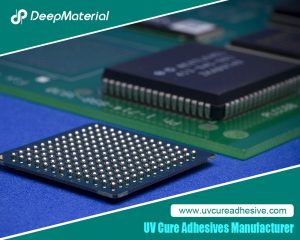
Waterproof Potting Compound: The Invisible Guardian of Electronic Devices
Waterproof Potting Compound: The Invisible Guardian of Electronic Devices In the era of rapid technological development today, electronic devices have become an indispensable part of our lives and work. From smart phones, tablets to smart home devices and industrial control systems, the application of electronic devices is everywhere. However, these devices often face the tests
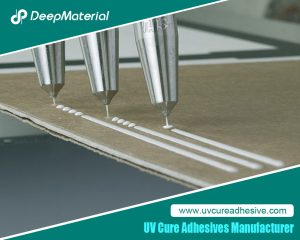
Potting Compound vs Epoxy: A Comparative Study and Application Overview
Potting Compound vs Epoxy: A Comparative Study and Application Overview In the modern industrial and electronic domains, the selection of materials holds a pivotal position in determining the performance, reliability, and longevity of products. Potting Compound and Epoxy are two frequently encountered materials that each demonstrate remarkable capabilities in numerous applications, yet they possess
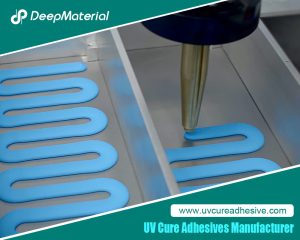
Exploring Potting Compound for Electronics: The Key Material for Providing Reliable Protection to Electronic Products
Exploring Potting Compound for Electronics: The Key Material for Providing Reliable Protection to Electronic Products In the current era of rapid technological development, electronic products have become an indispensable part of our lives. From smartphones, tablets to smart home devices and industrial control systems, the performance and reliability of electronic devices are crucial for
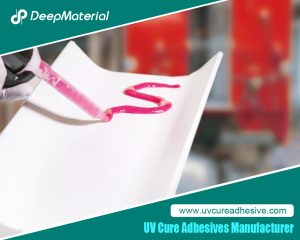
The Wonderful World of UV Curing Potting Compound
The Wonderful World of UV Curing Potting Compound In the rapid development of modern technology, various innovative materials continue to emerge, bringing unprecedented possibilities to applications in various fields. Among them, UV curing potting compound has become a shining star in the field of materials science with its unique performance and wide range of