- Home
- >
- UV Cure Adhesive
- >
- UV Cure Epoxy Adhesive
UV Cure Epoxy Adhesive
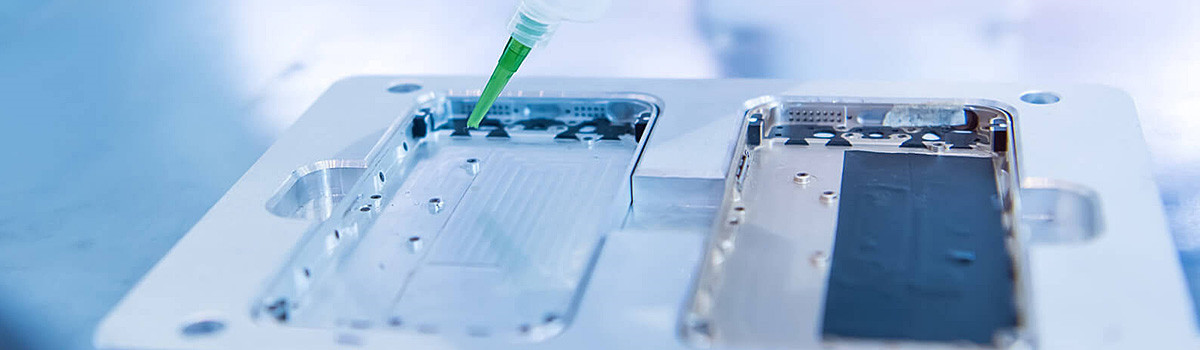
Discover the cutting-edge world of UV cure epoxy adhesive – a revolutionary bonding solution that transforms how materials adhere. UV cure epoxy adhesives offer rapid curing times, exceptional strength, and versatility across various applications. Harnessing the power of ultraviolet light, these adhesives provide efficient bonding without the need for heat or extended curing periods. Explore the limitless possibilities of UV cure epoxy adhesive and elevate your bonding experience.
Table of Contents
ToggleWhat is UV cure epoxy adhesive?
UV cure epoxy adhesive, also known as UV curing epoxy or UV resin, is an adhesive that cures or hardens when exposed to ultraviolet (UV) light. This type of adhesive is commonly used in various industries and applications due to its rapid curing process and strong bond.
Here are some critical characteristics of UV cure epoxy adhesive:
- Curing Process:UV cure epoxy adhesives contain photoinitiators that react to UV light, initiating a polymerization process that transforms the liquid resin into a solid state. This process occurs quickly, often within seconds or minutes, depending on the intensity of the UV light source.
- Application:UV-cure epoxy adhesives bond materials such as glass, plastics, metals, and ceramics. They are particularly suitable for applications requiring a fast and precise bond.
- Versatility:UV cure epoxy adhesives come in various formulations, allowing for viscosity, flexibility, and other properties. This versatility makes them suitable for different applications and industries.
- Minimal Heat Generation:Unlike some other curing processes, UV curing generates minimal heat. This is advantageous for applications where heat-sensitive materials are involved.
- Clear and Transparent:Many UV-cure epoxy adhesives are clear and transparent after curing. This makes them suitable for applications where aesthetics are essential, such as in the electronics or optical industries.
- Limited Depth of Cure:One limitation of UV cure epoxy adhesives is that the curing process is surface-dependent. The depth of cure is influenced by factors such as the intensity of the UV light and the transparency of the materials being bonded. Thicker layers may require multiple exposures to ensure complete curing.
Typical applications of UV cure epoxy adhesives include bonding in electronics, optics, medical devices, and jewelry manufacturing. They are also used for coating and sealing applications. Additionally, these adhesives are popular for DIY projects and crafts due to their ease of use and quick curing times.
How does UV curing work in epoxy adhesives?
UV curing in epoxy adhesives is a process that involves using ultraviolet (UV) light to initiate a chemical reaction that transforms the liquid epoxy resin into a solid, durable adhesive. This method is widely used in various industries for bonding, coating, and encapsulating applications. Here’s a basic overview of how UV curing works in epoxy adhesives:
Composition of Epoxy Adhesive:
- Epoxy adhesives have two main components: resin and a curing agent (a hardener). These components are mixed to create a liquid epoxy adhesive.
Introduction of Photoinitiators:
- Photoinitiators are added to the epoxy formulation. These substances are sensitive to UV light and can absorb energy from it.
Exposure to UV Light:
- When the mixed epoxy adhesive is exposed to UV light, the photoinitiators absorb the UV energy and undergo a photoreaction, generating free radicals.
Initiation of Polymerization:
- The free radicals generated in the photoreaction initiate the polymerization of the epoxy resin. Polymerization is a chemical process in which monomers (small molecules) link together to form a polymer (a large, chain-like molecule).
Formation of Cross-Links:
- As the polymerization process progresses, cross-links form between the polymer chains. Cross-links are chemical bonds that connect adjacent polymer chains, creating a three-dimensional network.
Solidification of Epoxy Adhesive:
- Cross-linking transforms the liquid epoxy resin into a solid, durable material. This solidification is crucial for building a strong and stable bond between the adhered surfaces.
Curing Speed Control:
- The curing speed of the epoxy adhesive can be controlled by adjusting factors such as the intensity of the UV light, the wavelength of the light, and the type and concentration of photoinitiators used. This control allows for flexibility in the curing process to meet specific application requirements.
Advantages of UV Curing in Epoxy Adhesives:
- UV curing offers several advantages, including rapid curing times, reduced energy consumption, and the ability to achieve precise and controlled curing. It is beneficial in applications where fast processing times and high bond strength are essential.
Overall, UV curing in epoxy adhesives provides an efficient and reliable method for creating strong bonds in various industrial applications.
What are the advantages of UV cure epoxy over traditional adhesives?
UV-curable epoxy adhesives offer several advantages over traditional adhesives, typically curing through a chemical reaction or drying process. Here are some of the critical benefits of UV-cure epoxy:
Rapid Cure Time:
- UV-curable epoxies cure almost instantly when exposed to ultraviolet (UV) light. This can significantly reduce assembly time and increase production efficiency compared to traditional adhesives, which may require extended curing periods.
Controlled Curing Process:
- UV curing is a photochemical process, which means the cure time and process can be precisely controlled. This allows for better quality control and ensures that the adhesive only cures when and where it is exposed to UV light.
Reduced Heat Generation:
- UV-cure adhesives generate less heat during the curing process than traditional adhesives, which may require elevated temperatures. This is particularly advantageous for heat-sensitive substrates or components.
No Solvents or Volatile Organic Compounds (VOCs):
- UV-cure epoxy formulations are often solvent-free or contain minimal volatile organic compounds. This makes them more environmentally friendly and safer to use in terms of health and safety regulations.
Improved Bond Strength:
- UV-cured epoxies can provide strong and durable bonds. The instant curing process allows for better adhesion, and controlled conditions ensure consistent bond strength.
Versatility:
- UV-cure epoxy adhesives can bond many substrates, including plastics, glass, metals, and composites. This versatility makes them suitable for various applications across different industries.
Minimal Shrinkage:
- UV-cure epoxy adhesives typically exhibit minimal shrinkage during the curing process. This can be important in applications where precise dimensional stability is crucial.
Easy to Apply:
- UV-cure adhesives are often accessible to apply as they remain liquid or gel until exposed to UV light. This allows for precise application and adjustment of parts before curing.
Lower Energy Consumption:
- Traditional adhesives may require elevated temperatures for curing, leading to higher energy consumption. UV-cure epoxy systems generally require less energy, contributing to energy efficiency in manufacturing processes.
While UV-cure epoxies offer numerous advantages, it’s important to note that their suitability depends on the specific application requirements. Substrate compatibility, bond strength, and instant curing should be considered when choosing an adhesive for a particular use case.
Can UV-cure epoxy be used on different materials?
UV-cure epoxy is an adhesive or resin that cures or hardens when exposed to ultraviolet (UV) light. It is commonly used in various applications due to its fast curing time and strong bonding properties. UV-cure epoxy can be used on multiple materials, but its effectiveness may depend on the specific properties of those materials. Here are some common materials on which UV-cure epoxy can be used:
- Plastics:UV-cure epoxy works well on various plastics, including acrylic, polycarbonate, and ABS.
- Glass:It adheres well to glass surfaces, making it suitable for bonding glass components or glass-to-glass bonding.
- Metals:UV-cure epoxy can bond to metals like aluminum, steel, and others. It is often used in electronic and industrial applications for connecting metal components.
- Ceramics:It is effective for bonding ceramics, making it suitable for applications in the manufacturing of electronic components.
- Wood:UV-cure epoxy can be used on wood surfaces, providing a robust and rapid bond.
- Composite Materials:It can be used on various composite materials, such as carbon fiber or fiberglass, commonly found in aerospace and automotive applications.
- Paper and Cardboard:UV-cure epoxy can bond paper and cardboard effectively, making it useful for specific packaging applications.
It’s important to note that while UV-cure epoxy is versatile, its compatibility with specific materials can vary based on surface preparation, cleanliness, and the particular epoxy formulation. Additionally, some materials may block UV light, preventing proper curing in shadowed areas. Always follow the manufacturer’s guidelines and recommendations for the specific UV-cure epoxy product you are using.
Are UV-cure epoxy adhesives suitable for outdoor applications?
UV-cure epoxy adhesives can be suitable for outdoor applications. Still, their performance will depend on various factors, including the specific formulation of the adhesive and the environmental conditions to which it will be exposed. UV-cure epoxy adhesives generally offer several advantages, such as fast curing times, high bond strength, and excellent clarity. However, there are some considerations to keep in mind for outdoor use:
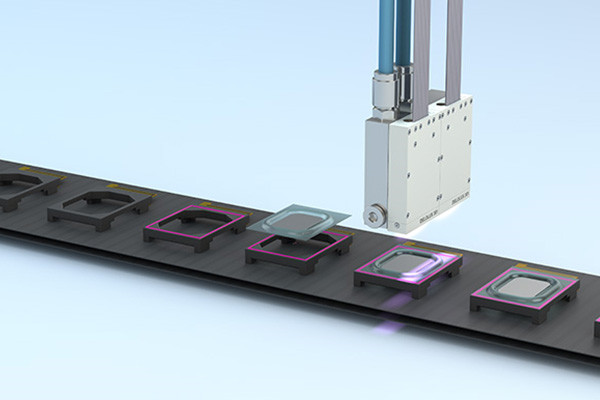
- UV Resistance:While UV-cure adhesives are designed to cure quickly when exposed to ultraviolet light, prolonged exposure to sunlight and outdoor UV radiation can cause some materials to degrade over time. Choosing an adhesive with good UV resistance is essential if it will be exposed to sunlight regularly.
- Weather Resistance:Outdoor environments can expose adhesives to weather conditions, including rain, temperature fluctuations, and humidity. Ensure that the UV-cure epoxy adhesive is designed to withstand these conditions and has good weather resistance properties.
- Temperature Stability:Consider the temperature range of the outdoor environment. Some UV-cure adhesives may have limitations in extreme temperatures, so choosing an adhesive that can maintain its performance across the expected temperature variations is crucial.
- Substrate Compatibility:The adhesive should be compatible with the bonding mato, which terialbonded materials may expand or contract differently under temperature variations, and the adhesive must be able to accommodate these changes without losing its bond strength.
- Chemical Resistance:If the outdoor application involves exposure to chemicals or pollutants, ensure the adhesive has adequate resistance to these substances.
- Manufacturer’s Recommendations:Always follow the manufacturer’s recommendations and guidelines for the specific UV-cure epoxy adhesive you use. They may provide information on its suitability for outdoor applications and any particular precautions or conditions to consider.
Before using a UV-cure epoxy adhesive for outdoor applications, it’s advisable to test it in representative conditions or consult with the manufacturer to confirm its suitability for your specific requirements. Additionally, consider other types of adhesives designed specifically for outdoor use, such as weather-resistant epoxies or polyurethane adhesives, which may offer extended durability in outdoor environments.
What industries benefit most from UV-cure epoxy adhesives?
UV-cure epoxy adhesives find applications in various industries due to their unique properties and advantages. Some of the sectors that benefit most from UV-cure epoxy adhesives include:
- Electronics and Semiconductors:UV-cure epoxy adhesives are commonly used for bonding and encapsulating components in the electronics industry. Their fast curing time and ability to bond sensitive materials without heat make them ideal for electronic applications.
- Medical Devices:In the medical sector, UV-cure epoxy adhesives are used for bonding and assembling medical devices. Their biocompatibility, rapid curing, and ability to bond various substrates make them suitable for medical applications.
- Automotive:UV-cure epoxy adhesives are employed in the automotive industry for bonding components, such as glass, plastic, and metal parts. The fast curing time allows for efficient manufacturing processes, and the high bond strength contributes to the durability of assembled components.
- Optics and Photonics:UV-cure epoxy adhesives are widely used for bonding lenses, optical fibers, and other components in the optics and photonics industry. Their transparency and ability to cure in the presence of light make them suitable for optical applications.
- Aerospace:In the aerospace industry, UV-cure epoxy adhesives are used for bonding lightweight materials, composites, and other components. The fast curing process is advantageous for assembly processes in aerospace manufacturing.
- Woodworking and Furniture:UV-cure epoxy adhesives are employed in woodworking and furniture manufacturing for bonding wooden components. The quick curing time and strong bond contribute to efficient production processes.
- Packaging:UV-cure adhesives are used in the packaging industry for bonding and sealing packages. Their ability to cure on demand and create strong bonds makes them suitable for packaging applications.
- Printing and Labeling:UV-cure epoxy adhesives are used in printing and labeling processes for bonding labels, decals, and other printed materials onto various surfaces. The quick curing time is beneficial for high-speed printing applications.
- Construction:UV-cure epoxy adhesives are employed in the construction industry for bonding glass, metal, and other building materials. Their ability to cure rapidly helps accelerate construction processes.
- Jewelry and Crafts:UV-cure epoxy adhesives create jewelry and crafts for bonding gemstones, metals, and other materials. The precise application and quick curing time are advantageous in these artistic applications.
Overall, the versatility, fast curing time, and strong bonding capabilities of UV-cure epoxy adhesives make them valuable in various industries.
How long does it take for UV cure epoxy to cure?
The curing time for UV-cure epoxy can vary depending on the specific product and its formulation. UV-cure epoxy is designed to cure quickly when exposed to ultraviolet (UV) light. Generally, the epoxy can take a few seconds to a few minutes to fully cure under UV light.
It’s essential to follow the manufacturer’s instructions and recommendations for the specific UV-cure epoxy you are using, as curing times can be influenced by factors such as the intensity of the UV light, the thickness of the epoxy layer, and the specific formulation of the epoxy.
Some UV-cure epoxies may require longer exposure times or multiple passes with UV light to ensure complete curing, especially for thicker layers. UV lamps with higher wattage or intensity may also accelerate the curing process.
Always refer to the product datasheet or contact the manufacturer for precise information on curing times and conditions for the UV-cure epoxy you use.
Are UV-cure epoxy adhesives environmentally friendly?
UV-cure epoxy adhesives can be considered more environmentally friendly than traditional adhesives, but their overall impact depends on various factors.
Advantages of UV-cure epoxy adhesives in terms of environmental friendliness include:
- Low VOCs (Volatile Organic Compounds):UV-cure adhesives typically have low or no volatile organic compounds, which helps reduce air pollution and potential health risks.
- Energy Efficiency:The curing process of UV-cure adhesives is generally faster than other adhesives, reducing energy consumption and associated environmental impacts.
- Reduced Waste:UV-cure adhesives often generate less waste because they don’t require mixing or solvents. This can contribute to a more sustainable manufacturing process.
- No Need for Heat or Solvents:Traditional adhesives may require heat or solvents for curing, which can have environmental and health implications. UV-cure adhesives cure through exposure to ultraviolet light, eliminating the need for these additional materials.
However, it’s important to note some considerations:
- Raw Materials:The environmental impact of any adhesive includes sourcing and producing raw materials. Producing epoxy resins, even those used in UV-cure adhesives may involve petrochemicals and other resources.
- Disposal of Uncured Material:Improper disposal of uncured epoxy or waste material from manufacturing could have environmental consequences. Following proper disposal practices is important to minimize potential negative effects.
- UV Light Source:The curing process relies on ultraviolet light, and the source of this light can impact the overall environmental footprint. If the UV light source is energy-efficient and uses renewable energy, it contributes to the environmental friendliness of the adhesive.
UV-cure epoxy adhesives can be a more environmentally friendly option compared to some traditional adhesives. Still, their overall impact depends on raw material sourcing, manufacturing processes, and proper disposal practices. It’s recommended to consider the specific product and its manufacturing details to assess its environmental impact accurately.
Can UV-cure epoxy withstand extreme temperatures?
UV-cure epoxy generally has good temperature resistance, but its ability to withstand extreme temperatures depends on the specific formulation of the epoxy. UV-cure epoxies are known for their quick curing time when exposed to ultraviolet (UV) light, making them convenient for particular applications.
UV-cure epoxies can generally withstand various temperatures, including moderate to high temperatures. However, the exact temperature range will vary based on the specific product and intended use. Some UV-cure epoxies are designed to withstand temperatures up to 300°F (149°C) or higher.
It’s essential to check the manufacturer’s specifications and technical data sheets for the specific UV-cure epoxy you plan to use. These documents typically provide information on the epoxy’s temperature resistance and other essential properties such as chemical resistance, adhesion strength, and flexibility.
Keep in mind that prolonged exposure to extreme temperatures, especially temperatures beyond the specified limits, may affect the performance of any epoxy, including UV-cure epoxy. If your application involves consistently high or low temperatures, it’s crucial to choose an epoxy formulated to handle those conditions.
Are there safety precautions when using UV cure epoxy?
Yes, there are several safety precautions to remember when using UV-cure epoxy. UV cure epoxy, also known as ultraviolet-curing epoxy resin, is a type of adhesive or coating that cures or hardens when exposed to ultraviolet (UV) light. Here are some general safety guidelines:
Eye and Skin Protection:
- Wear safety goggles to protect your eyes from exposure to UV light.
- Use gloves to prevent direct contact with the epoxy, which can cause skin irritation.
Ventilation:
- Work in a well-ventilated area or use an appropriate fume hood. This helps to minimize exposure to any fumes released during the curing process.
UV Light Exposure:
- Avoid direct exposure of your skin and eyes to UV light sources. Prolonged exposure can cause skin and eye damage.
- Use UV-blocking safety shields or curtains to contain the UV light if possible.
Protective Clothing:
- Wear appropriate protective clothing, such as long sleeves and long pants, to minimize skin exposure to the epoxy.
Read and Follow the Instructions:
- Carefully read and follow the manufacturer’s instructions and safety data sheet (SDS) for the specific UV cure epoxy product you are using.
Curing Time:
- Allow the epoxy to fully cure before handling the cured material. This ensures that residual chemicals have reacted and the material is no longer toxic.
Avoid Ingestion:
- Do not eat, drink, or smoke while working with UV-cure epoxy. Wash your hands thoroughly before eating.
Storage:
- Store UV-cure epoxy in a cool, dry place away from direct sunlight. Follow the manufacturer’s recommendations for proper storage conditions.
Emergency Preparedness:
- Know the location of emergency equipment, such as eye wash stations and first aid kits. Be familiar with the steps to take in case of accidental exposure or ingestion.
Dispose of Waste Properly:
- Follow proper waste materials disposal procedures, including used containers and disposable tools. Some cured epoxy residues may be hazardous and should be handled accordingly.
Always prioritize safety when working with any chemicals or materials. If you have specific questions or concerns about the UV cure epoxy you are using, consult the product’s technical data sheet or contact the manufacturer for guidance.
What are the key features when choosing a UV-cure epoxy adhesive?
When choosing a UV-cure epoxy adhesive, several key features should be considered to ensure that the adhesive meets the specific requirements of your application. Here are some essential elements to consider:
Curing Time:
- Check the curing time of the UV-cure epoxy. Some formulations cure rapidly under UV light, while others may take longer. Choose an adhesive with a curing time that aligns with your application needs.
Light Intensity and Wavelength:
- Different UV-cure epoxies may require specific light intensities and wavelengths for proper curing. Ensure the adhesive is compatible with your UV light source or plan to use.
Substrate Compatibility:
- Consider the types of materials or substrates you will be bonding. Ensure that the UV-cure epoxy is compatible with the materials you are working with, whether they are plastics, metals, glass, or other substrates.
Bond Strength:
- Evaluate the bond strength of the cured epoxy. Different formulations may offer varying levels of adhesion, so choose an adhesive that provides the strength required for your application.
Flexibility and Toughness:
- Depending on the application, the cured epoxy’s flexibility and toughness may be necessary. Some applications require a flexible adhesive that can withstand movement or thermal expansion.
Temperature Resistance:
- Consider the temperature range in which the cured epoxy needs to be performed. Some UV-cure epoxies offer better temperature resistance than others, making them suitable for high-temperature applications.
Chemical Resistance:
- Evaluate the chemical resistance of the cured epoxy. Resistance to chemicals, solvents, and other substances may be crucial depending on the environment.
Transparency and Color:
- If the appearance of the bond line is essential, consider the transparency and color of the cured epoxy. Some applications may require a clear or transparent adhesive for aesthetic reasons.
Viscosity:
- The viscosity of the UV-cure epoxy can impact its ease of application and flow characteristics. Choose a viscosity that suits your application method and the specific bonding requirements.
Shelf Life:
- Check the shelf life of the adhesive. Some UV-cure epoxies have a limited shelf life, so it’s essential to consider the storage conditions and potential expiration date.
Regulatory Compliance:
- Ensure that the UV-cure epoxy complies with relevant regulatory standards and certifications, especially if you work on projects requiring specific industry or safety standards.
Ease of Use:
- Consider the ease of handling and application. Some formulations may be easier to dispense, mix, or apply.
Before making a final decision, it’s advisable to consult the product data-sheet and technical specifications provided by the manufacturer. Testing the adhesive in a small-scale application or obtaining samples for evaluation can help ensure it meets your specific requirements.
Can UV-cure epoxy be used for medical device assembly?
UV-cure epoxy is an adhesive that cures (hardens) when exposed to ultraviolet (UV) light. It is commonly used for various industries’ bonding, sealing, and coating applications. Several factors must be considered when considering its use in medical device assembly to ensure safety and regulatory compliance.
Here are some considerations for using UV-cure epoxy in medical device assembly:
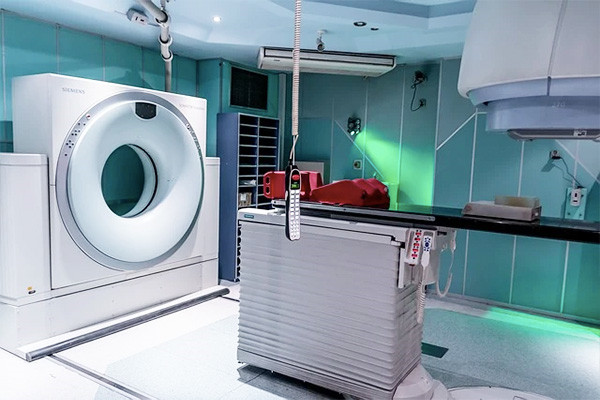
- Biocompatibility:Medical devices that come into contact with the human body must be biocompatible. Ensure the UV-cure epoxy used is biocompatible and complies with relevant standards and regulations, such as ISO 10993.
- Sterilization:Many medical devices need to be sterilized before use. Check if the UV-cure epoxy can withstand standard sterilization methods, such as autoclaving, ethylene oxide (EtO) sterilization, or gamma irradiation.
- Regulatory Compliance:Medical devices are subject to strict regulatory requirements. Ensure that the UV-cure epoxy complies with the regulations of the region where the medical device will be sold. For example, the FDA (Food and Drug Administration) regulates medical devices in the United States.
- Curing Depth and Speed:Consider the curing depth and speed of the UV-cure epoxy. Ensure that it can penetrate and heal effectively in areas where access may be limited and that the curing time is compatible with the assembly process.
- Chemical Resistance:Evaluate the chemical resistance of the cured epoxy to ensure it can withstand exposure to bodily fluids, cleaning agents, and other substances it may encounter during the life cycle of the medical device.
- Adhesion Properties:Confirm that the UV-cure epoxy provides the necessary adhesion strength for the specific materials being bonded in the medical device assembly.
- Temperature Resistance:Consider the operating temperature range of the medical device and ensure that the cured epoxy can withstand those temperatures without degrading.
- Testing and Validation:Perform testing and validation procedures to ensure the reliability and performance of the UV-cure epoxy in the intended medical device application.
Always consult with regulatory experts and follow industry standards and guidelines when selecting and using materials, such as UV-cure epoxy, in medical device manufacturing. It’s essential to work closely with regulatory authorities to ensure compliance with applicable regulations and standards.
Are there color options for UV-cure epoxy adhesives?
Yes, UV-cure epoxy adhesives are available in a variety of color options. The color of the adhesive can serve both functional and aesthetic purposes. Some standard color options include:
- Clear/Transparent:Clear UV-cure epoxy is often used when the appearance of the bond line or the materials being joined needs to be maintained without any color distortion.
- White:White UV-cure epoxy is proper when a lighter color is desired for aesthetic reasons or when bonding light-colored materials.
- Black:Black UV-cure epoxy is employed when a dark color is required or when bonding materials with dark surfaces. It can also be used for optical applications to reduce light transmission.
- Colored Variants:UV-cure epoxy adhesives may come in various color options, such as red, blue, green, etc. These colored adhesives can be chosen based on visibility needs or to provide a visual indicator of the adhesive presence.
- Tinted:Tinted UV-cure epoxies offer a subtle coloring that can enhance the appearance of the bond line without entirely obscuring the underlying materials.
The choice of color depends on the specific requirements of the application. In some cases, the color may be selected for functional reasons, such as matching the color of the bonded materials or providing contrast for visual inspection. In other cases, the color may be chosen for aesthetic purposes.
When selecting a colored UV-cure epoxy, it’s essential to consider factors such as bonded materials, curing properties, and specific application requirements. Additionally, for applications where the bond line’s appearance is critical, clear or transparent UV-cure epoxy may be preferred to maintain optical clarity.
How does UV cure epoxy perform in high-stress applications?
UV-curable epoxy is an adhesive that cures when exposed to ultraviolet (UV) light. Its performance in high-stress applications depends on various factors, including the specific formulation of the epoxy, the curing process, and the application requirements. Here are some considerations:
- Curing Process:UV-curable epoxy typically cures rapidly when exposed to UV light. The curing time is relatively short, which can be advantageous in specific applications. However, the speed of the curing process may affect the depth of cure and the overall bond strength.
- Bond Strength:The bond strength of UV-curable epoxy can be excellent, but it may only sometimes be as high as some other types of epoxies that cure through different mechanisms. The strength of the bond can be influenced by factors such as the substrate material, surface preparation, and the specific formulation of the epoxy.
- Material Compatibility:UV-curable epoxies may not be suitable for all materials. It’s essential to consider the compatibility of the epoxy with the materials being bonded. In high-stress applications, the ability of the epoxy to adhere well to different substrates is crucial for long-term performance.
- Temperature and Chemical Resistance:The performance of UV-curable epoxy in high-stress applications may be influenced by temperature and exposure to chemicals. Some UV-curable epoxies may have a different level of resistance to extreme temperatures or harsh chemicals than other epoxy formulations.
- Flexibility and Toughness:Depending on the specific formulation, UV-curable epoxy may exhibit different levels of flexibility and toughness. A more flexible and rigid epoxy may be desirable in high-stress applications with movement or impact.
- Quality of UV Light Source:The quality and intensity of the UV light source used for curing can impact the final properties of the cured epoxy. Insufficient or uneven exposure to UV light may lead to incomplete curing and compromise the performance of the epoxy.
Before using UV-curable epoxy in high-stress applications, it’s advisable to consult with the epoxy manufacturer and conduct thorough testing to ensure that the specific product meets the requirements of the intended application. Additionally, considering the environmental conditions, substrate materials, and any specific standards or regulations applicable to the application is crucial for successful and reliable performance.
Can UV-cure epoxy be applied in thin layers?
Yes, UV-cure epoxy is often designed to be applied in thin layers. UV-curing epoxy consists of a liquid resin and a hardening agent that reacts and solidifies when exposed to ultraviolet (UV) light. The UV light initiates the curing process, and it happens relatively quickly.
Applying UV-cure epoxy in thin layers has several advantages:
- Faster Curing:Thin layers allow quicker and more efficient curing since the UV light can penetrate through the epoxy more easily.
- Uniform Cure:Thinner layers promote a more even distribution of UV light, ensuring that the entire layer cures uniformly without incomplete or uneven curing issues.
- Reduced Heat Buildup:Thinner layers generate less heat during the curing process. Excessive heat can sometimes be an issue in thicker applications, potentially leading to problems like warping or cracking.
- Greater Precision:Thin layers provide better control and precision, making achieving the desired thickness easier and avoiding over-application.
When working with UV-cure epoxy, following the manufacturer’s instructions regarding the recommended thickness for each layer is essential. Exceeding the recommended thickness may result in incomplete curing and a tacky or soft finish. Additionally, proper surface preparation, cleanliness, and appropriate curing conditions (such as the correct wavelength and intensity of UV light) are crucial for successfully applying and curing UV-cure epoxy.
Are there limitations to UV-cure epoxy bonding thickness?
Yes, there are limitations to the thickness of UV-cure epoxy bonding. UV-cure epoxy adhesives rely on ultraviolet (UV) light to initiate the curing process. The curing reaction occurs when the adhesive is exposed to UV light, forming strong bonds.
The primary limitation associated with UV-cure epoxy bonding thickness is related to the penetration of UV light into the adhesive. UV light has a limited ability to penetrate through materials. As the thickness of the adhesive layer increases, the power of the UV light to reach the entire depth of the adhesive decreases.
Typically, UV-cure epoxy adhesives are suitable for bonding applications with thicknesses ranging from a few micrometers to millimeters. The exact thickness limitation can depend on various factors, including the specific formulation of the epoxy, the intensity of the UV light source, and the curing conditions.
If the adhesive layer is too thick, the UV light may not penetrate all the way through, leading to incomplete curing and weaker bonds. In such cases, it’s essential to consider alternative bonding methods for thicker applications or UV-cure adhesives in conjunction with other curing methods, such as heat curing.
It’s advisable to consult the manufacturer’s guidelines and technical data sheets for specific UV-cure epoxy products, as they often provide information on the recommended maximum thickness for adequate curing. Additionally, conducting trials and testing under the intended application conditions can help determine the suitability of UV-cure epoxy for a particular bonding thickness.
What surface preparation is needed for UV-cure epoxy adhesives?
When using UV-cure epoxy adhesives, surface preparation is crucial for achieving solid and durable bonds. Proper surface preparation helps ensure good wetting, adhesion, and bonding performance. Here are some general steps for surface preparation when using UV-cure epoxy adhesives:
Clean the Surfaces:
- Remove contaminants from the bonding surfaces, such as grease, oil, dust, or dirt. Use a suitable cleaning solvent or detergent.
- For some substrates, alcohol wipes or acetone can effectively remove contaminants.
Mechanical Abrasion:
- In some cases, especially when dealing with smooth or non-porous surfaces, it’s beneficial to rub them to improve adhesion mechanically.
- Abrasion methods can include sanding, scuffing, or using abrasive pads. The goal is to create a slightly roughened surface for better adhesion.
Surface Activation:
- Some materials may benefit from surface activation to enhance adhesion. This can be achieved through methods like plasma treatment or corona treatment.
- Plasma treatment can introduce functional groups on the surface, improving the bonding properties of specific substrates.
Substrate Compatibility:
- Ensure that the substrate materials are compatible with the UV-cure epoxy adhesive. Some substrates may require specific primers or surface treatments for optimal bonding.
Moisture Control:
- UV-cure epoxy adhesives are often sensitive to moisture. Ensure that the bonding surfaces are dry and free from moisture.
- It may be necessary to use a drying step or employ moisture-resistant formulations in humid environments.
Masking:
- Use masking materials to protect areas where adhesive bonding is not desired. This is particularly important when dealing with complex assemblies or when precise application is required.
Optical Transparency:
- UV light needs to penetrate through the adhesive to initiate the curing process. Ensure the substrates are transparent to UV light, or modify the adhesive application for proper curing.
Always refer to the manufacturer’s guidelines and technical data sheets for specific UV-cure epoxy products, as they provide detailed information on the recommended surface preparation methods for optimal performance. Additionally, conducting preliminary tests on representative samples is advisable to ensure that the chosen surface preparation methods are suitable for the specific application.
Can UV-cure epoxy be removed or repositioned after curing?
UV-cure epoxy is known for its fast curing process, which occurs when exposed to ultraviolet (UV) light. Once the epoxy is fully cured, it forms a strong and durable bond, making it challenging to remove or reposition. However, there are a few methods you can try, but success may vary depending on the specific epoxy and surfaces involved:
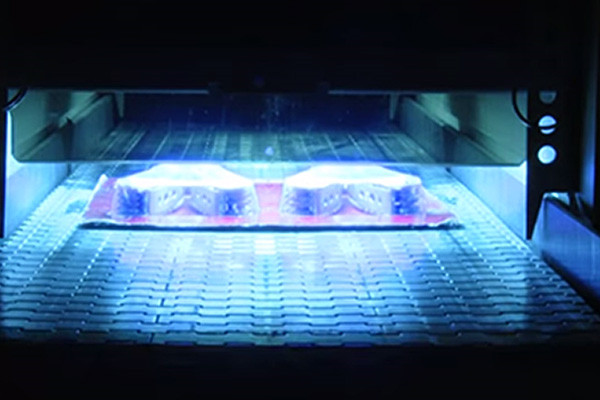
Heat:
- Some UV-cure epoxies can be softened with heat. You can try applying heat to the bonded area using a heat gun or a hairdryer. This can weaken the bond and make it easier to pry apart. Be cautious not to damage the surrounding materials.
Solvents:
- Certain solvents may be effective in breaking down cured epoxy. Acetone is a commonly used solvent for this purpose. However, keep in mind that acetone and other solvents may not work on all types of UV-cure epoxies, and they can also damage some materials. Test in an inconspicuous area first.
Mechanical Methods:
- Depending on the application and the materials involved, you may attempt to mechanically break or cut the cured epoxy. This can involve using tools like a chisel, knife, or razor blade. Exercise caution to avoid damaging the surfaces being separated.
Abrasion:
- Abrasive methods, such as sanding or grinding, might be considered to remove cured epoxy. This is a more aggressive approach and may damage the surfaces, so it should be used with care.
It’s important to note that attempting to remove cured epoxy can be challenging, and success may depend on various factors, including the specific epoxy formulation, the type of materials bonded, and the curing conditions. Always follow safety guidelines and recommendations provided by the epoxy manufacturer.
Before trying any of these methods, refer to the epoxy manufacturer’s instructions and safety data sheets (SDS) for guidance. Additionally, testing the chosen method in a small, inconspicuous area can help you assess its effectiveness without risking damage to the entire assembly.
Are there specific curing equipment requirements for UV cure epoxy?
UV-curable epoxy requires specific curing equipment to achieve proper and efficient curing. UV cure epoxy, also known as ultraviolet (UV) light-cured epoxy, cures when exposed to ultraviolet light. Here are some critical considerations for curing equipment:
UV Light Source:
- UV curing systems typically use high-intensity UV lamps or LED lights as the light source.
- The wavelength of the UV light should match the absorption spectrum of the photoinitiator in the epoxy formulation. Standard wavelengths are in the UVA (320-400 nm) and UVB (280-320 nm) ranges.
Intensity and Exposure Time:
- The curing equipment must provide the appropriate UV light intensity for the specific epoxy formulation.
- Exposure time depends on the light source’s intensity and the epoxy layer’s thickness.
Controlled Environment:
- UV curing is sensitive to environmental conditions. It’s essential to control factors such as temperature and humidity during the curing process to ensure consistent results.
Substrate Compatibility:
- Ensure that the substrate on which the epoxy is applied is transparent or translucent to the curing wavelength. Some materials may absorb or block UV light, hindering the curing process.
Uniformity of Cure:
- The UV light should be distributed evenly across the epoxy surface to achieve uniform curing. This is especially important for large or complex-shaped parts.
Safety Measures:
- UV light can be harmful to the eyes and skin. Curing equipment should include safety features such as shielding to prevent exposure to UV radiation.
Adherence to Manufacturer Guidelines:
- Follow the manufacturer’s recommendations and guidelines for the specific UV cure epoxy product. These guidelines may include information on the recommended UV light source, intensity, exposure time, and environmental conditions.
Monitoring and Quality Control:
- Consider incorporating monitoring systems to ensure the curing process is proceeding as expected. This may include sensors to measure UV intensity and systems to monitor temperature and humidity.
It’s important to note that different UV-cure epoxy formulations may have specific requirements, so it’s crucial to consult the product datasheet or contact the manufacturer for detailed information and recommendations.
What are common challenges when working with UV-cure epoxy adhesives?
Working with UV-cure epoxy adhesives presents particular challenges, and awareness can help overcome them effectively. Here are some common challenges associated with UV-cure epoxy adhesives:
Substrate Transparency:
- UV-cure epoxy adhesives require substrates that are transparent or translucent to UV light. Materials that are opaque or absorb UV light may hinder the curing process.
Shadowing Effects:
- In areas where the UV light cannot reach directly, such as in tight spaces or behind opaque structures, incomplete curing or shadowing effects may occur. Proper part design and fixture orientation can help mitigate this issue.
Surface Contamination:
- Contaminants on the substrate surface, such as dust, oils, or other residues, can interfere with the adhesion and curing. Thorough cleaning of surfaces before applying the adhesive is essential.
Inadequate UV Exposure:
- More UV exposure due to low light intensity or wrong curing time can result in incomplete curing and reduced bond strength. It’s crucial to ensure proper intensity and exposure duration based on the adhesive and application requirements.
Temperature and Humidity Sensitivity:
- UV curing can be sensitive to temperature and humidity. Variations in these conditions may affect the curing rate and final bond strength. Controlling the environment or adjusting the formulation for specific requirements may be necessary.
Thick Bond Lines:
- UV-cure adhesives may struggle to penetrate and cure in thick bond lines. For applications with significant adhesive thickness, it may be necessary to use adhesives formulated for deeper curing or consider alternative curing methods.
Post-Cure Shrinkage:
- Some UV-cure epoxies may exhibit post-cure shrinkage, which can affect the dimensional stability of bonded parts. Understanding the material properties and allowing for post-cure effects in the design phase is essential.
Photoinitiator Sensitivity:
- The photoinitiators in UV-cure adhesives may be sensitive to ambient light. It’s necessary to store and handle these adhesives in light-resistant containers to prevent premature curing.
Safety Concerns:
- UV light can be harmful to the eyes and skin. Adequate safety measures should be followed, such as wearing appropriate protective gear and implementing safety protocols.
Adhesive Selection:
- Selecting the suitable UV-cure epoxy adhesive for a specific application is crucial. Different formulations have varying properties, and understanding the application’s requirements is essential for success.
Addressing these challenges often involves proper process design, careful substrate preparation, adherence to manufacturer guidelines, and appropriate curing equipment. Consulting with the adhesive manufacturer and conducting thorough testing in the intended application conditions can help overcome these challenges.
Conclusion:
In conclusion, UV cure epoxy adhesive represents a groundbreaking advancement in bonding technology. Its rapid curing, robust strength, and versatility make it an ideal choice for various applications. Whether in manufacturing, electronics, or healthcare, exploring the answers to these questions will guide you in unlocking the full potential of UV cure epoxy adhesive, revolutionizing your bonding processes, and ensuring superior results. Embrace innovation and discover the transformative capabilities of UV cure epoxy adhesives for your projects.
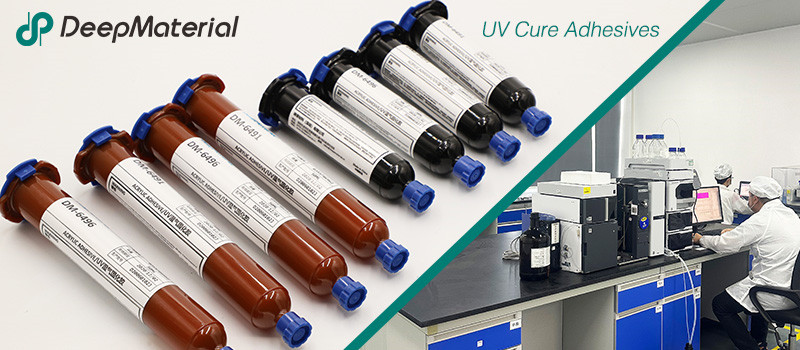
DeepMaterial
Based on the core technology of adhesives, DeepMaterial has developed adhesives for chip packaging and testing, circuit board level adhesives, and adhesives for electronic products. Based on adhesives, it has developed protective films, semiconductor fillers, and packaging materials for semiconductor wafer processing and chip packaging and testing. More…
UV Curing Adhesives
UV light cure have a number of benefits making them a popular choice among many product assembly and manufacturing applications. Many UV light cure adhesives can provide a nearly instantaneous bond to difficult substrates like glass and plastic. UV cure adhesives often require an accelerator or UV light for a bond to form.
Adhesive Blogs & News
The latest adhesive industry science and technology, Deepmaterial news, and market trends and forecasts.
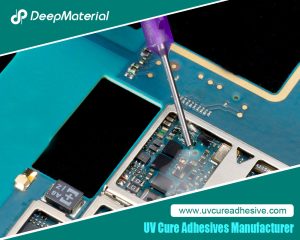
Electrical Potting Compound
Electrical Potting Compound In the vast field of modern electronic technology, Electrical Potting Compound plays a crucial role. It is like the invisible guardian inside electronic devices, providing reliable protection and stable performance support for various precise electronic components. Definition and Classification of Electrical Potting Compound Electrical Potting Compound is a special material
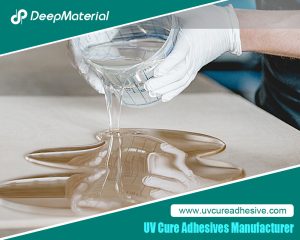
The Mystery and Application of Polyurethane Potting
The Mystery and Application of Polyurethane Potting In the modern industrial and technological fields, Polyurethane Potting is playing an increasingly important role. It not only provides reliable protection for various electronic devices and components but also shows unique advantages in optimizing performance and extending service life. What is Polyurethane Potting Polyurethane Potting is a
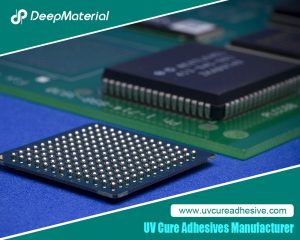
Waterproof Potting Compound: The Invisible Guardian of Electronic Devices
Waterproof Potting Compound: The Invisible Guardian of Electronic Devices In the era of rapid technological development today, electronic devices have become an indispensable part of our lives and work. From smart phones, tablets to smart home devices and industrial control systems, the application of electronic devices is everywhere. However, these devices often face the tests
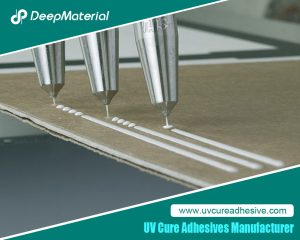
Potting Compound vs Epoxy: A Comparative Study and Application Overview
Potting Compound vs Epoxy: A Comparative Study and Application Overview In the modern industrial and electronic domains, the selection of materials holds a pivotal position in determining the performance, reliability, and longevity of products. Potting Compound and Epoxy are two frequently encountered materials that each demonstrate remarkable capabilities in numerous applications, yet they possess
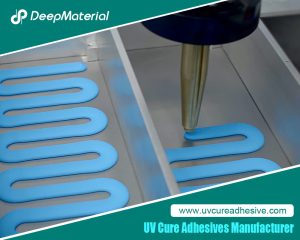
Exploring Potting Compound for Electronics: The Key Material for Providing Reliable Protection to Electronic Products
Exploring Potting Compound for Electronics: The Key Material for Providing Reliable Protection to Electronic Products In the current era of rapid technological development, electronic products have become an indispensable part of our lives. From smartphones, tablets to smart home devices and industrial control systems, the performance and reliability of electronic devices are crucial for
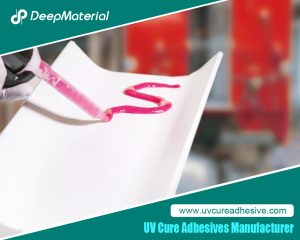
The Wonderful World of UV Curing Potting Compound
The Wonderful World of UV Curing Potting Compound In the rapid development of modern technology, various innovative materials continue to emerge, bringing unprecedented possibilities to applications in various fields. Among them, UV curing potting compound has become a shining star in the field of materials science with its unique performance and wide range of