- Home
- >
- Material Bonding
- >
- UV Cure Adhesive For Rubber
UV Cure Adhesive For Rubber
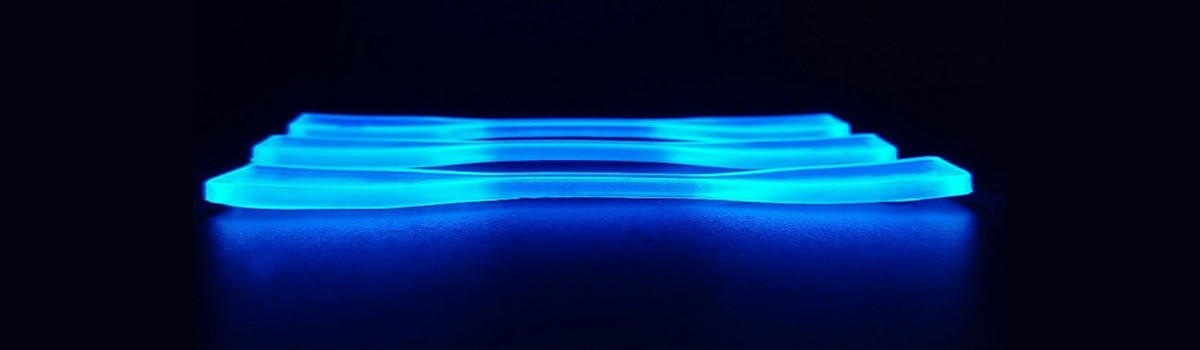
Table of Contents
ToggleWhat Constitutes UV Cure Adhesive Designed for Rubber?
UV-cure adhesives designed for rubber typically consist of a combination of various components to achieve the desired properties. These adhesives are formulated to cure rapidly when exposed to ultraviolet (UV) light. Here are some common constituents of UV-cure adhesives designed for rubber: Monomers and Oligomers:- Monomers:These are the building blocks of the adhesive. They undergo polymerization during the curing process. Common monomers for UV-cure adhesives include acrylates and methacrylates.
- Oligomers:These are short-chain polymers that improve the flexibility, adhesion, and overall performance of the adhesive.
- Photoinitiators are compounds that absorb UV light and initiate the curing reaction. They decompose upon exposure to UV light, releasing free radicals that initiate the polymerization of monomers and oligomers.
- Inhibitors may be added to control the curing rate and prevent premature curing of the adhesive before it is exposed to UV light.
- Stabilizers are included to prevent degradation of the adhesive during storage and use. They help maintain the adhesive’s performance over time.
- Various additives may be incorporated to enhance specific properties, such as flexibility, toughness, or adhesion to rubber surfaces.
- The adhesive formulation is tailored to be compatible with rubber substrates. This involves selecting monomers, oligomers, and additives that promote adhesion to rubber surfaces.
- UV light absorbers may be added to enhance the curing efficiency and depth of cure. These compounds help ensure that the adhesive cures completely, even in areas less exposed to UV light.
- Fillers like silica or other reinforcing agents may be included to modify the rheological properties and improve the mechanical strength of the adhesive.
How Does UV Cure Adhesive Work on Rubber Surfaces?
UV-cure adhesives cure (harden) when exposed to ultraviolet (UV) light. These adhesives are widely used in various industries due to their quick curing time, strong bond formation, and minimal environmental impact. The process of UV curing on rubber surfaces involves several key steps:- Formulation of UV-Cure Adhesive:UV-cure adhesives typically comprise oligomers, monomers, photoinitiators, and additives. Oligomers are pre-polymers with low molecular weight, while monomers are reactive molecules that can form polymer chains. Photoinitiators are compounds that initiate the polymerization process when exposed to UV light.
- Application on Rubber Surfaces:The UV-cure adhesive is applied to the rubber surfaces that need to be bonded. The adhesive is spread thin and even on the bonding surfaces.
- UV Light Exposure:The curing process begins when the UV-cure adhesive is exposed to UV light. The UV light activates the photoinitiators in the adhesive, causing them to undergo a chemical reaction. This reaction generates free radicals or other reactive species that initiate the polymerization of the oligomers and monomers in the adhesive.
- Polymerization:The activated oligomers and monomers start polymerizing, forming long molecular chains. This polymerization process is rapid and results in the formation of a three-dimensional network of interconnected polymer chains. This network structure is what gives the adhesive its strength and durability.
- Curing Time:UV-cure adhesives are known for quick curing times, often within seconds or minutes. This rapid curing is advantageous in industrial applications where fast assembly and processing are essential.
- Adhesion to Rubber:The adhesive forms a strong bond with the rubber surface during curing. The chemical compatibility of the adhesive formulation with rubber is crucial for achieving a durable and reliable bond.
- Benefits of UV Cure Adhesives on Rubber:
- Quick curing time: UV-cure adhesives offer fast assembly and processing.
- Minimal heat generation: UV curing is a low-temperature process, reducing the risk of heat damage to sensitive materials.
- Versatility: UV-cure adhesives can be formulated to bond various substrates, including rubber.
What Are the Different Formulations Available for UV Cure Adhesive?
UV-cure adhesives cure or harden when exposed to ultraviolet (UV) light. These adhesives are widely used in various industries due to their rapid curing, excellent bonding properties, and versatility. Several formulations are available for UV-cure adhesives, each designed for specific applications. Here are some standard formulations: Acrylated Urethanes (AU):- Description: Acrylated urethane formulations offer a balance of flexibility and durability. They are suitable for applications requiring a combination of strength and flexibility.
- Description: Acrylated epoxy formulations combine the toughness of epoxies with the fast-curing characteristics of acrylates. They are often chosen for applications that demand high chemical resistance and adhesion to various substrates.
- Description: Epoxy acrylates combine the properties of epoxy resins with the rapid curing capability of acrylates. They are known for their excellent adhesion to metals and other substrates.
- Description: While not strictly UV-cure adhesives, cyanoacrylates (known as superglues) can be formulated with photoinitiators to cure rapidly when exposed to UV light. They offer fast bonding for applications where quick assembly is crucial.
- Description: Silicone-based UV-cure adhesives are known for their flexibility, temperature resistance, and electrical insulation properties. They are often used in applications where these characteristics are essential.
- Description: Polyester acrylates are suitable for high-performance adhesives with good chemical resistance applications. They are often used in demanding environments.
- Description: Polyurethane acrylates offer a good balance between flexibility and strength. They are commonly used in applications where the adhesive needs to withstand dynamic stresses.
- Description: Methacrylate-based UV adhesives are versatile and offer high bond strength. They are often used in applications requiring rapid curing and good adhesion to various substrates.
- Description: Some UV-cure adhesives are designed to cure not only under UV light but also with the help of a secondary curing mechanism, such as heat or moisture. This dual-cure approach ensures complete curing in areas shadowed by UV light.
Which Industries Benefit Most from UV Cure Adhesive for Rubber?
UV-curable adhesives are versatile and find applications across various industries. However, using UV-cure adhesives for rubber bonding is particularly beneficial in industries where fast curing, precision bonding, and minimal heat generation are crucial. Here are some industries that benefit most from UV-cure adhesives for rubber: Electronics and Microelectronics:- UV-cure adhesives are commonly used to assemble electronic components, including bonding rubber seals, gaskets, and connectors.
- The quick curing time and precise bonding capabilities are advantageous in producing electronic devices and microelectronics.
- Medical devices often require bonding rubber components for sealing and insulation purposes.
- UV-cure adhesives are suitable for medical applications due to their rapid curing, minimal heat generation, and ability to bond materials without solvents.
- UV-cure adhesives are used in automotive manufacturing for bonding rubber components in interior and exterior applications.
- They are employed in assembling components like gaskets, seals, and trim pieces due to their fast curing and high bond strength.
- In producing optical and optoelectronic devices, UV-cure adhesives are used for bonding rubber components, such as lenses and seals.
- Curing quickly and creating optically clear bonds is crucial in this industry.
- The consumer electronics industry benefits from UV-cure adhesives for bonding rubber components in assembling gadgets, wearables, and other electronic devices.
- The quick curing time allows for efficient production processes.
- UV-cure adhesives find applications in the aerospace industry for bonding rubber components in aircraft, such as gaskets, seals, and vibration-dampening materials.
- The lightweight nature and fast curing properties are advantageous in aerospace applications.
- UV-curable adhesives are used in the packaging industry for bonding rubber components in labels, seals, and closures.
- The fast curing time contributes to increased production efficiency in packaging processes.
- UV-cure adhesives are utilized in various manufacturing processes where fast curing and precision bonding are critical, such as assembling industrial equipment and machinery.
Are UV Cure Adhesives Environmentally Friendly?
UV cure adhesives can be considered more environmentally friendly than traditional adhesives for several reasons. However, it’s important to note that the environmental impact of any material can depend on various factors, including its specific formulation, application, and disposal. Here are some factors to consider regarding the environmental friendliness of UV cure adhesives: Low VOC Emissions:- Volatile Organic Compounds (VOCs) are chemicals that can evaporate into the air and contribute to air pollution. UV cure adhesives typically have low VOC emissions compared to solvent-based adhesives, which can improve indoor air quality and the environment.
- UV cure adhesives require ultraviolet (UV) light for the curing process. The energy consumption during curing is generally lower than the energy-intensive processes required for curing some thermosetting adhesives. This can contribute to lower overall environmental impact, especially if the UV source is energy-efficient.
- UV cure adhesives often have a fast curing time, leading to increased productivity and less waste during manufacturing. Shorter curing times can also reduce the need for large ovens or other equipment, contributing to a more efficient and environmentally friendly process.
- UV cure adhesives are typically solvent-free. Solvents used in some traditional adhesives can have adverse environmental and health effects. The absence of solvents in UV cure adhesives reduces the risk of harmful emissions.
- Some traditional adhesives require high temperatures for curing, which can contribute to energy consumption and emissions. UV cure adhesives cure at lower temperatures, saving energy and reducing the environmental impact.
- UV cure adhesives are often single-component systems that do not require mixing before application. This can reduce the chances of errors and waste in the mixing process.
What Makes UV Cure Adhesive a Faster Bonding Solution Compared to Traditional Adhesives?
UV cure adhesives offer a faster bonding solution compared to traditional adhesives for several reasons:
*Rapid Curing Process:UV cure adhesives cure quickly when exposed to ultraviolet (UV) light. Curing takes only seconds to minutes, allowing for faster assembly and production processes. In contrast, traditional adhesives often require longer curing times, sometimes hours or even days.
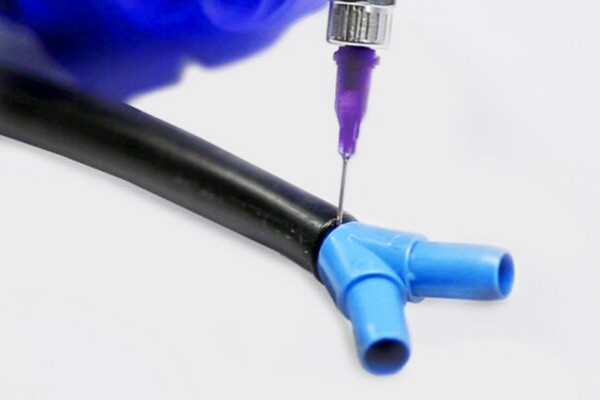
*Instantaneous Bonding:The adhesive matures instantly as soon as the UV light is applied. This enables immediate handling of the bonded components without waiting for the adhesive to set. Traditional adhesives may require clamping or other methods to hold the parts together during the extended curing period.
*Energy Efficiency:UV cure adhesives do not rely on heat or prolonged exposure to air for curing. The curing reaction is triggered by UV light, which makes the process more energy-efficient compared to traditional adhesives that may need elevated temperatures or extended open-air exposure.
*Consistent and Controlled Process:UV cure adhesives provide a more controlled and predictable curing process. The UV light can be precisely applied, ensuring consistent and uniform curing across the bonded area. In contrast, traditional adhesives may be more susceptible to variations in environmental conditions.
*Reduced Work-in-Progress Time:The fast curing time of UV cure adhesives reduces the work-in-progress time, allowing for a more efficient production flow. Manufacturers can achieve higher throughput and quicker turnaround times, increasing productivity.
*Lower VOC Emissions:UV cure adhesives often have softer volatile organic compound (VOC) emissions than traditional solvent-based adhesives. This can be beneficial in terms of environmental and occupational health considerations.
*Improved Quality Control:The rapid curing of UV adhesives allows for real-time quality control. Manufacturers can quickly assess the bond strength and integrity of the adhesive joint immediately after curing, facilitating timely adjustments or corrections if needed.
*Versatility:UV cure adhesives are suitable for bonding many substrates, including plastics, glass, metals, and composites. This versatility makes them applicable in various industries, from electronics to medical devices.
While UV cure adhesives offer many advantages, it’s important to note that they may not be suitable for all applications. Factors such as substrate compatibility, adhesive properties, and the specific requirements of the bonding application should be considered when choosing between UV cure adhesives and traditional adhesives.
Can UV Cure Adhesive Withstand Extreme Temperatures?
The temperature resistance of UV cure adhesives depends on the specific formulation of the adhesive. UV cure adhesives are generally known for their excellent temperature resistance, but their performance at extreme temperatures can vary.
UV cure adhesives are typically designed to withstand a wide range of temperatures, including both high and low extremes. However, it’s essential to check the manufacturer’s product specifications and technical data sheet for precise information on the temperature resistance of a particular UV cure adhesive.
Factors that can influence the temperature resistance of UV cure adhesives include:
- Chemical Composition:The specific chemicals and polymers used in the formulation of the adhesive play a significant role in determining its temperature resistance.
- Curing Process:The effectiveness of the curing process, which is initiated by exposure to ultraviolet (UV) light, can impact the final properties of the adhesive. Proper curing is crucial for achieving the desired temperature resistance.
- Application Environment:The intended application environment and the specific conditions the adhesive will be exposed to, such as continuous high temperatures or rapid temperature changes, can affect its performance.
- Manufacturer’s Recommendations:Always follow the manufacturer’s guidelines and recommendations for the proper use and temperature limits of the UV cure adhesive.
UV cure adhesives can have good temperature resistance, but it’s essential to select an adhesive that meets the specific requirements of your application. Consult the adhesive manufacturer for detailed information on temperature resistance and other relevant properties. If extreme temperatures are critical to your application, consider specialty adhesives designed for high-temperature environments.
Are There Any Limitations or Considerations When Using UV Cure Adhesive on Rubber?
UV cure adhesives are versatile and widely used in various industries for bonding applications. However, when using UV cure adhesives on rubber, there are some limitations and considerations to keep in mind:
Substrate Compatibility:
- Not all types of rubber are suitable for UV cure adhesives. Certain rubber compounds may not provide the necessary adhesion for the adhesive to bond effectively.
Surface Preparation:
- The surface of the rubber should be clean and free from contaminants, oils, or any substances that might inhibit bonding. Proper surface preparation is crucial for achieving strong and durable bonds.
Adhesive Selection:
- Choose a UV cure adhesive that is specifically formulated for bonding rubber. Adhesives vary in their formulations, and some may be more suitable for rubber than others.
Flexibility and Elongation:
- Consider the flexibility and elongation properties of the cured adhesive. Rubber is known for its elasticity, and the adhesive should be able to accommodate the movements and deformations of the rubber without losing adhesion.
UV Exposure:
- Ensure that the adhesive receives sufficient UV light for proper curing. Shadows or areas shielded from UV light may not cure completely, leading to weaker bonds.
UV Penetration:
- UV light may not penetrate thick or opaque rubber materials effectively. For thicker rubber parts, consider using adhesives that are designed to cure in shadowed areas or those that cure with visible light.
Temperature Sensitivity:
- Some UV cure adhesives may be sensitive to temperature variations during the curing process. Check the recommended curing conditions and ensure they are compatible with the temperature conditions of the application.
Chemical Resistance:
- Consider the chemical resistance of the cured adhesive, especially if the bonded rubber part will be exposed to chemicals, oils, or other harsh substances.
Testing and Compatibility:
- Conduct thorough testing to ensure that the UV cure adhesive provides the required bond strength and durability for the specific rubber material in your application.
Regulatory Compliance:
- Check if the UV cure adhesive complies with any industry standards or regulations that may apply to your application.
Always refer to the manufacturer’s guidelines and technical data sheets for both the rubber substrate and the UV cure adhesive to ensure proper compatibility and performance. Additionally, conducting small-scale tests or consulting with adhesive specialists can help address specific challenges related to bonding rubber with UV cure adhesives in your particular application.
What Types of Rubber Materials Can UV Cure Adhesive Bond Effectively?
UV-cure adhesives are commonly used in various industries for bonding applications due to their fast curing times and excellent bonding properties. However, the effectiveness of UV-cure adhesives can be influenced by the specific type of rubber materials involved. Here are some general considerations for bonding different kinds of rubber with UV-cure adhesives:
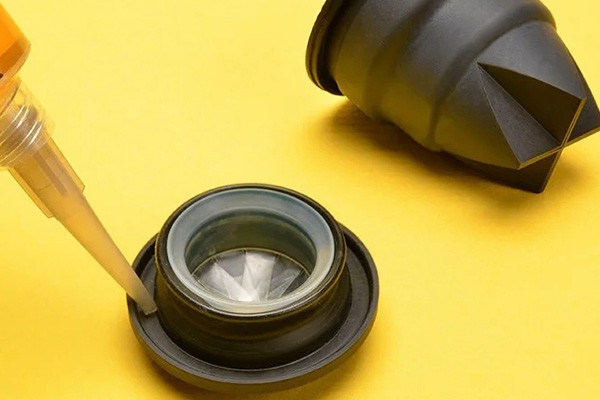
Ethylene Propylene Diene Monomer (EPDM):
- EPDM rubber is generally suitable for bonding with UV-cure adhesives, but surface preparation may be crucial for optimal adhesion. Cleaning the surface and ensuring it is contaminant-free can improve bond strength.
Nitrile Rubber (NBR):
- Nitrile rubber is often used in applications where oil resistance is required. UV-cure adhesives can bond effectively to NBR, but proper surface preparation is essential for good adhesion.
Silicone Rubber:
- Due to its low surface energy and inherent release properties, silicone rubber can be challenging to bond. Some UV-cure adhesives are formulated specifically for bonding silicone, and surface treatments may be necessary for optimal results.
Natural Rubber:
- Natural rubber can generally be bonded effectively with UV-cure adhesives. Surface preparation is essential, and the adhesive selection should consider the specific properties of the natural rubber.
Fluoroelastomers (Viton):
- Fluoroelastomers, such as Viton, are highly resistant to heat and chemicals. UV-cure adhesives may bond well to these materials, but surface preparation is crucial for a strong bond.
Butyl Rubber:
- Butyl rubber is known for its resistance to gases and moisture. UV-cure adhesives can effectively bond butyl rubber, and proper surface preparation is essential.
Neoprene Rubber:
- Neoprene rubber is often used in various applications. UV-cure adhesives can bond effectively to neoprene; surface cleaning is essential for optimal adhesion.
It’s important to note that surface preparation plays a critical role in the success of UV-cure adhesive bonding. Surfaces should be clean and free from contaminants and may require pre-treatment or priming to enhance adhesion.
Additionally, the specific formulation of the UV-cure adhesive matters and some adhesives may be designed for better compatibility with certain rubber materials. Always refer to the adhesive manufacturer’s guidelines and conduct compatibility testing before large-scale application.
How Does UV Cure Adhesive Enhance Productivity in Manufacturing Processes?
UV (ultraviolet) cure adhesives offer several advantages in manufacturing processes, contributing to enhanced productivity. Here are some key ways in which UV cure adhesives can improve efficiency in manufacturing:
Rapid Cure Time:
- UV cure adhesives cure almost instantly when exposed to ultraviolet light. This rapid cure time accelerates the bonding process, allowing for faster production cycles than traditional adhesives that may require longer curing times.
Reduced Processing Time:
- The quick-curing nature of UV adhesives reduces overall processing time. Manufacturers can move materials through the production line more rapidly, increasing throughput and efficiency.
Energy Efficiency:
- UV cure adhesives use energy-efficient curing methods. Traditional adhesives may require heat or extended curing times, consuming more energy. UV curing requires less fuel, contributing to lower operational costs and a smaller environmental footprint.
Precision and Control:
- UV curing provides precise control over the curing process. Manufacturers can apply the adhesive exactly where needed and then cure it selectively using UV light. This precision helps in achieving consistent and high-quality bonds.
Reduced Work-in-Progress Inventory:
- Because UV cure adhesives cure rapidly, there is less need for extensive work-in-progress inventory. Manufacturers can move products through different stages of production more quickly, minimizing the need for storage space and improving overall production efficiency.
Improved Quality and Performance:
- UV-cure adhesives often result in more robust and more durable bonds. The controlled process helps avoid uneven curing and provides consistent and reliable adhesive performance. This can lead to a reduction in rework and rejects, contributing to higher overall product quality.
Automation Compatibility:
- UV curing is well-suited for automated manufacturing processes. Computerized systems can easily integrate UV light sources for precise and consistent curing. This compatibility with automation helps streamline production lines and reduces the need for manual intervention.
Versatility:
- UV cure adhesives are available in various formulations, making them suitable for bonding a wide range of materials, including plastics, glass, metals, and composites. This versatility allows manufacturers to use a single adhesive for multiple applications, simplifying inventory management and reducing the need for different adhesive types.
Cleaner and Safer:
- UV cure adhesives typically do not emit volatile organic compounds (VOCs) during curing. This makes them a cleaner and safer option for workers and the environment, aligning with modern sustainability and safety standards.
UV cure adhesives enhance productivity in manufacturing processes by offering rapid cure times, energy efficiency, precision, improved quality, automation compatibility, versatility, and a cleaner, safer working environment. These advantages collectively contribute to faster and more efficient production lines.
Are UV Cure Adhesives Resistant to Chemicals and Solvents?
UV-cure or ultraviolet-curing adhesives are generally resistant to a wide range of chemicals and solvents once fully cured. However, the specific resistance can depend on the adhesive formulation and the intended application.
Here are some general points to consider:
Cured State Resistance: Once UV-cure adhesives have undergone curing, they often exhibit good resistance to chemicals and solvents. The curing process creates a polymer network that enhances the adhesive’s durability and resistance.
Chemical Compatibility: It’s essential to check the chemical compatibility of a specific UV cure adhesive with the intended chemicals and solvents in your application. Different formulations may have varying degrees of resistance to other substances.
Application Environment: The performance of UV cure adhesives can be influenced by factors such as temperature, humidity, and exposure conditions. Make sure the adhesive is suitable for the environmental conditions it will encounter.
Testing: Before using UV cure adhesives in critical applications, it is advisable to conduct compatibility and resistance tests. Testing under conditions similar to the application environment will provide more accurate information about the adhesive’s performance.
Consulting Manufacturers: Always refer to the manufacturer’s technical data sheets and recommendations for specific information regarding chemical resistance. Manufacturers can provide valuable insights into the capabilities and limitations of their products.
While UV cure adhesives can offer excellent resistance to chemicals and solvents, choosing the suitable adhesive based on your specific needs and following proper application and curing procedures to ensure optimal performance is crucial.
What Safety Measures Should Be Considered When Applying UV Cure Adhesive for Rubber?
When applying UV cure adhesive to rubber, it’s essential to follow safety measures to ensure the well-being of individuals involved in the process and to achieve successful adhesive bonding. Here are some safety considerations:
Personal Protective Equipment (PPE):
- Wear appropriate PPE, including safety glasses or goggles, to protect your eyes from UV radiation.
- Use gloves to prevent skin contact with the adhesive.
Ventilation:
- Ensure proper ventilation in the working area to prevent the buildup of fumes or vapors.
- If working in an enclosed space, consider using local exhaust ventilation systems to remove airborne contaminants.
UV Protection:
- Protect the skin from direct exposure to UV light. Long-sleeved shirts and long pants can help cover exposed skin.
- Use UV-blocking barriers, such as curtains or shields, to prevent UV radiation from reaching unintended surfaces or individuals.
UV Light Source Safety:
- Follow the manufacturer’s guidelines for the UV light source, ensuring it is properly calibrated and in good working condition.
- Keep the UV light source away from direct contact with skin and eyes.
Training:
- Provide adequate training to personnel applying UV cure adhesive, emphasizing safety precautions and emergency procedures.
Emergency Procedures:
- Establish and communicate emergency procedures, including first aid measures in case of accidental exposure or contact with the adhesive.
Material Compatibility:
- Ensure that the UV cure adhesive is compatible with the bonded rubber material. Some adhesives may not adhere well to certain types of rubber.
Preparation and Cleanliness:
- To ensure optimal adhesion, prepare the surfaces to be connected by cleaning them.
- Keep the work area clean and debris-free, as contaminants can affect the adhesive bond.
Adhesive Handling:
- Follow the manufacturer’s recommendations for handling and applying the adhesive.
- Store the adhesive according to the specified conditions (temperature, humidity) to maintain effectiveness.
Eye and Hand Wash Stations:
- Have eye wash stations and emergency hand wash facilities readily available in case of accidental exposure.
Read Material Safety Data Sheet (MSDS):
- Familiarize yourself with the MSDS provided by the adhesive manufacturer. It contains essential information on the potential hazards, safe use, and emergency procedures.
Always consult the specific guidelines and recommendations the adhesive manufacturer provides, as different products may have unique requirements and safety considerations.
Are UV Cure Adhesives Suitable for Outdoor Applications?
UV cure adhesives are generally suitable for outdoor applications, but their performance can depend on several factors. UV cure adhesives cure or harden when exposed to ultraviolet (UV) light. They are commonly used in electronics, medical devices, and optics.
Here are some considerations when using UV cure adhesives for outdoor applications:
UV Stability:
- UV-cure adhesives may degrade when exposed to prolonged sunlight and weathering. Some formulations are more UV-resistant than others, so choosing a product specifically designed for outdoor use is essential.
Weather Resistance:
- Outdoor applications expose adhesives to weather conditions, including rain, temperature fluctuations, and humidity. Ensure that the chosen UV cure adhesive is resistant to these environmental factors.
Temperature Range:
- Check the temperature range within which the adhesive remains effective. Extreme temperatures can impact the adhesive’s performance, especially in outdoor environments.
Moisture Resistance:
- Moisture can affect the performance of some adhesives. Ensure that the chosen UV cure adhesive has good moisture resistance, especially if exposed to rain or high humidity.
Substrate Compatibility:
- Consider the types of materials the adhesive will bond. Some UV cure adhesives may not be suitable for specific substrates commonly found in outdoor applications. Please verify that the adhesive is compatible with the materials it will bond.
Application Process:
- The curing process of UV adhesives relies on exposure to UV light. Ensure that the application process is suitable for the specific outdoor conditions, and consider factors like the availability of UV light in shaded or covered areas.
Testing:
- Before full-scale implementation, it’s advisable to conduct thorough testing to ensure that the UV cure adhesive meets the specific requirements of your outdoor application. This may include accelerated aging tests to simulate long-term exposure to outdoor conditions.
Always consult the adhesive manufacturer for detailed information about the product’s suitability for outdoor use and follow their guidelines for proper application and curing. Remember that advancements in adhesive technology may lead to new formulations that offer improved performance in outdoor environments.
What Role Does Surface Preparation Play in Ensuring Effective Bonding with UV Cure Adhesive?
Surface preparation is crucial in ensuring adequate bonding when using UV-cure adhesives. Proper surface preparation helps maximize the adhesive’s performance by promoting adhesion and preventing bonding failures. Here are some key aspects of surface preparation for UV cure adhesives:
Cleanliness:
- The surfaces to be bonded must be thoroughly clean and free from contaminants such as dust, grease, oil, and other residues. Contaminants can interfere with the adhesive’s ability to bond to the substrate.
Surface Activation:
- Some substrates may require surface activation to enhance adhesion. Methods such as plasma treatment or corona treatment can modify the substrate’s surface energy, improving the adhesive’s wetting and bonding characteristics.
Surface Roughness:
- The roughness of the substrate’s surface can impact the bonding strength. Sometimes, a slightly roughened surface may enhance mechanical interlocking and improve adhesion. However, the optimal level of roughness depends on the specific adhesive and substrate.
Compatibility Testing:
- Before applying the UV cure adhesive to the entire surface, it’s advisable to perform compatibility testing on a small area. This helps ensure that the adhesive bonds well to the substrate without causing any adverse effects, such as discoloration or degradation.
Substrate Type:
- Different substrates may require specific surface preparation methods. For example, metals may benefit from cleaning and light abrasion, while plastics may need treatments like corona discharge.
UV Transmission:
- UV cure adhesives rely on exposure to ultraviolet light for curing. Ensure that the substrates allow sufficient UV transmission to the adhesive. Transparent or translucent substrates are generally more suitable for UV cure applications.
Adhesive Compatibility:
- Verify that the chosen UV cure adhesive is compatible with the specific substrate material. Some adhesives may have limitations based on the types of materials they can effectively bond.
Avoiding Surface Contamination After Cleaning:
- Cleaning and preparing the surfaces are essential to prevent re-contamination. Handle the prepared surfaces with clean gloves and avoid touching them with bare hands.
By paying careful attention to surface preparation, you can optimize the bonding performance of UV cure adhesives, leading to more robust and more durable bonds. Always follow the manufacturer’s recommendations for surface preparation, as these can vary depending on the specific adhesive formulation and the types of substrates involved.
Can UV Cure Adhesives Be Used for Medical or Food-Grade Rubber Applications?
UV-cure adhesives are commonly used in various applications due to their fast curing time, strong bonding properties, and versatility. However, specific considerations and regulations must be considered to ensure safety and compliance when it comes to medical or food-grade applications.
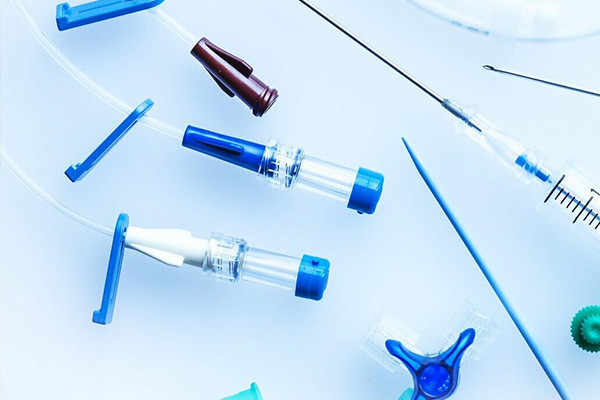
Medical Applications:
- The adhesive must comply with regulatory standards such as those set by the U.S. Food and Drug Administration (FDA) or the European Medicines Agency (EMA) for medical applications. The adhesive should be biocompatible and suitable for medical devices or equipment use.
- It is crucial to select UV-cure adhesives that are tested and approved for medical use. Some adhesives are designed to meet specific biocompatibility standards, such as ISO 10993.
- Always check with the adhesive manufacturer to confirm whether their product is suitable for medical applications and ensure that it has the necessary certifications.
Food-Grade Applications:
- In food-grade applications, adhesives must comply with regulations set by relevant authorities, such as the FDA in the United States or the European Food Safety Authority (EFSA) in Europe.
- The adhesive should not introduce harmful substances or contaminants into the food product. It should resist chemicals and cleaning agents commonly used in food processing environments.
- Manufacturers often produce adhesives specifically formulated for food contact. These adhesives may be labeled as “food-safe” or “FDA-compliant.” Always check for the appropriate certifications and documentation.
General Considerations:
- UV-cure adhesives should be chosen based on the application’s specific requirements, such as the type of rubber being bonded, the environmental conditions, and the expected load or stress on the bond.
- Ensure the adhesive is formulated to withstand the intended requirements, such as temperature extremes, moisture, and chemical exposure.
UV-cure adhesives can be used for medical or food-grade rubber applications. Still, selecting adhesives that meet the regulatory standards and requirements for these specific applications is crucial. Always consult the adhesive manufacturer and verify that the product has the necessary certifications and approvals for your intended use.
How Does UV Cure Adhesive Contribute to Reduced Environmental Impact in Manufacturing?
UV (ultraviolet) cure adhesives offer several advantages that can contribute to reduced environmental impact in manufacturing processes. Here are some ways in which UV cure adhesives contribute to environmental sustainability:
Energy Efficiency:
- UV cure adhesives typically require less energy than traditional adhesive curing methods. The rapid curing process occurs at room temperature, reducing the need for high temperatures and energy-intensive processes.
Reduced Emissions:
- UV cure adhesives often contain fewer volatile organic compounds (VOCs) than solvent-based adhesives. VOCs can contribute to air pollution and have adverse effects on human health. By minimizing VOC emissions, UV cure adhesives help improve air quality and reduce the environmental impact.
Low Hazardous Materials:
- UV cure adhesives often contain fewer hazardous materials compared to some traditional adhesives. This can contribute to a safer working environment for manufacturing personnel and reduce the environmental impact of producing and disposing of hazardous substances.
Minimal Waste Generation:
- UV cure adhesives typically have a longer shelf life and do not require mixing before use. This can reduce the likelihood of unused adhesive going to waste, contributing to more efficient material usage and less overall waste generation.
Improved Process Control:
- UV curing is a highly controlled process. Manufacturers can precisely control the intensity and duration of UV exposure, ensuring that only the required amount of energy is used for curing. This level of control can lead to more efficient use of resources and materials.
Reduced Carbon Footprint:
- The energy efficiency and rapid curing of UV adhesives contribute to a reduced carbon footprint in manufacturing. The lower energy consumption and faster curing times result in less overall environmental impact than traditional adhesive curing methods.
Water-Based Formulations:
- Some UV cure adhesives are water-based, further reducing the environmental impact. Water-based formulations typically have lower levels of VOCs and are less harmful to both the environment and human health.
Lower Maintenance and Clean-Up Costs:
- UV cure adhesives require less maintenance and have simplified clean-up procedures than other adhesive systems. This can lead to cost savings and reduced environmental impact associated with the disposal of cleaning solvents and other maintenance-related materials.
Improved Productivity:
- The fast curing times of UV adhesives contribute to increased productivity in manufacturing processes. Speedier production cycles can lead to energy savings and resource efficiency.
UV cure adhesives contribute to reduced environmental impact in manufacturing through energy efficiency, reduced emissions, minimal waste generation, improved process control, and the use of formulations with lower hazardous materials. Adopting UV cure adhesives can align with sustainability goals and promote more eco-friendly manufacturing practices.
Are UV Cure Adhesives Customizable for Specific Industrial Requirements?
UV cure adhesives are formulated with various components, and manufacturers can tailor these formulations to achieve specific properties and performance characteristics based on the application’s needs. Some of the factors that can be customized include:
- Chemical Composition:The choice of monomers, oligomers, and photoinitiators can be adjusted to achieve desired adhesive properties such as flexibility, hardness, or chemical resistance.
- Viscosity:The viscosity of the adhesive can be modified to suit different application methods, such as dispensing, spraying, or coating.
- Curing Speed:The speed at which the adhesive cures under UV light can be adjusted. Faster curing times may be desirable for high-speed production processes, while slower curing may be necessary for applications that require repositioning or alignment.
- Adhesion Strength:The bonding strength of the adhesive can be customized for specific substrates or bonding requirements.
- Color:The color of the adhesive can be adjusted for aesthetic purposes or to match the appearance of the bonded materials.
- Temperature Resistance:UV cure adhesives can be formulated to withstand specific temperature ranges, making them suitable for applications in varying temperatures.
- Chemical Resistance:The resistance of the adhesive to various chemicals can be enhanced based on the application requirements.
- Flexibility and Toughness:The flexibility and toughness of the cured adhesive can be modified to suit the mechanical properties needed for a particular application.
Manufacturers often work closely with industrial customers to understand their needs and develop a customized UV cure adhesive solution. This collaboration can involve adjusting the formulation or even creating entirely new formulations to meet the unique requirements of a particular industry or application.
What Factors Influence the Curing Time of UV Cure Adhesive on Rubber?
Several factors can influence the curing time of UV cure adhesive on rubber. UV cure adhesives are polymerized and cured using ultraviolet (UV) light. Here are some key factors that can affect the curing time:
UV Light Intensity:
- The intensity of the UV light source is crucial for the curing process. Higher intensity typically results in faster curing. Ensure that the UV light source is powerful enough for efficient curing.
Wavelength of UV Light:
- Different UV cure adhesives have specific wavelength requirements for optimal curing. Ensure that the UV light source emits the appropriate wavelength for the adhesive.
Adhesive Thickness:
- The thickness of the adhesive layer can impact curing time. Thicker coatings may require more time for the UV light to penetrate and cure the adhesive completely.
Adhesive Composition:
- The formulation of the UV cure adhesive plays a significant role. Different adhesive formulations may have varying curing requirements. Check the manufacturer’s recommendations for the specific adhesive being used.
Rubber Type:
- The type of rubber being bonded can affect the curing time. Some rubbers may be more transparent to UV light, allowing for faster curing, while others may absorb more light, requiring longer curing times.
Temperature:
- Temperature can influence the adhesive’s viscosity and the curing reaction’s speed. Higher temperatures can generally accelerate the curing process, but extreme temperatures may affect the adhesive properties.
Surface Preparation:
- The condition of the rubber surface can impact curing. Clean, dry, and properly prepared surfaces often lead to more efficient curing.
UV Light Exposure Time:
- The duration of exposure to UV light is critical. Ensure that the adhesive receives adequate UV light for the recommended time to achieve proper curing.
Oxygen Inhibition:
- Some UV cure adhesives are sensitive to oxygen inhibition, which can occur at the adhesive-air interface. This may require longer curing times or inert atmospheres to minimize the impact of oxygen.
Curing Equipment:
- The type of curing equipment, such as UV lamps or LED sources, can affect curing efficiency. Ensure that the equipment is suitable for the specific adhesive and application.
Following the manufacturer’s recommendations and guidelines for the UV cure adhesive being used is essential, as variations can exist among different products. Conducting small-scale tests and optimizing the curing parameters based on the specific application and materials involved is often necessary to achieve the desired results.
Do UV Cure Adhesives Provide Transparent Bonds on Rubber Surfaces?
UV cure adhesives provide transparent bonds on various surfaces, including rubber. However, the transparency of the bond may depend on the specific type of UV cure adhesive used, the formulation, and the properties of the rubber substrate.
UV cure adhesives typically consist of monomers, oligomers, photoinitiators, and other additives. When exposed to ultraviolet (UV) light, the photoinitiators in the adhesive initiate a polymerization reaction, causing the adhesive to cure and form a strong bond.
Certain UV cure adhesives provide transparent bonds for rubber surfaces, especially those that are transparent or translucent. It’s important to note that the transparency of the bond may also be influenced by the thickness of the adhesive layer, the curing conditions, and the compatibility between the adhesive and the rubber substrate.
When using UV cure adhesives on rubber surfaces, consider the following factors:
- Adhesive Formulation:Choose a UV cure adhesive formulation designed for bonding rubber. Some adhesives are formulated to provide better adhesion to specific materials, including rubber.
- Surface Preparation:Ensure that the rubber surface is clean and free of contaminants, which can impact the adhesion of the adhesive. Surface treatment or priming may be necessary in some cases.
- Curing Conditions:Follow the recommended curing conditions provided by the adhesive manufacturer. Proper exposure to UV light is crucial for achieving optimal bond strength and transparency.
- Rubber Type:Different types of rubber have varying properties, and adhesives may behave differently depending on the specific type of rubber. Consider the compatibility between the adhesive and the rubber substrate.
It’s advisable to consult the technical data sheet and guidelines provided by the adhesive manufacturer for specific recommendations regarding the use of their product on rubber surfaces. Additionally, conducting small-scale tests or trials on representative samples can help ensure that the UV cure adhesive meets the transparency requirements for your application.
Are There Innovations or Emerging Technologies in the UV Cure Adhesive for Rubber Industry?
However, for the most up-to-date and specific information on innovations and emerging technologies in the UV cure adhesive for the rubber industry, it’s recommended to check the latest industry publications, scientific journals, and news sources.
As of 2023, some trends and developments in UV cure adhesives include:
Formulation Improvements:
- Researchers and manufacturers continue to improve UV cure adhesive formulations to enhance their performance, durability, and versatility.
Customization for Specific Applications:
- There is a growing trend towards developing UV cure adhesives tailored for specific applications, including rubber industry ones. Customized formulations can address the unique challenges of different substrates and environmental conditions.
Dual-Cure Systems:
- Some advancements involve integrating dual-cure systems and combining UV curing with other mechanisms, such as heat or moisture. This approach provides more flexibility in the curing process and expands the range of applications.
Low-VOC Formulations:
- Developing low volatile organic compound (VOC) UV cure adhesives aligns with the increasing demand for environmentally friendly and sustainable solutions.
Application-Specific Properties:
- Innovations focus on achieving specific properties in UV cure adhesives, such as flexibility, chemical resistance, and adhesion strength, to meet the requirements of different industries, including rubber.
LED UV Technology:
- Adopting light-emitting diode (LED) technology for UV curing is becoming more prevalent. LED UV systems offer energy efficiency, longer life, and better control over the curing process than traditional mercury vapor lamps.
To find the latest developments in UV cure adhesives for the rubber industry, consider checking industry conferences, research papers, and updates from leading adhesive manufacturers. Additionally, contacting industry experts or organizations involved in adhesive research can provide insights into the most recent innovations in this field.
Conclusion:
In conclusion, UV cure adhesive for rubber showcases a remarkable stride in adhesive technology, transforming how materials are bonded in diverse applications. As we navigate the various questions surrounding UV cure adhesive, it becomes evident that its adaptability, efficiency, and eco-friendly nature make it a frontrunner in the adhesive industry. Whether in manufacturing, automotive, or medical sectors, UV cure adhesive for rubber continues to play a pivotal role in enhancing productivity and ensuring robust, enduring bonds.
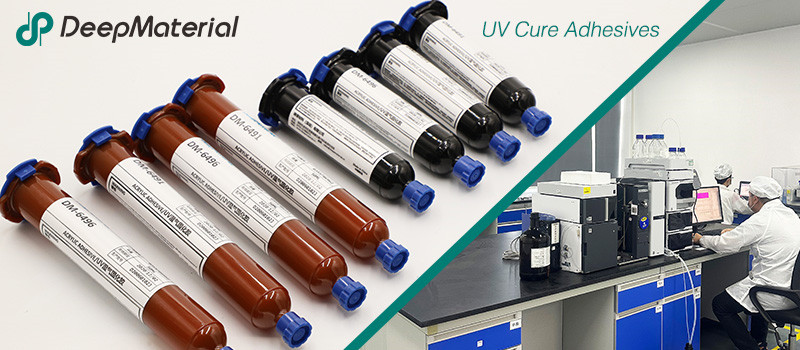
DeepMaterial
Based on the core technology of adhesives, DeepMaterial has developed adhesives for chip packaging and testing, circuit board level adhesives, and adhesives for electronic products. Based on adhesives, it has developed protective films, semiconductor fillers, and packaging materials for semiconductor wafer processing and chip packaging and testing. More…
UV Curing Adhesives
UV light cure have a number of benefits making them a popular choice among many product assembly and manufacturing applications. Many UV light cure adhesives can provide a nearly instantaneous bond to difficult substrates like glass and plastic. UV cure adhesives often require an accelerator or UV light for a bond to form.
Adhesive Blogs & News
The latest adhesive industry science and technology, Deepmaterial news, and market trends and forecasts.
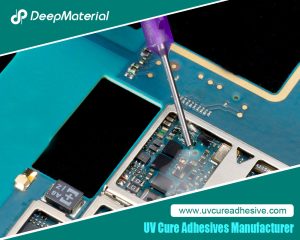
Biocompatibility of LED UV Glue Adhesive and Its Application Potential in Medical and Food Packaging Fields
Biocompatibility of LED UV Glue Adhesive and Its Application Potential in Medical and Food Packaging Fields LED UV glue adhesive has been widely applied in numerous fields due to its advantages such as rapid curing and easy operation. However, in fields with stringent safety requirements like medical and food packaging, its biocompatibility after curing becomes
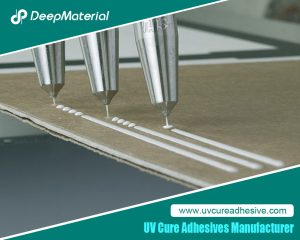
Biocompatibility of LED UV Glue Adhesive and Its Application Potential in Medical and Food Packaging Fields
Biocompatibility of LED UV Glue Adhesive and Its Application Potential in Medical and Food Packaging Fields LED UV glue adhesive has been widely applied in numerous fields due to its advantages such as rapid curing and easy operation. However, in fields with stringent safety requirements like medical and food packaging, its biocompatibility after curing
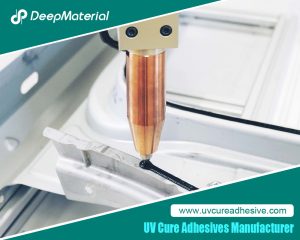
Exploring the Environmental Performance of UV Glue and Strategies for Optimizing Odor and VOC Content
Exploring the Environmental Performance of UV Glue and Strategies for Optimizing Odor and VOC Content UV glue, as an adhesive that achieves rapid curing through ultraviolet (UV) light irradiation, has been widely applied in numerous fields such as electronics, optics, healthcare, and automobiles, thanks to its advantages of fast curing speed, high bonding strength, and
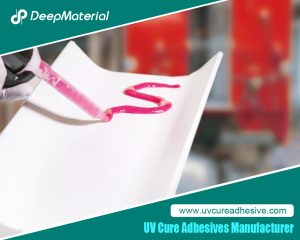
Compatibility Analysis and Countermeasures of LED UV Glue with Automated Production Equipment
Compatibility Analysis and Countermeasures of LED UV Glue with Automated Production Equipment LED UV glue has been widely used in modern manufacturing due to its advantages such as fast curing speed, high bonding strength, and environmental friendliness. However, in the automated production process, if there are problems with the adaptability between the glue and equipment
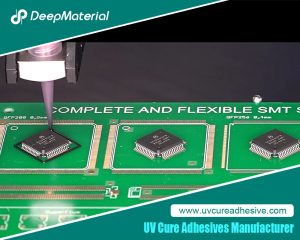
Influence of Viscosity and Thixotropy of Glue on the Quality of Glue Dots in the Dispensing Process and Solutions
Influence of Viscosity and Thixotropy of Glue on the Quality of Glue Dots in the Dispensing Process and Solutions The dispensing process is an important part of the application of LED UV glue adhesive, and the quality of this process directly affects the final performance of the product. The physical properties of the glue,
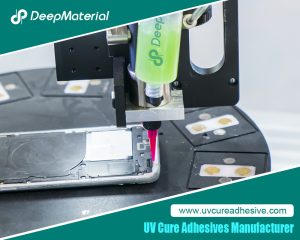
Aging Mechanism and Modification Strategies of LED UV Glue under Long-term Ultraviolet Irradiation
Aging Mechanism and Modification Strategies of LED UV Glue under Long-term Ultraviolet Irradiation LED UV glue, with its advantages of fast curing speed, high bonding strength, and environmental friendliness, has been widely used in fields such as optical device packaging, electronic assembly, and medical devices. However, in scenarios where it is exposed to ultraviolet environments