The Essential Guide to Mini Vibration Motor Bonding Adhesive
In the fast-paced electronics world, components’ reliability and performance are paramount. Among these components, mini vibration motors enhance user experience, particularly in mobile devices, wearables, and various consumer electronics. To ensure these motors function effectively, it is essential to bond them in place securely. It is where mini vibration motor bonding adhesive comes into play. This article delves into the various aspects of bonding adhesives used for mini vibration motors, exploring their types, applications, advantages, and selection considerations.
Understanding Mini Vibration Motors
What Are Mini Vibration Motors?
Mini vibration motors are small, compact devices that produce tactile feedback through vibration. Commonly found in:
- Smartphones
- Game controllers
- Wearable devices
- Robotics
These motors enhance user interaction by providing sensory feedback, making them essential in modern electronics.
Types of Mini Vibration Motors
Coin Vibration Motors:
- Circular in shape
- Compact and lightweight
- Widely used in mobile phones
Linear Vibration Motors:
- Produce linear motion
- Commonly used in applications requiring precise haptic feedback
Eccentric Rotating Mass (ERM) Motors:
- Utilize an unbalanced weight to generate vibrations
- Suitable for applications where strong vibrations are necessary
The Role of Bonding Adhesives
Importance of Bonding in Mini Vibration Motors
Bonding adhesives are critical for ensuring the longevity and effectiveness of mini vibration motors. They:
- Provide structural integrity
- Minimize vibration-related wear
- Enhance overall device performance
Characteristics of Effective Bonding Adhesives
When selecting a bonding adhesive for mini vibration motors, consider the following characteristics:
- Strength:The adhesive must provide a solid bond to withstand operational vibrations.
- Flexibility:Flexibility is crucial to accommodate movement and thermal expansion.
- Cure Time:Fast curing times are often preferred for efficient manufacturing processes.
- Temperature Resistance: The adhesive should withstand the device’s operating temperature range.
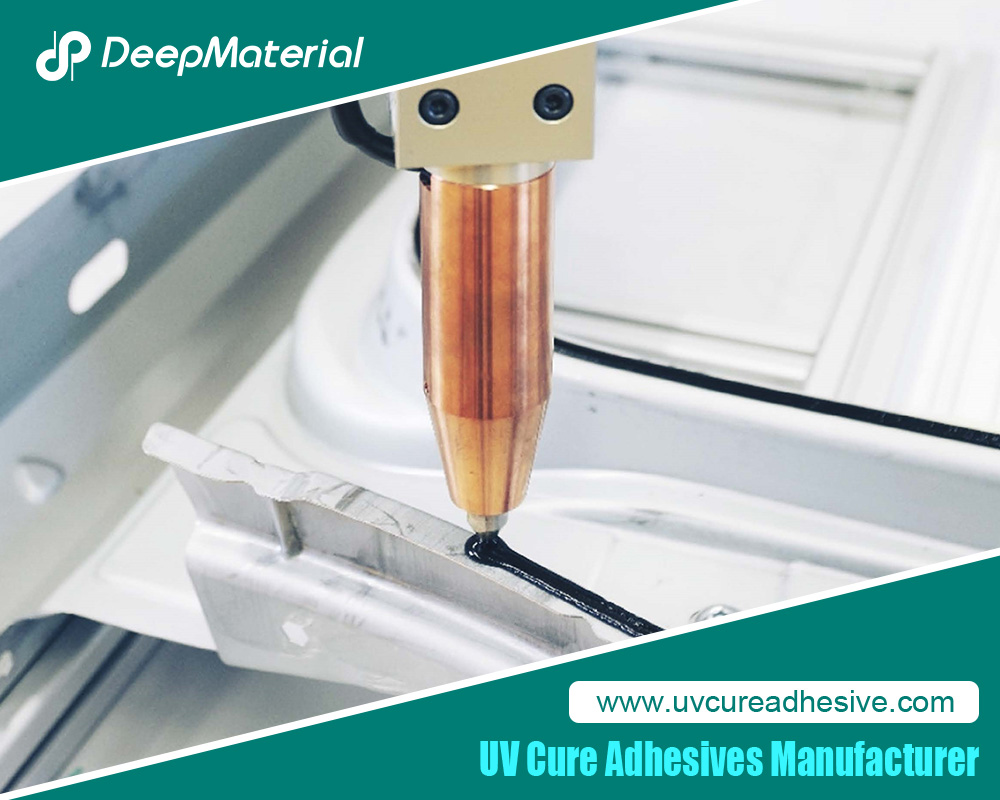
Types of Bonding Adhesives
1. Epoxy Adhesives
Advantages:
- Exceptional bond strength
- High resistance to chemicals and temperature
- Good for structural applications
Disadvantages:
- Longer curing time compared to other options
- A rigid bond may not be suitable for all applications
2. Silicone Adhesives
Advantages:
- Excellent flexibility
- Good temperature resistance
- Suitable for applications requiring movement
Disadvantages:
- Generally lower bond strength compared to epoxy
- It can be more expensive
3. Acrylic Adhesives
Advantages:
- Fast curing times
- Strong bond strength
- Good UV resistance
Disadvantages:
- It may not be as flexible as silicone
- Can be affected by certain chemicals
4. Polyurethane Adhesives
Advantages:
- Highly flexible and durable
- Excellent impact resistance
- Good adhesion to various substrates
Disadvantages:
- Longer curing time compared to acrylic
- Can be moisture-sensitive during the curing phase
Choosing the Right Bonding Adhesive
Factors to Consider
When selecting a bonding adhesive for mini vibration motors, consider the following:
- Application Requirements:Assess the specific needs of the device.
- Material Compatibility:Ensure the adhesive is compatible with the motor and the substrate.
- Environmental Conditions:Consider temperature fluctuations and exposure to chemicals.
- Manufacturing Process: Evaluate the efficiency of the adhesive application method.
Tips for Effective Bonding
- Surface Preparation:Clean and roughen surfaces to enhance adhesion.
- Correct Adhesive Application:Apply the right amount of adhesive; too much can lead to oozing, while too little can result in weak bonds.
- Curing Conditions:Follow manufacturer guidelines for curing times and conditions to ensure optimal performance.
Applications of Mini Vibration Motor Bonding Adhesive
- Consumer Electronics
- Bonding adhesives secure vibration motors in smartphones and tablets, ensuring they withstand daily use and provide reliable feedback.
- Automotive Industry
- Mini vibration motors alert drivers of critical information in advanced driver-assistance systems (ADAS). Reliable bonding is crucial for these applications.
- Wearable Technology
- Fitness trackers and smartwatches utilize mini vibration motors for notifications and alerts. Strong bonding adhesives help ensure the motors remain securely in place despite movement.
- Robotics
- In robotics, mini vibration motors enhance tactile feedback and interaction. Robust bonding solutions are essential for maintaining motor functionality.
Critical Considerations for Selecting Mini Vibration Motor Bonding Adhesive
When choosing the suitable bonding adhesive for mini vibration motors, several key factors must be taken into account to ensure optimal performance and reliability. Below are essential considerations to guide your selection process:
1. Application Environment
- Temperature Extremes:Determine the operating temperature range to choose an adhesive that can withstand fluctuations.
- Moisture Exposure:Assess if the application will be exposed to humidity or liquids, requiring moisture-resistant adhesives.
- Chemical Resistance:Consider potential exposure to chemicals that could degrade the adhesive over time.
2. Material Compatibility
- Substrate Material:Ensure the adhesive is compatible with the motor and the mounting surface, whether plastic, metal, or composite.
- Adhesive Type:Choose between epoxy, silicone, acrylic, or polyurethane based on how well they bond with the materials in your application.
3. Bonding Strength Requirements
- Load-Bearing Needs:Evaluate the stress and load the bond will experience during operation to select an adhesive with adequate strength.
- Vibration Resistance:Ensure the adhesive can withstand continuous vibrations without losing bond integrity.
4. Curing Time and Conditions
- Production Efficiency:Opt for adhesives with faster curing times if manufacturing speed is a priority.
- Cure Method:Check if the adhesive requires heat, UV light, or moisture for curing, and ensure compatibility with your production line.
5. Flexibility and Durability
- Flexibility:For applications involving movement, select adhesives that allow some flexibility to absorb shocks and prevent cracking.
- Longevity: Choose durable adhesives for long-term performance, particularly in high-wear applications.
6. Application Method
- Dispensing Ease: Consider how easily the adhesive can be applied, especially in automated or manual production processes.
- Viscosity:Higher-viscosity adhesives may be more challenging to apply but can provide better control, while lower-viscosity adhesives may flow better into tight spaces.
7. Cost-Effectiveness
- Budget Constraints:Balance performance requirements with cost to find a suitable adhesive that meets both quality and budget needs.
- Long-Term Savings:Consider the potential for reduced maintenance and replacement costs associated with high-quality adhesives.
Conclusion
The importance of mini vibration motor bonding adhesive cannot be overstated in today’s electronics landscape. From enhancing user experience to ensuring the longevity of devices, the suitable adhesive plays a critical role in the performance of mini vibration motors. By understanding the various types of adhesives available, their characteristics, and the considerations for selection, manufacturers can make informed choices that enhance product reliability and user satisfaction. As technology continues to evolve, so will the innovations in bonding adhesives, making them an essential component in the design and manufacturing of modern electronics.
For more about choosing a comprehensive guide to the essential guide to mini vibration motor bonding adhesive, you can pay a visit to DeepMaterial at https://www.uvcureadhesive.com/ for more info.