- Home
- >
- Application
- >
- Chip Manufacturing Process Adhesive
Chip Manufacturing Process Adhesive
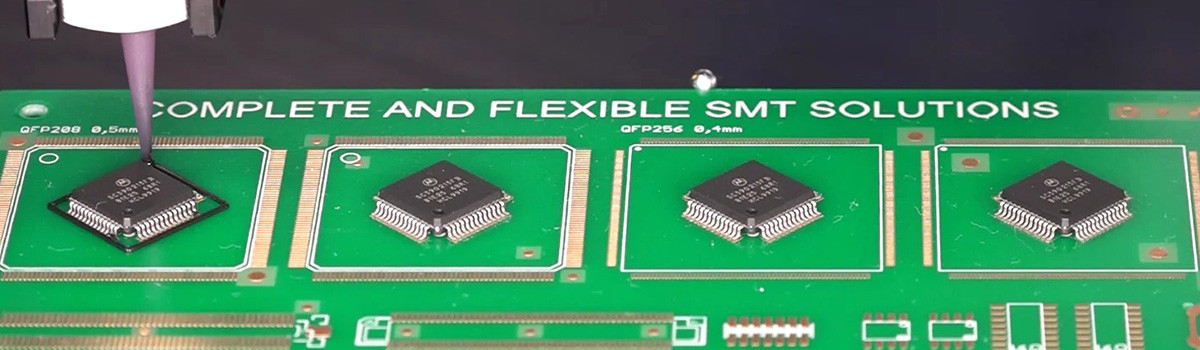
Chip Manufacturing Process Adhesive. In the ever-evolving world of technology, chip manufacturing plays a pivotal role in creating the powerful devices we rely on daily. The adhesive is a crucial component in this process, ensuring the integrity and efficiency of chip production. In this guide, we will explore various aspects of the chip manufacturing process adhesive, providing valuable insights into its importance, applications, and diverse questions surrounding this critical element.
Table of Contents
ToggleWhat is chip manufacturing process adhesive?
In chip manufacturing, adhesives play a crucial role in various stages of the semiconductor fabrication process. Adhesives bond different layers of materials together, provide structural support, and ensure the integrity of the final semiconductor device. The specific adhesive used can vary depending on the application and the bonded materials.
Here are some key points related to adhesives in the chip manufacturing process:
- Wafer Bonding:In some semiconductor processes, wafer bonding joins two semiconductor wafers together. Adhesives play a role in holding the wafers in place during bonding. This can enhance the mechanical strength and thermal conductivity of the final device.
- Die Attach:In assembling integrated circuits (ICs), die-attach involves bonding the semiconductor die (the actual chip) to its package or substrate. Adhesives are used in this process to secure the die and provide electrical and thermal conductivity.
- Encapsulation:After the semiconductor device is assembled, it is often encapsulated to protect it from environmental factors such as moisture, contaminants, and mechanical stress. Adhesives are used in this stage to seal and encapsulate the device.
- Underfill:In flip-chip packaging, where the semiconductor die is mounted upside down on the substrate, underfill adhesives fill the gap between the die and the substrate. This helps to improve the mechanical strength and thermal performance of the package.
- Thermal Interface Materials (TIMs):Adhesives with good thermal conductivity are often used as thermal interface materials. These materials help in efficient heat dissipation by improving the thermal contact between the semiconductor device and a heat sink.
The choice of adhesive depends on various factors, such as the materials being bonded, the thermal and mechanical requirements of the application, and the overall manufacturing process. Adhesives used in chip manufacturing must have specific properties to meet the demanding conditions of semiconductor devices. These properties may include high thermal conductivity, low outgassing, and compatibility with the materials involved in the semiconductor process.
How does adhesive contribute to the chip manufacturing process?
Adhesives play a crucial role in the chip manufacturing process, contributing to the assembly and performance of semiconductor devices in several ways. Here are some critical contributions of adhesives in chip manufacturing:
- Die Attach:Adhesives are used in the die attach process to bond the semiconductor die (the actual chip) to its substrate or package. This bonding is critical for ensuring a secure mechanical connection and providing electrical and thermal pathways between the die and the package. The adhesive helps create a strong and reliable bond, allowing for efficient heat transfer from the chip to the surrounding environment.
- Wafer Bonding:In some semiconductor processes, multiple wafers may be bonded together. During the bonding process, adhesives are used in wafer bonding to hold the wafers in place. This bonding can create structures with improved mechanical strength and thermal performance.
- Encapsulation:After the semiconductor device is assembled, it is often encapsulated to protect it from environmental factors such as moisture, dust, and mechanical stress. Adhesives are used in the encapsulation process to seal the device, providing a protective barrier and enhancing its durability.
- Underfill:In flip-chip packaging, where the semiconductor die is mounted upside down on the substrate, underfill adhesives fill the gap between the die and the substrate. This helps to reduce mechanical stress caused by differences in thermal expansion coefficients between the die and the substrate. Underfill adhesives also contribute to improved thermal conductivity, ensuring efficient heat dissipation.
- Thermal Interface Materials (TIMs):Adhesives are often used as thermal interface materials to improve the thermal conductivity between the semiconductor device and a heat sink. This is crucial for managing the heat generated during the operation of the chip. TIMs help dissipate heat efficiently, preventing overheating and maintaining the performance and reliability of the device.
- Alignment and Bonding in MEMS (Micro-Electro-Mechanical Systems):Adhesives are used in MEMS fabrication for bonding different components together, providing mechanical stability, and aligning structures during the manufacturing process.
Adhesives contribute to chip manufacturing by providing structural support, enabling efficient thermal management, ensuring reliable electrical connections, and protecting the semiconductor device from environmental factors. The specific type of adhesive and its properties are carefully selected based on the requirements of each stage in the manufacturing process.
What are the primary types of adhesives used in chip manufacturing?
Several types of adhesives are used in chip manufacturing, each serving specific purposes in different stages of the semiconductor fabrication process. The primary types of adhesives used in chip manufacturing include:
- Epoxy Resins:Epoxy adhesives are widely used for die attach and encapsulation in chip manufacturing. They provide excellent adhesion strength, chemical resistance, and thermal stability. Epoxy resins are often preferred for their mechanical strength and reliability in semiconductor packaging.
- Polyimides:Polyimide adhesives are known for their high-temperature resistance and excellent electrical insulation properties. They are commonly used in applications with extreme temperature conditions, such as wafer bonding and specific encapsulation processes.
- Acrylic Adhesives:Acrylic adhesives are used in chip manufacturing for die attach, substrate bonding, and encapsulation. They offer good adhesion properties, rapid curing times, and flexibility. Acrylic adhesives are suitable for applications that require a balance of mechanical strength and ease of processing.
- Silicone Adhesives:Silicone adhesives are chosen for their flexibility, high-temperature resistance, and electrical insulation properties. They are commonly used in encapsulation processes and as thermal interface materials (TIMs) for effective heat dissipation.
- Underfill Adhesives:Underfill adhesives are formulated to fill the gap between the semiconductor die and the substrate in flip-chip packaging. These adhesives reduce mechanical stress caused by thermal expansion differences and enhance the thermal and mechanical performance of the package. Epoxy-based underfill adhesives are frequently used in this application.
- Anisotropic Conductive Adhesives (ACAs):ACAs are used for bonding components in applications requiring electrical conductivity in specific directions. ACAs contain conductive particles that allow electrical connections in the desired directions while providing insulation in other directions. They are often used in microelectronics assembly, including chip-on-glass (COG) and chip-on-flex (COF) applications.
- Non-Conductive Pastes:Non-conductive pastes form conductive traces on semiconductor devices. They are applied before metallization processes to create patterns that define the electrical pathways on the chip.
- Thermal Interface Materials (TIMs):TIMs are adhesives specifically designed to improve the thermal conductivity between a semiconductor device and a heat sink. They help dissipate heat efficiently to prevent overheating and maintain optimal performance.
The choice of adhesive depends on the specific requirements of the chip manufacturing process, including mechanical strength, thermal conductivity, chemical resistance, and electrical properties. Adhesive selection is a critical aspect of semiconductor fabrication, and manufacturers carefully choose materials based on the intended application and performance criteria.
How does adhesive bonding impact the overall performance of semiconductor devices?
Adhesive bonding plays a crucial role in the overall performance of semiconductor devices, as it is used in various stages of semiconductor manufacturing and assembly processes. Here are some ways in which adhesive bonding impacts semiconductor devices:
- Die Attachment:Adhesive bonding is often used in the die attachment process, where the semiconductor chip (die) is bonded to a substrate or package. The quality of this bond is critical for the electrical and thermal performance of the device. A solid, reliable adhesive bond ensures good electrical connectivity and efficient heat dissipation.
- Package Sealing:Adhesives seal the semiconductor package, protecting the delicate electronic components from environmental factors such as moisture, dust, and contaminants. Proper sealing is essential for preventing performance degradation and ensuring the long-term reliability of the device.
- Wire Bonding:Adhesive materials are sometimes used in wire bonding, where thin wires connect the semiconductor die to the package or substrate. The adhesive helps secure the cables and provides mechanical stability to the bond. This is crucial for maintaining the integrity of the electrical connections.
- Encapsulation:In some cases, semiconductor devices are encapsulated in a protective material using adhesive bonding. This encapsulation helps protect the device from mechanical stress and environmental factors and enhances its durability. It also contributes to the overall robustness and reliability of the semiconductor device.
- Thermal Management:Adhesives with high thermal conductivity may enhance thermal management in semiconductor devices. Efficient heat dissipation is crucial for preventing overheating and maintaining the optimal performance of semiconductor components.
- Microelectromechanical Systems (MEMS):Adhesive bonding is commonly used to fabricate MEMS devices. MEMS devices often involve intricate structures and delicate components, and the choice of adhesive material and bonding process can impact their mechanical stability and overall performance.
- Wafer Bonding:In advanced semiconductor processes, wafer bonding integrates different materials and technologies. Adhesives create strong bonds between wafers, facilitating the fabrication of complex devices and structures.
It’s important to note that selecting the appropriate adhesive material and bonding process depends on the specific requirements of the semiconductor application. Factors such as thermal conductivity, mechanical strength, electrical properties, and reliability considerations all influence the choice of adhesives in semiconductor device manufacturing.
What challenges does chip manufacturing process adhesive address in the industry?
Adhesive materials play a crucial role in chip manufacturing processes, addressing various challenges in the semiconductor industry. Here are some key challenges that adhesive bonding helps address:
- Die Attachment and Bonding:Attaching the semiconductor die to a substrate or package is critical in chip manufacturing. Adhesives help create a strong and reliable bond, ensuring good electrical connectivity and heat dissipation. Challenges include achieving uniform and high bond strength, minimizing voids, and accommodating different materials and sizes of semiconductor components.
- Wire Bonding:Wire bonding connects the semiconductor die to the package or substrate. Adhesives are often involved in securing the thin wires in place. Challenges include ensuring proper alignment, bonding wire consistency, and device lifespan reliability.
- Package Sealing:Adhesive bonding is essential for sealing semiconductor packages to protect the internal components from moisture, contaminants, and other environmental factors. Challenges include achieving an airtight seal, preventing delamination, and addressing thermal cycling and mechanical stress issues.
- Thermal Management:Efficient heat dissipation is crucial for the performance and reliability of semiconductor devices. Adhesives with high thermal conductivity help transfer heat away from the semiconductor components. Challenges include selecting adhesives with optimal thermal properties, addressing thermal interface resistance, and managing thermal expansion mismatches.
- Encapsulation:Some semiconductor devices require encapsulation for protection against mechanical stress and environmental factors. Adhesives used in encapsulation must provide a solid protective barrier while maintaining the integrity of the internal components. Challenges include achieving proper adhesion, avoiding voids, and selecting materials compatible with the device’s requirements.
- MEMS Fabrication:In fabricating Microelectromechanical Systems (MEMS), adhesives are used in various processes. Challenges include achieving precise alignment, ensuring the structural integrity of delicate MEMS components, and addressing compatibility issues with different materials.
- Wafer Bonding:Wafer bonding is employed in advanced semiconductor processes for integrating different materials and technologies. Challenges include achieving defect-free bonds, ensuring uniformity across large wafer surfaces, and addressing issues related to thermal and mechanical stresses.
- Alignment and Precision:Many semiconductor manufacturing processes require precise alignment of components. Adhesives help in achieving accurate positioning and alignment during bonding processes. Challenges include addressing misalignment issues and ensuring high precision in the placement of parts.
- Material Compatibility:Semiconductor manufacturing involves various materials with different thermal, electrical, and mechanical properties. Adhesives must be selected based on compatibility with these materials to avoid delamination, material degradation, or mismatched thermal expansion coefficients.
- Reliability and Longevity:Semiconductor devices often have long lifespans, and adhesives must be chosen to ensure the reliability and longevity of the bonds. Challenges include addressing aging, thermal cycling, and environmental exposure that can affect the adhesive’s performance over time.
Addressing these challenges requires carefully selecting adhesive materials, optimizing bonding processes, and adhering to stringent quality control measures throughout the semiconductor manufacturing workflow. Continuous advancements in adhesive technology are essential to meet the evolving demands of the semiconductor industry.
Can you explain the adhesive’s role in bonding different semiconductor material layers?
Adhesive bonding is critical in bonding different semiconductor material layers, especially in fabricating complex semiconductor devices with multiple layers. The choice of adhesive and the bonding process are crucial to ensure robust, reliable, and durable bonds between different materials. Here’s how adhesives contribute to bonding various semiconductor material layers:
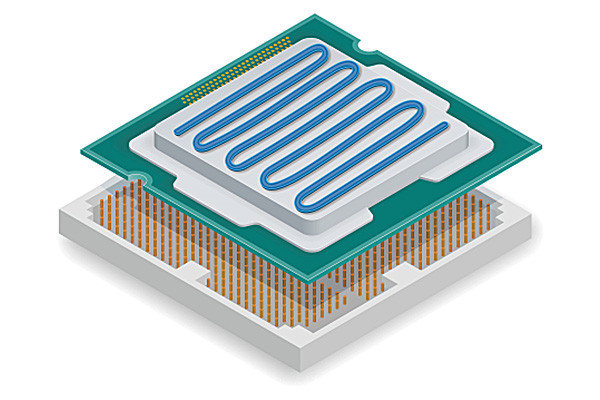
- Material Compatibility:Semiconductor devices often involve layers of different materials, such as silicon, silicon dioxide, metal, and various compound semiconductors. Adhesives must be selected to be compatible with these materials to ensure proper adhesion and avoid material degradation or delamination.
- Thermal Expansion Matching:Different semiconductor materials have different coefficients of thermal expansion (CTE). This can lead to thermal stresses during temperature variations. Adhesives with a CTE closely matching the bonded materials help minimize the risk of thermal stress-induced failure.
- Wafer Bonding:In wafer bonding processes, where two semiconductor wafers are bonded, adhesives create a strong bond between the wafers. This technique often integrates different materials, such as silicon-on-insulator (SOI) structures or compound semiconductors. Adhesives in wafer bonding help achieve direct wafer-to-wafer bonding, allowing the integration of various materials and technologies on the same device.
- Die Attachment:Adhesives are used in the die attachment process, where the semiconductor chip (die) is bonded to a substrate or package. This involves bonding materials like silicon to metal or ceramic substrates. The adhesive provides a reliable bond, ensuring good thermal conductivity and mechanical stability.
- Through-Silicon Via (TSV) Bonding:In 3D semiconductor packaging, through-silicon vias (TSVs) connect different semiconductor device layers vertically. Adhesives bond the TSV structures, ensuring electrical connectivity and mechanical stability between the layers.
- Encapsulation:Adhesives are used in the encapsulation process to bond protective materials around semiconductor components. This helps protect the layers from environmental factors and mechanical stress. The adhesive ensures a strong bond between the encapsulant and the semiconductor layers.
- MEMS Fabrication:Microelectromechanical Systems (MEMS) often involve integrating different materials, such as silicon, metals, and polymers. Adhesives are used in various MEMS fabrication processes, helping to bond different layers and create complex structures with precision.
- Interposer Bonding:In advanced packaging technologies, interposers connect different semiconductor components or packages. Adhesives bond the interposer to the components, providing electrical connectivity and ensuring mechanical stability.
- Thin-Film Deposition:Adhesives can also be used to deposition thin films on semiconductor substrates. This involves bonding a thin film of material onto a substrate, and adhesives can help ensure uniform adhesion and bonding during deposition.
The adhesive’s role in bonding different semiconductor material layers is multifaceted, encompassing considerations of material compatibility, thermal properties, mechanical stability, and overall reliability. The specific requirements of each semiconductor application dictate the choice of adhesive and the bonding process to achieve optimal performance and longevity of the devices.
Are there environmental considerations in the selection of chip-manufacturing adhesives?
Yes, environmental considerations are increasingly important in the selection of chip-manufacturing adhesives. The semiconductor industry has been paying more attention to ecological sustainability and reducing the environmental impact of manufacturing processes. Several factors come into play when considering the ecological effect of the used adhesives in chip manufacturing:
- Volatile Organic Compounds (VOCs):Some adhesives release volatile organic compounds during manufacturing and curing. VOCs can contribute to air pollution and have environmental and health implications. Environmentally friendly adhesives aim to minimize or eliminate the emission of VOCs.
- Hazardous Substances:Hazardous substances in adhesives, such as heavy metals or toxic solvents, can have adverse environmental effects. Regulations like the Restriction of Hazardous Substances (RoHS) directive in the European Union restrict the use of certain hazardous substances in electronic products, including semiconductor devices.
- Waste Reduction:Adhesive bonding processes that generate minimal waste or enable easy recycling contribute to environmentally friendly manufacturing practices. Manufacturers are increasingly focusing on waste reduction and recycling initiatives to minimize the environmental impact of semiconductor production.
- Energy Consumption:The energy required for adhesive manufacturing and curing processes is a consideration. Adhesive formulations and processes that require lower energy consumption contribute to a more sustainable manufacturing environment.
- Biodegradability:Adhesives that are biodegradable or environmentally benign after the end of the product life cycle can help reduce the long-term environmental impact. This consideration is particularly relevant when looking at electronic device disposal and end-of-life management.
- Water-Based Adhesives:Water-based adhesives are considered more environmentally friendly than solvent-based alternatives because they typically have lower VOC emissions and reduced environmental impact. Water-based adhesives are often preferred in applications where environmental concerns are a priority.
- Life Cycle Assessment (LCA):Assessing the environmental impact of adhesives throughout their entire life cycle, from raw material extraction to disposal, is becoming more common. Life cycle assessments help identify areas for improvement and guide the selection of adhesives with lower overall environmental impact.
- Regulatory Compliance:Adhesive selection must align with relevant environmental regulations and standards. Compliance with regional and global laws, such as RoHS and Registration, Evaluation, Authorization, and Restriction of Chemicals (REACH), is critical for environmentally responsible manufacturing.
As environmental awareness and sustainability goals become integral to corporate strategies and industry standards, semiconductor manufacturers increasingly seek adhesives that align with these principles. Adhesive suppliers are responding by developing eco-friendly formulations and providing documentation on the environmental characteristics of their products to assist manufacturers in making more sustainable choices.
What innovations have occurred in chip manufacturing adhesives in recent years?
In recent years, several innovations in chip manufacturing adhesives have been driven by the need for improved performance, miniaturization, and environmental sustainability. Some notable innovations include:
- Low-Temperature Curing Adhesives:Traditional adhesive curing processes often require elevated temperatures, which can be challenging for heat-sensitive components or substrates. Low-temperature curing adhesives have been developed to enable bonding at lower temperatures, reducing the risk of thermal damage to delicate semiconductor components.
- Nanoscale Adhesives:The trend toward smaller and more densely packed semiconductor devices has led to the development of nanoscale adhesives. These adhesives are designed to provide precise and robust bonding at the microscopic level, facilitating the assembly of advanced semiconductor structures with tight tolerances.
- Thermally Conductive Adhesives:With the increasing power density of semiconductor devices, effective thermal management is crucial. Thermally conductive adhesives have been developed to enhance heat dissipation, ensuring that heat generated by the semiconductor components is efficiently transferred to heat sinks or other cooling mechanisms.
- Flexible and Stretchable Adhesives:The demand for flexible and stretchable electronics has led to the development adhesives that maintain their integrity and adhesion even when subjected to bending or stretching. These adhesives are essential for applications such as flexible displays, wearable electronics, and other emerging technologies.
- Environmentally Friendly Adhesives:Adhesive formulations with reduced environmental impact have gained importance. Water-based adhesives, solvent-free formulations, and adhesives with minimal volatile organic compound (VOC) emissions contribute to environmentally friendly manufacturing processes.
- Multi-Material Bonding:As semiconductors incorporate diverse materials, including metals, ceramics, and polymers, adhesives capable of bonding dissimilar materials have become essential. Innovations in adhesives facilitate strong and reliable bonds between different materials, supporting the integration of diverse components.
- Advanced Die-Attach Adhesives:Die-to-attach adhesives, which bond semiconductor chips to substrates or packages, have seen advancements in thermal conductivity, cure speed, and reliability. These improvements are crucial for the efficient functioning of high-performance semiconductor devices.
- Innovative Adhesives:Adhesives with sensing or self-healing capabilities have been explored. Innovative adhesives can provide additional functionalities, such as monitoring structural integrity or automatically repairing minor damage to the bond interface, contributing to the overall reliability of semiconductor devices.
- Low Outgassing Adhesives:Low outgassing adhesives have been developed in applications where outgassing can be detrimental, such as in aerospace or vacuum environments. These adhesives release minimal volatile components, reducing the risk of contamination in sensitive environments.
- Conductive Adhesives for Microelectronics:Developing conductive adhesives has facilitated the assembly of microelectronic components without soldering. These adhesives enable electrically conductive bonds and are used in applications such as flexible circuits and electronic packaging.
These innovations reflect the dynamic nature of the semiconductor industry, with ongoing efforts to address challenges related to performance, miniaturization, and environmental sustainability. As technology advances, further innovations in chip manufacturing adhesives will likely contribute to developing more efficient, reliable, and environmentally friendly semiconductor devices.
How does adhesive quality control impact the reliability of semiconductor devices?
Adhesive quality control is a critical aspect of semiconductor manufacturing, directly impacting semiconductor devices’ reliability. The quality of adhesives used in various bonding processes can influence the electrical performance, thermal management, and overall durability of semiconductor devices. Here are several ways in which adhesive quality control is crucial for ensuring the reliability of semiconductor devices:
- Bond Strength:The adhesive bond strength is a critical factor in the reliability of semiconductor devices. Quality control measures ensure the adhesive provides a strong and durable bond between components, such as the semiconductor die and the substrate or package. Inadequate bond strength can lead to mechanical failures, delamination, and compromised device integrity.
- Uniformity:Adhesive quality control ensures uniform application of adhesives across semiconductor wafers or components. Non-uniform distribution can result in variations in bond strength and may lead to performance inconsistencies or failures in the final devices.
- Material Compatibility:Semiconductor devices often involve the bonding of different materials, such as silicon, metals, and insulating layers. Adhesive quality control ensures that the adhesive is compatible with these materials, preventing issues like corrosion, material degradation, or mismatched thermal expansion coefficients that could impact device reliability.
- Curing Process Control:The curing process of adhesives is crucial for achieving the desired properties. Quality control monitors factors such as curing time, temperature, and humidity to ensure that the adhesive cures properly. Only complete or proper curing can result in solid bonds, reduced thermal conductivity, and other performance issues.
- Contamination Control:Adhesive quality control measures help prevent contamination during the manufacturing process. Contaminants, such as dust or foreign particles, can compromise the integrity of the adhesive bond and lead to device failures.
- Adhesive Thickness Control:The thickness of the adhesive layer is critical for achieving the desired electrical and thermal properties. Quality control ensures that the adhesive coating is within specified tolerances to meet design requirements. Inconsistent adhesive thickness can affect heat dissipation and electrical connectivity.
- Reliability Testing:Rigorous reliability testing of adhesive bonds is crucial to quality control. This may involve thermal cycling, mechanical stress testing, and other accelerated aging tests to simulate real-world operating conditions. Reliable adhesives should withstand these tests without degrading or compromising device performance.
- Traceability and Documentation:Quality control processes include proper documentation of adhesive specifications, manufacturing parameters, and testing results. This traceability is essential for identifying and addressing issues and ensuring consistency in adhesive quality over time.
- Environmental Considerations:Adhesives used in semiconductor manufacturing should comply with environmental regulations. Quality control ensures that adhesives meet environmental standards, such as restrictions on hazardous substances, contributing to the sustainability of semiconductor manufacturing processes.
- Process Consistency:Quality control measures ensure that adhesive application processes are consistent throughout the manufacturing line. Consistency is crucial for reproducibility and minimizing variations that could impact the reliability of semiconductor devices.
Adhesive quality control is a comprehensive process that involves monitoring and ensuring various factors, including bond strength, uniformity, material compatibility, curing processes, contamination control, reliability testing, and environmental considerations. Rigorous adherence to quality control standards is essential for producing reliable semiconductor devices with consistent performance and longevity.
What role does adhesive play in the miniaturization of electronic components in chips?
Adhesives play a crucial role in the miniaturization of electronic chip components, contributing to developing and manufacturing smaller, more compact, and highly integrated semiconductor devices. Several critical roles of adhesives in the miniaturization process include:
- Die to Attach:In semiconductor manufacturing, die-attach refers to bonding the semiconductor chip (die) to a substrate or package. Adhesives are used in this step to create a strong and reliable bond, allowing for precise placement of the die. As electronic components shrink in size, the accuracy and uniformity of die attach become even more critical, and adhesives enable the necessary precision.
- Package Sealing:As electronic components become smaller and more densely packed, effective package sealing becomes paramount. Adhesives seal the semiconductor package, protecting the delicate components from environmental factors like moisture, contaminants, and mechanical stress. This sealing is crucial for maintaining the reliability of miniaturized devices.
- Wire Bonding:Adhesives play a role in wire bonding, where thin wires connect the semiconductor die to the package or substrate. Miniaturization often involves finer and more closely spaced wire bonds. Adhesives help secure the wires, ensuring proper electrical connections and mechanical stability.
- 3D Integration:Adhesives are essential in 3D integration, a technology that involves stacking multiple semiconductor layers on top of each other. Adhesives facilitate the bonding of these layers, enabling the creation of vertically integrated circuits. This stacking approach contributes to the miniaturization of electronic components by utilizing space more efficiently.
- Microelectromechanical Systems (MEMS):Adhesives are used to fabricate MEMS, where miniaturized mechanical and electronic components are integrated into a single chip. Adhesives assist in bonding different materials and components, allowing for the creation of small-scale sensors, actuators, and other microdevices.
- Interposer Bonding:Interposers are layers that provide connectivity between various semiconductor components or packages. Adhesives play a role in bonding interposers to facilitate the integration of miniaturized electronic components, enabling efficient communication between layers.
- Flexible Electronics:The trend toward flexible and bendable electronics involves using adhesives in bonding components to flexible substrates. Adhesives must be flexible and adhere well to different materials to enable the creation of compact and deformable electronic devices.
- Reducing Component Size:Adhesives can be applied in precise amounts, allowing for the accurate bonding of tiny components. This capability is crucial in the miniaturization process, where the size of individual electronic components, such as resistors, capacitors, and transistors, is significantly reduced.
- Enhanced Thermal Management:Miniaturized electronic components generate heat more densely. Adhesives with high thermal conductivity are employed to help dissipate heat efficiently, contributing to the thermal management of miniaturized devices.
Adhesives play a multifaceted role in the miniaturization of electronic components in chips. They enable precise bonding, sealing, and interconnection of smaller parts, support 3D integration, and contribute to miniaturized semiconductor devices’ overall reliability and functionality. As the demand for smaller and more powerful electronic devices continues to grow, the role of adhesives in supporting miniaturization remains critical in advancing semiconductor technology.
Are there specific considerations for adhesives in advanced packaging technologies?
Yes, there are several specific considerations for adhesives in advanced packaging technologies. Advanced packaging technologies often involve integrating multiple components, such as semiconductor devices, sensors, and other advanced materials. Adhesives play a crucial role in bonding and securing these components together. Here are some key considerations:
Temperature Resistance:
- Many advanced packaging processes involve high temperatures, such as during soldering or other bonding processes. Adhesives must have the appropriate temperature resistance to withstand these conditions without degradation.
Thermal Conductivity:
- In applications where heat dissipation is critical, such as in microelectronics, adhesives with good thermal conductivity may be necessary to ensure efficient heat transfer and prevent overheating of components.
Chemical Compatibility:
- Adhesives must be compatible with the materials they are bonding. This includes compatibility with the substrates and other materials used in the packaging to prevent issues like corrosion or chemical reactions that could affect the performance of the device.
Electrical Properties:
- In some cases, adhesives need specific electrical properties to ensure the proper functioning of the packaged device. For example, in microelectronic applications, adhesives may need to be electrically insulating or conductive, depending on the requirements.
Mechanical Strength:
- The adhesive should provide sufficient mechanical strength to withstand thermal cycling, mechanical shocks, and vibrations. This is especially important in applications where the packaged devices may be subjected to harsh environmental conditions.
Miniaturization and Thin Profiles:
- As packaging technologies continue to evolve towards smaller form factors and thinner profiles, adhesives need to be able to bond components in these compact spaces without compromising performance.
Curing Time and Process Compatibility:
- The curing time of adhesives is essential in manufacturing processes. Some applications may require adhesives that cure quickly to optimize production efficiency. The curing process should also be compatible with the overall packaging process, including any temperature or pressure requirements.
Reliability and Long-Term Stability:
- Adhesives must provide reliable, long-term bonding to ensure the durability and stability of the packaged device over its operational lifespan. This is particularly critical in applications where the failure of the adhesive bond could lead to device malfunction or damage.
Regulatory Compliance:
- Adhesives used in advanced packaging technologies must comply with industry regulations and standards, primarily if the packaged devices are intended for specific medical or aerospace applications.
Environmental Considerations:
- Some applications may have specific environmental requirements, such as resistance to moisture, chemicals, or other environmental factors. Adhesives should be chosen based on their ability to withstand these conditions.
It’s important to note that the specific requirements for adhesives in advanced packaging technologies can vary depending on the type of technology, industry, and application. Manufacturers typically work closely with adhesive suppliers to select the most suitable materials.
How do temperature and environmental factors affect chip manufacturing adhesives?
Temperature and environmental factors can significantly impact chip manufacturing adhesives, which are crucial components in the fabrication of semiconductor devices. Here are some ways in which these factors can influence the adhesive and, consequently, the overall chip manufacturing process:
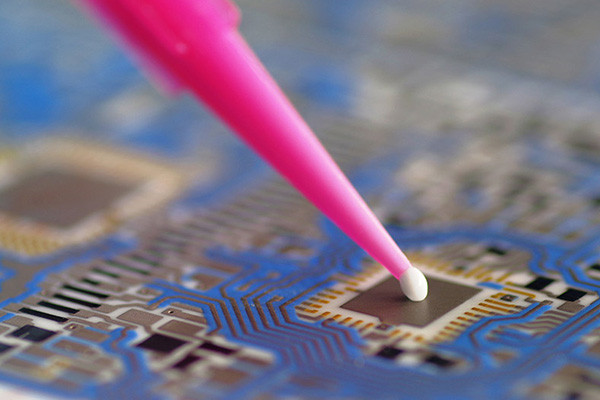
Curing and Setting Time:
- Temperature:The curing or setting time of adhesives is often temperature-dependent. Higher temperatures can accelerate the curing process, while lower temperatures may slow it down. Manufacturers must carefully control these conditions to ensure that adhesives cure at the desired rate, preventing issues such as incomplete bonding or excessive curing times.
Adhesive Viscosity:
- Temperature:The viscosity of adhesives tends to change with temperature. Higher temperatures can reduce viscosity, making the adhesive more fluid, while lower temperatures may increase viscosity, making it thicker. Proper viscosity is essential for applying the adhesive during the manufacturing process.
Chemical Stability:
- Temperature and Environmental Conditions:Adhesives may undergo chemical changes or degradation when exposed to high temperatures or harsh environmental conditions. It’s crucial to choose adhesives with suitable chemical stability to withstand the specific conditions of the chip manufacturing environment.
Adhesion Strength:
- Temperature and Cure Time:The adhesion strength of the adhesive may be influenced by both temperature and the time it takes for the glue to cure. Insufficient curing time or improper temperature control can lead to weaker bonds, affecting the overall reliability of the semiconductor device.
Thermal Conductivity:
- Temperature:The thermal conductivity of adhesives is essential for efficient heat dissipation within the chip. High temperatures can impact the thermal properties of the adhesive, affecting its ability to transfer heat away from the semiconductor components.
Moisture Sensitivity:
- Environmental Conditions:Some adhesives are sensitive to moisture. Exposure to high humidity levels can lead to moisture absorption, potentially compromising the adhesive’s performance and the integrity of the semiconductor device.
Material Compatibility:
- Environmental Factors:Adhesives should be compatible with the materials they are bonding with. Exposure to certain environmental factors, such as chemicals or gasses, can lead to material compatibility issues, affecting the adhesive’s adhesion strength and overall performance.
Contamination:
- Environmental Conditions:Dust, particles, or contaminants in the manufacturing environment can adversely affect the adhesive’s performance. Proper cleanroom conditions are crucial to prevent contamination and ensure the quality of the adhesive bonds.
Precise control of temperature and environmental conditions is essential in chip manufacturing to ensure the proper performance of adhesives. Manufacturers must select adhesives that can withstand the specific requirements of the semiconductor fabrication process and carefully monitor and control the manufacturing environment to maintain consistent adhesive performance.
What are the safety considerations associated with handling chip-manufacturing adhesives?
Handling chip-manufacturing adhesives involves several safety considerations to protect workers, maintain product quality, and ensure overall facility safety. Here are some essential safety considerations associated with running these adhesives:
Material Safety Data Sheet (MSDS):
- Always review the MSDS for the specific adhesive being used. The MSDS provides information on the chemical composition, potential hazards, safe handling procedures, and emergency response measures.
Personal Protective Equipment (PPE):
- Use appropriate PPE, gloves, safety glasses or goggles, and protective clothing, as the MSDS recommends. The type of PPE required may vary depending on the adhesive’s composition and the risks associated with its use.
Ventilation:
- Work in well-ventilated areas or use local exhaust ventilation systems to control and minimize exposure to fumes, vapors, or airborne particles generated during the adhesive application and curing process.
Respiratory Protection:
- If there is a potential for inhalation exposure to airborne contaminants, use respiratory protection equipment by occupational health and safety regulations.
Training:
- Ensure that personnel are adequately trained in safely handling, storing, and disposing of adhesives. Training should cover emergency procedures, the proper use of PPE, and the importance of following established safety protocols.
Handling and Storage:
- Follow appropriate procedures for handling and storing adhesives, including temperature and humidity requirements. Store adhesives in designated areas away from incompatible materials and heat sources.
Emergency Response:
- Establish and communicate emergency response procedures in case of spills, leaks, or accidents. This includes readily available spill response kits, eyewash stations, and emergency showers.
Avoid Skin Contact:
- Minimize skin contact with adhesives to prevent potential skin irritation or sensitization. Follow proper first aid procedures outlined in the MSDS in case of contact.
Avoid Eye Contact:
- Use appropriate eye protection to prevent accidental splashes or contact with adhesives. In case of eye contact, rinse your eyes immediately with water and seek medical attention.
Housekeeping:
- Maintain a clean and organized work environment to reduce the risk of spills and accidents. Promptly clean up any spills and dispose of waste materials according to regulations.
First Aid:
- Ensure that personnel are familiar with first aid procedures for adhesive-related incidents. Provide access to first aid supplies and have trained personnel available to respond to emergencies.
Regulatory Compliance:
- Adhere to local, regional, and national regulations and standards related to the handling and disposing adhesives. Stay informed about any updates or changes in regulations.
By implementing these safety considerations, manufacturers can create a safer working environment, reduce the risk of accidents, and protect the health and well-being of workers involved in chip manufacturing processes that use adhesives. Regular training and communication about safety practices are essential to a comprehensive safety program.
Can you elaborate on the process of applying adhesive during chip manufacturing?
Applying adhesive in chip manufacturing is a critical step in assembling and packaging integrated circuits (ICs). Adhesive, often called die to attach or die bonding material, bonds the semiconductor die (the actual chip) to the substrate or package. This process is essential for creating a secure and reliable connection between the die and the package, providing mechanical support and facilitating heat dissipation.
Here is a general overview of the die attach process in chip manufacturing:
Substrate Preparation:
- The substrate is the base material to which the semiconductor die will attach.
- The substrate is typically made of ceramic or organic laminate and may have conductive traces for electrical connections.
Die Placement:
- The semiconductor die containing the actual integrated circuit is picked and placed onto the prepared substrate.
- Automated equipment is often used for precise and accurate die placement.
Adhesive Dispensing:
- The adhesive material is dispensed onto the substrate in a controlled manner.
- The type of adhesive used can vary and may include epoxy-based adhesives or other materials with good thermal and electrical properties.
Die Bonding:
- The semiconductor die is lowered onto the substrate, and the adhesive facilitates the bonding between the die and the substrate.
- The process must be carefully controlled to ensure proper alignment and bonding without damaging the delicate circuits on the die.
Curing or Setting:
- The adhesive is allowed to cure or set, a process that involves a chemical reaction or physical hardening to achieve the desired mechanical properties.
- The curing process may involve heat, UV light, or other methods depending on the type of adhesive used.
Wire Bonding (if applicable):
- In some cases, wire bonding is performed after the die attaches to the med to establish electrical connections between the die and the substrate.
- Wire bonding involves attaching thin wires (usually made of aluminum or gold) from the die’s bonding pads to corresponding pads on the substrate.
Encapsulation or Sealing:
- The bonded die may be encapsulated or sealed with a protective material to shield it from environmental factors, such as moisture and contaminants.
- The encapsulation process ensures the reliability and durability of the IC.
Testing:
- The assembled and encapsulated chip undergoes testing to meet quality and performance standards.
The die-attach process is crucial for the overall reliability and performance of the integrated circuit. The choice of adhesive material, precision in placement, and careful control of the bonding process are all critical factors in producing high-quality semiconductor devices. Different manufacturing facilities may use variations of this process based on the specific requirements of the chips.
What factors influence the selection of adhesive materials for different chip applications?
The selection of adhesive materials for chip applications depends on various factors, and choosing the suitable adhesive is crucial to ensure the reliability and performance of the integrated circuit (IC). Here are some key factors that influence the selection of adhesive materials for different chip applications:
Thermal Conductivity:
- Adhesives with good thermal conductivity are essential for effective heat dissipation from the semiconductor die.
- High thermal conductivity helps in transferring heat away from the die, preventing overheating and ensuring the long-term reliability of the IC.
Electrical Conductivity:
- Some applications may require adhesives with specific electrical properties, especially in cases where the adhesive is part of the electrical path.
- For instance, in particular power devices, minimizing electrical resistance in the adhesive is essential to ensure efficient power transfer.
Adhesive Strength:
- The adhesive must bond strongly between the die and the substrate to ensure mechanical stability.
- The strength of the adhesive is crucial for withstanding thermal cycling, mechanical stress, and other environmental factors.
Curing Time and Process:
- The speed at which the adhesive cures is essential for the manufacturing process. Some applications may require fast-curing adhesives to increase production throughput.
- Whether it involves heat, UV light, or other methods, the curing process should be compatible with the overall manufacturing process.
Chemical Compatibility:
- The adhesive material must be chemically compatible with the semiconductor die and substrate.
- Chemical compatibility ensures the adhesive does not degrade over time, leading to a stable and long-lasting bond.
Coefficient of Thermal Expansion (CTE) Matching:
- The CTE of the adhesive should be well-matched with the CTE of both the die and the substrate.
- CTE matching helps to minimize the risk of thermal stresses during temperature variations, preventing potential damage to the IC.
Reliability and Durability:
- Adhesive materials should exhibit long-term reliability, durability, and resistance to environmental factors such as humidity, chemicals, and temperature extremes.
- These characteristics are critical for the performance and lifespan of the integrated circuit.
Dielectric Properties:
- In applications where the adhesive is near active components, dielectric properties become essential to avoid interference with electrical signals.
- Adhesives with low dielectric constants and low dissipation factors are often preferred for such applications.
Cost Considerations:
- The cost of the adhesive material is a practical consideration in the manufacturing process. It’s essential to balance performance requirements with cost constraints.
Process Compatibility:
- Adhesive materials should be compatible with the specific manufacturing processes used in the semiconductor facility. This includes dispensing, curing, and any post-bonding processes.
Application-Specific Requirements:
- Different chip applications may have unique requirements. For example, high-frequency applications may demand adhesives with specific dielectric properties, while automotive applications may require enhanced reliability under harsh environmental conditions.
The selection of adhesive materials is often a complex decision that involves considering a combination of these factors to meet the specific requirements of the intended application. It’s common for semiconductor manufacturers to work closely with adhesive suppliers and conduct extensive testing to ensure the chosen adhesive meets the desired performance criteria.
How do advancements in adhesive technology align with the evolution of chip design?
Advancements in adhesive technology play a crucial role in supporting and aligning with the evolution of chip design. As chip design evolves to meet increasing performance demands, smaller form factors, and enhanced functionalities, the adhesive materials used in the manufacturing process must keep pace to address new challenges and requirements. Here are several ways in which adhesive technology advancements align with the evolution of chip design:
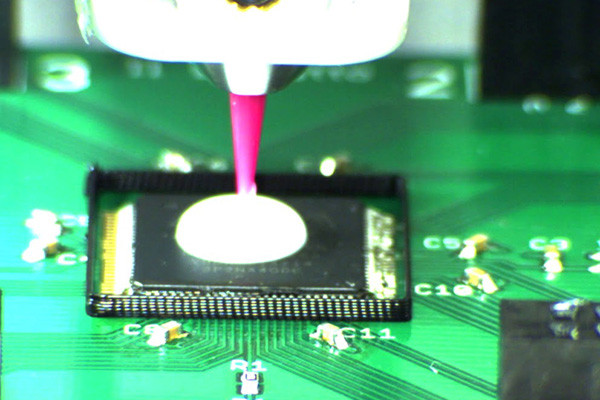
Miniaturization and Packaging Trends:
- As chip designs become more compact and feature-packed, the demand for smaller and thinner packages increases.
- Advanced adhesive technologies enable the development of ultra-thin bonding materials that maintain strong mechanical bonds while accommodating the trend toward smaller form factors.
Thermal Management:
- Modern chip designs often involve higher power densities, leading to increased heat generation.
- Adhesive technologies with improved thermal conductivity help dissipate heat more efficiently, preventing overheating and ensuring the reliability of the integrated circuit.
Higher Frequency and Performance:
- With the growing demand for higher frequencies and improved performance, the electrical properties of adhesive materials become more critical.
- Advanced adhesives with low dielectric constants and minimal signal loss are essential to support high-speed and high-frequency chip design performance requirements.
Material Compatibility:
- As chip designs incorporate various materials, including advanced semiconductor materials and substrates, adhesive technologies must be compatible with these materials.
- Adhesives that can bond reliably to diverse materials while maintaining stability over time contribute to the success of multifaceted chip designs.
Reliability Under Harsh Conditions:
- Adhesives must meet the reliability demands of chip designs in diverse environments, including automotive, aerospace, and industrial applications.
- Advancements in adhesive formulations enhance resistance to environmental factors such as temperature extremes, humidity, and chemical exposure, ensuring the chip’s longevity.
Fine Pitch and High-Density Interconnections:
- Evolving chip designs often involve finer pitches and higher-density interconnections.
- Adhesive technologies that enable precise dispensing and bonding in fine-pitch applications support the realization of advanced chip architectures.
Integration with Advanced Packaging Technologies:
- Advanced packaging technologies, such as 3D packaging and heterogeneous integration, require adhesives that accommodate complex structures and bonding configurations.
- Adhesive advancements contribute to the successful implementation of innovative packaging solutions.
Flexible and Hybrid Electronics:
- With the rise of flexible and hybrid electronics, adhesive technologies that can adhere to flexible substrates and accommodate mechanical deformations are essential.
- Adhesives designed for flexibility and durability contribute to realizing flexible and stretchable electronic devices.
Process Compatibility:
- As chip manufacturing processes evolve, adhesive technologies must be compatible with new techniques and equipment.
- Advancements in dispensing methods, curing processes, and overall process compatibility contribute to the efficiency of chip assembly.
Cost-Effective Solutions:
- Adhesive technologies that offer improved performance without significantly increasing manufacturing costs align well with the industry’s goals of achieving higher functionality at competitive prices.
Advancements in adhesive technology are closely aligned with the evolution of chip design by addressing critical challenges associated with miniaturization, thermal management, electrical performance, material compatibility, reliability, and the integration of advanced packaging techniques. Collaboration between semiconductor manufacturers and adhesive suppliers is essential to developing and implementing solutions that meet the specific needs of next-generation chip designs.
What impact does adhesive choice have on the overall cost of chip manufacturing?
The choice of adhesive in chip manufacturing can significantly impact the manufacturing process’s overall cost. While adhesive costs are just one component of the entire manufacturing cost structure, selecting the suitable adhesive can influence various factors contributing to the overall cost. Here are some ways in which adhesive choice can impact the cost of chip manufacturing:
Material Cost:
- The cost of the adhesive material itself is a direct factor. Advanced adhesive formulations with specialized properties may come at a higher price than standard adhesives.
- However, the overall impact on material cost may be relatively small compared to other factors.
Process Efficiency:
- Adhesives that allow faster curing times or more efficient dispensing can increase process throughput.
- Faster manufacturing processes can reduce labor costs and increase production capacity, ultimately affecting the overall cost structure.
Yield and Reliability:
- The choice of adhesive can impact the yield of the manufacturing process. Adhesives that provide solid and reliable bonds contribute to higher yield rates by reducing the likelihood of defects and rework.
- Higher yield rates translate to cost savings as fewer resources are needed to address manufacturing defects.
Equipment Compatibility:
- Adhesives compatible with existing manufacturing equipment may reduce the need for equipment upgrades or modifications.
- Avoiding the cost of extensive equipment changes can contribute to overall cost savings.
Energy Consumption:
- Certain adhesives may require specific curing conditions, such as elevated temperatures or UV light exposure. The energy consumption associated with these curing processes can impact manufacturing costs.
- Adhesives for lower energy consumption or shorter curing times can contribute to cost efficiency.
Waste Reduction:
- Adhesives that minimize waste through precise dispensing or reduced rework can contribute to cost savings.
- Waste reduction is not only environmentally responsible but also economically advantageous by maximizing the utilization of materials.
Long-Term Reliability:
- Adhesives that contribute to the long-term reliability of the chips can impact the overall cost of ownership. Products with enhanced reliability may require fewer warranty claims or returns, reducing associated costs.
Environmental and Regulatory Compliance:
- Adhesive choices that align with environmental regulations and sustainability goals may impact costs associated with compliance.
- Adhesives with hazardous materials or processes may incur additional disposal or regulatory compliance costs.
Application-Specific Requirements:
- Some applications may have specific requirements that necessitate the use of specialized adhesives. While these adhesives may come at a higher cost, they are essential for meeting the performance criteria of the application.
Market Competition:
- The overall cost of adhesive materials can be influenced by market competition. The availability of alternative adhesive suppliers and formulations can affect pricing.
The impact of adhesive choice on the overall cost of chip manufacturing is multifaceted. It involves not only the direct cost of the adhesive material but also considerations related to process efficiency, yield, reliability, equipment compatibility, waste reduction, long-term performance, and compliance with environmental regulations. The optimization of adhesive selection should be a balanced decision that considers both the short-term and long-term cost implications and the specific requirements of the chip application.
Are there specific challenges in adhesive application for 3D chip stacking?
Yes, 3D chip stacking, also known as 3D IC (integrated circuit) packaging, introduces unique challenges in adhesive applications due to the complex nature of stacking multiple semiconductor dies on top of each other. The adhesive used in 3D chip stacking plays a critical role in ensuring the stacked layers’ mechanical integrity, thermal performance, and electrical connectivity. Here are some specific challenges associated with adhesive application in 3D chip stacking:
Alignment and Precision:
- Achieving precise alignment of multiple layers during the stacking process is crucial. Adhesive materials must allow for accurate placement and bonding of each die to ensure proper electrical connections and minimize the risk of misalignment.
Thin and Uniform Bond Lines:
- In 3D stacking, the adhesive layers between the stacked dies must be thin and uniform. Controlling the thickness of the adhesive bond lines is essential to prevent variations in thermal conductivity and to ensure consistent mechanical support.
Curing Process:
- The curing process of the adhesive becomes more challenging in 3D chip stacking. Since the adhesive is sandwiched between multiple layers, ensuring complete and uniform curing throughout the stacked structure is essential for optimal mechanical and thermal performance.
Thermal Management:
- Heat dissipation is a critical consideration in 3D chip stacking due to the proximity of multiple active layers. Adhesives must exhibit high thermal conductivity to transfer heat away from the stacked efficiently dies. Balancing thermal management with other material properties is crucial for overall reliability.
Material Compatibility:
- Different materials are used in various layers of 3D stacked chips, including diverse semiconductor materials and substrates. The adhesive must be compatible with all materials to ensure robust and reliable bonding.
Dielectric Properties:
- Adhesives in 3D chip stacking must have appropriate dielectric properties to avoid interference with electrical signals between the stacked layers. Low dielectric constants and low dissipation factors are often desirable.
Stress Management:
- Stacking multiple dies introduces mechanical stresses, including thermal expansion mismatches and warping. Adhesives must be capable of managing these stresses to prevent delamination, cracking, or other mechanical failures.
Process Complexity:
- 3D chip stacking processes are inherently more complex than traditional 2D packaging. Adhesive application processes must be carefully optimized to accommodate the added complexity without compromising yield or efficiency.
Cleaning and Residue:
- Residue from the adhesive application process can be challenging, especially when dealing with multiple layers. Cleaning processes should be effective without causing damage to the delicate features of the stacked dies.
Volume and Cost Considerations:
- The cost of adhesive material and the volume of adhesive used in 3D chip stacking can impact overall manufacturing costs. Balancing performance requirements with cost considerations is crucial in optimizing the adhesive selection for 3D ICs.
Addressing these challenges requires a combination of advanced adhesive formulations, precise manufacturing processes, and close collaboration between semiconductor manufacturers and adhesive suppliers. Research and development efforts focus on overcoming these challenges to enable the widespread adoption of 3D chip stacking for improved performance and efficiency in semiconductor devices.
How do researchers and manufacturers address sustainability concerns in chip manufacturing adhesives?
Addressing sustainability concerns in chip manufacturing adhesives is an essential focus for researchers and manufacturers as environmental awareness and sustainable practices become increasingly crucial. Several strategies and approaches are being employed to minimize the ecological impact of adhesives used in chip manufacturing:
Material Selection:
- Researchers aim to develop adhesives using environmentally friendly materials, such as bio-based or renewable resources. This includes exploring alternatives to traditional petrochemical-based adhesives that may have a lower environmental footprint.
Low-impact Formulations:
- Adhesive formulations are being optimized to reduce the use of hazardous or environmentally harmful substances. Manufacturers seek alternatives with lower toxicity, fewer volatile organic compounds (VOCs), and less impact on air and water quality.
Reduced Energy Consumption:
- Adhesive curing processes often involve energy-intensive steps. Researchers are developing adhesives that can cure at lower temperatures or through more energy-efficient methods, reducing energy consumption during manufacturing.
Recyclability and Biodegradability:
- The push for adhesives that can be easily recycled or are biodegradable is growing. Adhesives that break down naturally or can be separated from other materials for recycling contribute to a more sustainable manufacturing process.
Waste Reduction:
- Manufacturing processes are being optimized to minimize waste generated during adhesive application. Precise dispensing and efficient curing methods can reduce the amount of excess adhesive, contributing to less waste in the manufacturing process.
Life Cycle Analysis:
- Researchers and manufacturers are conducting life cycle assessments (LCAs) to understand the environmental impact of adhesives at every stage, from raw material extraction to disposal. This comprehensive approach helps identify areas for improvement and informs sustainable decision-making.
Green Certifications:
- Adhesives meeting specific environmental and sustainability criteria are often awarded green certifications. Manufacturers may choose adhesives with certifications such as REACH (Registration, Evaluation, Authorization, and Restriction of Chemicals) or other eco-labels to ensure compliance with environmental standards.
Closed-loop Systems:
- Closed-loop systems, where waste materials are collected and reused within the manufacturing process, are being explored. This reduces the need for new raw materials and minimizes the overall environmental impact.
Collaboration and Information Sharing:
- Industry collaboration and information sharing are essential for advancing sustainable practices. Researchers and manufacturers work together to share best practices, innovations, and advancements in sustainable adhesive technologies.
Regulatory Compliance:
- Adhesive manufacturers strive to comply with and exceed environmental regulations. Adhering to strict ecological standards ensures that the adhesives used in chip manufacturing meet or exceed regulatory requirements.
Education and Awareness:
- Raising awareness about the environmental impact of adhesives and promoting sustainable practices within the industry is essential. This includes educating manufacturers, suppliers, and end-users about the benefits of choosing sustainable adhesive solutions.
By incorporating these strategies, researchers and manufacturers aim to develop and adopt adhesive technologies that align with broader sustainability goals, reducing the environmental impact of chip manufacturing processes. Continuous innovation and a commitment to sustainability will be crucial in addressing the environmental challenges associated with adhesive use in the semiconductor industry.
What future trends can we expect in chip manufacturing process adhesives?
The chip manufacturing process adhesives field is dynamic, and several future trends are expected to shape the industry. These trends reflect technological advancements, the evolving landscape of semiconductor manufacturing, and the increasing demand for improved performance, efficiency, and sustainability. Here are some anticipated future trends in chip manufacturing process adhesives:
Advanced Material Formulations:
- Future adhesives will likely feature advanced formulations with enhanced properties, such as improved thermal conductivity, electrical conductivity, and resistance to environmental factors. The development of novel materials, including bio-based and sustainable options, will continue to gain importance.
Nanotechnology in Adhesives:
- Nanotechnology is expected to play a significant role in developing adhesives for chip manufacturing. Nanomaterials can offer unique properties, such as improved strength, thermal conductivity, and precision, making them valuable for advanced applications.
Flexible and Stretchable Adhesives:
- As flexible and stretchable electronics become more prevalent, there will be an increasing need for adhesives that can accommodate mechanical deformations without compromising performance. Adhesives designed for flexible and stretchable applications will be in demand.
Integration with Advanced Packaging Technologies:
- Adhesives must adapt to and integrate with advanced packaging technologies, including 2.5D and 3D chip stacking, fan-out wafer-level packaging (FOWLP), and system-in-package (SiP). This involves addressing challenges related to multiple die stacking, fine pitch interconnections, and heterogeneous integration.
Innovative Adhesives with Self-Healing Properties:
- The development of intelligent adhesives with self-healing properties is an emerging trend. Adhesives that can autonomously repair minor defects or cracks over time could enhance the long-term reliability of semiconductor devices.
Reduced Environmental Impact:
- Sustainable and environmentally friendly adhesive formulations will continue to gain prominence. Adhesives with reduced environmental impact, lower toxicity, and improved recyclability will be prioritized to align with global sustainability goals.
Industry 4.0 and Smart Manufacturing:
- Adopting Industry 4.0 principles in semiconductor manufacturing will likely influence adhesive application processes. Innovative manufacturing technologies, including real-time monitoring, data analytics, and process optimization, will contribute to more efficient and controlled adhesive applications.
Customization and Application-Specific Solutions:
- Adhesives tailored to specific applications and manufacturing processes will become more prevalent. Customized solutions will address the unique requirements of diverse semiconductor devices, ensuring optimal performance and reliability.
3D Printing for Adhesive Application:
- 3D printing or additive manufacturing techniques may be explored for depositing adhesives with high precision. This approach could enable intricate and customized adhesive patterns, improving performance and reducing waste.
Improved Dispensing Technologies:
- Advancements in dispensing technologies will contribute to more precise and efficient application of adhesives. This includes developments in automated dispensing systems, jetting technologies, and other methods to enhance accuracy and throughput.
Regulatory Compliance and Safety:
- Adhesive formulations must adhere to evolving regulatory standards related to environmental, health, and safety considerations. Manufacturers will continue to prioritize formulations that comply with global regulations.
These trends reflect the ongoing efforts to address the challenges and opportunities in chip manufacturing process adhesives. The industry will likely see a continued emphasis on innovation, collaboration, and sustainability to meet the evolving needs of semiconductor technologies.
Conclusion:
In conclusion, the chip manufacturing process adhesive world is complex and dynamic, with continuous advancements shaping the landscape. As technology progresses, the demand for reliable and efficient adhesives in semiconductor manufacturing continues to rise. This guide aims to shed light on the various facets of chip manufacturing process adhesive, offering valuable information to engineers, researchers, and enthusiasts navigating this fascinating field. Stay tuned for the latest updates and emerging trends in chip manufacturing adhesives as we continue to explore cutting-edge technology.
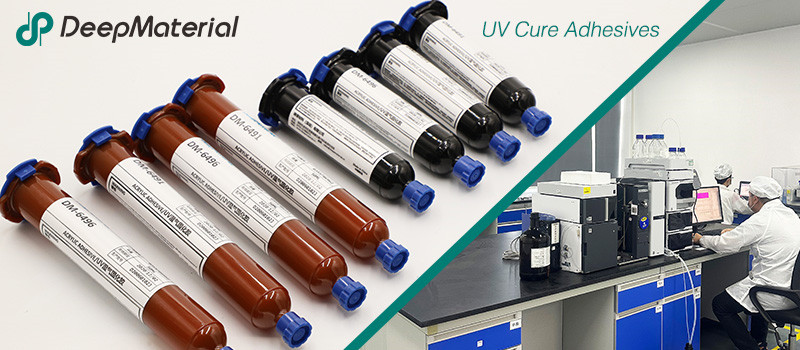
DeepMaterial
Based on the core technology of adhesives, DeepMaterial has developed adhesives for chip packaging and testing, circuit board level adhesives, and adhesives for electronic products. Based on adhesives, it has developed protective films, semiconductor fillers, and packaging materials for semiconductor wafer processing and chip packaging and testing. More…
UV Curing Adhesives
UV light cure have a number of benefits making them a popular choice among many product assembly and manufacturing applications. Many UV light cure adhesives can provide a nearly instantaneous bond to difficult substrates like glass and plastic. UV cure adhesives often require an accelerator or UV light for a bond to form.
Adhesive Blogs & News
The latest adhesive industry science and technology, Deepmaterial news, and market trends and forecasts.
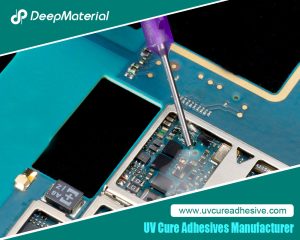
Electrical Potting Compound
Electrical Potting Compound In the vast field of modern electronic technology, Electrical Potting Compound plays a crucial role. It is like the invisible guardian inside electronic devices, providing reliable protection and stable performance support for various precise electronic components. Definition and Classification of Electrical Potting Compound Electrical Potting Compound is a special material
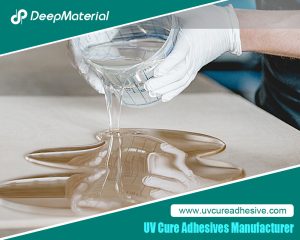
The Mystery and Application of Polyurethane Potting
The Mystery and Application of Polyurethane Potting In the modern industrial and technological fields, Polyurethane Potting is playing an increasingly important role. It not only provides reliable protection for various electronic devices and components but also shows unique advantages in optimizing performance and extending service life. What is Polyurethane Potting Polyurethane Potting is a
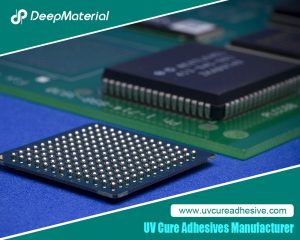
Waterproof Potting Compound: The Invisible Guardian of Electronic Devices
Waterproof Potting Compound: The Invisible Guardian of Electronic Devices In the era of rapid technological development today, electronic devices have become an indispensable part of our lives and work. From smart phones, tablets to smart home devices and industrial control systems, the application of electronic devices is everywhere. However, these devices often face the tests
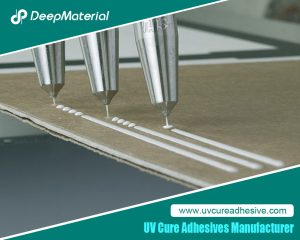
Potting Compound vs Epoxy: A Comparative Study and Application Overview
Potting Compound vs Epoxy: A Comparative Study and Application Overview In the modern industrial and electronic domains, the selection of materials holds a pivotal position in determining the performance, reliability, and longevity of products. Potting Compound and Epoxy are two frequently encountered materials that each demonstrate remarkable capabilities in numerous applications, yet they possess
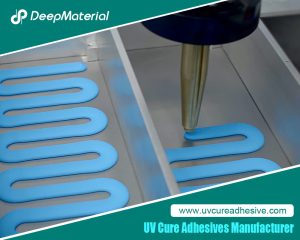
Exploring Potting Compound for Electronics: The Key Material for Providing Reliable Protection to Electronic Products
Exploring Potting Compound for Electronics: The Key Material for Providing Reliable Protection to Electronic Products In the current era of rapid technological development, electronic products have become an indispensable part of our lives. From smartphones, tablets to smart home devices and industrial control systems, the performance and reliability of electronic devices are crucial for
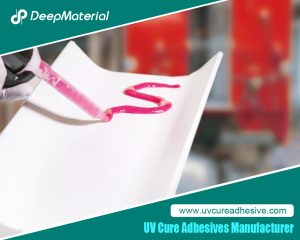
The Wonderful World of UV Curing Potting Compound
The Wonderful World of UV Curing Potting Compound In the rapid development of modern technology, various innovative materials continue to emerge, bringing unprecedented possibilities to applications in various fields. Among them, UV curing potting compound has become a shining star in the field of materials science with its unique performance and wide range of