- Home
- >
- Application
- >
- Digital Battery Adhesive
Digital Battery Adhesive
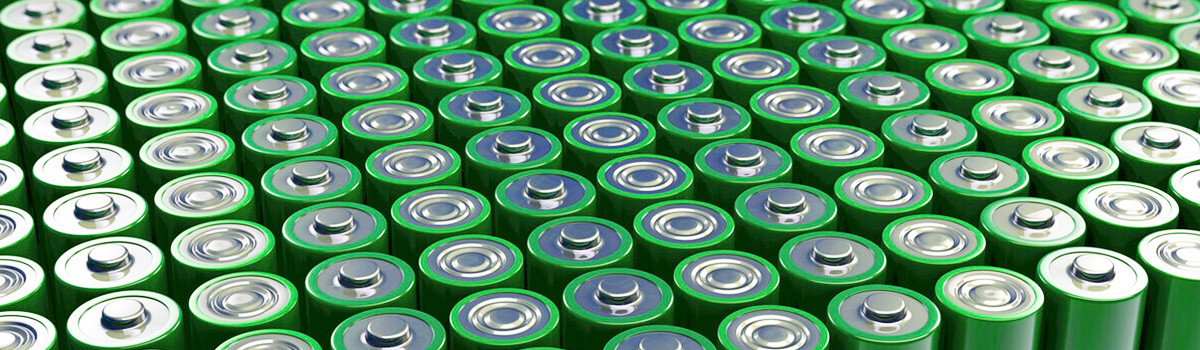
A comprehensive guide on Digital Battery Adhesive, where we delve into the various aspects and questions surrounding this essential component in the digital world. As technology advances, efficient and reliable digital batteries become increasingly critical. Whether you’re a tech enthusiast, a professional in the electronics industry, or simply curious about the ins and outs of digital devices, this guide is designed to provide valuable insights into Digital Battery Adhesive.
Table of Contents
ToggleWhat is digital battery adhesive, and what is its role in electronic devices?
Battery adhesives are used in electronic devices to secure and hold the battery. These adhesives are designed to be solid and durable, providing a reliable bond between the battery and the device’s housing. The adhesive helps prevent the battery from shifting or coming loose during the device’s operation or movement.
The role of a battery adhesive includes:
- Securing the Battery:Adhesives attach the battery to the device’s internal components, ensuring it stays in place during everyday use.
- Vibration Dampening:Electronic devices, especially those with moving parts or that are subject to vibrations, can benefit from adhesives that help dampen vibrations, reducing the risk of internal damage to the battery or other components.
- Space Optimization:Adhesives can be crucial in compact devices with limited space. They allow manufacturers to design machines with tight tolerances and ensure the battery fits securely within the available space.
- Thermal Management:Some battery adhesives are designed to have thermal management properties, helping to dissipate heat generated during the battery’s operation. This can contribute to the overall temperature control and safety of the device.
If “digital battery adhesive” refers to a specific technological advancement or product that emerged after my last update in January 2022, I recommend checking the latest sources, product releases, or industry news for the most up-to-date information.
How Does Digital Battery Adhesive Differ from Traditional Adhesives?
However, based on the context of the term, it’s possible that “digital battery adhesive” could refer to adhesive materials or technologies specifically designed or optimized for use in digital or electronic devices. In general, advancements in adhesive technologies for electronic devices often focus on efficiency, miniaturization, and performance optimization. Here are some potential differences that could be associated with a hypothetical “digital battery adhesive”:
- Precision and Miniaturization:Adhesives designed for digital devices might be formulated to provide strong bonds in tiny spaces, allowing for more compact designs and efficient use of internal space within electronic devices.
- Conductive Properties:Some advanced adhesives for electronic applications may have conductive properties. This could be important for maintaining electrical connectivity within the device or for facilitating grounding and shielding.
- Thermal Management:Digital devices often generate heat during operation. Adhesives optimized for electronic devices may incorporate thermal management properties to help dissipate heat and contribute to overall cooling.
- Compatibility with Electronic Components:The adhesive may be formulated to be compatible with the materials used in electronic components, preventing damage or degradation over time.
- Adhesive Strength and Durability:Given the compact and portable nature of many digital devices, the adhesive might be engineered to provide a strong and durable bond, ensuring that components, including batteries, remain securely in place despite potential impacts or vibrations.
What Are the Primary Components of Digital Battery Adhesive?
The formulations and components of adhesives can vary among manufacturers, and technological advancements may have led to changes since then.
Battery adhesives are designed to securely hold components together within electronic devices, providing stability and preventing movement that could damage delicate components. Some standard features or components of adhesives used in electronic devices, including those associated with batteries, may include:
- Polymer Resins:Adhesives often contain polymer resins contributing to the adhesive’s strength, flexibility, and adhesion properties.
- Solvents or Carriers:These are used to adjust the viscosity of the adhesive and aid in its application. They evaporate during the curing process.
- Fillers:Certain adhesives may contain silica or other materials to enhance properties like thermal conductivity, electrical insulation, or hardness.
- Initiators and Catalysts:These substances promote and control the curing or hardening of the adhesive.
- Modifiers:Additives may be included to modify specific properties of the adhesive, such as improving resistance to temperature extremes, moisture, or chemicals.
- Pressure-Sensitive Adhesives (PSAs):Some battery adhesives may have pressure-sensitive properties, making them easier to apply and providing initial adhesion without needing heat or solvent curing.
- Conductive Materials:In specific applications, adhesives may contain conductive materials to enhance electrical connectivity within the device.
It’s crucial to note that specific formulations can vary based on the intended use, type of battery, and electronic device requirements. Safety and environmental considerations also play a significant role in selecting materials for electronic components. For the most up-to-date and accurate information, it is recommended to consult the technical specifications or contact the manufacturer of the specific battery adhesive in question.
How Does Adhesive Contribute to Battery Performance and Longevity?
Adhesives play a crucial role in the performance and longevity of batteries by providing structural integrity, thermal management, and electrical insulation. Here are several ways in which adhesives contribute to battery performance and longevity:
Structural Integrity:
- Securing Components:Adhesives bond various components of a battery together, ensuring they stay in place and preventing internal movement. This is crucial for maintaining the structural integrity of the battery, especially in portable devices subject to vibrations and shocks.
Thermal Management:
- Heat Dissipation:Adhesives with specific thermal properties can help dissipate heat generated during the operation of the battery. Efficient thermal management prevents overheating, which can degrade battery performance and lifespan.
Protection Against Environmental Factors:
- Sealing and Insulation:Adhesives are often used to seal and insulate batteries from external environmental factors, such as moisture and contaminants. This helps prevent corrosion and maintains the performance of the battery over time.
Vibration and Shock Resistance:
- Impact Absorption:In applications where batteries may experience vibrations or shocks, adhesives can act as a shock absorber, protecting the internal components from damage and extending the battery’s lifespan.
Preventing Electrolyte Leaks:
- Sealing Components:Adhesives create a sealed environment within the battery, preventing electrolyte leaks. This is crucial for safety and ensures that the battery’s internal chemistry remains stable.
Electrical Connectivity:
- Enhancing Contact:Adhesives with conductive properties can enhance electrical contact between components, reducing electrical resistance and improving overall battery performance.
Flexibility and Expansion:
- Flexibility:Some batteries may undergo slight expansion and contraction during charge and discharge cycles. Adhesives with flexible properties can accommodate these movements without compromising the structural integrity of the battery.
Ease of Manufacturing:
- Assembly:Adhesives can simplify the manufacturing process by efficiently attaching and securing components, leading to consistent and reliable battery assembly.
Choosing adhesive materials and formulations is crucial in optimizing these contributions to battery performance. Manufacturers carefully select adhesives based on factors such as the battery chemistry, intended use, and environmental conditions to ensure the best possible performance and longevity for the specific application.
Are There Different Types of Digital Battery Adhesives for Various Devices?
Yes, there are different types of adhesives used in batteries, and the specific type chosen depends on various factors, including the type of device, battery chemistry, performance requirements, and environmental conditions. Here are some common types of adhesives used in batteries for various devices:
Thermal Adhesives:
- Purpose:These adhesives are designed to manage heat by efficiently conducting it away from the battery, preventing overheating.
- Applications:Often used in high-performance or high-temperature applications, such as electric vehicles or high-power electronic devices.
Conductive Adhesives:
- Purpose:Designed to provide both adhesive properties and electrical conductivity.
- Applications are usedin applications where electrical connectivity is critical, such as in certain types of battery connections or devices that require electromagnetic interference (EMI) shielding.
Flexible Adhesives:
- Purpose:Designed to remain flexible after curing, accommodating slight movements and expansions without compromising the structural integrity.
- Applications:Commonly used in batteries for portable devices or wearables where flexibility is essential.
Structural Adhesives:
- Purpose:Provide strong bonding and structural support, ensuring components remain securely attached.
- Applications:Used in various battery types, including those for consumer electronics and industrial equipment.
Pressure-Sensitive Adhesives (PSAs):
- Purpose:Adhesives that provide instant adhesion under slight pressure.
- Applications:Suitable for applications where quick bonding without additional curing or heat is desirable, such as in the assembly of small electronic devices.
Sealants:
- Purpose:Designed to create a secure seal, preventing the ingress of moisture, contaminants, or electrolyte leaks.
- Applications:Commonly used in batteries to protect internal components from environmental factors, contributing to safety and longevity.
Low Outgassing Adhesives:
- Purpose:Minimize the release of volatile substances during curing, which is crucial in applications where outgassing can affect nearby sensitive electronic components.
- Applications:Used in aerospace and high-reliability applications where strict performance and safety standards must be met.
UV-Curing Adhesives:
- Purpose:Cure rapidly when exposed to ultraviolet (UV) light, allowing for faster manufacturing processes.
- Applications:Suitable for applications where quick curing is essential, such as in automated assembly lines.
The choice of adhesive depends on the specific requirements of the device, the type of battery used, and the operating conditions it will encounter. Manufacturers carefully select adhesives to ensure optimal performance, safety, and reliability in their products.
What Factors Should Be Considered When Choosing Digital Battery Adhesive?
Choosing the suitable digital battery adhesive is a critical decision that depends on various factors to ensure optimal performance, safety, and longevity. Here are crucial elements to consider when selecting battery adhesives:
Battery Type:
- Different battery chemistries (e.g., lithium-ion, nickel-metal hydride) have other characteristics and requirements. The adhesive must be compatible with the specific chemistry and materials used in the battery.
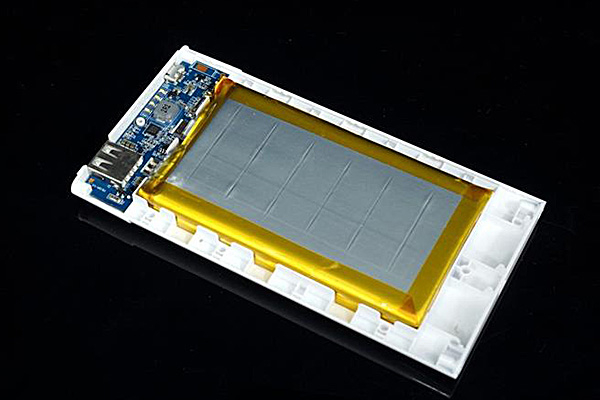
Performance Requirements:
- Consider the performance demands of the device. Factors such as temperature range, mechanical stress, and electrical conductivity requirements will influence the choice of adhesive.
Thermal Properties:
- Evaluate the thermal conductivity and dissipation properties of the adhesive. Efficient thermal management is crucial for preventing overheating and preserving battery life.
Flexibility:
- Depending on the application, the adhesive may need to be flexible to accommodate any expansion or contraction of the battery during charge and discharge cycles.
Adhesion Strength:
- Assess the required bond strength based on the design and mechanical stress the battery may experience. The adhesive should provide a solid and durable bond to ensure the structural integrity of the battery.
Electrical Conductivity:
- In some applications, especially in complex electronic devices, adhesives with good electrical conductivity or specific conductive properties may be necessary to maintain proper electrical connections.
Chemical Compatibility:
- Consider the compatibility of the adhesive with the materials used in the battery and the surrounding components. Ensure that the adhesive is resistant to chemicals or substances that may be present in the device.
Environmental Resistance:
- Evaluate the adhesive’s resistance to environmental factors such as moisture, chemicals, and UV exposure. This is important for maintaining the adhesive’s performance over time.
Safety Considerations:
- Prioritize adhesives that meet safety standards and regulations. This is particularly crucial in applications where safety is a primary concern, such as electric vehicles or medical devices.
Manufacturing Process:
- Consider the manufacturing process and curing requirements. Some adhesives may require specific curing conditions, such as heat or UV light, impacting production efficiency.
Cost:
- Balance performance requirements with cost considerations. While choosing a high-quality adhesive that meets the necessary criteria is essential, cost-effectiveness is also a factor, especially in large-scale manufacturing.
Industry Standards:
- Check if there are industry-specific standards or regulations that the adhesive must comply with. Adhering to industry standards ensures that the battery and device meet quality and safety requirements.
Application Method:
- Consider the ease of application and the chosen method (e.g., dispensing, coating). Some adhesives are designed for specific application techniques, and the preferred method can impact the overall efficiency of the manufacturing process.
By carefully evaluating these factors, manufacturers can select the most suitable adhesive for their specific battery application, ensuring optimal performance and reliability. Consulting with adhesive suppliers or experts in the field can also provide valuable insights into the selection process.
How Does Temperature Affect the Performance of Digital Battery Adhesive?
However, it can give you a general understanding of how temperature affects adhesive materials’ performance, including those used in battery applications.
Viscosity and Flow:
- Low Temperatures:Adhesives become more dense and rigid at low temperatures. This can result in decreased flowability, making applying or spreading the adhesive effectively challenging.
- High Temperatures:High temperatures can reduce the viscosity of adhesives, causing them to become more fluid. This may lead to issues such as dripping or uneven application.
Curing Time:
- Low Temperatures:An adhesive’s curing or setting time may be prolonged in colder temperatures. Slower curing can impact the bonding process and may require more extended periods for the adhesive to achieve its optimal strength.
- High Temperatures:Conversely, higher temperatures can accelerate the curing process. While this might be advantageous for quicker bonding, it can also pose challenges if the adhesive sets too rapidly, potentially leading to inadequate bonding.
Adhesive Strength:
- Low Temperatures:Cold temperatures can sometimes compromise the strength of adhesive bonds. This is particularly relevant for adhesives used in everyday mechanical or thermal stress applications.
- High Temperatures:Elevated temperatures can soften some adhesives, potentially reducing strength. It’s essential to consider the specific temperature range within which the adhesive is designed to perform optimally.
Chemical Stability:
- Low and High Temperatures:Extreme temperatures can affect the chemical stability of adhesives, leading to changes in their composition and properties. This can result in a decrease in overall performance and durability.
It’s crucial to note that the performance of any specific adhesive, including a “digital battery adhesive,” if it exists, would depend on its formulation and intended application. Manufacturers typically provide guidelines regarding the recommended temperature range for the storage, application, and use of their adhesive products.
For accurate and up-to-date information on how temperature affects the performance of a particular adhesive, it is recommended to consult the technical specifications or contact the manufacturer directly.
Is Digital Battery Adhesive Environmentally Friendly?
The environmental friendliness of any material, including digital battery adhesives, depends on various factors, and specific information on a particular product would be needed to provide a precise answer. However, it can provide you with some general considerations regarding the environmental impact of adhesives, and you can use these principles to evaluate the environmental friendliness of a specific digital battery adhesive:
Composition:
- The components and chemicals used in the adhesive formulation play a significant role. Environmentally friendly adhesives often aim to minimize the use of hazardous or toxic substances.
Biodegradability:
- Some adhesives are designed to be biodegradable, meaning they can break down naturally over time, reducing their environmental impact. However, the biodegradability of an adhesive can vary.
Recyclability:
- Adhesives used in electronic devices like digital batteries may be part of complex systems. The recyclability of the entire product, including the adhesive, contributes to environmental friendliness.
VOC Emissions:
- Volatile Organic Compounds (VOCs) can vaporize into the air. Environmentally friendly adhesives often aim to minimize VOC emissions, as these can contribute to air pollution.
Energy Consumption:
- The manufacturing process of adhesives can have an environmental impact. Adhesives produced using energy-efficient processes or renewable energy sources may be more environmentally friendly.
End-of-Life Considerations:
- The disposal and end-of-life management of products containing the adhesive are essential. Adhesives that do not pose significant environmental risks during disposal are generally more environmentally friendly.
Certifications and Standards:
- Look for certifications or compliance with environmental standards. Some adhesives may adhere to specific criteria set by organizations or regulatory bodies focusing on ecological sustainability.
To determine the environmental friendliness of a digital battery adhesive, you may need to refer to the product’s technical specifications, safety data sheets, or information provided by the manufacturer. Companies that prioritize environmental sustainability often highlight these aspects in their product documentation. Additionally, industry certifications such as Green Seal or the European Eco-label may provide indications of a product’s environmental credentials.
Can Digital Battery Adhesive Be Used for DIY Battery Replacements?
Digital battery adhesive, often referred to as adhesive strips or stickers, is designed to secure batteries in electronic devices like smartphones, tablets, or laptops. While it’s specifically manufactured for such purposes, using it for DIY battery replacements depends on the context and the type of battery you are dealing with.
If you are replacing the battery in a device for which digital battery adhesive is designed, it can be used for DIY battery replacements. These adhesive strips are typically used to attach the battery securely to the device’s housing, ensuring it stays in place during use and prevents any movement that could damage the battery or other components.
However, it’s crucial to note that different devices and batteries may have additional requirements. Some batteries may not need adhesive strips, and instead, they could be held in place by screws or other mechanisms. Additionally, sure batteries might come with their adhesive pre-applied.
Here are some general guidelines if you’re considering using digital battery adhesive for a DIY battery replacement:
- Compatibility:Ensure the adhesive is compatible with the specific battery and device you are working on.
- Clean Surface:Before applying the adhesive, ensure the surface is clean and free of any residue from the old glue.
- Positioning:Apply the adhesive carefully, following any guidelines or markings provided by the device manufacturer.
- Instructions:If you’re using a battery replacement kit, follow the included instructions carefully. If you’re using separate adhesive strips, ensure that you cut them to the correct size and shape for your device.
Always refer to the manufacturer’s guidelines for the specific device and battery you are working on. Suppose you need more certainty or comfort with the process. In that case, it’s advisable to seek professional assistance or use a certified battery replacement service to ensure the safety and functionality of your device.
What Innovations Are Emerging in the Field of Digital Battery Adhesive?
Provide you with some general trends and potential areas of innovation that were relevant in the broader field of battery technology up to that point. Keep in mind that developments may have occurred since then:
Smart Adhesives:
- Integration of sensors and intelligent functionalities directly into battery adhesives. This could include sensors for monitoring temperature, pressure, or the state of charge. Innovative adhesives could enable real-time data collection and communication about the battery’s performance.
Responsive Adhesives:
- Adhesives that respond to environmental conditions or external stimuli. For example, adhesives that change properties in response to temperature variations, pressure, or electrical currents. This adaptability could enhance the performance and reliability of batteries in different operating conditions.
Improved Thermal Management:
- Innovations in digital battery adhesives may focus on enhancing thermal conductivity and management. This is particularly important in high-performance batteries where efficient heat dissipation is crucial for safety and performance.
Advanced Materials for Flexibility:
- Development of adhesive materials that maintain their properties in flexible and stretchable electronic devices. This is essential for applications such as wearable technology and flexible electronics.
Digital Manufacturing Techniques:
- Integration of digital manufacturing technologies, such as additive manufacturing or 3D printing, in the application of battery adhesives. This could lead to more precise and customized application methods, potentially reducing waste and improving efficiency.
Environmental Sustainability:
- Innovations in adhesive materials with a focus on sustainability. This could involve the use of eco-friendly materials, reduced environmental impact during manufacturing, and adhesives designed for easy recycling or disposal.
Automation in Application Processes:
- Advances in automated processes for applying battery adhesives during manufacturing. Automation can lead to more consistent application, reducing variability in battery performance and improving overall quality.
Enhanced Safety Features:
- Integrating safety features directly into the adhesive, such as materials that can act as barriers to prevent or mitigate thermal runaway reactions in batteries.
To get the most up-to-date information on emerging innovations in digital battery adhesive technology, I recommend checking recent scientific literature, industry publications, and news sources for the latest research and developments in battery technology and materials.
How Does Digital Battery Adhesive Impact the Recycling of Electronic Devices?
Provide insights into how advancements in battery adhesive technology, including potential digital aspects, might influence electronic device recycling:
Ease of Disassembly:
- Digital battery adhesive technologies could facilitate easier disassembly of electronic devices during recycling. Adhesives that can be digitally activated or deactivated might simplify separating battery components from other device parts.
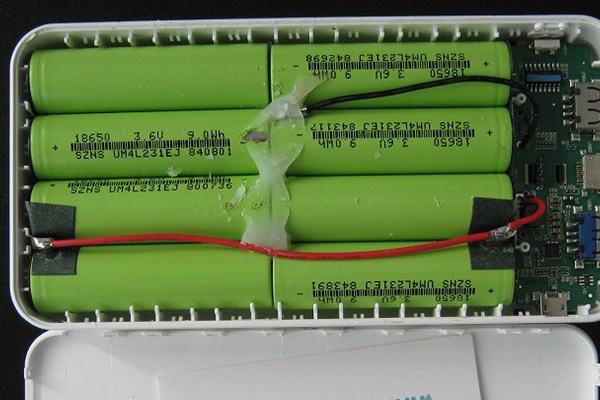
Identification and Sorting:
- Digital features within battery adhesives could be used for identification purposes. For instance, unique digital markers or RFID (Radio-Frequency Identification) tags integrated into adhesives help in the automated sorting of devices during recycling, ensuring that batteries are correctly identified and separated.
Condition Monitoring:
- Innovative adhesives with embedded sensors could provide real-time information about the condition of batteries. This data could help recycling facilities assess the state of batteries before disassembly, helping them make informed decisions about reusing or recycling specific components.
Recyclability of Adhesive Materials:
- Innovations in battery adhesive materials may also focus on recyclability. Adhesives that are easier to separate from other materials or that can be recycled alongside other components could contribute to more sustainable recycling processes.
Reducing Contamination:
- If digital battery adhesive technologies can enhance the precision of application and removal, there is potential to reduce contamination during the recycling process. This is crucial for maintaining the quality of recycled materials.
Enhanced Battery Recovery:
- Digital features enable more efficient and targeted recovery of batteries during the recycling process. This could lead to increased recovery rates of valuable materials from batteries, improving the overall sustainability of electronic waste recycling.
The impact of digital battery adhesive technologies on recycling is likely to be part of a broader trend toward designing electronics with easier recyclability and better sustainability. For the latest developments in this field, it’s recommended to check recent publications, industry news, and research articles for updates on digital adhesive technologies and their impact on electronic device recycling.
Are There Safety Concerns Associated with Digital Battery Adhesive?
However, it’s essential to note that the safety considerations associated with any adhesive used in electronic devices, whether traditional or digital, are critical and should be thoroughly addressed during the design and manufacturing processes. Here are some general safety concerns that could be relevant to digital battery adhesive:
Thermal Stability:
- Adhesives play a role in the thermal management of batteries. Ensuring that digital battery adhesives can withstand high temperatures without degradation is crucial for the overall safety of the battery.
Compatibility with Battery Chemistry:
- Different battery chemistries may require specific adhesives. It’s essential to ensure that the chosen adhesive is compatible with the materials used in the battery and does not lead to chemical reactions that could compromise safety.
Adhesive Integrity:
- The integrity of the adhesive over time is crucial. Any degradation or loss of adhesion could lead to mechanical failure of the battery components, potentially resulting in safety hazards.
Electronic Components Integration:
- If digital functionalities are integrated into the adhesive, ensuring that these electronic components do not pose safety risks, such as short circuits or electromagnetic interference, is essential.
Environmental Impact:
- Consideration of the environmental impact of the adhesive, mainly if it contains hazardous materials. This is important not only during the use of the device but also during manufacturing and end-of-life disposal or recycling.
User Interaction:
- If the digital features in the adhesive involve user interaction, there should be considerations for user safety. For example, if the adhesive has sensors, there should be mechanisms to prevent unintended user exposure to electrical components.
Manufacturers must conduct thorough testing and adhere to safety standards while developing and implementing digital battery adhesive technologies. The specific safety concerns may vary depending on the type of technology, the application, and the intended use of the electronic devices.
For the latest information on this topic, including any safety concerns related to digital battery adhesives, it is recommended to check recent research publications, industry guidelines, and updates from relevant regulatory bodies.
Can Digital Battery Adhesive Be Applied to Different Battery Chemistries?
The choice of battery adhesive depends on various factors, and selecting the suitable adhesive for the specific battery chemistry is crucial. Different battery chemistries have distinct characteristics, and using the wrong adhesive may lead to compatibility issues, reduced performance, or even safety risks.
Standard battery chemistries include lithium-ion (Li-ion), nickel-metal hydride (NiMH), nickel-cadmium (NiCd), and alkaline batteries. Each chemistry has unique voltage, current, temperature, and chemical compatibility requirements.
Digital battery adhesives are designed to provide secure attachment and electrical insulation for batteries in electronic devices. They often must withstand the conditions inside the battery compartment, such as temperature variations, vibrations, and potential chemical exposure.
Before applying a digital battery adhesive, check the manufacturer’s specifications and recommendations for compatibility with different battery chemistries. Some adhesives may be specifically formulated for specific battery types, ensuring optimal performance and safety.
In summary, while digital battery adhesives can be suitable for various battery chemistries, verifying compatibility with the specific type of battery you are using is essential. Always follow the manufacturer’s guidelines and recommendations to ensure proper bonding and electrical insulation without compromising the performance or safety of the batteries.
What Are the Challenges in Manufacturing High-Quality Digital Battery Adhesives?
Manufacturing high-quality digital battery adhesives comes with several challenges due to the demanding requirements of their applications. Here are some of the critical challenges associated with producing high-quality digital battery adhesives:
Chemical Compatibility: Battery adhesives must be compatible with the chemicals in different battery types, such as lithium-ion, nickel-metal hydride, and alkaline batteries. The adhesive formulation must resist chemical degradation over time to maintain its integrity and performance.
Temperature Resistance: Batteries can generate heat during operation, and adhesives must withstand a wide range of temperatures without losing their adhesive properties or causing damage to the battery. Extreme temperatures can affect the adhesive’s bonding strength and electrical insulation.
Electrical Insulation Properties: Digital battery adhesives must provide effective electrical insulation to prevent short circuits and ensure the proper functioning of electronic devices. Maintaining consistent insulation properties over time and under various environmental conditions is crucial.
Mechanical Strength: Adhesives must offer sufficient mechanical strength to the battery securely within the device. Vibrations, shocks, and other mechanical stresses should not compromise the adhesive bond, ensuring the battery remains in place throughout the device’s lifecycle.
Adhesive Application Process: Achieving uniform and precise adhesive application is essential for consistent product quality. Manufacturing processes must be optimized to apply the adhesive accurately in the right amount and distribution.
Curing Time and Process: The adhesive’s curing time can impact production efficiency. Balancing the need for a quick curing process with ensuring that the adhesive has adequate time to bond correctly is a challenge.
Regulatory Compliance: Adhesive formulations must comply with industry and environmental regulations. Meeting safety standards and environmental requirements complicate the formulation and production processes.
Long-Term Stability: Adhesives should maintain their properties over the long term. Stability over time is critical to ensure the adhesive continues to perform well throughout the product’s lifespan.
Cost Considerations: Balancing the cost of production with the need for high-quality materials and processes is an ongoing challenge. Manufacturers must find ways to optimize the production process without compromising the performance of the adhesive.
Addressing these challenges requires collaboration between material scientists, chemists, and manufacturing experts to develop formulations and processes that meet the stringent requirements of digital battery adhesives. Continuous research and development are essential to stay ahead of technological advancements and industry standards.
How Does Digital Battery Adhesive Contribute to Device Design and Form Factor?
Digital battery adhesive, or simply adhesive used in the assembly of digital batteries, plays a crucial role in the overall device design and form factor. The form factor refers to the physical dimensions and specifications of a device, and the choice of adhesive can impact this in several ways:
Space Optimization:
- Digital battery adhesives can be engineered to be very thin and still provide strong bonding. This allows for more compact designs, enabling manufacturers to optimize internal space within a device. As a result, machines can be made smaller and lighter without compromising structural integrity.
Flexible Design:
- Some adhesives are more flexible than others, allowing for the creating of devices with curved or flexible form factors. This is particularly important in the design of wearable devices, foldable smartphones, and other innovative form factors.
Heat Dissipation:
- The choice of adhesive can impact the thermal conductivity of a device. Some adhesives are designed to dissipate heat efficiently, contributing to the thermal management of the device. This is crucial for high-performance devices, preventing overheating and ensuring optimal functioning.
Waterproofing and Durability:
- Adhesives can be formulated to provide a waterproof seal, protecting internal components from moisture and enhancing the device’s overall durability. This is important in machines exposed to harsh environmental conditions or used in outdoor settings.
Ease of Assembly:
- Digital battery adhesives that are easy to work with can streamline manufacturing. They may facilitate automated assembly processes, reducing production time and costs. This is especially relevant in mass production scenarios.
Vibration Damping:
- In some devices, especially those with moving parts or subject to vibrations, the adhesive can dampen vibrations. This helps reduce wear and tear on internal components and enhances the device’s overall reliability.
Aesthetics:
- The adhesive also impacts the appearance of a device. Transparent adhesives or those with specific optical properties can contribute to a sleek and visually appealing design, especially in devices with glass or delicate components.
Battery Integration:
- Adhesives are crucial in securely attaching the battery to the device chassis. The strength and reliability of this bond are essential for the overall structural integrity of the device.
In summary, the choice of digital battery adhesive is a critical consideration in device design, influencing the end product’s form factor, durability, flexibility, and overall performance. Manufacturers carefully select adhesives based on the specific requirements of their devices and the user experience they aim to deliver.
What Role Does Adhesive Technology Play in Wearable Device Batteries?
Adhesive technology plays a significant role in wearable device batteries, contributing to these devices’ overall performance, durability, and form factor. Here are several key roles that adhesive technology plays in wearable device batteries:
Flexibility and Form Factor:
- Wearable devices often have unique and flexible form factors. Adhesives allow for the secure bonding of batteries to flexible substrates, creating thin, lightweight, and bendable devices. This is crucial for wearables like smartwatches, fitness trackers, and health monitoring devices.
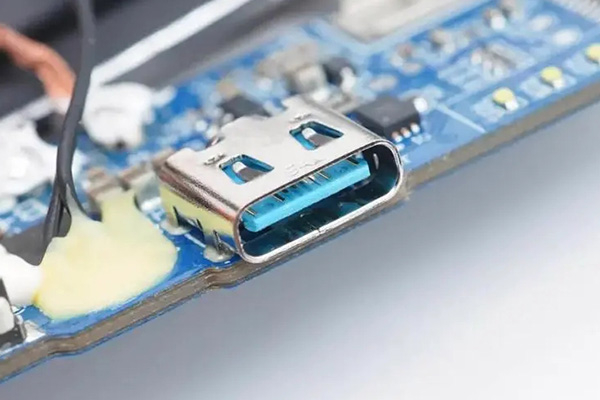
Water Resistance:
- Wearable devices are frequently exposed to sweat and other environmental factors. Adhesive technologies can provide water-resistant and even waterproof seals, protecting the batteries from moisture. This is essential for maintaining the functionality and longevity of wearable devices.
Skin-Friendly Adhesives:
- Some wearables, particularly those designed for health monitoring, may come into direct contact with the skin. Adhesives used in these devices need to be skin-friendly, hypoallergenic, and free from harmful substances to ensure user comfort and safety.
Vibration and Shock Resistance:
- Wearable devices are often subject to movement, impacts, and vibrations, especially during physical activities. Adhesive technologies can be tailored to provide strong bonding that resists shocks and vibrations, ensuring the stable integration of batteries in dynamic usage scenarios.
Thermal Management:
- Wearable devices can generate heat, particularly those with sensors and continuous monitoring capabilities. Adhesives with good thermal conductivity help dissipate heat efficiently, preventing overheating and maintaining optimal device performance.
Low Profile and Thin Designs:
- Wearables are generally designed to be discreet and comfortable. Adhesives that allow for low-profile and thin battery integration contribute to these devices’ overall sleekness and wearability.
Ease of Manufacturing:
- Adhesive technologies that are easy to apply and integrate into the manufacturing process contribute to the efficiency of wearable device production. This is particularly important in high-volume manufacturing, where streamlined processes are essential.
Biocompatibility:
- For wearables that come in direct contact with the skin or may be implanted, biocompatible adhesives are crucial to prevent skin irritation or adverse reactions. Biocompatible adhesives are designed to be safe for prolonged skin contact without causing harm.
Battery Attachment and Encapsulation:
- Adhesives are used to securely attach batteries to the wearable device’s housing or chassis. Additionally, they may be employed in the encapsulation process, providing a protective layer around the battery to enhance safety and prevent damage.
Adhesive technology plays a multifaceted role in wearable device batteries, addressing challenges related to flexibility, water resistance, durability, thermal management, and user comfort. Manufacturers of wearable devices carefully choose adhesive materials and formulations based on the specific requirements of their products and the user experience they aim to deliver.
Are There Regulations and Standards Governing Digital Battery Adhesive?
No regulations or standards specifically for digital battery adhesives were widely recognized or mandated. However, it’s essential to note that rules and standards can change, and new ones may have been introduced since then.
Some general regulations and standards may apply in electronics and batteries, especially regarding safety, environmental impact, and product labeling. For instance:
- Safety Standards:Products containing batteries often must adhere to safety standards to ensure they don’t pose risks like fire or explosion. These standards may vary by region or country.
- Environmental Regulations:Depending on the materials used in the adhesive and the batteries’ disposal, ecological regulations may need to be followed.
- Consumer Product Regulations:Regulations related to consumer products, including electronic devices, may have requirements that indirectly apply to the components used in these products.
- Industry Standards:Industry organizations may establish standards for specific components or aspects of electronic devices.
To get the most accurate and up-to-date information, it’s recommended to check with relevant regulatory bodies in the specific region where the product is being manufactured, sold, or used. Additionally, manufacturers and designers should stay informed about any changes in standards that may impact their products.
How Can Consumers Extend the Lifespan of Digital Batteries Using Adhesives?
Various factors can influence the lifespan of digital batteries, and while adhesives themselves may not directly impact battery life, proper use and maintenance of electronic devices, which may involve adhesives, can contribute to extending battery lifespan. Here are some general tips:
Avoid Extreme Temperatures:
- High temperatures can accelerate the degradation of battery materials. Avoid exposing your device to extreme heat, and store it in a cool, dry place.
Proper Charging Practices:
- Follow the manufacturer’s guidelines for charging your device. Overcharging or consistently draining the battery to deficient levels can impact its longevity. Most modern devices are equipped with technologies to prevent overcharging, but it’s still a good practice to unplug the device once fully charged.
Use Original or Compatible Accessories:
- Ensure that you use original or compatible charging cables and adapters. Using substandard or counterfeit accessories may affect the charging process and, consequently, the battery.
Firmware/Software Updates:
- Keep your device’s firmware and software up-to-date. Manufacturers often release updates that can include optimizations for battery performance.
Optimize Settings:
- Adjust your device’s settings to optimize battery life. For example, reduce screen brightness, turn off unnecessary background processes, and manage location services.
Regular Maintenance:
- Periodically check for software updates and app updates. Outdated software or poorly optimized apps can sometimes cause excessive battery drain.
Proper Adhesive Use:
- While adhesives won’t extend battery life, proper assembly and sealing of devices can help prevent environmental factors (like moisture) from affecting the internal components, indirectly contributing to the battery’s longevity.
Avoid Physical Stress:
- Handle your device with care to avoid physical stress on the battery. Dropping or subjecting the device to impact can damage the battery and reduce lifespan.
Battery Calibration:
- Some devices benefit from occasional battery calibration. This involves fully charging and then fully discharging the battery. Check your device’s manual or support documentation for guidance on calibration procedures.
Remember that digital batteries have a finite lifespan and will eventually need to be replaced. If you notice a significant decrease in battery performance or overall lifespan, it might indicate that the battery needs replacement. Always refer to the manufacturer’s guidelines for specific recommendations related to your device.
What research and development efforts are invested in improving digital battery adhesiveness?
However, advancements in electronic devices and batteries are continually being pursued by researchers, engineers, and manufacturers. Some areas where research and development efforts may be focused include:
Adhesive Materials:
- Researchers may develop new adhesive materials with improved properties, such as enhanced conductivity, better heat dissipation, and increased durability. These materials aim to ensure the secure and efficient bonding of battery components.
Environmentally Friendly Adhesives:
- There is a growing emphasis on developing environmentally friendly and sustainable adhesives. Researchers may explore alternatives to traditional adhesives that reduce environmental impact during production, usage, and disposal.
Thermal Management:
- Enhanced thermal management is crucial for electronic devices, including batteries. Research efforts may be directed towards adhesives that can help dissipate heat more efficiently, thus improving the overall thermal performance of the battery.
Flexible and Wearable Electronics:
- With the rise of flexible and wearable electronics, research into adhesives specifically designed for these applications could exist. These adhesives need to be flexible, lightweight, and durable to accommodate the unique form factors of such devices.
Integration with Advanced Battery Technologies:
- As battery technologies evolve, adhesives may need to be developed or modified to accommodate new types of batteries, such as solid-state batteries or advanced lithium-ion battery designs.
Smart Adhesives:
- Research may focus on creating “smart” adhesives that adapt to different conditions. This could involve adhesives with self-healing properties or those that can respond to changes in temperature or pressure.
Manufacturing Processes:
- Optimization of manufacturing processes related to the application of adhesives is an ongoing area of research. This includes developing more efficient and cost-effective methods for applying adhesives to electronic components.
For the latest and specific information on research and development efforts in this field, it is recommended to review recent academic publications, industry conferences, and news from relevant research institutions and companies involved in electronics and battery technologies. Advances in digital battery adhesiveness will likely be part of broader research initiatives in materials science, electronics, and energy storage.
Are there alternative solutions to digital battery adhesiveness in powering electronic devices?
While adhesives are commonly used in assembling and packaging electronic devices, they are not directly involved in powering the devices. The role of adhesives is typically to secure and seal components rather than contribute to the energy supply. The primary power sources for electronic devices are batteries and, in some cases, external power sources. However, there are alternative and emerging technologies and methods related to power sources for electronic devices:
Alternative Battery Technologies:
- Researchers continually explore alternative battery technologies to improve energy density, charging times, and overall performance. This includes developments in solid-state batteries, lithium-sulfur batteries, and other advanced chemistries.
Energy Harvesting:
- Energy harvesting technologies aim to capture ambient energy from the surrounding environment and convert it into electrical power. This can include harvesting energy from solar power, kinetic energy (vibration or motion), thermal energy, or radiofrequency (RF) signals.
Wireless Charging:
- Wireless charging technology allows electronic devices to be charged without physical connectors. Devices are placed on a charging pad or within a designated charging area, transferring power wirelessly. This technology is becoming increasingly common for smartphones, smartwatches, and other portable devices.
Flexible and Stretchable Electronics:
- Advancements in flexible and stretchable electronics enable the development of wearable devices that can conform to the body’s shape. These devices often incorporate loose batteries and can be integrated into clothing or worn as patches.
Supercapacitors:
- Supercapacitors, or ultracapacitors, are energy storage devices that can deliver rapid bursts of power and have a longer cycle life than traditional batteries. They are suitable for applications requiring quick energy discharge and recharge.
Hybrid Systems:
- Some electronic devices use a combination of power sources to optimize performance. For example, a device may have a primary battery and an energy-harvesting component to extend battery life.
Fuel Cells:
- Fuel cells generate electricity through chemical reactions, typically involving hydrogen and oxygen. While not widely used in consumer electronics, fuel cells are being explored as potential power sources for specific applications.
Bioenergy Harvesting:
- Research is ongoing in bioenergy harvesting, which involves harnessing energy from biological sources. For instance, devices could be powered by converting glucose in the bloodstream into electrical energy.
It’s important to note that the choice of power source depends on the specific requirements of the device and its intended use. As technology advances, we can expect further innovations in the power sources for electronic instruments.
Conclusion:
In conclusion, Digital Battery Adhesive is a crucial element in the world of electronics, influencing the performance, sustainability, and design of digital devices. As technology continues to evolve, exploring these questions will deepen our understanding of Digital Battery Adhesive’s role in powering the digital landscape. Stay informed, stay connected, and power up with confidence in the digital age.
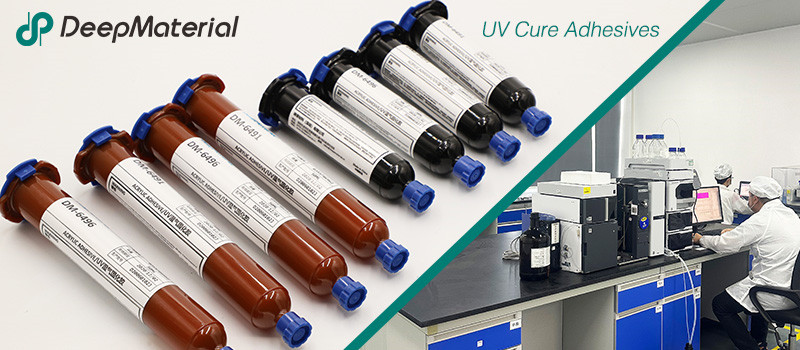
DeepMaterial
Based on the core technology of adhesives, DeepMaterial has developed adhesives for chip packaging and testing, circuit board level adhesives, and adhesives for electronic products. Based on adhesives, it has developed protective films, semiconductor fillers, and packaging materials for semiconductor wafer processing and chip packaging and testing. More…
UV Curing Adhesives
UV light cure have a number of benefits making them a popular choice among many product assembly and manufacturing applications. Many UV light cure adhesives can provide a nearly instantaneous bond to difficult substrates like glass and plastic. UV cure adhesives often require an accelerator or UV light for a bond to form.
Adhesive Blogs & News
The latest adhesive industry science and technology, Deepmaterial news, and market trends and forecasts.
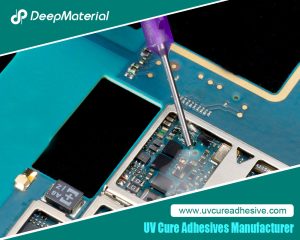
Technical Strategies for Balancing the Rapid Curing Property and Long Operating Time of UV Adhesives
Technical Strategies for Balancing the Rapid Curing Property and Long Operating Time of UV Adhesives UV adhesives have been widely used in many fields such as electronics, optics, and medicine due to their advantages of rapid curing, high bonding strength, and environmental protection. However, their rapid curing property also brings challenges in some application scenarios.
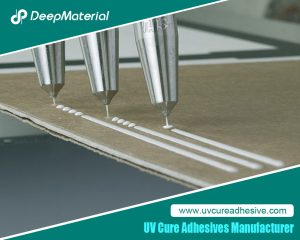
Biocompatibility of LED UV Glue Adhesive and Its Application Potential in Medical and Food Packaging Fields
Biocompatibility of LED UV Glue Adhesive and Its Application Potential in Medical and Food Packaging Fields LED UV glue adhesive has been widely applied in numerous fields due to its advantages such as rapid curing and easy operation. However, in fields with stringent safety requirements like medical and food packaging, its biocompatibility after curing
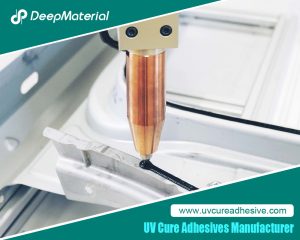
Exploring the Environmental Performance of UV Glue and Strategies for Optimizing Odor and VOC Content
Exploring the Environmental Performance of UV Glue and Strategies for Optimizing Odor and VOC Content UV glue, as an adhesive that achieves rapid curing through ultraviolet (UV) light irradiation, has been widely applied in numerous fields such as electronics, optics, healthcare, and automobiles, thanks to its advantages of fast curing speed, high bonding strength, and
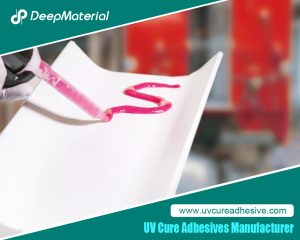
Compatibility Analysis and Countermeasures of LED UV Glue with Automated Production Equipment
Compatibility Analysis and Countermeasures of LED UV Glue with Automated Production Equipment LED UV glue has been widely used in modern manufacturing due to its advantages such as fast curing speed, high bonding strength, and environmental friendliness. However, in the automated production process, if there are problems with the adaptability between the glue and equipment
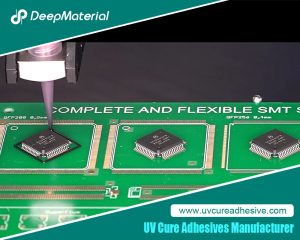
Influence of Viscosity and Thixotropy of Glue on the Quality of Glue Dots in the Dispensing Process and Solutions
Influence of Viscosity and Thixotropy of Glue on the Quality of Glue Dots in the Dispensing Process and Solutions The dispensing process is an important part of the application of LED UV glue adhesive, and the quality of this process directly affects the final performance of the product. The physical properties of the glue,
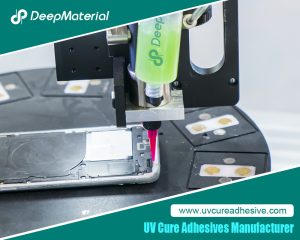
Aging Mechanism and Modification Strategies of LED UV Glue under Long-term Ultraviolet Irradiation
Aging Mechanism and Modification Strategies of LED UV Glue under Long-term Ultraviolet Irradiation LED UV glue, with its advantages of fast curing speed, high bonding strength, and environmental friendliness, has been widely used in fields such as optical device packaging, electronic assembly, and medical devices. However, in scenarios where it is exposed to ultraviolet environments