- Home
- >
- Application
- >
- Consumer Electronics Adhesive
Consumer Electronics Adhesive
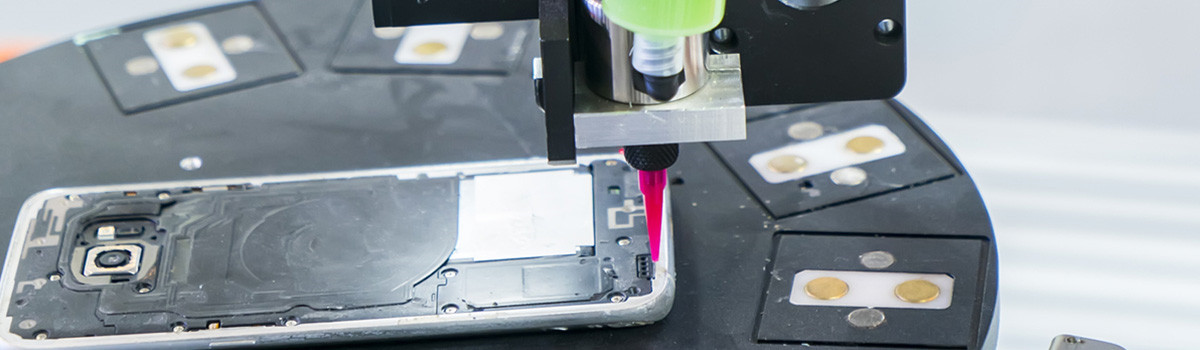
As technology advances, the demand for reliable and efficient adhesives to enhance the performance and longevity of consumer electronics is on the rise. Whether you’re a tech enthusiast, a DIY electronics hobbyist, or a professional, this page aims to provide valuable insights into various aspects of Consumer Electronics Adhesive.
Table of Contents
ToggleWhat is Consumer Electronics Adhesive?
Consumer Electronics Adhesive refers to adhesives designed and formulated for consumer electronic devices. These adhesives play a crucial role in assembling and manufacturing various electronic products. They bond different components together, provide structural support, offer thermal management, and ensure electronic devices’ overall reliability and durability.
Consumer electronics adhesives need to meet specific requirements due to the unique challenges of electronic applications. Some common characteristics and features of these adhesives include:
- Bonding Strength:Consumer electronics adhesives must provide solid and reliable bonds to hold components together securely. This is important for the structural integrity of the device.
- Thermal Conductivity:Many electronic devices generate heat during operation, and efficient thermal management is essential for preventing overheating. Some adhesives are formulated to conduct heat away from sensitive components.
- Electrical Insulation:Adhesives used in electronic applications should insulate against electrical currents to prevent short circuits and other electrical issues.
- Flexibility:Consumer electronics often have compact and intricate designs, and adhesives must be flexible to accommodate movements or vibrations without compromising the bond.
- Chemical Compatibility:Adhesives should be compatible with the materials used in electronic components to avoid any adverse reactions that could lead to degradation or malfunction.
- Low Outgassing:Outgassing refers to releasing volatile substances from the adhesive over time. Low outgassing is crucial in consumer electronics, especially in enclosed spaces, to prevent contamination of sensitive components like lenses or sensors.
- Fast Curing Time:In manufacturing processes, quick curing times are often desirable to increase efficiency and reduce production time.
The types of adhesives used in consumer electronics can vary, including epoxy adhesives, cyanoacrylate adhesives, silicone adhesives, and other specialty formulations. The choice of adhesive depends on the application’s specific requirements, the materials being bonded, and the manufacturing processes involved. Manufacturers often work closely with suppliers to select the most suitable adhesive for their electronic devices.
Why is adhesive crucial in consumer electronics manufacturing?
Adhesives play a crucial role in consumer electronics manufacturing for several reasons:
- Assembly and Bonding:Adhesives are used to bond different components together during the assembly process. This is important for creating a solid and reliable structure for electronic devices.
- Miniaturization:As consumer electronics continue to become smaller and more compact, traditional mechanical fastening methods like screws and bolts may not be practical. Adhesives provide a lightweight and efficient solution for bonding small and intricate components.
- Weight Reduction:Adhesives are generally lighter than traditional mechanical fasteners, contributing to overall weight reduction in electronic devices. This is particularly important in industries where lightweight and portable products are desirable, such as smartphones and tablets.
- Vibration Dampening:Electronic devices often generate vibrations during operation. Adhesives can help dampen these vibrations, preventing damage to delicate components and improving the product’s overall durability.
- Sealing and Insulating:Adhesives can be formulated to provide sealing and insulating properties. This protects electronic components from environmental factors such as moisture, dust, and chemicals. It also helps prevent short circuits and enhance longevity.
- Considerations:Adhesives can be aesthetically pleasing without visible fasteners. This is important for consumer electronics, where design and appearance are critical to product success.
- Conductivity and Heat Dissipation:Some adhesives are formulated to conduct heat away from electronic components. This is important in preventing overheating and maintaining the optimal operating conditions for electronic devices.
- Flexibility:Adhesives can provide flexibility in design, allowing manufacturers to bond dissimilar materials or materials with different coefficients of thermal expansion. This flexibility is essential in designing innovative and efficient electronic devices.
- Cost Efficiency:Adhesives can be cost-effective in terms of both materials and labor. Automating adhesive application processes can contribute to faster and more economical manufacturing.
- Environmental Considerations:Certain adhesive formulations are environmentally friendly, which aligns with the growing trend of sustainable and eco-friendly manufacturing practices.
Adhesives offer a versatile and efficient solution for various challenges in consumer electronics manufacturing, ranging from structural integrity and miniaturization to environmental protection and aesthetics.
How does Consumer Electronics Adhesive contribute to device durability?
Consumer Electronics Adhesives play a crucial role in enhancing the durability and performance of electronic devices. Here are several ways in which these adhesives contribute to device durability:
Structural Integrity:
- Consumer Electronics Adhesives bond various components together, providing structural support to the device. This helps maintain the device’s overall integrity, especially in the case of slim and compact designs.
Vibration and Shock Absorption:
- Devices, especially portable ones, are subjected to vibrations and shocks during regular use. Adhesives help in dampening these vibrations, preventing internal components from shifting or getting damaged. This is particularly important for handheld devices in automotive or industrial settings.
Sealing and Water Resistance:
- Adhesives are often used to seal the electronic components and create a barrier against moisture and other environmental factors. This protects sensitive electronics from water damage, significantly impacting device performance and lifespan.
Thermal Management:
- Adhesives with thermal conductivity properties bond heat-generating components like processors and batteries to heat sinks or other thermal management structures. This helps in efficient heat dissipation, preventing overheating and ensuring optimal performance over an extended period.
Flexibility and Stress Relief:
- In devices with moving parts or flexible displays, adhesives can provide flexibility and stress relief. This is important in preventing mechanical failure due to repeated bending or flexing, especially in devices like foldable smartphones.
Electrical Insulation:
- Adhesives protect electrical connections from moisture, dust, and other contaminants. This insulation helps prevent short circuits and electrical malfunctions from exposure to external elements.
Chemical Resistance:
- Some Consumer Electronics Adhesives resist chemicals and solvents, providing additional protection against corrosive substances that could damage internal components.
Enhanced Manufacturing Processes:
- Adhesives can simplify the manufacturing process by allowing for automation, reducing the need for mechanical fasteners, and enabling the assembly of intricate and compact designs. This can contribute to the overall efficiency and reliability of the manufacturing process.
Consumer Electronics Adhesives contribute to device durability by providing structural support, enhancing resistance to environmental factors, managing heat, ensuring electrical insulation, and facilitating manufacturing of robust and reliable electronic products. The specific type of adhesive and its application depend on the design and requirements of the electronic device.
Are there different types of adhesives used in consumer electronics?
Yes, various types of adhesives are used in consumer electronics, each tailored to specific applications and requirements. The choice of adhesive depends on factors such as the bonded materials, the environmental conditions the device will be exposed to, the manufacturing processes, and the desired performance characteristics. Here are some common types of adhesives used in consumer electronics:
Epoxy Adhesives:
- These adhesives provide strong bonding and are often used for structural applications. They are known for their high strength, durability, and chemical resistance. Epoxy adhesives are commonly used in bonding metal, glass, and rigid plastics.
Cyanoacrylate (Super Glue):
- Cyanoacrylate adhesives are fast-bonding and provide excellent adhesion for various materials, including plastics, rubber, and metals. They are often used for quick assembly and bonding of small electronic components.
Acrylic Adhesives:
- Acrylic adhesives offer a good balance of strength and flexibility. They are commonly used for bonding plastics and metals. Acrylic adhesives also provide good resistance to environmental factors and are often used in applications requiring transparency.
Polyurethane Adhesives:
- Polyurethane adhesives offer flexibility and are resistant to impact and vibration. They are suitable for bonding dissimilar materials and are commonly used in devices requiring some degree of flexibility.
Silicone Adhesives:
- Silicone adhesives are known for their flexibility, resistance to extreme temperatures, and excellent sealing properties. They are often used for applications where there is a need for thermal management and moisture resistance.
Thermal Interface Materials (TIMs):
- TIMs are a specialized adhesive for efficient heat transfer between electronic components and heat sinks. They are crucial for thermal management in electronic devices, helping to dissipate heat and prevent overheating.
Conductive Adhesives:
- Conductive adhesives contain conductive particles and create electrical connections instead of soldering. They are employed in applications where a flexible electrical contact is needed, such as in flexible circuits and some wearable devices.
Pressure-Sensitive Adhesives (PSAs):
- PSAs are adhesives that bond instantly under light pressure. They are commonly used in applications like attaching displays, touchscreens, and protective films to electronic devices.
Hot-Melt Adhesives:
- Hot-melt adhesives are solid at room temperature but melt when heated. They are often used in automated manufacturing processes for bonding components quickly.
The choice of adhesive depends on the application’s specific requirements, and manufacturers often consider factors like adhesion strength, flexibility, thermal conductivity, curing time, and environmental resistance when selecting the appropriate adhesive for a particular consumer electronic device.
What are the fundamental properties to consider when choosing adhesives for electronics?
Choosing the suitable adhesive for electronics is crucial to ensure proper electronic device performance, reliability, and longevity. Several fundamental properties should be considered when selecting adhesives for electronic applications:
Electrical Insulation:
- Adhesives should provide electrical insulation to prevent short circuits and other electrical issues.
Thermal Conductivity:
- For applications where heat dissipation is critical, such as in power electronics, adhesives with good thermal conductivity are essential to transfer heat away from sensitive components.
Temperature Resistance:
- Consider the operating temperature range of the electronic device and choose an adhesive that can withstand these conditions without losing its integrity.
Chemical Resistance:
- Adhesives should resist exposure to chemicals, solvents, and other substances commonly found in the environment where the electronic device will be used.
Mechanical Strength:
- The adhesive should provide sufficient mechanical strength to withstand mechanical stresses, such as vibrations, shocks, and thermal expansion and contraction.
Flexibility:
- In applications with movement or flexing, the adhesive should be flexible to accommodate such stresses without cracking or losing adhesion.
Adhesion to Different Substrates:
- Ensure the adhesive has good adhesion to the materials used in the electronic components and substrates, such as metals, plastics, and ceramics.
Curing Time:
- Consider the curing or setting time of the adhesive, as it can affect the manufacturing process and production efficiency.
Viscosity:
- The viscosity of the adhesive is essential for ease of application. Some applications require low-viscosity adhesives for better flow, while others may benefit from higher viscosity for gap filling.
Dielectric Strength:
- The adhesive should have a high dielectric strength to prevent electrical breakdown and leakage in electronic components.
UL Ratings and Compliance:
- Ensure that the adhesive meets relevant safety and compliance standards, such as Underwriters Laboratories (UL) ratings, especially if the electronic device will be subject to regulatory requirements.
Moisture Resistance:
- In environments with high humidity or the possibility of exposure to moisture, it’s essential to choose adhesives that offer good moisture resistance to prevent degradation.
UV Stability:
- If the electronic device is exposed to UV light, consider adhesives with UV stability to prevent degradation and maintain long-term performance.
Compatibility with Manufacturing Processes:
- Consider the compatibility of the adhesive with the specific manufacturing processes involved, such as dispensing, curing methods, and any post-application requirements.
By carefully considering these fundamental properties, you can choose an adhesive that aligns with the electronic application’s specific requirements and conditions, ensuring the assembled components’ reliability and performance.
How does adhesive affect heat dissipation in electronic devices?
Adhesives can positively and negatively affect heat dissipation in electronic devices, depending on their thermal conductivity and other properties. Heat dissipation is crucial in electronic devices to prevent overheating, leading to decreased performance, reduced lifespan, or even permanent damage. Here are some ways in which adhesives can affect heat dissipation:
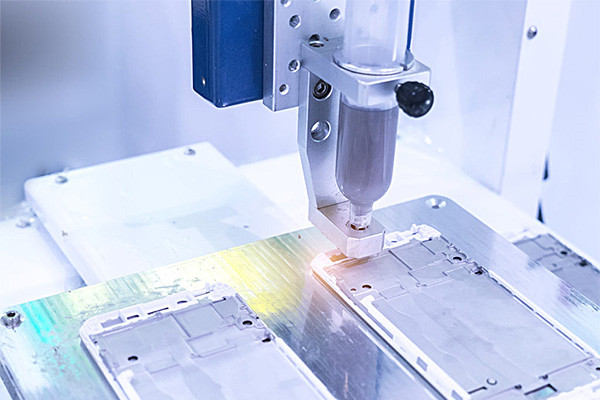
Thermal Conductivity:
- Positive Effect:Some adhesives are designed with high thermal conductivity, so they can efficiently transfer heat away from electronic components. These adhesives, often called thermal interface materials (TIMs), improve the thermal contact between heat-generating components (such as processors or integrated circuits) and heat sinks or other cooling solutions.
- Adverse Effect:Conversely, if the adhesive has low thermal conductivity, it can act as a thermal insulator, hindering the transfer of heat and exacerbating the overheating problem in electronic devices.
Bonding and Contact Enhancement:
- Positive Effect:Adhesives can enhance the contact between electronic components and heat sinks or other cooling elements, ensuring a more efficient heat transfer. This is particularly important in applications where maintaining a secure bond is crucial for long-term reliability and performance.
- Adverse Effect:If the adhesive layer is too thick or poorly applied, it can create thermal barriers, reducing heat dissipation effectiveness.
Flexibility and Mechanical Stress:
- Positive Effect:Adhesives that provide flexibility can help accommodate the thermal expansion and contraction of different materials in electronic devices. This flexibility can prevent mechanical stress on components, essential for maintaining reliable long-term performance.
- Adverse Effect:If the adhesive is rigid and does not allow for thermal expansion, it may lead to mechanical stress on electronic components, potentially causing damage over time.
Insulating Properties:
- Positive Effect:In some cases, adhesives with insulating properties may be used intentionally to isolate certain components electrically. However, ensuring that such adhesives do not impede heat dissipation is crucial.
- Adverse Effect:Adhesives with high electrical insulation properties might also have poor thermal conductivity, which can negatively impact heat dissipation.
The choice of adhesive in electronic devices is critical, and it should be selected based on the specific thermal requirements of the application. Manufacturers often consider the thermal conductivity, thickness, flexibility, and other properties of adhesives to optimize heat dissipation and overall device performance.
Can Consumer Electronics Adhesive withstand environmental factors like moisture and temperature changes?
Consumer electronics adhesives are designed to meet specific requirements for bonding in electronic devices. The ability of an adhesive to withstand environmental factors like moisture and temperature changes depends on the type of adhesive used and its formulation. Different adhesives have different properties, and manufacturers choose adhesives based on the specific needs of their products.
Moisture Resistance:
- Some adhesives are formulated to be moisture-resistant or waterproof. These adhesives often have properties that prevent water or moisture from affecting the bond. For example, cyanoacrylate (super glue) is known for its moisture resistance.
Temperature Resistance:
- High-temperature adhesives are designed to withstand elevated temperatures without losing their adhesive properties. Examples include epoxy adhesives, which can offer good temperature resistance.
Specialized Adhesives:
- In some cases, manufacturers use specialized adhesives specifically designed for extreme conditions. For instance, in automotive electronics or aerospace applications, where temperature variations can be significant, adhesives with high-temperature resistance may be preferred.
Conformal Coatings:
- In addition to adhesives, conformal coatings are sometimes applied to electronic components to protect them from environmental factors. These coatings can protect against moisture, dust, and temperature extremes.
Testing and Certification:
- Manufacturers often subject their products to various tests to ensure they meet specific environmental resistance standards. This may include temperature cycling tests, humidity tests, and more.
It’s essential to consult the specifications provided by the adhesive manufacturer and consider the specific requirements of the electronic device and its intended environment. Additionally, compliance with industry standards and regulations may factor in selecting adhesives for electronic applications.
Remember that while many adhesives offer good resistance to environmental factors, no adhesive is universally immune to all conditions. Therefore, choosing the suitable adhesive for a specific application requires careful consideration of the operating environment and the intended use of the electronic device.
What role does adhesive play in the miniaturization of electronic components?
Adhesives play a crucial role in the miniaturization of electronic components by bonding and securing these components within electronic devices. The miniaturization trend in electronics involves reducing individual components’ size and increasing circuit boards’ packing density. Adhesives contribute to this process in several ways:
Bonding Small Components:
- Using adhesives, miniaturized electronic components, such as microchips, resistors, and capacitors, are often related to circuit boards or substrates. Adhesives provide a secure attachment without mechanical fasteners, allowing for more compact designs.
Reducing Weight:
- Adhesives are typically lighter than traditional mechanical fasteners. In applications where weight is critical, such as in portable electronic devices or aerospace applications, using adhesives can help achieve weight savings.
Enhancing Structural Integrity:
- Miniaturized electronic devices often require structural integrity to withstand mechanical stresses, vibrations, and shocks. Adhesives can distribute stress more evenly than mechanical fasteners, contributing to the overall strength and durability of the device.
Enabling Flexible and Hybrid Electronics:
- Adhesives are vital in assembling flexible and hybrid electronics with components mounted on flexible substrates. These adhesives allow for conformal bonding and help maintain the flexibility of the overall system.
Thermal Management:
- Miniaturized electronic components generate heat, and efficient thermal management is crucial. Adhesives with thermal conductivity properties can bond heat-generating components to heat sinks or other thermal management solutions, ensuring effective heat dissipation.
Encapsulation and Protection:
- Adhesives encapsulate and protect electronic components from environmental factors such as moisture, dust, and chemicals. This protection is critical in miniaturized devices where components are closely packed and exposed to external elements.
Precision Application:
- Adhesives can be precisely applied in thin layers, allowing for fine control over the bonding process in miniaturized assemblies. This precision is essential when dealing with small and delicate electronic components.
Facilitating Automated Assembly:
- Adhesives are often compatible with automated manufacturing processes, facilitating high-throughput and consistent assembly of miniaturized electronic devices.
Adhesives contribute significantly to the miniaturization of electronic components by providing secure bonding, reducing weight, enhancing structural integrity, enabling flexibility, managing heat, protecting components, allowing precision application, and supporting automated assembly processes. The choice of adhesive is critical to ensure compatibility with the specific requirements of miniaturized electronic applications.
Are there specialized adhesives for specific consumer electronics applications?
Yes, there are specialized adhesives designed for specific consumer electronics applications. These adhesives are formulated to meet the unique requirements of electronic devices, providing features such as conductivity, thermal conductivity, flexibility, and resistance to environmental factors. Here are some examples of specialized adhesives used in consumer electronics:
Conductive Adhesives:
- Silver Conductive Adhesives:These adhesives contain silver particles for electrical conductivity. They are commonly used in bonding electronic components and creating conductive paths.
- Carbon Conductive Adhesives:Similar to silver conductive adhesives, these contain carbon particles and are used in applications where cost or other considerations make silver impractical.
Thermal Interface Materials (TIMs):
- Thermal Conductive Adhesives:These adhesives are designed to transfer heat away from electronic components, ensuring efficient thermal management. They are often used in applications like bonding heat sinks to processors or other heat-generating components.
Flexible Adhesives:
- Flexible Epoxy Adhesives:Electronics with flexible or bendable components, such as flexible printed circuits or wearable devices, often require adhesives that can withstand repeated bending and flexing without losing their adhesive properties.
UV-Curable Adhesives:
- UV-Curable Adhesives:These adhesives cure quickly when exposed to ultraviolet (UV) light. They are commonly used in electronics manufacturing processes where rapid bonding and curing are essential.
Optically Clear Adhesives (OCAs):
- OCAs:Used in applications such as touchscreen displays, OCAs are transparent adhesives that provide optical clarity while bonding components.
Low Outgassing Adhesives:
- Low Outgassing Adhesives:In applications where outgassing can be a concern, such as in the aerospace industry or enclosed electronic devices, these adhesives release minimal volatile compounds.
Electrically Insulating Adhesives:
- Dielectric Adhesives:Designed to provide electrical insulation, these adhesives prevent the flow of electric current between bonded components.
Cyanoacrylate Adhesives (Instant Adhesives):
- Cyanoacrylate Adhesives:Known as instant adhesives, they are often used in quick bonding applications in electronics assembly due to their fast curing properties.
Manufacturers and designers often choose adhesives based on the specific needs and characteristics of the electronic device they are working on. When selecting adhesives for consumer electronics applications, it’s essential to consider factors such as electrical conductivity, thermal properties, flexibility, and adhesion strength.
How does the adhesive bonding process impact the overall assembly of electronic devices?
The adhesive bonding process plays a crucial role in the overall assembly of electronic devices, impacting various aspects such as structural integrity, thermal management, electrical conductivity, and general reliability. Here are some ways in which the adhesive bonding process influences electronic device assembly:
Structural Integrity:
- Adhesives are often used to bond various components together, providing structural support and stability to the device. Choosing a suitable adhesive and proper bonding techniques contribute to the overall structural integrity of the device.
Component Positioning:
- Adhesives help secure components in their designated positions during the assembly process. This is especially important in devices with precise alignments, such as microelectronics and miniature components.
Thermal Management:
- Adhesives with thermal conductivity properties bond heat-generating components to heat sinks or other thermal management structures. This facilitates the efficient transfer of heat away from critical electronic components, preventing overheating and ensuring optimal performance.
Vibration Damping:
- Adhesives can act as a vibration-damping mechanism, reducing the impact of mechanical vibrations on sensitive electronic components. This is particularly important in applications with critical vibration resistance, such as automotive electronics.
Water and Dust Resistance:
- Properly selected adhesives can create a barrier against environmental factors such as water and dust. This helps protect electronic components from moisture-related damage, enhancing the device’s durability and reliability.
Electrical Connectivity:
- Conductive adhesives play a crucial role in establishing electrical connections between components. They are used for bonding conductive traces, connecting wires, or attaching components that need electrical continuity.
Flexibility and Bendability:
- In devices with flexible or bendable components, adhesives with elastic properties ensure that the bonds can withstand repeated bending without compromising the assembly’s integrity. This is common in flexible printed circuits and wearable electronics.
Assembly Speed and Efficiency:
- Some adhesives, such as UV-curable adhesives, offer fast curing times, contributing to the efficiency of the assembly process. Quick curing allows for shorter production cycles and reduces the overall assembly time.
Aesthetic Considerations:
- Optically clear adhesives are used in applications where transparency and aesthetics are crucial, such as in displays and touchscreen assemblies. These adhesives maintain optical clarity, ensuring a visually appealing final product.
Reliability and Longevity:
- The proper selection and application of adhesives contribute to electronic devices’ overall reliability and longevity. Adhesives that resist aging, thermal cycling, and environmental stresses help ensure the machine performs consistently over its expected lifespan.
The adhesive bonding process has a multifaceted impact on electronic device assembly, influencing the final product’s physical structure and functional performance. Manufacturers carefully choose adhesives based on the specific requirements of the device, considering factors such as material compatibility, thermal properties, electrical conductivity, and environmental durability.
What challenges are associated with using adhesives in consumer electronics?
Using adhesives in consumer electronics comes with various challenges despite their benefits in bonding and assembly. Some of the critical challenges associated with using adhesives in this context include:
Thermal Management:
- Consumer electronics often generate heat during operation. Adhesives may need to withstand elevated temperatures without losing their adhesive properties or degrading. Ensuring proper thermal management is crucial to prevent overheating and potential damage to electronic components.
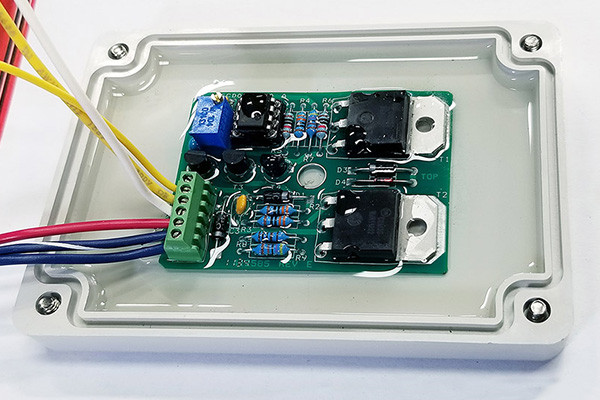
Material Compatibility:
- Adhesives must be compatible with materials commonly used in electronics, including plastics, metals, glass, and multiple coatings. Incompatibility can lead to reduced adhesion strength or damage to the bonded materials.
Electrical Insulation:
- Adhesives in electronic applications must exhibit electrical insulating properties to prevent short circuits or interference. Conductive adhesives may be used in specific cases, but generally, insulating properties are essential.
Durability and Reliability:
- Consumer electronics are often subjected to various stresses, including mechanical shocks, vibrations, and fluctuations in temperature and humidity. Adhesives must maintain their integrity over time to ensure the longevity and reliability of the electronic device.
Precision in Application:
- Achieving precise and uniform application of adhesives can be challenging, especially in miniaturized electronic components. Inconsistent applications can lead to performance issues and compromised structural integrity.
Repairability:
- In some cases, consumer electronics may need to be repaired or upgraded. Adhesives can make disassembly difficult, leading to challenges in the repair process. Designing for both strong bonding and ease of repair is a delicate balance.
Environmental Considerations:
- Adhesives may contain volatile organic compounds (VOCs) or other substances that can be environmentally harmful. An increasing emphasis is on using eco-friendly adhesives to align with environmental regulations and consumer preferences.
Cost Considerations:
- The cost of high-performance adhesives can be a factor in the overall production cost of electronic devices. Manufacturers must balance the benefits of using adhesives with the economic considerations of production.
Process Compatibility:
- Adhesive curing or setting processes must align with the overall manufacturing process of electronic devices. This includes considerations for production speed, automation, and compatibility with other assembly steps.
Adhesive Selection and Testing:
- Choosing a suitable adhesive for a specific application requires careful consideration of the factors above. Rigorous testing is often necessary to ensure that the selected adhesive meets the performance requirements for the intended use.
Addressing these challenges requires collaboration between materials scientists, engineers, and manufacturers to develop and implement effective adhesive solutions that meet the unique demands of consumer electronics.
Are there environmentally friendly adhesive options for electronics?
Yes, there are environmentally friendly adhesive options available for electronics. As the demand for sustainable and eco-friendly products has increased, manufacturers have developed adhesives that minimize environmental impact. Here are some environmentally friendly adhesive options for electronics:
Bio-Based Adhesives:
- These adhesives are derived from renewable resources such as plant-based materials (e.g., soy, corn, or starch). Bio-based adhesives are often biodegradable and can reduce the reliance on fossil fuels.
Water-Based Adhesives:
- Water-based adhesives are formulated with water as the primary solvent instead of volatile organic compounds (VOCs) found in traditional adhesives. They are less toxic, emit less harmful fumes, and are more environmentally friendly.
Solvent-Free Adhesives:
- Solvent-free adhesives eliminate or significantly reduce the use of harmful solvents. This decreases the environmental impact and improves the safety of both workers and end-users.
Recyclable Adhesives:
- Some adhesive formulations are designed to be readily detachable from materials during recycling. This feature supports the recycling of electronic components and reduces the environmental footprint.
UV-Curable Adhesives:
- UV-curable adhesives use ultraviolet (UV) light for curing instead of heat or chemical reactions. They often contain fewer harmful substances and have a faster curing process, reducing energy consumption.
Adhesives with Low VOCs:
- Adhesives with low volatile organic compound (VOC) content contribute to improved indoor air quality and reduced environmental impact. VOCs can contribute to air pollution and have potential health effects.
Reusable Adhesives:
- Some adhesives are designed to be reusable, allowing components to be easily detached and re-bonded without causing damage. This feature supports a circular economy and reduces electronic waste.
Plant-Based Adhesives:
- Adhesives from plant-based sources, such as cellulose or lignin, are considered more sustainable. These adhesives can be biodegradable and have a lower environmental impact than traditional petroleum-based adhesives.
Green Certification Standards:
- Look for adhesives that meet specific environmental certification standards, such as those set by organizations like the Forest Stewardship Council (FSC) or the U.S. Green Building Council (USGBC). Compliance with such standards indicates a commitment to sustainability.
When selecting environmentally friendly adhesives, it’s essential to consider the specific application requirements and performance characteristics needed for electronic devices. Manufacturers and suppliers may provide information about the environmental attributes of their adhesive products, making it easier for consumers to make informed choices that align with sustainability goals.
How can consumers repair electronic devices using adhesives?
Repairing electronic devices using adhesives can be a practical and effective approach, especially for fixing components, securing loose parts, or replacing certain elements. Here are general steps that consumers can follow when using adhesives for electronic device repair:
Identification of the Issue:
- Identify the specific problem with the electronic device. Determine which component needs repair or replacement and understand the nature of the damage.
Safety First:
- Ensure the device is powered off and, if applicable, disconnected from any power source before attempting any repairs. This reduces the risk of electrical shock and damage to the device.
Disassembly:
- Carefully disassemble the device using appropriate tools. Some devices may have screws or clips that need to be removed, while others may require prying or careful separation of parts. Refer to the device’s user manual or online guides for disassembly instructions.
Cleaning Surfaces:
- Clean the surfaces to be bonded with the adhesive. Use isopropyl alcohol or another appropriate cleaning agent to remove any dust, debris, or residue. Clean surfaces promote better adhesion.
Adhesive Selection:
- Choose the right adhesive for the repair. Different adhesives are suitable for various materials and applications. For example, cyanoacrylate (super glue) may work well for bonding plastics, while epoxy may be ideal for more durable and long-lasting repairs.
Application of Adhesive:
- Apply the adhesive according to the manufacturer’s instructions. Use a small, controlled amount, ensuring even distribution on the surfaces to be bonded. Avoid applying too much; the excess adhesive may squeeze out when parts are pressed together.
Bonding:
- Join the parts together and apply gentle pressure to ensure a secure bond. Follow the recommended curing time for the adhesive, allowing it to set and reach its full strength. This duration varies depending on the type of adhesive used.
Reassembly:
- Once the adhesive has cured, reassemble the device in the reverse order of disassembly. Take care to align components properly and tighten any screws or fasteners as needed.
Testing:
- Power on the device and test its functionality. Ensure that the repaired component is working as intended. If the repair involves screens or displays, check for issues like dead pixels or touch sensitivity problems.
Post-Repair Considerations:
- Some adhesives may have a noticeable appearance after curing. Consider aesthetics and visibility when using adhesives, especially for repairs on visible surfaces.
It’s important to note that not all electronic device repairs can be effectively carried out by consumers, and some repairs may require professional expertise. Additionally, certain manufacturers design devices with adhesives that make disassembly challenging, complicating repair attempts. Always refer to the device’s warranty and seek professional assistance if needed.
What innovations are occurring in the field of Consumer Electronics Adhesive?
In consumer electronics adhesives, several innovations are occurring to address challenges and improve performance. These innovations aim to enhance the bonding process, durability, and environmental impact of adhesives used in electronic devices. Some notable trends and innovations include:
Flexible Adhesives for Bendable Electronics:
- As flexible and foldable electronics become more prevalent, adhesives need to maintain strong bonds while accommodating repeated flexing and bending. Innovations include the development of flexible adhesives that can withstand mechanical stresses without compromising performance.
Thermally Conductive Adhesives:
- With the increasing power density in electronic devices, there is a demand for adhesives that can effectively transfer heat away from components. Thermally conductive adhesives help in heat dissipation, preventing overheating and improving the overall reliability of electronic devices.
Low-Temperature Curing Adhesives:
- Traditional adhesives may require high temperatures for curing, which can be unsuitable for temperature-sensitive electronic components. Low-temperature curing adhesives are being developed to enable bonding without subjecting components to excessive heat.
Nanotechnology in Adhesives:
- Nanomaterials, such as nanoparticles or nanofibers, are incorporated into adhesives to enhance their mechanical and thermal properties. This can result in stronger bonds and improved performance, particularly in demanding electronic applications.
Smart Adhesives:
- Innovations are focusing on adhesives with intelligent functionalities, such as self-healing properties. These adhesives can repair minor damages autonomously, extending the lifespan of bonded components and improving device durability.
Sustainable and Eco-Friendly Adhesives:
- There is a growing emphasis on developing adhesives with reduced environmental impact. Innovations include bio-based adhesives derived from renewable resources, water-based formulations, and adhesives with minimal or no volatile organic compounds (VOCs).
Electrically Conductive Adhesives:
- Electrically conductive adhesives are gaining importance in electronic applications where traditional soldering may not be suitable. These adhesives enable electrical connectivity while providing the benefits of adhesion.
Adhesives for Wearables and Medical Devices:
- As the market for wearables and medical devices expands, specialized adhesives are being developed to meet the unique requirements of these applications. This includes adhesives that are skin-friendly, biocompatible, and able to withstand various environmental conditions.
Advanced Dispensing Techniques:
- Innovations in dispensing techniques and equipment contribute to more precise and controlled application of adhesives. This is particularly important in the miniaturized assembly of electronic components, where accuracy is crucial.
Recyclable Adhesives:
- Adhesives designed for easy separation during recycling processes are becoming more common. These adhesives contribute to the recyclability of electronic components and help reduce electronic waste.
The field of consumer electronics adhesives is dynamic, with ongoing research and development aimed at addressing emerging challenges and supporting advancements in electronic device design and manufacturing. These innovations produce more reliable, durable, and environmentally friendly electronic products.
Are there safety considerations when working with electronic adhesives?
Yes, there are several safety considerations when working with electronic adhesives. These considerations help protect individuals from potential health hazards associated with using these materials. Here are some general safety guidelines:
Ventilation:
- Work in a well-ventilated area to minimize exposure to fumes. Use fume extraction systems or work near an open window or exhaust fan.
Personal Protective Equipment (PPE):
- Wear appropriate PPE, including safety glasses or goggles, gloves, and a lab coat or apron to protect against splashes or skin contact.
Skin Contact:
- Avoid direct skin contact with adhesives. If contact occurs, wash the affected area immediately with soap and water.
Eye Protection:
- Use safety glasses or goggles to protect your eyes from splashes or accidental contact with the adhesive.
Inhalation:
- Avoid inhaling fumes from the adhesive. Use a respirator with the appropriate filters if you are working with adhesives that produce vapors.
Read and Follow Material Safety Data Sheets (MSDS):
- Familiarize yourself with the MSDS for the specific adhesive you are using. MSDS provides essential information about the chemical composition, hazards, and recommended safety measures.
Storage:
- Store adhesives in a cool, dry place away from direct sunlight and incompatible materials. Follow the manufacturer’s recommendations for storage conditions.
Avoid Mixing Incompatible Substances:
- Only mix different types of adhesives if explicitly recommended by the manufacturer. Some substances may react with each other, producing harmful by-products.
Emergency Procedures:
- Know the location of emergency equipment, such as eyewash stations and safety showers. Have a first aid kit available, and know the appropriate steps to take in case of accidental exposure or ingestion.
Training:
- Ensure that personnel working with electronic adhesives are adequately trained in safely handling and using these materials.
Disposal:
- Dispose of adhesive waste by local regulations. Some adhesives may be considered hazardous waste, and proper disposal is essential.
Always refer to the specific safety recommendations provided by the manufacturer of the electronic adhesive you are using, as different adhesives may have unique safety considerations. Following proper safety practices minimizes risks and ensures a safe working environment.
How does adhesive selection impact the design of electronic circuits and PCBs?
Adhesive selection plays a crucial role in the design and assembly of electronic circuits and printed circuit boards (PCBs). The choice of adhesive can impact various aspects of electronic components’ design, performance, and reliability. Here are some key ways in which adhesive selection influences the design of electronic circuits and PCBs:
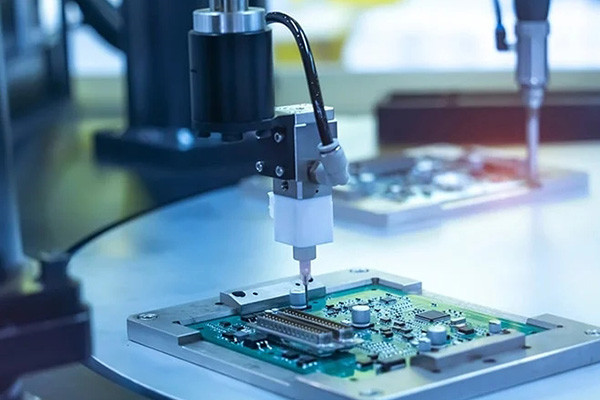
Bonding and Assembly:
- Adhesives bond different components, such as attaching parts to the PCB substrate or bonding layers in multilayer PCBs. The adhesive’s properties, such as adhesion strength and curing time, influence the assembly process and overall bond quality.
Thermal Management:
- Some adhesives have good thermal conductivity, helping heat dissipation from electronic components. This is particularly important in applications where thermal management is critical, as excessive heat can affect the performance and reliability of electronic devices.
Electrical Insulation:
- Adhesives can provide electrical insulation, preventing short circuits and ensuring proper electrical performance. Insulating adhesives are often used where components need to be secured without creating electrical paths between them.
Environmental Protection:
- Adhesives can be a barrier to environmental factors such as moisture, dust, and chemicals. Selecting adhesives with appropriate protective properties is crucial for ensuring the long-term reliability of electronic devices, especially in harsh environments.
Flexibility and Stress Absorption:
- Flexible adhesives are often used in applications where the PCB or electronic components experience mechanical stress or thermal expansion. Adhesive flexibility helps absorb stress, reducing the risk of mechanical failure or component damage.
Dielectric Properties:
- Adhesives may have specific dielectric properties that affect signal integrity and the overall performance of the circuit. High-frequency applications, in particular, may require adhesives with low dielectric constants to minimize signal loss.
Solder Mask Adhesion:
- In PCB manufacturing, adhesives are used in the solder mask application process. The adhesion properties of the adhesive used in the solder mask affect the integrity of the mask, which, in turn, influences the protection and reliability of the PCB.
Surface Mount Technology (SMT) and Component Attachment:
- Adhesives are commonly used in surface mount technology for attaching components to the PCB before soldering. The adhesive must be compatible with the assembly process and provide a reliable bond until the soldering process is complete.
Miniaturization and Weight Considerations:
- As electronic devices become smaller and lighter, the adhesive’s weight, thickness, and overall footprint become critical factors in design. Low-profile and lightweight adhesives are often preferred for compact electronic assemblies.
Compliance with Industry Standards:
- Adhesive selection should align with industry standards and regulations applicable to electronic devices. Meeting specific adhesive standards ensures the final product meets safety and performance requirements.
Careful consideration of these factors during the design phase is essential to select adhesives that meet the specific requirements of the electronic circuit or PCB application. Collaboration between design engineers and materials specialists is often necessary to choose adhesives that balance performance, reliability, and manufacturability.
What are the common misconceptions about Consumer Electronics Adhesive?
Several misconceptions exist regarding consumer electronics adhesives, and it’s essential to dispel these misunderstandings to make informed decisions during product design and assembly. Here are some common misconceptions:
Misconception: Adhesives are Only for Bonding
- Reality:While bonding is a primary function of adhesives, they serve various purposes in consumer electronics. Adhesives can provide insulation, thermal management, vibration dampening, environmental protection, and bonding.
Misconception: All Adhesives are the Same
- Reality:Adhesives come in a wide variety with different formulations and properties. They are designed for specific applications, and using the wrong type of adhesive can lead to performance issues or even failure. It’s crucial to select adhesives based on the requirements of the application.
Misconception: Stronger Adhesives are Always Better
- Reality:The strength of an adhesive should match the application’s requirements. Using an adhesive that is too strong may make disassembly difficult, and it could damage components during removal. It’s important to balance strength with other factors like flexibility and ease of rework.
Misconception: Adhesives Always Weaken Over Time
- Reality:While some adhesives may degrade over time due to exposure to UV light, heat, or chemicals, many are designed for long-term stability and durability. Understanding the environmental conditions and selecting the appropriate adhesive can mitigate degradation concerns.
Misconception: Adhesives are Not Important in Electronic Devices
- Reality:Adhesives play a critical role in the performance and reliability of electronic devices. They contribute to structural integrity, heat dissipation, and protection against environmental factors. Neglecting the importance of adhesives can lead to component failure, reduced lifespan, or compromised functionality.
Misconception: Adhesives Always Require Lengthy Curing Times
- Reality:While some adhesives may have longer curing times, many modern adhesives offer fast curing options. Manufacturers often provide adhesives with varying cure times to accommodate different assembly processes and production schedules.
Misconception: Adhesives are Always Harmful to the Environment
- Reality:The environmental impact of adhesives depends on the specific formulation. Many adhesives today are designed to be environmentally friendly, with low volatile organic compound (VOC) emissions and compliance with environmental regulations. It’s essential to choose adhesives with eco-friendly formulations when possible.
Misconception: Adhesives Are Only for Permanent Bonding
- Reality:While some adhesives create permanent bonds, others are designed for temporary or reworkable applications. Reworkable adhesives allow for disassembly and component replacement, providing device maintenance or upgrade flexibility.
Misconception: Adhesives Are Not Relevant in Miniaturized Devices
- Reality:Adhesives are crucial for component attachment, thermal management, and overall structural integrity in miniaturized devices. Low-profile adhesives are essential in compact electronics to minimize space consumption.
Misconception: Adhesives Are Always Visible
- Reality:Many adhesives are designed to be virtually invisible once applied. This is particularly important for consumer electronics, where aesthetics are a priority. Transparent and color-matching adhesives are used to maintain a clean and polished appearance.
It’s essential for designers, engineers, and manufacturers to stay informed about the diverse range of adhesives available and to consider their specific properties and applications to ensure optimal performance in consumer electronic devices.
Can adhesives enhance the aesthetic appeal of consumer electronic devices?
Yes, adhesives can significantly contribute to the aesthetic appeal of consumer electronic devices. The aesthetic aspects of electronic devices are increasingly important to consumers, and manufacturers often use adhesives strategically to achieve a polished and visually pleasing appearance. Here are several ways in which adhesives enhance the aesthetic appeal of consumer electronic devices:
Seamless Bonding:
- Adhesives can create seamless bonds between materials like metal, glass, or plastics. This eliminates the need for visible fasteners or mechanical joints, resulting in a sleek and modern appearance.
Invisible Bonds:
- Transparent adhesives are often used to create invisible bonds, ensuring that the adhesive lines are not visible on the surface of the device. This is particularly important for applications where a clear and unobstructed view is desired.
Low Profile and Thin Bond Lines:
- Modern adhesives can provide low-profile and thin bond lines, reducing the visibility of joints and seams. This is crucial for achieving a slim and elegant design in electronic devices.
Color Matching:
- Adhesives are available in various colors, allowing manufacturers to choose formulations that match the color of the bonded materials. This helps maintain a cohesive and harmonious color scheme throughout the device.
Flexible Design Options:
- Adhesives offer design flexibility, enabling materials to be bonded with irregular shapes or contours. This flexibility allows designers to create unique and visually appealing device designs that might be challenging with traditional mechanical fastening methods.
Enhanced Surface Finish:
- Adhesives can enhance the surface finish of materials, providing a glossy, matte, or textured appearance. This contributes to the overall visual and tactile experience of the electronic device.
Display Enhancement:
- Adhesives assemble display components, such as bonding glass, to the device frame. The use of high-quality adhesives ensures a precise and uniform display, enhancing the overall visual quality of the device.
Water and Dust Resistance:
- Adhesives play a role in creating water-resistant and dust-resistant seals, preventing the intrusion of foreign particles and liquids. This contributes to the device’s durability and maintains its aesthetic appeal by keeping it clean and functional.
Customization and Branding:
- Adhesives can apply logos, labels, or decorative elements to the device. This allows manufacturers to customize the appearance of the device and reinforce brand identity.
Reworkable Adhesives for Upgrades:
- In devices where reworkability is essential, such as smartphones, reworkable adhesives allow for easy disassembly and component replacement without leaving visible marks or damage.
Manufacturers can achieve the desired aesthetic qualities in consumer electronic devices by carefully selecting adhesives based on their optical properties, transparency, color, and texture. The use of adhesives as a design element contributes to the visual appeal and the overall user experience and brand perception.
Are there adhesive solutions for flexible and foldable electronics?
Yes, adhesive solutions play a critical role in the design and assembly of flexible and foldable electronics. These electronic devices often involve bendable or foldable components, so that traditional rigid adhesives may be unsuitable. Here are some adhesive solutions specifically designed for flexible and foldable electronics:
Flexible Adhesives:
- Adhesives engineered to be flexible can accommodate the bending and flexing of materials without losing their bond strength. These adhesives maintain their integrity even when subjected to repeated bending, making them ideal for flexible electronic applications.
Low Modulus Adhesives:
- Low-modulus adhesives are characterized by their flexibility and elasticity. They are designed to absorb stresses caused by bending or flexing, reducing the risk of material or component damage in flexible and foldable electronic devices.
Stretchable Adhesives:
- For applications that involve significant stretching or deformation, stretchable adhesives are designed to elongate and contract without losing adhesion. These adhesives are suitable for wearable electronics and other devices with dynamic shapes.
Conductive Adhesives:
- In flexible and foldable electronics, where circuits may need to flex with the device, conductive adhesives are used to maintain electrical connectivity while accommodating movement. These adhesives can bond flexible substrates while allowing for electrical conduction.
Optically Clear Adhesives (OCAs):
- OCAs are transparent adhesives with optical clarity, making them suitable for bonding components in displays and touchscreens. They are often used in foldable smartphones and tablets to maintain a clear and sharp visual display.
Thin Bond Lines:
- Adhesives that can form thin bond lines are essential for maintaining a low profile in flexible and foldable electronics. Thin bond lines contribute to the overall flexibility of the device.
Heat-Activated Adhesives:
- Some flexible electronic components may be assembled using heat-activated adhesives. These adhesives are applied in a non-tacky form and become adhesive when exposed to heat during the assembly process.
Elastomeric Adhesives:
- Elastomeric adhesives are designed to have rubber-like properties, offering flexibility and resilience. These adhesives are suitable for applications where the device may undergo repeated bending or stretching.
UV-Curable Adhesives:
- UV-curable adhesives offer fast curing times and are often used to produce flexible electronics. They can be cured with UV light, allowing for rapid bonding without extended drying or curing periods.
Reworkable Adhesives:
- When disassembly and rework are necessary, reworkable adhesives allow for the separation of components without causing damage. This can be important for repairability and upgrades in flexible and foldable devices.
The selection of the most appropriate adhesive depends on the specific requirements of the flexible or foldable electronic application. Manufacturers often collaborate with adhesive specialists to choose formulations that balance flexibility, adhesion strength, durability, and other critical factors to ensure the success of these innovative devices.
How can consumers ensure proper disposal of electronics containing adhesive components?
Proper disposal of electronics containing adhesive components is essential to minimize environmental impact and adhere to waste disposal regulations. Consumers can take several steps to ensure the responsible disposal of electronic devices. Here are some guidelines:
Check Local Regulations:
- Familiarize yourself with local rules and guidelines for electronic waste (e-waste) disposal. Different regions may have specific regulations and facilities for handling electronic devices.
Participate in E-Waste Recycling Programs:
- Many communities and electronic retailers offer e-waste recycling programs. Look for collection events or drop-off locations where you can safely dispose of your electronic devices.
Manufacturer Take-Back Programs:
- Some electronics manufacturers have take-back programs that allow consumers to return their old devices for proper recycling. Check the manufacturer’s website or contact them directly for such programs.
Find Certified E-Waste Recyclers:
- Look for certified e-waste recycling facilities that follow environmentally responsible practices. These facilities are equipped to recycle and dispose of electronic components, including adhesives and other materials.
Remove Personal Data:
- Before disposing of electronic devices, ensure you have removed any personal or sensitive data. Perform a factory reset or use data-erasing tools to clean the device.
Separate Components:
- If possible, disassemble the electronic device and separate its components. This can make it easier for recycling facilities to handle different materials, including adhesives, plastics, metals, and circuit boards.
Follow Recycling Guidelines:
- Adhere to guidelines provided by recycling facilities regarding adequately preparing electronic devices for recycling. Some facilities may have specific requirements for handling adhesives or other materials.
Dispose of Batteries Properly:
- If the electronic device contains batteries, remove them and dispose of them properly. Many communities have specific programs for battery recycling.
Check for Hazardous Materials:
- Some electronic components, such as certain adhesives or display technologies, may contain hazardous materials. Be aware of any potential hazards and follow disposal guidelines for hazardous waste.
Donate or Sell Still-Functional Devices:
- If the electronic device is still functional and in good condition, consider donating it to a local charity or selling it to someone who can use it. Extending the life of electronics is an environmentally friendly practice.
Educate Yourself:
- Stay informed about the environmental impact of electronic waste and the importance of responsible disposal. By educating yourself, you can make more informed decisions about the products you use and how to dispose of them.
Remember that improper disposal of electronic devices, including adhesives and other materials, can contribute to environmental pollution and health risks. Following proper disposal practices helps protect the environment and ensures that valuable materials are recycled responsibly.
Conclusion:
In conclusion, Consumer Electronics Adhesive is a critical component that plays a pivotal role in electronic device functionality, durability, and design. As technology continues to evolve, so do the demands for advanced and specialized adhesives. Whether you’re a manufacturer, designer, or end-user, understanding the nuances of Consumer Electronics Adhesive is essential for creating and maintaining cutting-edge electronic devices. Stay informed, explore the possibilities, and make informed choices in the world of Consumer Electronics Adhesive.
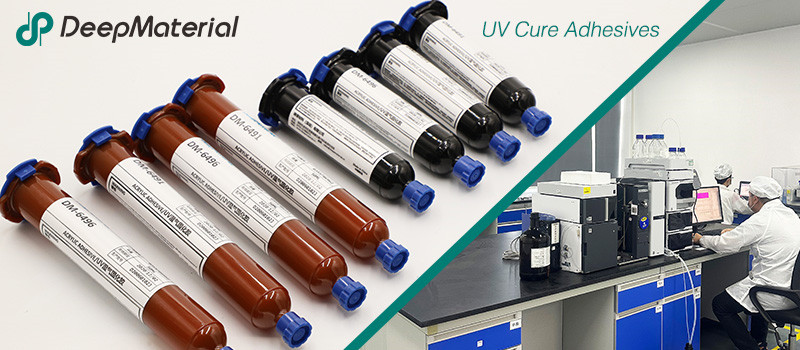
DeepMaterial
Based on the core technology of adhesives, DeepMaterial has developed adhesives for chip packaging and testing, circuit board level adhesives, and adhesives for electronic products. Based on adhesives, it has developed protective films, semiconductor fillers, and packaging materials for semiconductor wafer processing and chip packaging and testing. More…
UV Curing Adhesives
UV light cure have a number of benefits making them a popular choice among many product assembly and manufacturing applications. Many UV light cure adhesives can provide a nearly instantaneous bond to difficult substrates like glass and plastic. UV cure adhesives often require an accelerator or UV light for a bond to form.
Adhesive Blogs & News
The latest adhesive industry science and technology, Deepmaterial news, and market trends and forecasts.
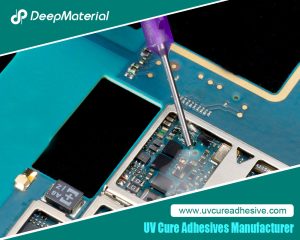
Electrical Potting Compound
Electrical Potting Compound In the vast field of modern electronic technology, Electrical Potting Compound plays a crucial role. It is like the invisible guardian inside electronic devices, providing reliable protection and stable performance support for various precise electronic components. Definition and Classification of Electrical Potting Compound Electrical Potting Compound is a special material
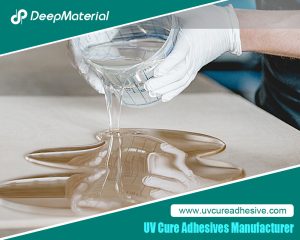
The Mystery and Application of Polyurethane Potting
The Mystery and Application of Polyurethane Potting In the modern industrial and technological fields, Polyurethane Potting is playing an increasingly important role. It not only provides reliable protection for various electronic devices and components but also shows unique advantages in optimizing performance and extending service life. What is Polyurethane Potting Polyurethane Potting is a
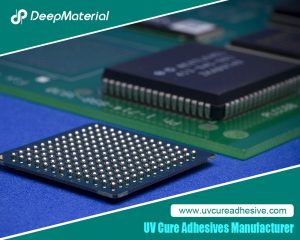
Waterproof Potting Compound: The Invisible Guardian of Electronic Devices
Waterproof Potting Compound: The Invisible Guardian of Electronic Devices In the era of rapid technological development today, electronic devices have become an indispensable part of our lives and work. From smart phones, tablets to smart home devices and industrial control systems, the application of electronic devices is everywhere. However, these devices often face the tests
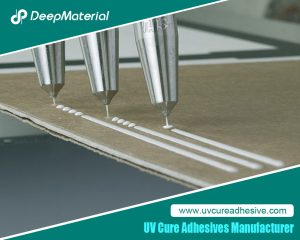
Potting Compound vs Epoxy: A Comparative Study and Application Overview
Potting Compound vs Epoxy: A Comparative Study and Application Overview In the modern industrial and electronic domains, the selection of materials holds a pivotal position in determining the performance, reliability, and longevity of products. Potting Compound and Epoxy are two frequently encountered materials that each demonstrate remarkable capabilities in numerous applications, yet they possess
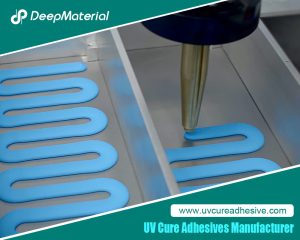
Exploring Potting Compound for Electronics: The Key Material for Providing Reliable Protection to Electronic Products
Exploring Potting Compound for Electronics: The Key Material for Providing Reliable Protection to Electronic Products In the current era of rapid technological development, electronic products have become an indispensable part of our lives. From smartphones, tablets to smart home devices and industrial control systems, the performance and reliability of electronic devices are crucial for
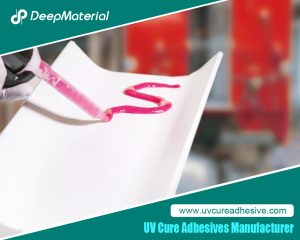
The Wonderful World of UV Curing Potting Compound
The Wonderful World of UV Curing Potting Compound In the rapid development of modern technology, various innovative materials continue to emerge, bringing unprecedented possibilities to applications in various fields. Among them, UV curing potting compound has become a shining star in the field of materials science with its unique performance and wide range of